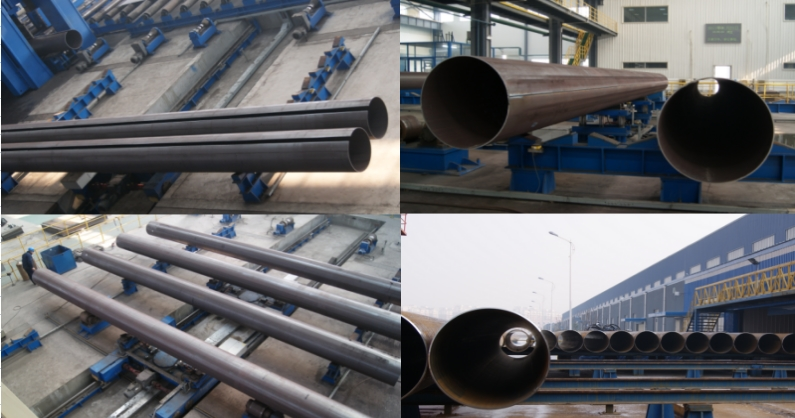
What is the difference between SSAW ,LSAW and ERW steel pipes ?
July 19, 2023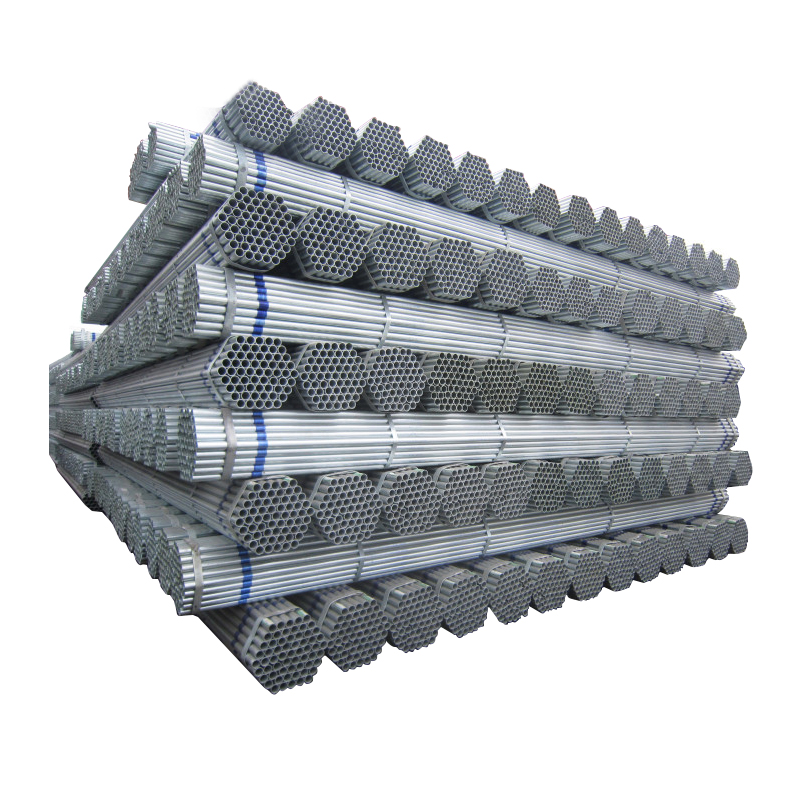
what is the difference between galvanized steel pipe and Zinc Plated steel pipe
July 25, 2023What is the FBE, 2PE, 3LPE, Anti-Corrosion Coating Steel Pipe
Anti-corrosion coating is an essential process in the construction of steel pipes. These coatings serve as a barrier layer that protects the steel from the corrosive effects of water, soil, and other environmental factors, significantly enhancing the pipe’s durability and lifespan. Three commonly used anti-corrosion coatings are FBE (Fusion Bonded Epoxy), 2PE (Two-layer Polyethylene), and 3LPE (Three-layer Polyethylene).
1. FBE (Fusion Bonded Epoxy) Coating
FBE is a high-performance anti-corrosion coating that provides excellent protection for small and large diameter pipelines with moderate operating temperatures. Its key characteristics include:
- Good adhesion to steel and resistance to cathodic disbondment
- High electrical resistance and low permeability to water and water vapor
- Resistance to harmful effects of soil and different environments
The FBE layer in FBE coated pipes is thermosetting, meaning it’s cured by heat.
2. 2PE (Two-layer Polyethylene) Coating
2PE anti-corrosion coating consists of two layers: The first layer (or the inner layer) is FBE, and the second layer (or the outer layer) is adhesive (AD) and a polyethylene (PE) layer. The 2PE anti-corrosion layer combines the excellent properties of FBE and the advantages of PE, including:
- Excellent water resistance, flexibility, and high-temperature resistance
- Strong resistance to impact and bending, making it highly suitable for environments with high soil stress
3. 3LPE (Three-layer Polyethylene) Coating
The 3LPE system is a multilayer coating composed of three functional components: a high-performance fusion-bonded epoxy (FBE), followed by a copolymer adhesive and an outer layer of polyethylene. The three layers combined provide excellent protection against corrosion and mechanical damage.
- The first layer, FBE, provides excellent adhesion to the steel pipe
- The second layer, the copolymer adhesive, acts as a link between the FBE and the PE layer
- The third layer, PE, provides good resistance to mechanical damage and water absorption
3LPE provides excellent protection against extreme environmental conditions and aggressive substances.
These three coatings are widely used due to their excellent performance in preventing corrosion, extending the life of pipes, and reducing the potential for leaks and failures in the pipeline systems.
Details:
Coating | FEB, 2PE/3LPE, 3PP, HDPE, Cement Mortar lining |
Coating Standard | DIN30670, CSA, Z245.21, CSA Z245.20, AS1518, AWWA C213 |
Process | LSAW: Longitudinal Submerge-arc Welded) UO(UOE),RB(RBE),JCO(JCOE) DSAW: Double Submerged arc welded SSAW: Spiral Submerge arc welded ERW: Electric Resistance welded pipe Seamless: Seamless |
Ends | Plain ends, Beveled ends |
Delivery | Depends on the order quantity, normal within 30 days |
Payment | T/T, L/C, Western Union |
Packing | Bundled, In Bulk, Plastic caps plugged, Waterproof paper wrapped etc. |
Application | Oil pipeline, Natural gas industry, Refineries, Sewage treatment facilities, Water treatment applications, Electric power plants, Food handling industry, Waterworks pipelines etc |
Tests of LSAW steel pipe | Chemical Component Analysis; Mechanical Properties–Elongation; Yield Strength; Ultimate tensile strength; Technical Properties–Flattening test; Bending test; Blow test; Impact test; X-ray Test Hydrostatic test |
Sizes:
O.D. | 219mm -4064mm (8″ to 160″) |
W.T. | 2.9mm-60mm |
Length | SRL, DRL, Random length from 1M to 18M |
Standard & Grade:
API 5L PLS1 & PLS2 | Gr.B, X42, X52, X60, X65, X70, X80,Q235B, Gr.C |
GB/T9711 | L175, L210, L245, L290, L320, L360, L390, L415, L450, L4785, L555 |
ASTM A252 | Gr.2, Gr.3 |
ASTM A53 | Gr.A, Gr.B, Gr.C, Gr.D |
EN10217 & EN10219 | S185, S235,S235JR, S235 G2H, S275, S275JR, S355JRH, S355J2H, St12, St13, St14, St33, St37, St44, ST52 |
ISO 3183 | / |
GB | Q195, Q215, Q235, Q275, Q295, Q345, 10#, 20#, 08F, 08, 08AL, 08F, 10F, 10, HG5, DF08 SPHC, M8 |
Part of detailed descriptions on coatings;
1) FBE–Fusion Bonded Epoxy Coating
FBE Technical Parameter | |
Capability/Property | FBE |
Minimum recommended handling and construction temperature | -30ºC |
Maximum recommended operating temperature | 110ºC |
Bendability | Yes |
2) 2PE/3PE anti-corrosive pipe–2/3 Layer Polyethylene coating
Two Layer Polyethylene coating | The first layer adhesive (AD) |
The second layer of polyethylene (PE) | |
Three Layer Polyethylene coating | The first layer with epoxy powder (FBE> 100um) |
The second layer with adhesive (AD), 170-250um | |
The third layer with polyethylene (PE) 2.5-3.7mm |
Size: DN50-DN2200
DN | Polyethylene | Polypropylene |
≤ 100 | 2.5mm | 1.8mm |
>100 and ≤ 250 | 2.7mm | 2.0mm |
>250 and ≤500 | 2.9mm | 2.2mm |
>500 and ≤800 | 3.2mm | 2.5mm |
>800 | 3.7mm | 2.5mm |