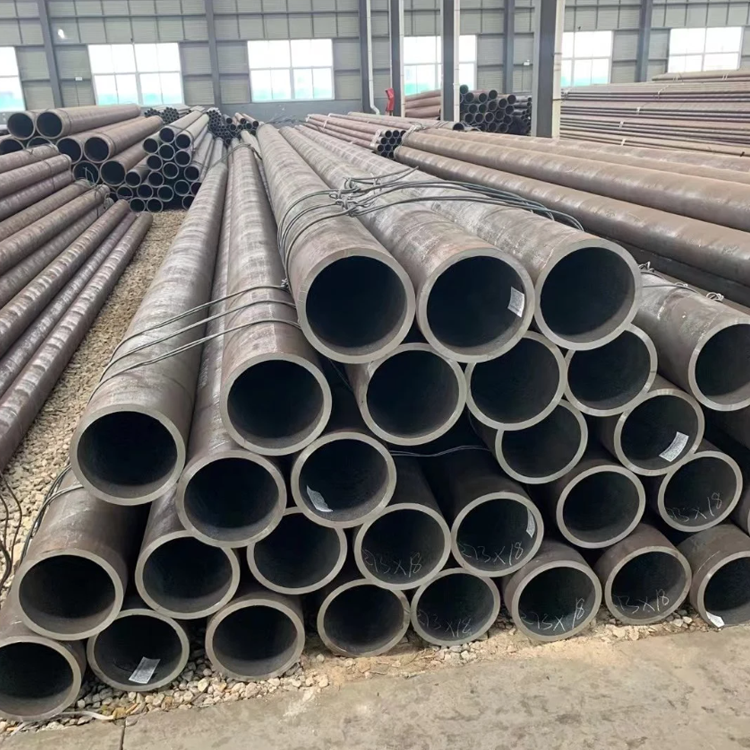
Structural Seamless Steel Pipe
August 22, 2023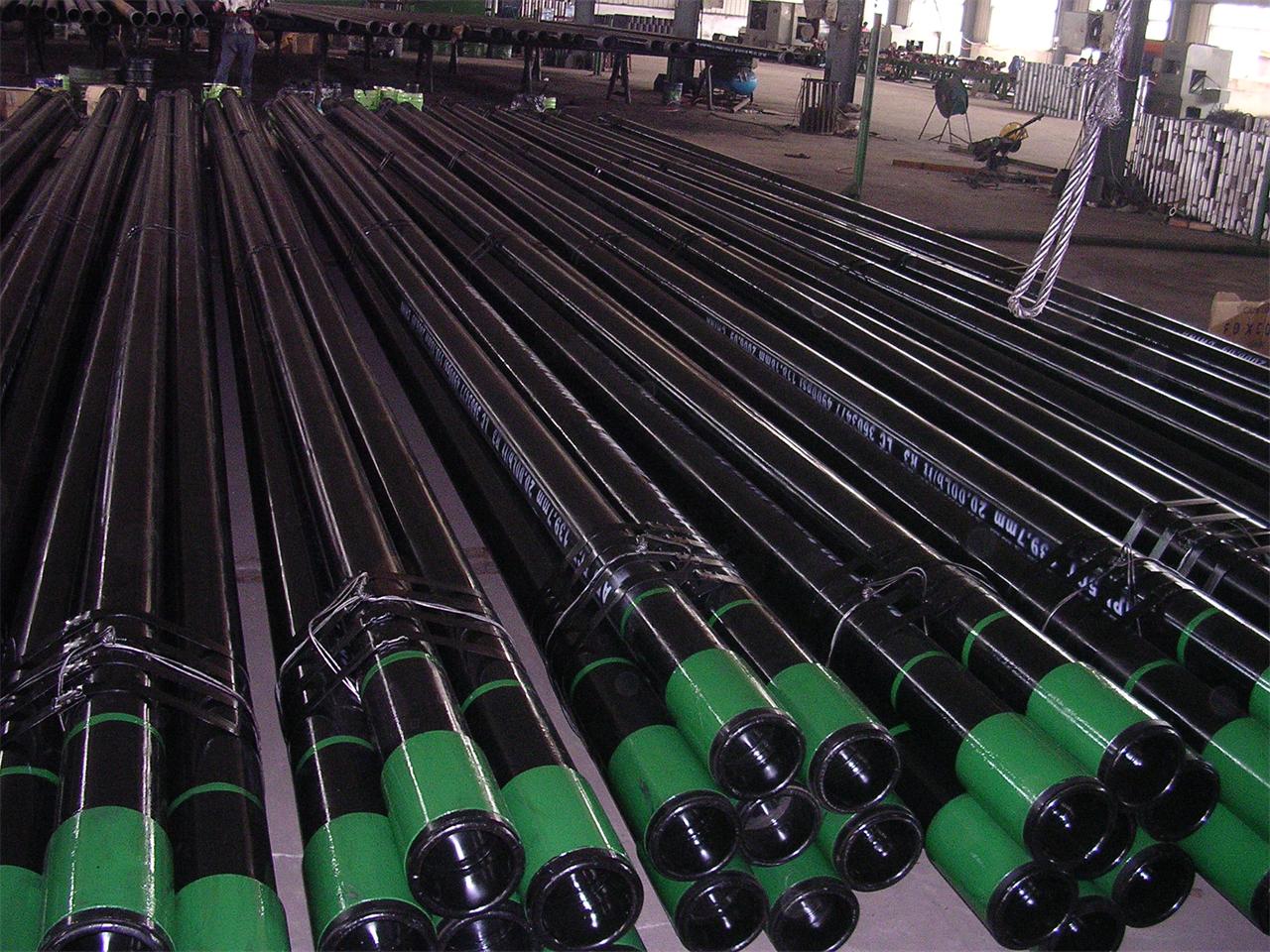
oil casing pipes heat treatment process,How are the oil casings inspected and tested to ensure their quality?
September 4, 2023Oil Casing with High Strength and Toughness and Production Method Thereof
Description
An oil casing with high strength and toughness is a critical component in oil and gas drilling operations. It is designed to withstand high pressure, abrasive materials, and corrosive environments, commonly encountered in drilling operations. The oil casing is often made out of steel and should have specific properties like high strength, toughness, and corrosion resistance.
Production Method
The production method involves several steps, including the selection of materials, heat treatment, forming, and inspection.
1. Material Selection
The base material for the casing is usually a high-quality carbon steel or alloy steel. The material is selected based on the expected conditions of the drilling operation, such as the temperature, pressure, and corrosive environment.
2. Forming
The steel is heated to a specific temperature and then formed into pipes. This is often done by hot rolling, where the steel is passed through a series of rollers that shape it into the desired pipe shape and size. The pipes are then cooled and hardened.
3. Heat Treatment
Next, the pipes undergo a heat treatment process. This can include quenching and tempering, which are used to increase the strength and toughness of the steel. Quenching involves heating the steel to a high temperature and then rapidly cooling it, while tempering involves heating the steel to a lower temperature and then slowly cooling it.
4. Inspection and Testing
Finally, the pipes are inspected and tested to ensure they meet the required standards. This can include visual inspections, hardness testing, and ultrasonic testing. If the pipes pass these tests, they are then ready to be used as oil casings.
This is a basic outline of how high strength and toughness oil casings are produced. The actual processes can be more complex and can vary depending on the specific requirements of the casing.
Advantages
- Increased Durability: The high strength and toughness of these oil casings allow them to withstand high pressure and abrasive materials, increasing their lifespan and reducing the need for replacements.
- Improved Safety: These properties also improve the safety of drilling operations, as they reduce the risk of casing failure, which can lead to catastrophic accidents.
- Cost-Effective: Although the production process may be more complex and costly, the increased durability and safety of these casings can lead to significant cost savings in the long run.
Conclusion
The production of oil casings with high strength and toughness is a critical aspect of ensuring safe and efficient drilling operations. While the production process can be complex, the benefits in terms of durability, safety, and cost savings make it a worthwhile investment.
The invention belongs to the technical field of manufacturing seamless steel pipes in the metallurgical industry, and in particular relates to an oil casing with super high strength and toughness suitable for deep wells or ultra-deep wells and a production method thereof.
Background technique
With the increase of drilling depth in oil and gas fields, the increase of temperature and pressure, the geological environment of petroleum casing used for fixed wellheads has changed significantly, and the mechanical conditions used have also changed accordingly. The external extrusion load it bears and axial loads are getting higher and higher. High-quality oil casings such as V125 specified by the American Petroleum Institute standard generally use Cr-Mo-V series alloy steels. Due to the complex smelting, rolling and heat treatment processes of oil casings of this steel type, the alloy composition and manufacturing process are not appropriate. , will cause the strength and toughness of the oil casing to decrease, and cannot withstand the external extrusion load and axial load brought by deep or ultra-deep wells, which will aggravate the damage and failure of the oil casing, and the damage and failure of the casing will easily lead to the failure of the wellbore. Complex problems such as instability, reservoir damage, drilling and cementing difficulties, etc., seriously threaten the safety of oilfield operations, and even lead to major economic losses such as well destruction accidents. Therefore, the oil field puts forward higher requirements on the performance of oil casing.
At present, the problem to be solved for oil casing for deep or ultra-deep wells is the matching of ultra-high strength and high toughness. The performance of high-strength and toughness oil casing is not only related to the material composition used, but also closely related to its manufacturing method. As we all know, the impact toughness of ultra-high-strength steel depends on the purity of the steel, the composition and refinement of the structure. Ultra-pure smelting technology is adopted to reduce the content of sulfur, phosphorus impurity elements and gases in ultra-high-strength steel as much as possible, and reduce the number of inclusions, so that satisfactory impact toughness can be obtained. Using an appropriate heat treatment process, the microstructure characterized by ultra-fine lath martensite as the matrix and dispersed austenite ductile phase is obtained in ultra-high strength steel, and obtained during the rolling and straightening process High-precision oil casing size and surface quality and low residual stress are the key technical and effective ways to achieve ultra-high strength and toughness oil casing.
However, the current steel grades used in oil casings contain high impurities such as sulfur and phosphorus, and the metal structure contains flaky inclusions. The uneven flow of metal during the rolling process results in inconsistent mechanical properties in the horizontal and vertical directions. Moreover, in the current oil casing production method, the quenching medium in the heat treatment process is water, which is easy to cause cracking. At the same time, due to the unreasonable piercing and rolling process, heat treatment process and straightening method, the best The strength and toughness of the casing match, and cause excessive residual stress, and the geometric dimension accuracy of the casing is poor, which directly affects the ability of the product to resist collapse.
Contents of the invention
The purpose of the invention is to overcome the deficiencies in the prior art and provide an oil casing with high strength and toughness that can meet the requirements of deep well or ultra-deep parallel production conditions in oil fields.
Another object of the present invention is to provide a production method of an oil casing with high strength and toughness, which can meet the production conditions of deep wells or ultra-deep wells in oil fields.
The present invention realizes through following technical scheme:
An oil casing with high strength and toughness, characterized in that the components by weight percentage are: C: 0.22-0.35%, Si: 0.17-0.30%, Mn: 0.45-0.60%, Cr: 0.80-1.10%, Mo: 0.70-1.10%, Al: 0.015-0.040%, Ni<0.20%, Cu<0.20%, V: 0.070-0.100%, Nb<0.050%, Ca<0.0015%, P<0.010%, S<0.003% , and the balance is iron.
The role of the main alloying elements is:
C: 0.22-0.35%. C is a carbide-forming element that can increase the strength of steel. If it is too low, the effect is not obvious, and if it is too high, it will greatly reduce the toughness of steel.
Mn: 0.45-0.60%, Mn is an austenite-forming element, which can improve the hardenability of steel, increase the amount of retained austenite in steel, and affect the uniformity of hot-rolled structure.
Cr: 0.80-1.10%. Chromium can improve the mechanical properties, corrosion resistance and hardenability of steel, but it can increase the temper brittleness of steel.
V: 0.070-0.100%, can refine grains, form carbides, and improve the strength and toughness of steel. But when the content reaches a certain amount, the increase in its effect will not be obvious. At the same time, because the price is high, the usage amount should be limited.
Mo: 0.70-1.10%, mainly through carbide and solid solution strengthening to increase the strength of steel, if the content is too high, the toughness of steel will be reduced.
Nb<0.050 mainly refines grains and significantly improves the toughness of high-strength steel.
Ni<0.20 mainly improves the strength and toughness of steel, improves the corrosion resistance of steel, and reduces the brittle transition temperature of steel.
Cu<0.20, copper in the alloy steel can improve the strength and atmospheric corrosion resistance of the steel, too much addition will make the steel brittle, generally not more than 0.2%.
In order to ensure excellent strength and toughness matching, the production method of the oil casing of the present invention comprises the following steps:
(1) Ingredients smelting: Sponge iron and scrap steel are used as raw materials for steelmaking, melted into molten steel in an electric arc furnace (EFA), and molten steel for manufacturing oil casings is obtained after refining outside the furnace (LF) and vacuum (VD) degassing The composition by weight percentage is: C: 0.22-0.35%, Si: 0.17-0.30%, Mn: 0.45-0.60%, Cr: 0.80-1.10%, Mo: 0.70-1.10%, Al: 0.015-0.040%, Ni< 0.20%, Cu<0.20%, V: 0.070-0.100%, Nb<0.050%, Ca<0.0015%, P<0.010%, S<0.003%, and the balance is iron.
(2) Continuous casting and rolling: The above-mentioned high-purity molten steel is continuously cast into a round billet, and the cooled continuous casting billet is heated in an annular heating furnace. The temperature of the tube billet heating furnace is 1300-1320 ° C. , continuous rolling, fixed diameter reduction, cooling, and sawing; among them, the heat centering temperature is 1260-1270 °C, the hot piercing temperature is 1240-1250 °C, the continuous rolling temperature is 1070-1120 °C, and the fixed diameter reduction temperature is 910-910 °C 930°C.
Ring furnace:
Tube blank heating temperature: 1280~1290℃, allowable temperature difference: ±5℃.
Perforation process:
A three-roller conical piercer is used to reduce the piercing shear strain of the alloy steel and prevent defects such as cracks, folding, and delamination on the surface of the capillary. The elongation rate of the piercing is 3.5-4.2, the diameter-to-wall ratio is 20-28, the diameter expansion rate is below 35%, the exit speed of the piercing machine is below 0.9m/s, and the diameter tolerance of the continuous casting round tube blank is required to be ≤±1.4% , Ovality tolerance ≤ 2.5%, to ensure the geometric size and shape accuracy of the capillary. The piercing temperature is 1240-1250°C.
Continuous rolling process:
The purpose of the continuous rolling process is to reduce the diameter, extend and reduce the wall of the capillary tube transferred from the piercing process, and at the same time improve the roughness of the inner and outer surfaces of the blank tube and improve the uniformity of the wall thickness.
During continuous rolling, the inner surface of the capillary is in contact with the mandrel at the top of the pass, but not at the sidewall. The metal at the top of the hole is extended due to the external pressure of the roll and the pressure of the mandrel, and it expands in the circumferential direction while extending axially, while the metal on the side wall of the hole also expands when the metal at the top of the hole extends. It is stretched and correspondingly shrinks in the longitudinal direction. Control the reduction rate of each process of continuous rolling, so that the ratio of the effective cross-sectional area of the blank pipe before and after deformation in the continuous rolling process is 2.8 to 6.5, so as to ensure that the vertical and horizontal impact energy of the oil casing tends to be consistent. The maximum entrance speed of continuous rolling is within 1.5m/s, the exit speed is within 3.5m/s, and the ratio of the cross-sectional area of the capillary tube to the blank tube is about 3.7. Continuous rolling temperature is 1070~1120℃.
Fixed diameter reduction process:
The sizing and reducing process is a process of continuous rolling of hollow bodies. In addition to the role of sizing, it also requires a large reduction rate, and the number of working stands is 24. First, the waste pipes are heated to 920°C to 1050°C in the reheating furnace and then released. After measuring the surface temperature at the exit of the roller table, a 20MPa high-pressure water descaling device is used to remove the waste pipes from the continuous rolling unit during the rolling process. Scale, then rolled in a sizing and reducing mill. The sizing rolling temperature is 910-930°C, the sizing rolling entrance speed is between 0.5-1.4m/s, the exit speed is between 0.51-7m/s, and the effective cross-sectional area ratio is within 1.5.
(3) Heat treatment: the heat treatment process of quenching and then tempering is adopted for the above-mentioned blank pipe.
The quenching process is as follows: heating the petroleum casing to 940° C. to 920° C. and keeping it warm for 30 minutes to fully form austenite. The quenching medium is an oily quenching liquid to increase the strength and hardness of the steel.
The tempering process is as follows: the tempering temperature is 640° C. to 660° C., heat preservation for 2 hours, air cooling is used to refine the crystal grains, homogenize the structure, eliminate internal stress, and improve the toughness of the steel.
(4) The waste pipe after the above heat treatment is subjected to heat sizing and heat straightening treatment, and finally flaw detection to obtain the finished petroleum casing.
In order to minimize the residual stress of the oil casing, reduce the residual stress caused by sizing, improve the size and roundness accuracy of the oil casing, and improve the mechanical properties of the oil casing, the sizing temperature is between 550 and 600 °C During the period, the sizing outlet velocity of the waste pipe is between 1.2 and 2.4m/s.
In the thermal straightening process, the elastic limit reduction of 1.55 to 1.75 times (the elastic limit reduction is the starting point of the plastic deformation of the steel pipe surface) and the appropriate straightening temperature are selected to reduce the residual stress generated by the straightening process. Improve the roundness and straightness of the oil casing and improve the performance of the oil casing. The optimal temperature determined by theoretical calculation and experiment is 450-580°C, but in the actual process, for the sake of safety, the thermal straightening temperature is between 500°C-540°C.
In order to improve the performance of oil casing, a strict geometrical accuracy control range has been established. The geometrical accuracy of the casing meets the following requirements: the diameter error is ±0.8% of the diameter size, the wall thickness error is ±8% of the wall thickness size, and the ellipse The straightness error of the pipe end is ±0.5%, the straightness error of the pipe end is 1.5mm/m, and the straightness error of the pipe body is 1.0mm/m.
The oil casing manufactured by the production method of the invention can reach V150 steel grade. The indicators achieved by the mechanical properties of the oil casing are as follows:
Yield strength: 1057~1210MPa
Tensile strength: ≥1180MPa
Impact toughness: Longitudinal full-scale Charpy impact energy ≥ 80J
Transverse full-scale Charpy impact energy ≥ 75J
Elongation: ≥16%
The overall performance of the casing (take φ244.48×15.11 as an example)
Pipe body anti-collapse strength: ≥80MPa;
Slip strength: ≥2800KN;
Yield strength in the pipe: ≥115MPa;
Residual stress: ≤200MPa.
Geometric dimensions of oil casing;
Diameter range: 242.52mm~246.43mm;
Out of roundness: ≤1.2mm;
Wall thickness: -8.0%t~8.0%t;
Straightness: pipe end 1.5mm/m, pipe body 1.0mm/m.
The present invention has following technical effect:
1. The oil casing pipe of the present invention adopts Cr-Ni-Mo-V alloy system quenched and tempered steel grade, which can obtain a certain amount of austenite toughness dispersed on the ultrafine lath martensite matrix after heat treatment Phase, improve the strength and toughness of steel to adapt to withstand the external extrusion load and axial load brought by deep or ultra-deep wells.
2. In the production method of the present invention, through rational formulation of processes such as piercing and rolling, the crystal grains of steel can be refined to the greatest extent, and structural defects can be avoided.
3. In the production method of the present invention, the selection of the heat treatment process is reasonable, and it is possible to form a submicron-order lath martensite as a matrix, a nano-scale second phase particle as a precipitation strengthening phase and a certain amount of austenite with high stability. The multi-phase composite structure of the tough phase ensures excellent strength and toughness matching.
4. In the production method of the present invention, the thermal straightening process is reasonably formulated, which can minimize the residual stress of the casing.
5. A strict geometrical accuracy control range has been formulated, which can improve the performance of the oil casing at a reasonable cost.
6. The quenching medium in the heat treatment process of the present invention is an oily quenching liquid, which can avoid defects such as cracks on the surface of the steel pipe.
Detailed ways
The present invention will be described in detail below in conjunction with specific examples.
The present invention will be described in detail below by taking the production of φ244.48×15.11 oil casing as an example.
Example:
Sponge iron and scrap steel are used as raw materials for steelmaking, and melted into molten steel in an electric arc furnace. After refining outside the furnace and vacuum degassing, the components of molten steel for manufacturing petroleum casing are: C: 0.22-0.35%, Si: 0.17-0.30%, Mn: 0.45-0.60%, Cr: 0.80-1.10%, Mo: 0.70-1.10%, Al: 0.015-0.040%, Ni<0.20%, Cu<0.20%, V: 0.070-0.100%, Nb<0.050%, Ca<0.0015%, P<0.010%, S<0.003%, and the balance is iron.
The above molten steel is continuously cast into a round billet. Heat the cooled continuous casting billet in the ring heating furnace, the temperature of the pipe billet heating furnace is 1310°C, after that, centering, piercing, continuous rolling, sizing and reducing, cooling, sawing; among them, the heat centering is 1265°C , the hot piercing temperature is 1245°C, the continuous rolling temperature is 1100°C, and the fixed diameter reduction temperature is 920°C. It is rapidly cooled to 450°C by cooling bed and blowing cooling method, and sawing. The heat treatment process of quenching and then tempering is adopted for the above blank pipe: quenching at 930°C (oily quenching liquid), tempering at 645°C. After heat sizing at 560°C, heat straightening at 520°C, and final flaw detection, the finished oil casing is obtained.
In the piercing process, the elongation rate is 3.7, the diameter expansion rate is 28%, and the exit speed of the piercing machine is 0.7m/s. In the continuous rolling process, the ratio of the effective cross-sectional area of the barren tube before and after continuous rolling deformation is 4.3, the entrance velocity is 1.2m/s, and the exit velocity is 2.9m/s. In the fixed and reduced diameter process, the effective cross-sectional area ratio is 1.2, the entrance velocity is 0.9m/s, and the exit velocity is 1.3m/s. The sizing exit velocity of the blank pipe is 1.8m/s. In the thermal straightening process, the straightening reduction coefficient is 1.6 times the elastic limit reduction.
The mechanical properties of the oil casing produced by the above method can reach the following indicators:
Yield strength: 1109MPa;
Tensile strength: 1213MPa;
Impact toughness: Longitudinal full-scale Charpy impact energy: 121J;
Horizontal full-scale Charpy impact energy: 114J;
Elongation: 17%.
The overall performance of the casing:
Pipe collapse strength: 93.1MPa;
Slip strength: 3208KN;
Yield strength in the tube: 130.6MPa;
Residual stress: 162.31MPa.
Geometric dimensions of oil casing:
Diameter range: 245.90mm~246.20mm;
Out of roundness: ≤0.6mm;
Wall thickness: -4.5%t~7.0%t;
Straightness: pipe end 1.2mm/m, pipe body 0.9‰.
The oil casing produced through the steel type design of the invention and the reasonable control of various process conditions can meet the strength and toughness requirements of deep wells or ultra-deep wells. Control rolling deformation and heat treatment, obtain effects such as precipitation strengthening, grain refinement and phase transformation strengthening, improve the strength and toughness of steel, and solve the problem of easy cracks in the heat treatment of alloy steel seamless steel pipes. Using thermal sizing and thermal straightening processing methods, the low residual stress required by seamless steel pipes is solved, and the bending, elliptical deformation, and dimensional accuracy of seamless steel pipes are controlled.