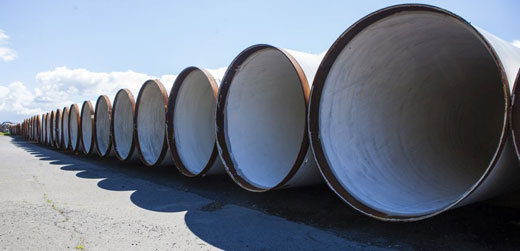
FBE | 2PE | 3LPE | Anti corrosion coating steel pipe
July 19, 2023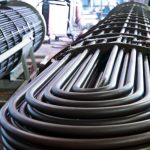
Stainless Steel Heat Exchanger U Bend pipe | SS 304 316
July 25, 2023Both galvanized steel pipe and zinc-plated steel pipe are methods of applying a layer of zinc to steel in order to prevent rusting and corrosion. However, the methods used to apply the zinc and their applications differ.
Galvanized Steel Pipe
Galvanized steel pipe is made by dipping steel pipe into a vat of molten zinc. This process is called “hot-dip galvanizing”. The zinc forms a thick and durable layer over the steel that is highly resistant to corrosion and rust.
- Durability: The galvanization process forms a coating that is bonded metallurgically to the steel, resulting in a highly durable finish.
- Thickness: The zinc coating is typically much thicker than with zinc plating. This makes galvanized steel pipes ideal for outdoor applications and in harsh environments where the steel needs to withstand elements such as water, soil, and harsh weather.
- Color: Galvanized steel tends to be duller and have a rougher surface due to the thick zinc coating.
Zinc-Plated Steel Pipe
Zinc plating, also known as electroplating, is a process where zinc is applied by using an electric current. The steel pipe is placed in a solution of zinc salts and an electric current is run through the solution, causing the zinc to bond to the steel. This creates a thin, smooth layer of zinc on the surface of the steel.
- Smoothness: Zinc-plated parts have a smoother and shinier finish than galvanized parts. This makes them more suitable for applications where aesthetics are important.
- Thickness: The zinc layer in zinc-plated pipes is much thinner than in galvanized pipes. This means it provides less protection against corrosion. For this reason, zinc-plated steel is typically used for indoor applications or where the steel is not exposed to harsh environmental conditions.
- Cost: Zinc plating is usually less expensive than galvanizing, but it also provides less protection.
In summary, the primary differences between galvanized and zinc-plated steel pipe lie in the method of application, the thickness and durability of the zinc layer, and their appropriate uses based on these factors.
Hot Dipped Galvanized Steel Pipe
1. Galvanzied Steel Pipe Parameter
Shape | Square:20*20-200*200mm |
Rectangular :30*20-250*150mm | |
Thickness | 1.0-12.0mm |
Length | 3-12m,or as per your request |
Technique | Hot Rolled, Cold Rolled,ERW,High-frequency welded,Extruded |
Surface | Bared, Oil, Galvanized, Paint,etc |
Standard | GB/T3094-2000,GB/T6728-2002,ASTM A500,JIS G3466,DIN EN10210,or others |
Material | Q195,Q235,Q275,Q345,S355,St33,St37,St52A500,A513,A106 and so on |
Certification | ISO9001:2000,CE,SGS |
Package | Wooden box,steel strip,pallet,or as your request |
Productivity | 15000tons/month |
Usage | Machinery manufacture,Roads and Bridges,Construction,Transportation |
What Are The Different Galvanisation steel pipe Processes and Zinc-Plated Steel Pipe Processes ?
Galvanization and zinc plating are both processes that coat a layer of zinc onto a steel surface to protect it against corrosion. However, they use different methods to achieve this.
Galvanization Processes
There are several types of galvanization:
- Hot-Dip Galvanizing (HDG): The most common method, where the steel is cleaned and then submerged in a bath of molten zinc. The zinc reacts with the steel to form a series of zinc-iron alloy layers, which are covered by a layer of pure zinc. This process is typically used for larger items, such as steel beams or pipes, and provides a thick, durable zinc coating.
- Pre-Galvanizing: In this method, steel sheets are rolled through a cleaning process and then into a bath of molten zinc. The sheets are then rolled flat while the zinc is still liquid. This process provides a thinner coating than hot-dip galvanizing and is typically used for steel sheets that will be further processed into products like ductwork, or that will be painted or powder-coated.
- Electro-Galvanizing: This is a form of electroplating. The steel is placed in an electrolyte solution, and an electric current is used to deposit zinc onto the steel. This provides a very thin, smooth coating and is often used for items that require a high aesthetic finish, such as automotive parts.
Zinc-Plating Processes
The common process for zinc plating is electroplating, also known as zinc electro-deposition:
- Electroplating: The steel part is cleaned and then placed in a bath containing a solution of zinc ions. An electric current is applied, causing the zinc ions to react with the steel and form a thin layer of zinc. The thickness of the layer can be controlled by adjusting the voltage and time. This process provides a thinner, less-durable coating than galvanizing, but it is smoother and shinier, making it more suitable for decorative applications, or for parts that will be exposed to less harsh environments.
It’s important to note that both galvanization and zinc plating require proper surface preparation, such as degreasing and pickling, to ensure good adhesion of the zinc layer to the steel. The choice between galvanizing and zinc plating depends on the intended use of the product, with galvanizing typically chosen for its superior corrosion resistance, and zinc plating for its lower cost and better finish.