-steel-pipe-150x150.jpg)
ASTM A335 P91 10Cr9Mo1VNbN Alloy Steel Pipe – Research on Welding and Heat Treatment Process
October 15, 2024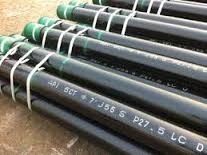
J55 Casing Pipe Expansion Properties
October 28, 2024Internal Corrosion in Oil and Gas Wells: Challenges and Opportunities of Corrosion Inhibitors
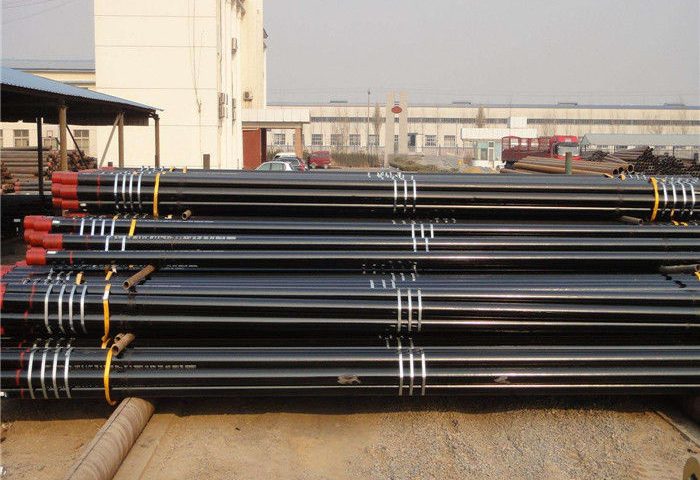
Seamess Casing Pipe, Tubing Pipe, Api Casing Pipes manufacturer / supplier in China, offering API Casing Pipe & Tubing Pipe (J55/ K55/ N80/ L80/ P110/ C95), API-5CT OCTG Casing Pipe&Tubing Pipe for Oilfield Service, Octg Tubing Pipe (API-5CT Oilfield...
Internal Corrosion in Oil and Gas Wells: Challenges and Opportunities of Corrosion Inhibitors
Introduction
In the oil and gas industry, managing the integrity of wells is crucial for operational efficiency and safety. Among the various challenges faced, internal corrosion of casings and tubing stands out as a significant concern. This phenomenon not only threatens the structural integrity of the wells but also poses environmental and economic risks. Corrosion inhibitors have emerged as a vital solution to mitigate these issues, offering both challenges and opportunities for innovation and application.
Understanding Internal Corrosion
Internal corrosion in oil and gas wells occurs when the metal surfaces of casings and tubing react with corrosive agents present in the well environment. These agents typically include carbon dioxide (CO2), hydrogen sulfide (H2S), and chlorides, which are prevalent in oil and gas reservoirs. The presence of water further exacerbates the situation, creating an electrolyte that facilitates electrochemical reactions leading to corrosion.
Types of Corrosion
- Uniform Corrosion: This is a widespread form of corrosion where the metal surface corrodes at a consistent rate. Although it is predictable, it can lead to significant material loss over time.
- Localized Corrosion: This includes pitting and crevice corrosion, where small areas of the metal surface corrode at a much faster rate than the rest. This type of corrosion is particularly dangerous as it can lead to sudden failures.
- Galvanic Corrosion: Occurs when two dissimilar metals are in contact in the presence of an electrolyte, leading to accelerated corrosion of the more anodic metal.
- Stress Corrosion Cracking (SCC): This is a result of the combined effect of tensile stress and a corrosive environment, leading to the formation of cracks.
Challenges in Managing Internal Corrosion
Managing internal corrosion in oil and gas wells is fraught with challenges, ranging from detection and monitoring to the effective application of corrosion inhibitors.
Detection and Monitoring
Detecting internal corrosion is a complex task due to the harsh and inaccessible environment of oil and gas wells. Traditional methods such as ultrasonic testing and radiography have limitations in terms of accuracy and feasibility. Newer technologies like smart sensors and real-time monitoring systems are being developed, but they require significant investment and expertise.
Selection of Corrosion Inhibitors
Choosing the right corrosion inhibitor is critical and depends on several factors, including the type of corrosion, the composition of the well fluids, temperature, and pressure conditions. The inhibitor must be compatible with the well environment and should not interfere with the production process.
Application and Delivery
The effective delivery of corrosion inhibitors to the target areas within the well is another challenge. This requires a thorough understanding of the well’s flow dynamics and the behavior of the inhibitor under various conditions. Techniques such as continuous injection, batch treatment, and squeeze treatment are commonly used, each with its own set of advantages and limitations.
Environmental and Safety Concerns
The use of chemical inhibitors raises environmental and safety concerns. Many inhibitors are toxic and pose risks to both human health and the environment. Therefore, there is a growing demand for environmentally friendly inhibitors that are biodegradable and non-toxic.
Opportunities in Corrosion Inhibition
Despite the challenges, the field of corrosion inhibition presents numerous opportunities for innovation and improvement.
Advanced Materials and Formulations
Research is ongoing to develop advanced materials and formulations that offer superior corrosion protection. This includes the use of nanotechnology to enhance the properties of inhibitors and the development of multi-functional inhibitors that can address multiple types of corrosion simultaneously.
Green Chemistry
The push towards sustainability has led to the exploration of green chemistry in corrosion inhibition. Natural extracts and biodegradable polymers are being investigated as potential inhibitors that are both effective and environmentally benign.
Smart Inhibitors
The concept of smart inhibitors that can respond to changes in the well environment is gaining traction. These inhibitors can adjust their activity based on factors such as pH, temperature, and the presence of specific ions, providing targeted protection.
Integration with Digital Technologies
The integration of corrosion inhibition strategies with digital technologies offers exciting possibilities. The use of data analytics, machine learning, and artificial intelligence can enhance the prediction and monitoring of corrosion, leading to more informed decision-making and optimized inhibitor application.
Case Studies and Applications
Several case studies highlight the successful application of corrosion inhibitors in oil and gas wells. For instance, the use of a specific inhibitor formulation in a high-CO2 environment resulted in a significant reduction in corrosion rates, extending the lifespan of the well components. Another example involves the application of a biodegradable inhibitor in an offshore well, demonstrating both effectiveness and environmental compliance.
Conclusion
Internal corrosion in oil and gas wells is a complex challenge that requires a multifaceted approach. Corrosion inhibitors play a crucial role in mitigating this issue, offering both challenges and opportunities. By embracing advanced materials, green chemistry, smart technologies, and digital integration, the industry can enhance the effectiveness of corrosion inhibition strategies, ensuring the integrity and sustainability of oil and gas operations.
Future Directions
Looking ahead, the focus should be on developing inhibitors that are not only effective but also sustainable. Collaboration between industry, academia, and regulatory bodies will be essential to drive innovation and establish best practices. As technology continues to evolve, the potential for more sophisticated and efficient corrosion management solutions will undoubtedly grow, paving the way for a safer and more sustainable oil and gas industry.