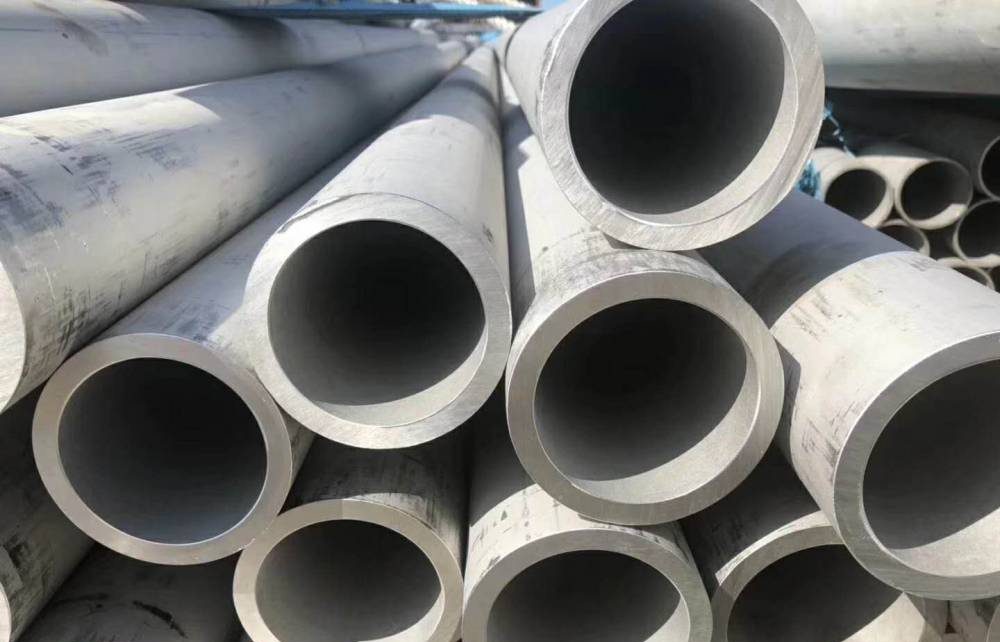
difference between A312 stainless steel pipe and TP304L seamless pipe?
February 13, 2023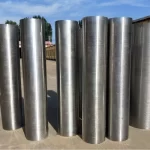
Wire Wound Screen (Filter Pipe)
February 17, 2023EN 10216 Steel Pipe vs ASTM A333 Alloy Pipe
The differences between EN 10216 steel pipe and ASTM A333 alloy pipe are vast and numerous, but the primary differences lie in their chemical composition and mechanical properties. EN 10216 is a standard for seamless steel pipes that are used for pressure applications, while ASTM A333 is a standard for welded and seamless alloy steel pipes. Both are used primarily in the industrial and energy sectors.
Chemical Composition
The chemical composition of EN 10216 steel pipe and ASTM A333 alloy pipe differ significantly. EN 10216 steel pipe contains carbon, silicon, manganese, phosphorus, sulfur, chromium, nickel, molybdenum, copper, and vanadium. ASTM A333 alloy pipe contains carbon, manganese, phosphorus, sulfur, silicon, chromium, molybdenum, and nickel.
Mechanical Properties
The mechanical properties of EN 10216 steel pipe and ASTM A333 alloy pipe also differ significantly. The EN 10216 steel pipe has a maximum yield strength of 295 MPa and a minimum yield strength of 240 MPa. The ASTM A333 alloy pipe has a maximum yield strength of 415 MPa and a minimum yield strength of 205 MPa.
Additionally, the EN 10216 steel pipe has a maximum tensile strength of 530 MPa and a minimum tensile strength of 415 MPa. The ASTM A333 alloy pipe has a maximum tensile strength of 690 MPa and a minimum tensile strength of 485 MPa.
The EN 10216 steel pipe has an elongation of 22% at a gauge length of 50mm, while the ASTM A333 alloy pipe has an elongation of 25% at a gauge length of 50mm. The EN 10216 steel pipe has an impact energy of 27 Joules at -20°C, while the ASTM A333 alloy pipe has an impact energy of 27 Joules at -20°C.
Applications
The applications of EN 10216 steel pipe and ASTM A333 alloy pipe also differ significantly. EN 10216 steel pipe is used primarily in the industrial and energy sectors for boilers, heat exchangers, and condensers. ASTM A333 alloy pipe is used primarily in the automotive and construction industries for structural components, such as pipes, tubes, and valves.
Conclusion
The differences between EN 10216 steel pipe and ASTM A333 alloy pipe are vast and numerous. EN 10216 steel pipe is typically used in the industrial and energy sectors for boilers, heat exchangers, and condensers, while ASTM A333 alloy pipe is typically used in the automotive and construction industries for structural components. The chemical composition and mechanical properties of these two types of pipes differ significantly.
EN 10216-2 Chemical Composition:
Steel grades | EN10216-2 CHEMICAL COMPOSITION (LADLE ANALYSIS) | |||||||||||||
---|---|---|---|---|---|---|---|---|---|---|---|---|---|---|
C% max | Si% max | Mn% max | P% max | S% max | Cr% max | Mo% max | Ni% max | Al.cał% min | Cu% max | Nb% max | Ti% max | V% max | Cr+ Cu+ Mo+ Ni% MAX | |
P195GH | 0.13 | 0.35 | 0.70 | 0.025 | 0.020 | 0.30 | 0.08 | 0.30 | ≥ 0.020 | 0.30 | 0.010 | 0.040 | 0.02 | 0.70 |
P235GH | 0.16 | 0.35 | 1,20 | 0.025 | 0.020 | 0.30 | 0.08 | 0.30 | ≥ 0.020 | 0.30 | 0.010 | 0.040 | 0.02 | 0.70 |
P265GH | 0.20 | 0.40 | 1,40 | 0.025 | 0.020 | 0.30 | 0.08 | 0.30 | ≥ 0.020 | 0.30 | 0.010 | 0.040 | 0.02 | 0.70 |
16Mo3 | 0.12- 0.20 | 0.35 | 0.40- 0.70 | 0.025 | 0.020 | 0.30 | 0.25- 0.35 | 0.30 | ≥ 0.020 | 0.30 | – | – | – | – |
14MoV6-3 | 0.10- 0.15 | 0.15- 0.35 | 0.40- 0.70 | 0.025 | 0.020 | 0.30- 0.60 | 0.50- 0.70 | 0.30 | ≥ 0.020 | 0.30 | – | 0.22-0.28 | – | – |
13CrMo4-5 | 0.15 | 0.50- 1,00 | 0.30- 0.60 | 0.025 | 0.020 | 1,00- 1,50 | 0.45- 0.65 | 0.30 | ≥ 0.020 | 0.30 | – | – | – | – |
10CrMo9-10 | 0.10- 0.17 | 0.35 | 0.40- 0.70 | 0.025 | 0.020 | 0.70- 1,15 | 0.40- 0.60 | 0.30 | ≥ 0.020 | 0.30 | – | – | – | – |
EN 10216-2 Mechanical Property:
EN 10216-2 Mechanical properties | |||||||||||||
---|---|---|---|---|---|---|---|---|---|---|---|---|---|
Steel grades | Mechanical properties during tensile testing in room temperature | Resilience | |||||||||||
Upper yield limit or yield strength Re or R0.2 for wall thickness of t min | Tensile strength Rm | Elongation A min% | Minimum energy average absorbed KVJ at the temperature of 0°C | ||||||||||
T≤16 | 16<T≤40 | 40<t≤60 | 60<T≤60 | I | T | ||||||||
MPa | MPa | MPa | MPa | MPa | I | t | 20 | 0 | -10 | 20 | 0 | ||
P195GH | 195 | – | – | – | 320- 440 | 27 | 25 | – | 40 | 28 | – | 27 | |
P235GH | 235 | 225 | 215 | – | 360- 500 | 25 | 23 | – | 40 | 28 | – | 27 | |
P265GH | 265 | 255 | 245 | – | 410- 570 | 23 | 21 | – | 40 | 28 | – | 27 | |
16Mo3 | 280 | 270 | 260 | – | 450- 600 | 22 | 20 | 40 | – | – | 27 | – | |
14MoV6-3 | 320 | 320 | 310 | – | 460- 610 | 20 | 18 | 40 | – | – | 27 | – | |
13CrMo4-5 | 290 | 290 | 280 | – | 440- 590 | 22 | 20 | 40 | – | – | 27 | – | |
10CrMo9-10 | 280 | 280 | 270 | – | 480- 630 | 22 | 20 | 40 | – | – | 27 | – |
EN 10216-2 Equivalent steel grade:
Steel Grade | Steel Standard | Steel Grade | Steel Standard | Steel Grade |
---|---|---|---|---|
P235GH | DIN 17175 | St 35.8 | ||
P265GH | DIN 17175 | St 45.8 | ||
16Mo3 | DIN 17175 | 15Mo3 | ||
10CrMo55 | 15Mo3 | BS 3606 | 621 | |
13CrMo45 | DIN 17175 | BS 3606 | 620 | |
10CrMo910 | DIN 17175 | 13CrMo44 | BS 3606 | 622 |
25CrMo4 | 10CrMo910 | |||
P355N | DIN 17179 | StE 355 | ||
P355NH | DIN 17179 | TStE 355 | ||
P355NL1 | DIN 17179 | WStE 460 | ||
P460N | DIN 17179 | TStE 460 | ||
P460NH | DIN 17179 | WStE 460 | ||
P460NL1 | DIN 17179 | TStE 460 |
ANSON can supply EN 10216-2 steel pipe from stock or from reputed steel mills. We also offer steel fabrication service where steel tube can go through processings like cutting, welding, bending, machining, pre-coating, pre-lined, beveling, or as you require. Our steel mills have fabricating employees that have 5-10 years of working experience. If you are interested in buying EN10216-2 steel pipe products, contact us now for the latest price or check the following table for equivalent steel grade of EN10216-2.
Dimension for EN10216-2 Steel pipe
EN 10216-2 Outside diameter and wall thickness tolerances | |||||
---|---|---|---|---|---|
Outside diameter D mm | Permissible deviations of outside diameter D | Permissible deviations of wall thickness t depending on the T/D ratio | |||
≤0.025 | >0.025 ≤0.050 |
>0.050 ≤0.10 |
>0.10 | ||
D≤219,1 | +\- 1% or =\- 0.5mm depending on which is greater | +\- 12,5% or 0.4 mm depending on which is greater | |||
D>219,1 | =\- 20% | =\- 15% | =\- 12,5% | =\- 10% | |
For the outside diameter of D≥355,6 mm, local deviation outside of the upper deviation limit by further 5% of the wall thickness T is permitted |
EN 10216-2 Inside diameter and wall thickness tolerances | |||||
---|---|---|---|---|---|
Permissible deviations of inside diameter | Permissible T deviations depending on the T/d ratio | ||||
d | dmin | <\-0.03 | >0.03 ≤0.06 |
>0.06 ≤0.12 |
>0.12 |
+\- 1% or +\- 2mm depending on which is greater | +2% +4mm depending on which is greater |
+\-20% | +\-15% | +\-12,5% | +\-10% |
For the outside diameter of D≥355,6 mm, local deviation outside of the upper deviation limit by further 5% of the wall thickness T is permitted |
Inspection and Test For EN 10216-2 Steel Pipe
Inspection and test type | Test frequency | Test category | ||
---|---|---|---|---|
Mandatory tests | Ladle analysis | One per ladle | 1 | 2 |
Tensile testing in room temperature | One per every test pipe | X | X | |
Flattening test for D<600mm and the ratio of D≤0.15 but T≤40mm or ring testing for D>150mm and T ≤40mm | X | X | ||
Rolling test on a mandrel bar for D≤150mm and T≤10mm or ring testing for D≤114,3mm and T ≤12,5mm | X | X | ||
Resilience testing at the temperature of 20 ºC | X | X | ||
Tightness testing | Every pipe | X | X | |
Dimensional testing | X | X | ||
Visual inspection | X | X | ||
NDT in order to identify longitudinal discontinuity | Every pipe | X | X | |
Material identification for alloy steel | X | X | ||
Optional tests | Final product analysis | One per ladle | X | X |
Tensile testing at elevated temperature | One per ladle and for the same thermal processing conditions | X | X | |
Resilience testing | One per every test pipe | X | X | |
Resilience testing in the machine direction at the temperature of -10ºC for non-alloy steel grades | X | X | ||
Wall thickness measurement at a distance from pipe ends | X | X | ||
NDT in order to identify transverse discontinuity | Every pipe | X | X | |
NDT in order to identify delamination | X | X |
ASTM A333 Steel Pipe Surface inspection requirements
Surface imperfections that penetrate more than 12½ % of the nominal wall thickness or encroach on the minimum wall thickness shall be considered defects. ASTM A333 steel pipe with such defects shall be given one of the following dispositions:
- The defect may be removed by grinding provided that the remaining wall thickness is within specified limits.
- Repaired in accordance with the repair welding provisions.
- The section of pipe containing the defect may be cut off within the limits of requirements on length.
- The defective pipe may be rejected.
ASTM A333 Steel Pipe Chemical Composition:
Standard | Grade | Chemical Composition (%) | ||||||||||
---|---|---|---|---|---|---|---|---|---|---|---|---|
C | Si | Mn | P | S | Cr | Ni | Cu | Mo | V | Al | ||
ASTM A333 | Grade 1 | ≤0.30 | 0.40~1.06 | ≤0.025 | ≤0.025 | |||||||
Grade 3 | ≤0.19 | 0.18~0.37 | 0.31~0.64 | ≤0.025 | ≤0.025 | 3.18~3.82 | ||||||
Grade 4 | ≤0.12 | 0.18~0.37 | 0.50~1.05 | ≤0.025 | ≤0.025 | 0.44~1.01 | 0.47~0.98 | 0.40~0.75 | 0.04~0.30 | |||
Grade 6 | ≤0.30 | ≥0.10 | 0.29~1.06 | ≤0.025 | ≤0.025 | |||||||
Grade 7 | ≤0.19 | 0.13~0.32 | ≤0.90 | ≤0.025 | ≤0.025 | 2.03~2.57 | ||||||
Grade 8 | ≤0.13 | 0.13~0.32 | ≤0.90 | ≤0.025 | ≤0.025 | 8.40~9.60 | ||||||
Grade 9 | ≤0.20 | 0.40~1.06 | ≤0.025 | ≤0.025 | 1.60~2.24 | 0.75~1.25 | ||||||
Grade 10 | ≤0.20 | 0.10~0.35 | 1.15~1.50 | ≤0.03 | ≤0.015 | ≤0.15 | ≤0.25 | ≤0.015 | ≤0.50 | ≤0.12 | ≤0.06 | |
Grade 11 | ≤0.10 | ≤0.35 | ≤0.6 | ≤0.025 | ≤0.025 | ≤0.50 | 35.0~37.0 | ≤0.50 |
ASTM A333 Steel Pipe Mechanical Property:
Standard | Grade | Tensile Strength (MPa) | Yield Point (MPa) | Elongation (%) | |
---|---|---|---|---|---|
Y | X | ||||
ASTM A333 | Grade 1 | ≥380 | ≥205 | ≥35 | ≥25 |
Grade 3 | ≥450 | ≥240 | ≥30 | ≥20 | |
Grade 4 | ≥415 | ≥240 | ≥30 | ≥16.5 | |
Grade 6 | ≥415 | ≥240 | ≥30 | ≥16.5 | |
Grade 7 | ≥450 | ≥240 | ≥30 | ≥22 | |
Grade 8 | ≥690 | ≥515 | ≥22 | ||
Grade 9 | ≥435 | ≥315 | ≥28 | ||
Grade 10 | ≥550 | ≥450 | ≥22 | ||
Grade 11 | ≥450 | ≥240 | ≥18 |
ASTM A333 Steel Pipe Strike temperature condition:
Grade | The lowest temperature for strike test | |
---|---|---|
°F | °C | |
ASTM A333 Grade 1 | -50 | -45 |
ASTM A333 Grade 3 | -150 | -100 |
ASTM A333 Grade 4 | -150 | -100 |
ASTM A333 Grade 6 | -50 | -45 |
ASTM A333 Grade 7 | -100 | -75 |
ASTM A333 Grade 8 | -320 | -195 |
ASTM A333 Grade 9 | -100 | -75 |
ASTM A333 Grade 10 | -75 | -60 |