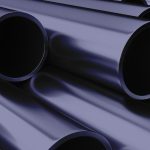
Difference Between Inconel Alloy 600 and Incoloy Alloy 800 Steel Pipes
November 20, 2024ASTM A234 WP11 Chemical composition and mechanical properties
November 28, 2024
Structural Design of Pipeline Casing Pipes: A Comprehensive Guide
Introduction
The structural design of pipeline casing pipes is a critical aspect of engineering in industries such as oil and gas, water supply, and utilities. Casing pipes serve as protective enclosures for pipelines, shielding them from external loads, environmental factors, and physical damage. They are essential for ensuring the safety, durability, and functionality of pipelines in challenging conditions, such as road crossings, railways, or areas with unstable soil.
This article provides an in-depth exploration of the structural design principles, materials, standards, and applications of pipeline casing pipes. We will also discuss the factors influencing their design, the calculation of loads, and best practices to ensure optimal performance and longevity.
What Are Pipeline Casing Pipes?
Pipeline casing pipes are large-diameter steel pipes or other durable materials that encase and protect smaller carrier pipelines. They are typically installed in areas where the carrier pipeline is exposed to external forces, such as:
- Road and Railway Crossings: To prevent damage from traffic loads.
- Boreholes and Tunnels: For added protection in underground installations.
- Corrosive Environments: To shield pipelines from chemical or environmental degradation.
Key Functions of Casing Pipes
- Protection: Safeguard the carrier pipeline from external loads, corrosion, and physical damage.
- Load Distribution: Distribute external loads, such as traffic or soil pressure, over a wider area.
- Environmental Isolation: Provide a barrier against environmental factors, such as groundwater or chemicals.
- Ease of Maintenance: Allow for the removal or replacement of the carrier pipeline without disturbing the surrounding environment.
Materials for Pipeline Casing Pipes
The selection of materials for casing pipes depends on the application, environmental conditions, and structural requirements. Common materials include:
1. Carbon Steel
- Advantages: High strength, durability, and cost-effectiveness.
- Applications: Widely used in oil and gas pipelines, road crossings, and industrial installations.
- Standards: Manufactured according to standards such as API 5L or ASTM A252.
2. Stainless Steel
- Advantages: Excellent corrosion resistance and durability in harsh environments.
- Applications: Used in corrosive environments, such as chemical plants or offshore installations.
3. HDPE (High-Density Polyethylene)
- Advantages: Lightweight, corrosion-resistant, and easy to install.
- Applications: Suitable for low-pressure applications or non-structural casing.
4. Concrete
- Advantages: High compressive strength and resistance to environmental factors.
- Applications: Used in large-diameter pipelines or areas with high external loads.
Standards and Codes for Casing Pipe Design
The structural design of casing pipes must comply with industry standards and codes to ensure safety and reliability. Common standards include:
- API 5L: Specifies requirements for steel casing pipes used in oil and gas pipelines.
- ASTM A252: Covers the design and manufacturing of welded and seamless steel pipes for structural applications.
- AWWA C200: Provides guidelines for steel water pipes.
- ASME B31.4: Covers pipeline transportation systems for liquids and slurries.
- AREMA Guidelines: Used for casing pipes under railways.
Factors Influencing the Structural Design of Casing Pipes
The structural design of casing pipes involves several factors to ensure they can withstand external loads and environmental conditions. Key considerations include:
1. External Loads
Casing pipes must be designed to withstand various external loads, including:
- Traffic Loads: Dynamic and static loads from vehicles or trains passing above the pipeline.
- Soil Pressure: Lateral and vertical pressure from surrounding soil.
- Hydrostatic Pressure: Pressure from groundwater or other fluids around the casing.
2. Pipe Diameter and Wall Thickness
The diameter and wall thickness of the casing pipe are critical for its structural integrity. Larger diameters and thicker walls are required for high-load or high-pressure applications.
3. Corrosion Resistance
Casing pipes must be resistant to corrosion caused by environmental factors, such as groundwater, chemicals, or salt. Protective coatings, cathodic protection, or corrosion-resistant materials may be used.
4. Installation Method
The method of installation affects the design of casing pipes. Common methods include:
- Open Cut: Involves digging a trench to install the casing pipe.
- Horizontal Directional Drilling (HDD): Used for trenchless installations, such as under roads or rivers.
- Jack and Bore: Involves jacking the casing pipe into place while boring through the soil.
5. Temperature and Pressure
The design must account for temperature fluctuations and internal or external pressures that may affect the casing pipe’s performance.
Structural Design Principles for Casing Pipes
The structural design of casing pipes involves calculating the loads and stresses they will encounter and ensuring they meet the required safety factors. Key design principles include:
1. Load Analysis
Casing pipes must be designed to withstand the following loads:
- Dead Load: The weight of the soil and any structures above the pipe.
- Live Load: Dynamic loads from vehicles, trains, or equipment.
- Impact Load: Sudden loads caused by equipment or environmental events.
- Thermal Load: Stresses caused by temperature changes.
2. Stress Analysis
The pipe must be analyzed for the following types of stress:
- Axial Stress: Caused by longitudinal forces.
- Hoop Stress: Caused by internal or external pressure.
- Bending Stress: Caused by uneven loads or soil movement.
3. Wall Thickness Calculation
The required wall thickness of the casing pipe is determined using formulas from industry standards, such as:
t = (P × D) / (2 × S × F)
Where:
- t = Wall thickness
- P = External pressure
- D = Outer diameter
- S = Allowable stress
- F = Safety factor
4. Deflection and Buckling
The design must ensure that the casing pipe does not deflect or buckle under external loads. Finite element analysis (FEA) or other simulation tools may be used to evaluate these risks.
Best Practices for Casing Pipe Design and Installation
To ensure the optimal performance and longevity of casing pipes, follow these best practices:
1. Material Selection
Choose materials that meet the specific requirements of the application, including strength, corrosion resistance, and cost-effectiveness.
2. Protective Coatings
Apply protective coatings, such as fusion-bonded epoxy (FBE) or polyethylene, to prevent corrosion and extend the pipe’s lifespan.
3. Cathodic Protection
Use cathodic protection systems to prevent corrosion in underground or submerged installations.
4. Proper Bedding and Backfill
Ensure proper bedding and backfill materials are used to distribute loads evenly and prevent pipe deformation.
5. Regular Inspection and Maintenance
Perform regular inspections to identify and address issues such as corrosion, deformation, or damage.
Applications of Pipeline Casing Pipes
Pipeline casing pipes are used in a variety of applications across different industries, including:
1. Oil and Gas
- Protecting pipelines in road and railway crossings.
- Shielding pipelines in offshore installations.
2. Water Supply
- Encasing water pipelines in urban areas to prevent damage from traffic or construction.
3. Telecommunications
- Housing cables and conduits in underground installations.
4. Railway and Highway Crossings
- Providing structural protection for pipelines under heavy traffic loads.
Conclusion
The structural design of pipeline casing pipes is a critical aspect of ensuring the safety, durability, and functionality of pipelines in challenging environments. By considering factors such as external loads, material selection, and installation methods, engineers can design casing pipes that meet the specific requirements of their applications.
Whether used in oil and gas, water supply, or telecommunications, casing pipes play a vital role in protecting pipelines and ensuring their long-term performance. By following industry standards and best practices, you can ensure the success of your pipeline projects.
FAQ
1. What is the purpose of pipeline casing pipes?
Pipeline casing pipes protect carrier pipelines from external loads, corrosion, and physical damage, ensuring their safety and functionality.
2. What materials are used for casing pipes?
Common materials include carbon steel, stainless steel, HDPE, and concrete, depending on the application and environmental conditions.
3. How are casing pipes installed?
Casing pipes can be installed using methods such as open cut, horizontal directional drilling (HDD), or jack and bore.
4. How is the wall thickness of a casing pipe determined?
The wall thickness is calculated based on external pressure, pipe diameter, allowable stress, and safety factors, using formulas from industry standards.
5. What standards govern the design of casing pipes?
Standards such as API 5L, ASTM A252, AWWA C200, and ASME B31.4 provide guidelines for the design and manufacturing of casing pipes.