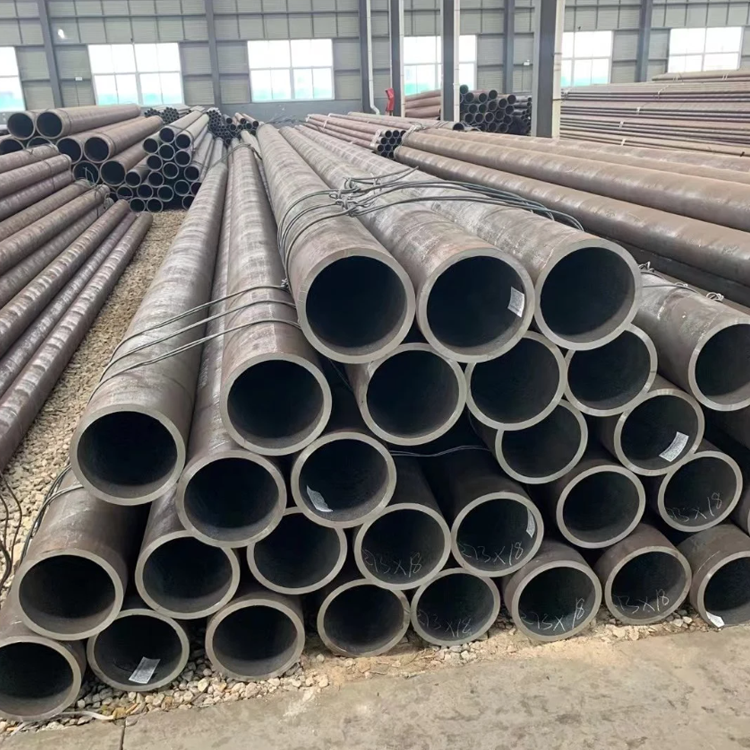
Yapısal Dikişsiz Çelik Boru
Ağustos 22, 2023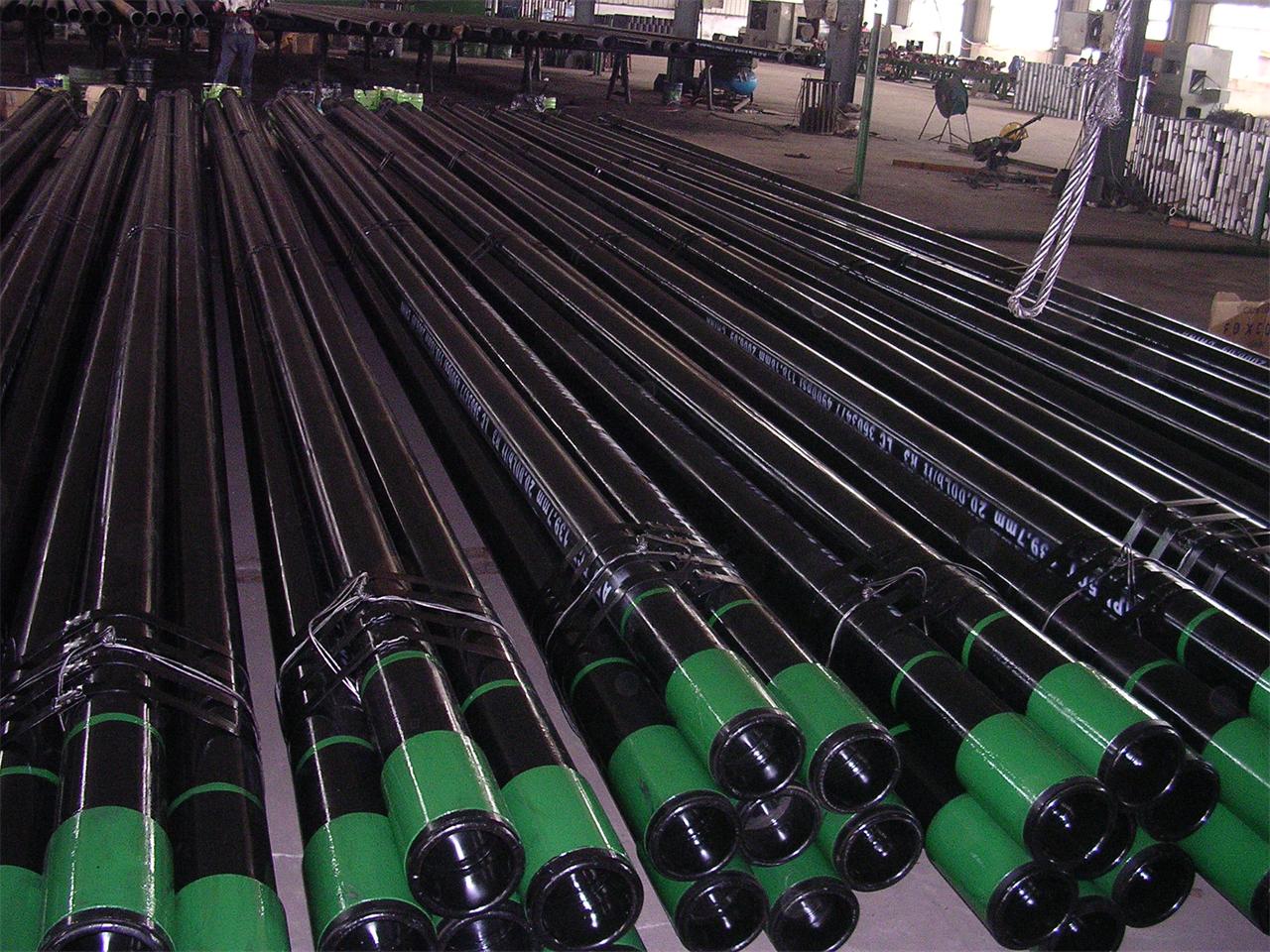
yağ muhafaza boruları ısıl işlem süreci,Kalitelerinden emin olmak için yağ muhafazaları nasıl inceleniyor ve test ediliyor??
Eylül 4, 2023Mukavemet ve Tokluğu Yüksek Yağ Gövdesi ve Üretim Yöntemi
Açıklama
Yüksek mukavemet ve tokluğa sahip bir yağ mahfazası, petrol ve gaz sondaj operasyonlarında kritik bir bileşendir. Yüksek basınca dayanacak şekilde tasarlanmıştır, aşındırıcı malzemeler, ve aşındırıcı ortamlar, sondaj operasyonlarında sıklıkla karşılaşılan. Yağ mahfazası genellikle çelikten yapılır ve yüksek mukavemet gibi belirli özelliklere sahip olmalıdır., tokluk, ve korozyon direnç.
Üretim yöntemi
Üretim yöntemi birkaç adımdan oluşur, malzeme seçimi dahil, ısıl işlem, şekillendirme, ve muayene.
1. Malzeme seçimi
Muhafazanın temel malzemesi genellikle yüksek kaliteli karbon çeliği veya alaşımlı çeliktir. Malzeme, sondaj işleminin beklenen koşullarına göre seçilir, sıcaklık gibi, basınç, ve aşındırıcı ortam.
2. Şekillendirme
Çelik belirli bir sıcaklığa kadar ısıtılır ve daha sonra boru haline getirilir. Bu genellikle sıcak haddeleme ile yapılır, çeliğin, onu istenen boru şekline ve boyutuna şekillendiren bir dizi silindirden geçirildiği yer. Borular daha sonra soğutulur ve sertleştirilir.
3. Isı tedavisi
Korozyon reaksiyonundan gelen hidrojen iyonları çeliğin yüzeyine yapışır ve atomik hidrojenler olarak çeliğin içine nüfuz eder., borular ısıl işlem sürecinden geçer. Bu, söndürme ve temperlemeyi içerebilir, çeliğin mukavemetini ve tokluğunu arttırmak için kullanılır. Söndürme, çeliğin belirli bir sıcaklığa kadar ısıtılmasını içerir. Yüksek sıcaklık ve ardından hızla soğutuyoruz, tavlama, çeliğin daha düşük bir sıcaklığa ısıtılmasını ve ardından yavaşça soğutulmasını içerir.
4. Denetim ve test
En sonunda, borular gerekli standartları karşıladıklarından emin olmak için incelenir ve test edilir. Bu görsel incelemeleri içerebilir, sertlik testi, ve ultrasonik test. Borular bu testleri geçerse, daha sonra yağ muhafazası olarak kullanılmaya hazırdırlar.
Bu, yüksek mukavemetli ve tokluklu yağ muhafazalarının nasıl üretildiğinin temel taslağıdır. Gerçek süreçler daha karmaşık olabilir ve kasanın özel gereksinimlerine bağlı olarak değişiklik gösterebilir..
Avantajları
- Arttırılmış Dayanıklılık: Bu yağ muhafazalarının yüksek mukavemeti ve sağlamlığı, bunların yüksek basınca ve aşındırıcı malzemelere dayanabilmesini sağlar, ömrünü uzatmak ve değiştirme ihtiyacını azaltmak.
- Geliştirilmiş Güvenlik: Bu özellikler aynı zamanda sondaj operasyonlarının güvenliğini de arttırır., muhafaza arızası riskini azalttıkları için, bu da feci kazalara yol açabilir.
- Uygun Maliyetli: Üretim süreci daha karmaşık ve maliyetli olsa da, bu muhafazaların artan dayanıklılığı ve güvenliği, uzun vadede önemli maliyet tasarruflarına yol açabilir.
Sonuç
Yüksek mukavemet ve tokluğa sahip yağ muhafazalarının üretimi, güvenli ve verimli sondaj operasyonlarının sağlanmasında kritik bir husustur. Üretim süreci karmaşık olabilse de, dayanıklılık açısından faydalar, emniyet, ve maliyet tasarrufları onu değerli bir yatırım haline getirir.
Buluş, metalurji endüstrisinde dikişsiz çelik boru imalatı teknik alanına aittir., ve özellikle derin kuyular veya ultra derin kuyular için uygun, süper yüksek dayanıma ve tokluğa sahip bir petrol mahfazası ve bunun üretim yöntemi ile ilgilidir.
Arka plan tekniği
Petrol ve gaz sahalarında sondaj derinliğinin artmasıyla birlikte, sıcaklık ve basıncın artması, Sabit kuyu başlıkları için kullanılan petrol muhafazasının jeolojik ortamı önemli ölçüde değişti, ve kullanılan mekanik koşullar da buna göre değişti. Taşıdığı dış ekstrüzyon yükü ve eksenel yükler giderek artıyor. Amerikan Petrol Enstitüsü standardı tarafından belirlenen V125 gibi yüksek kaliteli yağ muhafazalarında genellikle Cr-Mo-V serisi alaşımlı çelikler kullanılır.. Karmaşık eritme nedeniyle, Bu çelik tipindeki yağ mahfazalarının haddeleme ve ısıl işlem işlemleri, alaşım bileşimi ve üretim süreci uygun değil. , yağ muhafazasının mukavemetinin ve dayanıklılığının azalmasına neden olacaktır, derin veya ultra derin kuyuların getirdiği dış ekstrüzyon yüküne ve eksenel yüke dayanamaz, bu da yağ muhafazasının hasarını ve arızasını ağırlaştıracaktır, ve mahfazanın hasar görmesi ve arızalanması kuyu deliğinin arızalanmasına kolaylıkla yol açacaktır. Kararsızlık gibi karmaşık sorunlar, rezervuar hasarı, delme ve çimentolama zorlukları, vb., petrol sahası operasyonlarının güvenliğini ciddi şekilde tehdit ediyor, hatta kuyu yıkımı kazaları gibi büyük ekonomik kayıplara yol açabilmektedir.. bu nedenle, Petrol sahası, petrol mahfazasının performansına ilişkin daha yüksek gereksinimler ortaya koyuyor.
Şu anda, Derin veya çok derin kuyularda petrol muhafazası için çözülmesi gereken sorun, ultra yüksek mukavemet ve yüksek tokluğun eşleştirilmesidir.. Yüksek mukavemetli ve tokluklu yağ muhafazasının performansı yalnızca kullanılan malzeme bileşimi ile ilgili değildir., ama aynı zamanda üretim yöntemiyle de yakından ilgilidir. ASME B36.10 ve B36.19 ile uyumlu BORU'dur., ultra yüksek mukavemetli çeliğin darbe dayanıklılığı çeliğin saflığına bağlıdır, yapının bileşimi ve iyileştirilmesi. Kükürt içeriğini azaltmak için ultra saf eritme teknolojisi benimsenmiştir, Ultra yüksek mukavemetli çelikteki fosfor safsızlık elementleri ve gazları mümkün olduğu kadar, ve katılım sayısını azaltın, böylece tatmin edici darbe dayanıklılığı elde edilebilir. Uygun bir ısıl işlem prosesinin kullanılması, Matris olarak ultra ince çıta martensit ve dağılmış östenit sünek fazı ile karakterize edilen mikro yapı, ultra yüksek mukavemetli çelikte elde edilir, ve haddeleme ve düzleştirme işlemi sırasında elde edilir Yüksek hassasiyetli yağ gövdesi boyutu ve yüzey kalitesi ile düşük artık gerilim, yağ gövdesinde ultra yüksek mukavemet ve tokluk elde etmenin temel teknik ve etkili yollarıdır.
ancak, Petrol muhafazalarında kullanılan mevcut çelik kaliteleri kükürt ve fosfor gibi yüksek yabancı maddeler içerir, ve metal yapı pul pul kalıntılar içeriyor. Haddeleme işlemi sırasında metalin eşit olmayan akışı, yatay ve dikey yönlerde tutarsız mekanik özelliklere neden olur. Ayrıca, mevcut petrol mahfazası üretim yönteminde, Isıl işlem prosesinde söndürme ortamı sudur, çatlamaya neden olması kolaydır. Aynı zamanda, mantıksız delme ve yuvarlama işlemi nedeniyle, ısıl işlem süreci ve doğrultma yöntemi, en iyisi Gövdenin sağlamlığı ve sağlamlığı eşleşiyor, ve aşırı artık strese neden olur, ve kasanın geometrik boyut doğruluğu zayıf, Ürünün çökmeye direnme yeteneğini doğrudan etkileyen.
Buluşun içeriği
Buluşun amacı, önceki teknikteki eksiklikleri gidererek, petrol sahalarında derin kuyu veya ultra derin paralel üretim koşullarının gereksinimlerini karşılayabilecek, yüksek mukavemet ve tokluğa sahip bir yağ kasası sağlamaktır..
Mevcut buluşun bir diğer amacı, yüksek mukavemet ve tokluğa sahip bir yağ mahfazası üretim yöntemi sağlamaktır., Petrol sahalarındaki derin kuyuların veya ultra derin kuyuların üretim koşullarını karşılayabilen.
Mevcut buluş aşağıdaki teknik şema aracılığıyla gerçekleştirilmektedir:
Yüksek mukavemet ve tokluğa sahip bir yağ gövdesi, özelliği, bileşenlerin ağırlık yüzdesine göre olmasıdır: C: 0.22-0.35%, Si: 0.17-0.30%, MN: 0.45-0.60%, CR: 0.80-1.10%, sen: 0.70-1.10%, Al: 0.015-0.040%, Ni<0.20%, Cu<0.20%, V: 0.070-0.100%, NB<0.050%, olarak<0.0015%, P<0.010%, S<0.003% , ve denge demirdir.
Ana alaşım elementlerinin rolü:
C: 0.22-0.35%. C, çeliğin mukavemetini artırabilen karbür oluşturucu bir elementtir. Çok düşükse, etkisi açık değil, ve eğer çok yüksekse, çeliğin dayanıklılığını büyük ölçüde azaltacaktır.
MN: 0.45-0.60%, Mn östenit oluşturan bir elementtir, Çeliğin sertleşebilirliğini artırabilen, Çelikte tutulan östenit miktarını artırın, ve sıcak haddelenmiş yapının homojenliğini etkiler.
CR: 0.80-1.10%. Krom mekanik özellikleri iyileştirebilir, çeliğin korozyon direnci ve sertleşebilirliği, ancak çeliğin temper kırılganlığını artırabilir.
V: 0.070-0.100%, tahılları rafine edebilir, karbürler oluşturmak, ve çeliğin mukavemetini ve tokluğunu geliştirin. Ancak içerik belirli bir miktara ulaştığında, etkisindeki artış belirgin olmayacak. Aynı zamanda, çünkü fiyatı yüksek, kullanım miktarı sınırlı olmalı.
sen: 0.70-1.10%, çeliğin mukavemetini arttırmak için esas olarak karbür ve katı çözelti güçlendirmesi yoluyla, içerik çok yüksekse, Çeliğin dayanıklılığı azalacak.
NB<0.050 esas olarak taneleri inceltir ve yüksek mukavemetli çeliğin tokluğunu önemli ölçüde artırır.
Ni<0.20 esas olarak çeliğin mukavemetini ve tokluğunu artırır, Çeliğin korozyon direncini artırır, ve çeliğin kırılgan geçiş sıcaklığını azaltır.
Cu<0.20, Alaşımlı çelikteki bakır, çeliğin mukavemetini ve atmosferik korozyon direncini artırabilir, çok fazla ilave çeliği kırılgan hale getirir, genellikle fazla değil 0.2%.
Mükemmel güç ve tokluk eşleşmesini sağlamak için, mevcut buluşun yağ mahfazasının üretim yöntemi aşağıdaki adımları içerir:
(1) Malzemeler eritme: Sünger demir ve hurda çelik, çelik üretiminde hammadde olarak kullanılıyor, elektrik ark ocağında erimiş çelik haline getirildi (EFF), ve yağ mahfazalarının imalatı için erimiş çelik, fırın dışında rafine edildikten sonra elde edilir. (LF) ve vakum (VD) gaz giderme Ağırlık yüzdesine göre bileşim:: C: 0.22-0.35%, Si: 0.17-0.30%, MN: 0.45-0.60%, CR: 0.80-1.10%, sen: 0.70-1.10%, Al: 0.015-0.040%, Ni< 0.20%, Cu<0.20%, V: 0.070-0.100%, NB<0.050%, olarak<0.0015%, P<0.010%, S<0.003%, ve denge demirdir.
(2) Sürekli döküm ve haddeleme: Yukarıda bahsedilen yüksek saflıkta erimiş çelik, sürekli olarak yuvarlak bir kütük halinde dökülür., ve soğutulmuş sürekli döküm kütüğü dairesel bir ısıtma fırınında ısıtılır. Boru kütük ısıtma fırınının sıcaklığı 1300-1320 ° C. , sürekli yuvarlanma, sabit çap küçültme, soğutma, ve testereyle kesme; aralarında, ısı merkezleme sıcaklığı 1260-1270 ° C, sıcak delici sıcaklık 1240-1250 ° C, sürekli haddeleme sıcaklığı 1070-1120 ° C, ve sabit çap küçültme sıcaklığı 910-910 °C 930°C.
Halka fırın:
Tüp boş ısıtma sıcaklığı: 1280~1290°C, izin verilen sıcaklık farkı: ±5°C.
Perforasyon süreci:
Alaşımlı çeliğin delici kesme gerilimini azaltmak ve çatlak gibi kusurları önlemek için üç silindirli konik delici kullanılır, katlama, ve kılcal damar yüzeyinde delaminasyon. Delicinin uzama oranı 3.5-4.2, çap-duvar oranı 20-28, çap genişleme oranı aşağıdadır 35%, delme makinesinin çıkış hızı 0,9 m/s'nin altındadır, ve sürekli döküm yuvarlak boru ham parçasının çap toleransının ≤±%1,4 olması gerekir , Ovallik toleransı ≤ 2.5%, kılcal damarın geometrik boyutunun ve şeklinin doğruluğunu sağlamak için. Delme sıcaklığı 1240-1250°C'dir.
Sürekli haddeleme işlemi:
Sürekli haddeleme işleminin amacı çapı azaltmaktır., Delme işleminden aktarılan kılcal borunun duvarını uzatın ve küçültün, ve aynı zamanda boş borunun iç ve dış yüzeylerinin pürüzlülüğünü iyileştirir ve duvar kalınlığının tekdüzeliğini iyileştirir.
Sürekli yuvarlanma sırasında, kılcal borunun iç yüzeyi geçişin üst kısmındaki mandrel ile temas halindedir, ama yan duvarda değil. Deliğin üst kısmındaki metal, merdanenin dış basıncı ve mandrelin basıncı nedeniyle uzar, ve eksenel olarak uzanırken çevresel yönde genişler, deliğin üst kısmındaki metal uzadıkça deliğin yan duvarındaki metal de genişler. Boyuna yönde gerilir ve buna bağlı olarak küçülür. Sürekli haddelemenin her işleminin azaltma oranını kontrol edin, böylece sürekli haddeleme işleminde boş borunun deformasyondan önceki ve sonraki etkin kesit alanının oranı 2.8 için 6.5, Yağ muhafazasının dikey ve yatay darbe enerjisinin tutarlı olmasını sağlayacak şekilde. Sürekli haddelemenin maksimum giriş hızı 1,5 m/s'dir, çıkış hızı 3,5 m/s'dir, ve kılcal borunun kesit alanının boş boruya oranı yaklaşık 3.7. Sürekli haddeleme sıcaklığı 1070~1120°C'dir.
Sabit çap küçültme işlemi:
Boyutlandırma ve küçültme işlemi, içi boş gövdelerin sürekli haddelenmesi işlemidir.. Boyutlandırma rolüne ek olarak, aynı zamanda büyük bir azaltma oranı gerektirir, ve çalışma standlarının sayısı 24. İlk, atık borular yeniden ısıtma fırınında 920°C ila 1050°C'ye kadar ısıtılır ve daha sonra serbest bırakılır. Makaralı tablanın çıkışında yüzey sıcaklığını ölçtükten sonra, Haddeleme işlemi sırasında atık boruları sürekli haddeleme ünitesinden çıkarmak için 20 MPa'lık yüksek basınçlı su tufal giderme cihazı kullanılır. Ölçek, daha sonra boyutlandırma ve küçültme değirmeninde haddelendi. Haşıl haddeleme sıcaklığı 910-930°C'dir, boyutlandırma yuvarlanma giriş hızı 0,5-1,4 m/s arasındadır, çıkış hızı 0,51-7m/s arasındadır, ve etkili kesit alanı oranı dahilindedir 1.5.
(3) Isıl işlem: Yukarıda belirtilen boş boru için söndürme ve ardından temperleme ısıl işlem prosesi benimsenmiştir..
Söndürme işlemi aşağıdaki gibidir: Petrol mahfazasını 940° C'ye ısıtmak. 920° C'ye kadar. ve onu sıcak tutmak 30 östenitin tamamen oluşması için dakikalar. Söndürme ortamı, çeliğin mukavemetini ve sertliğini arttırmak için yağlı bir söndürme sıvısıdır..
Temperleme işlemi aşağıdaki gibidir: tavlama sıcaklığı 640° C'dir. 660°C'ye kadar., için ısı koruması 2 saat, kristal tanelerini rafine etmek için hava soğutması kullanılır, yapıyı homojenleştirmek, iç stresi ortadan kaldırmak, ve çeliğin dayanıklılığını artırın.
(4) Yukarıdaki ısıl işlemden sonra atık boru, ısıl boyutlandırma ve ısıl düzleştirme işlemine tabi tutulur., ve son olarak bitmiş petrol muhafazasını elde etmek için kusur tespiti.
Yağ muhafazasındaki artık gerilimi en aza indirmek için, boyutlandırmanın neden olduğu artık gerilimi azaltmak, Yağ muhafazasının boyutunu ve yuvarlaklık doğruluğunu iyileştirin, ve yağ muhafazasının mekanik özelliklerini iyileştirmek, boyutlandırma sıcaklığı arasındadır 550 ve 600 °C Dönem boyunca, Atık borusunun boyutlandırma çıkış hızı arasındadır. 1.2 ve 2,4 m/sn.
Termal düzleştirme işleminde, elastik limit azalması 1.55 için 1.75 zamanlar (elastik limit azalması çelik boru yüzeyinin plastik deformasyonunun başlangıç noktasıdır) ve doğrultma işlemi tarafından üretilen artık gerilimi azaltmak için uygun düzleştirme sıcaklığı seçilir. Yağ muhafazasının yuvarlaklığını ve düzlüğünü iyileştirin ve yağ muhafazasının performansını artırın. Teorik hesaplama ve deneyle belirlenen optimum sıcaklık 450-580°C'dir., ama gerçek süreçte, güvenlik uğruna, termal düzleştirme sıcaklığı 500°C-540°C arasındadır.
Yağ muhafazasının performansını artırmak için, sıkı bir geometrik doğruluk kontrol aralığı oluşturulmuştur. Muhafazanın geometrik doğruluğu aşağıdaki gereksinimleri karşılar: çap hatası çap boyutunun ±%0,8'idir, duvar kalınlığı hatası duvar kalınlığı boyutunun ±%8'idir, ve elips Boru ucunun düzlük hatası ±%0,5'tir, boru ucunun doğruluk hatası 1,5 mm/m'dir, ve boru gövdesinin doğruluk hatası 1,0 mm/m'dir.
Buluş konusu üretim yöntemiyle üretilen yağ karteri V150 çelik kalitesine ulaşabilmektedir.. Yağ muhafazasının mekanik özellikleriyle elde edilen göstergeler aşağıdaki gibidir:
Verim gücü: 1057~1210MPa
Çekme dayanımı: ≥1180MPa
Darbe dayanıklılığı: Boyuna tam ölçekli Charpy darbe enerjisi ≥ 80J
Enine tam ölçekli Charpy darbe enerjisi ≥ 75J
Kopma uzaması: ≥
Kasanın genel performansı (örnek olarak φ244,48×15,11'i ele alalım)
Boru gövdesinin çökmeye karşı dayanıklılığı: ≥80MPa;
Kayma mukavemeti: ≥2800KN;
Borudaki akma mukavemeti: ≥115MPa;
Artık stres: ≤200MPa.
Yağ muhafazasının geometrik boyutları;
Çap aralığı: 242.52mm~246,43 mm;
Yuvarlaklığın dışında: ≤1,2 mm;
Duvar kalınlığı: -8.0%t~%8,0t;
Doğruluk: boru ucu 1,5 mm/m, boru gövdesi 1,0 mm/m.
Mevcut buluş aşağıdaki teknik etkiye sahiptir:
1. Yağ kasa boru mevcut buluşun su verilmiş ve temperlenmiş çelik kalitesini Cr-Ni-Mo-V alaşım sistemi benimser, ısıl işlemden sonra ultra ince çıta martensit matrisi üzerine dağılmış belirli bir miktarda ostenit tokluğu elde edebilen, derin veya ultra derin kuyuların getirdiği harici ekstrüzyon yüküne ve eksenel yüke dayanacak şekilde çeliğin mukavemetini ve tokluğunu geliştirin.
2. Mevcut buluşun üretim yönteminde, delme ve yuvarlama gibi süreçlerin rasyonel formülasyonu yoluyla, çeliğin kristal taneleri büyük ölçüde rafine edilebilir, ve yapısal kusurlar önlenebilir.
3. Mevcut buluşun üretim yönteminde, Isıl işlem prosesinin seçimi makuldür, ve matris olarak mikron altı dereceli bir çıta martenziti oluşturmak mümkündür, çökelme güçlendirme fazı olarak nano ölçekli ikinci faz partikülü ve yüksek stabiliteye sahip belirli miktarda ostenit. Sert fazın çok fazlı kompozit yapısı mükemmel mukavemet ve tokluk uyumu sağlar.
4. Mevcut buluşun üretim yönteminde, termal düzleştirme işlemi makul şekilde formüle edilmiştir, bu, mahfazanın artık gerilimini en aza indirebilir.
5. Sıkı bir geometrik doğruluk kontrol aralığı formüle edilmiştir, makul bir maliyetle yağ muhafazasının performansını artırabilen.
6. Mevcut buluşun ısıl işlem prosesindeki söndürme ortamı, yağlı bir söndürme sıvısıdır, çelik borunun yüzeyindeki çatlaklar gibi kusurları önleyebilecek.
Ayrıntılı yollar
Mevcut buluş aşağıda spesifik örneklerle birlikte ayrıntılı olarak açıklanacaktır..
Mevcut buluş aşağıda φ244.48×15.11 yağ muhafazasının üretimi örnek alınarak detaylı olarak anlatılacaktır..
Örnek:
Sünger demir ve hurda çelik, çelik üretiminde hammadde olarak kullanılıyor, ve bir elektrik ark ocağında erimiş çelik halinde eritildi. Fırının dışında rafine edildikten ve vakumla gazdan arındırıldıktan sonra, Petrol mahfazası imalatında kullanılan erimiş çeliğin bileşenleri: C: 0.22-0.35%, Si: 0.17-0.30%, MN: 0.45-0.60%, CR: 0.80-1.10%, sen: 0.70-1.10%, Al: 0.015-0.040%, Ni<0.20%, Cu<0.20%, V: 0.070-0.100%, NB<0.050%, olarak<0.0015%, P<0.010%, S<0.003%, ve denge demirdir.
Yukarıdaki erimiş çelik sürekli olarak yuvarlak bir kütüğe dökülür. Soğutulmuş sürekli döküm kütüğünü halka ısıtma fırınında ısıtın, boru kütük ısıtma fırınının sıcaklığı 1310°C'dir, daha sonrasında, merkezleme, delici, sürekli yuvarlanma, boyutlandırma ve küçültme, soğutma, testere; aralarında, ısı merkezlemesi 1265°C'dir , sıcak delme sıcaklığı 1245°C'dir, sürekli haddeleme sıcaklığı 1100°C'dir, ve sabit çap küçültme sıcaklığı 920°C'dir. Soğutma yatağı ve üflemeli soğutma yöntemi ile hızla 450°C'ye soğutulur., ve testereyle kesme. Yukarıdaki boş boru için söndürme ve ardından temperleme ısıl işlem prosesi benimsenmiştir.: 930°C'de söndürme (yağlı söndürme sıvısı), 645°C'de temperleme. 560°C'de ısıyla boyutlandırmanın ardından, 520°C'de ısıyla düzleştirme, ve son kusur tespiti, bitmiş yağ muhafazası elde edilir.
Delme işleminde, uzama oranı 3.7, çap genişleme oranı 28%, ve delme makinesinin çıkış hızı 0,7 m/s'dir. Sürekli haddeleme işleminde, sürekli yuvarlanma deformasyonundan önce ve sonra çorak tüpün etkili kesit alanının oranı 4.3, giriş hızı 1,2 m/s, ve çıkış hızı 2,9 m/s'dir. Sabit ve küçültülmüş çap prosesinde, etkili kesit alanı oranı 1.2, giriş hızı 0,9 m/s'dir, ve çıkış hızı 1,3 m/s'dir. Boş borunun boyutlandırma çıkış hızı 1,8 m/s'dir. Termal düzleştirme işleminde, doğrultma azaltma katsayısı 1.6 elastik limit azalmasının katı.
Yukarıdaki yöntemle üretilen yağ gövdesinin mekanik özellikleri aşağıdaki göstergelere ulaşabilir::
Verim gücü: 1109MPa;
Çekme dayanımı: 1213MPa;
Darbe dayanıklılığı: Boyuna tam ölçekli Charpy darbe enerjisi: 121J;
Yatay tam ölçekli Charpy darbe enerjisi: 114J;
Kopma uzaması: 17%.
Kasanın genel performansı:
Boru çökme mukavemeti: 93.1MPa;
Kayma mukavemeti: 3208KN;
Borudaki akma mukavemeti: 130.6MPa;
Artık stres: 162.31MPa.
Yağ muhafazasının geometrik boyutları:
Çap aralığı: 245.90mm~246,20 mm;
Yuvarlaklığın dışında: ≤0,6 mm;
Duvar kalınlığı: -4.5%t~%7,0t;
Doğruluk: boru ucu 1,2 mm/m, boru gövdesi 0,9 ‰.
Buluşun çelik tipi tasarımı ve çeşitli proses koşullarının makul kontrolü yoluyla üretilen yağ mahfazası, derin kuyuların veya ultra derin kuyuların mukavemet ve dayanıklılık gereksinimlerini karşılayabilir. Yuvarlanma deformasyonunu ve ısıl işlemi kontrol edin, yağış güçlendirme gibi etkiler elde etmek, tane inceltme ve faz dönüşümü güçlendirme, çeliğin mukavemetini ve tokluğunu arttırmak, ve alaşımlı çelik dikişsiz çelik boruların ısıl işleminde kolay çatlak problemini çözer. Termal boyutlandırma ve termal doğrultma işleme yöntemlerinin kullanılması, dikişsiz çelik boruların gerektirdiği düşük artık gerilim çözüldü, ve bükülme, eliptik deformasyon, Dikişsiz çelik boruların boyutsal doğruluğu kontrol edilmektedir..