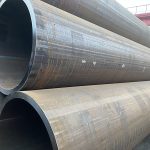
JCOE Welded Steel Pipe | JCOE UOE LSAW
November 26, 2023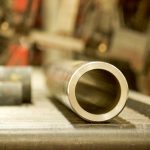
DIN 17175 Heat-resistant Seamless Steel Pipe
November 29, 2023LSAW Steel Pipe Technology
LSAW (Longitudinally Submerged Arc Welding) Steel Pipe technology involves the welding of steel pipes using a single plate as raw material. The process is conducted by molding the plate into a tubular shape and subsequently welding the seam using a submerged arc welder. Here is the general step-by-step process:
1. Plate Ultrasonic Inspection
Raw materials are subjected to ultrasonic inspection to evaluate and ensure their quality before production begins.
2. Edge Milling
The edges of the steel plates are milled to achieve a specific bevel angle, which is a crucial step for the welding process.
3. Plate Edge Crimping
The edges of the steel plates are then crimped to facilitate the forming process.
4. Forming
The crimped steel plate is formed into a tubular shape by bending the plate. The bending can be carried out using either the UOE (Uing, Oing, Expanding) method or the JCOE (J-ing, C-ing, O-ing, Expanding) method.
- Longitudinally Submerged Arc Welded (LSAW) pipes are commonly used in the oil and gas industry because of their ability to withstand high pressure. They are made from steel by using specific welding techniques. Two techniques commonly used in the production of LSAW pipes are UOE (Uing and Oing forming) and JCOE (J-ing, C-ing and O-ing) processes.
UOE Process
The UOE pipe manufacturing process is as follows:
- Edge Milling: The steel plate is first milled on both sides to achieve the required width.
- Pre-Bending: The edges of the milled plate are then bent into a “U” shape using a U-press.
- Forming: The “U” shaped plate is then formed into an “O” shape using an O-press.
- Welding: The “O” shaped pipe is then welded. There are two welding stages, inside welding and outside welding, to ensure the pipe’s strength and durability.
- Calibration and Testing: The welded pipe is inspected, calibrated, and tested to ensure it meets the required standards.
JCOE Process
The JCOE pipe manufacturing process is as follows:
- Edge Milling: Similar to the UOE process, the steel plate is first milled on both sides.
- Pre-Bending: The edges of the milled plate are bent into a “J” shape using a J-press.
- Forming: The “J” shaped plate is then formed into a “C” shape using a C-press, and finally into an “O” shape using an O-press.
- Welding: The formed pipe is then welded, both on the inside and the outside.
- Calibration and Testing: The welded pipe is inspected, calibrated, and tested.
5. Pre-Welding
This step involves tack welding the formed pipe to maintain its shape during the final welding process.
6. Inside Welding
The inside of the pipe is welded using the submerged arc welding technique.
7. Outside Welding
The outside of the pipe is also welded using the submerged arc welding technique. The inside and outside welding ensures a strong and durable pipe.
8. Ultrasonic Inspection
The finished pipe is inspected using ultrasonic testing to detect any defects or imperfections in the welds.
9. X-Ray Inspection
X-ray inspection is used to further evaluate the welds and ensure their quality.
10. Pipe End Machining
The ends of the pipe are machined to achieve the required specifications.
11. Hydrostatic Testing
The finished pipe undergoes hydrostatic testing to test its ability to withstand pressure.
12. Final Inspection and Coating
Lastly, the pipe undergoes a final inspection before it is coated for corrosion protection and prepared for shipping.
This technology allows the creation of large-diameter pipes suited for high-pressure environments, making LSAW pipes an ideal choice for oil and gas transmission, engineering projects, and offshore projects.
Comparison
Both methods give a similar end product. However, the JCOE process allows for a wider range of diameters and wall thicknesses, as it is more flexible in handling variations in material properties and dimensions. The UOE process, on the other hand, is more common and is typically used for pipes with larger diameters.
Both UOE and JCOE processes are efficient and reliable methods for making LSAW pipes. The choice between the two often depends on the specific requirements of the pipe, such as its diameter, wall thickness, and the material used.
Product Specification: LSAW Steel Pipe, SAWL Steel Pipe
Size
- Outer Diameter: 355.6mm-2320mm
- Wall Thickness: 7-50mm
- Length: 5.8m / 6m / 11.8m / 12m / 18m / 32m
Standard
- API 5L PSL1 / PSL2 Gr.A, Gr.B, X42, X46, X52, X56, X60, X65, X70
- ASTM A53 / A252 / A500 / A672 / A691 / A139
- EN10025 / EN10210 / EN10219 / EN10217 / EN10208 / EN10297
- AS1163 / JIS G3457 / JIS G3101
- DIN 17100
Ends
- Black ends
- Bevelled ends
- Plain ends
Surface Treatment
- Bare
- Black Painting
- Varnished
- Galvanized
- Anti-corrosion coating
Application
The LSAW(Longitudinally Submerged Arc Welding) Pipe is suitable for use in oil and gas transmission, engineering projects, and offshore projects.
Features of LSAW Steel Pipe
- Large diameter
- Thick wall
- High Pressure resistance
UOE LSAW Pipe
- Outside Diameter:Φ508mm – 1118mm (20″- 44″)
- Wall Thickness: 6.0 – 25.4mm 1/4″-1″
- Quality Standards: API、DNV、ISO、DEP、EN、ASTM、DIN、BS、JIS、GB、CSA
- Length: 9 – 12.3m (30′- 40′)
- Grades: API 5L A-X90, GB/T9711 L190-L625
JCOE LSAW Pipe
- Outside Diameter:Φ406mm – 1626mm (16″ – 64″ )
外径:Φ406mm – 1626mm (16″ – 64″ ) - Wall Thickness:6.0 – 75mm (1/4″ – 3″ )
- Quality Standards:API、DNV、ISO、DEP、EN、ASTM、DIN、BS、JIS、GB、CSA
- Length:3 – 12.5m ( 10′- 41′ )
- Grades:API 5L A-X100, GB/T9711 L190-L690
PRODUCTION EQUIPMENT
Pre Bending Machine
JCOE Forming Machine
Sewing Machine
Plasma Cutting Machine
Internal and External Welding Machine
Hydraulic Press Machine
Edge Milling Machine
Straightening Machine
Pipe End Facing Machine
Specification