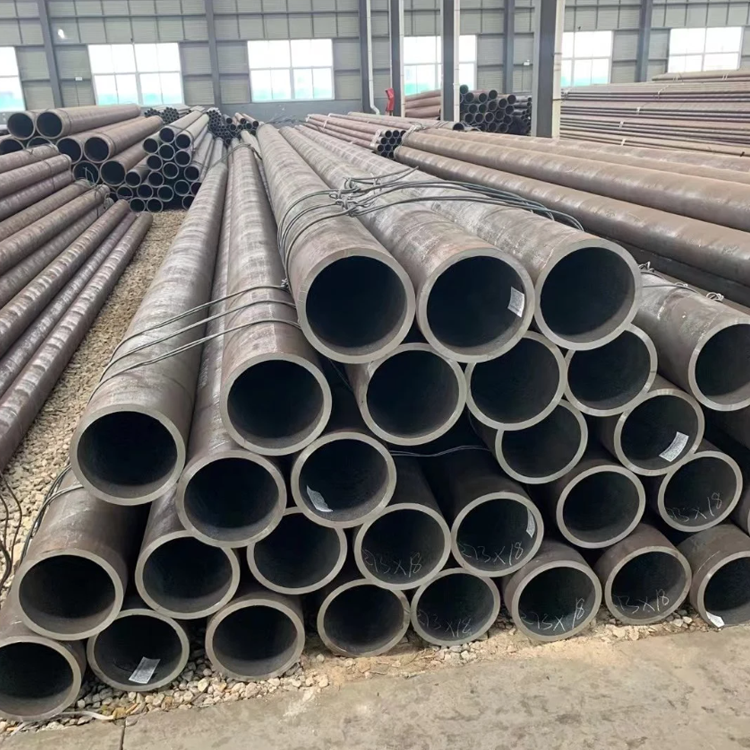
Конструкционная бесшовная стальная труба
августейший 22, 2023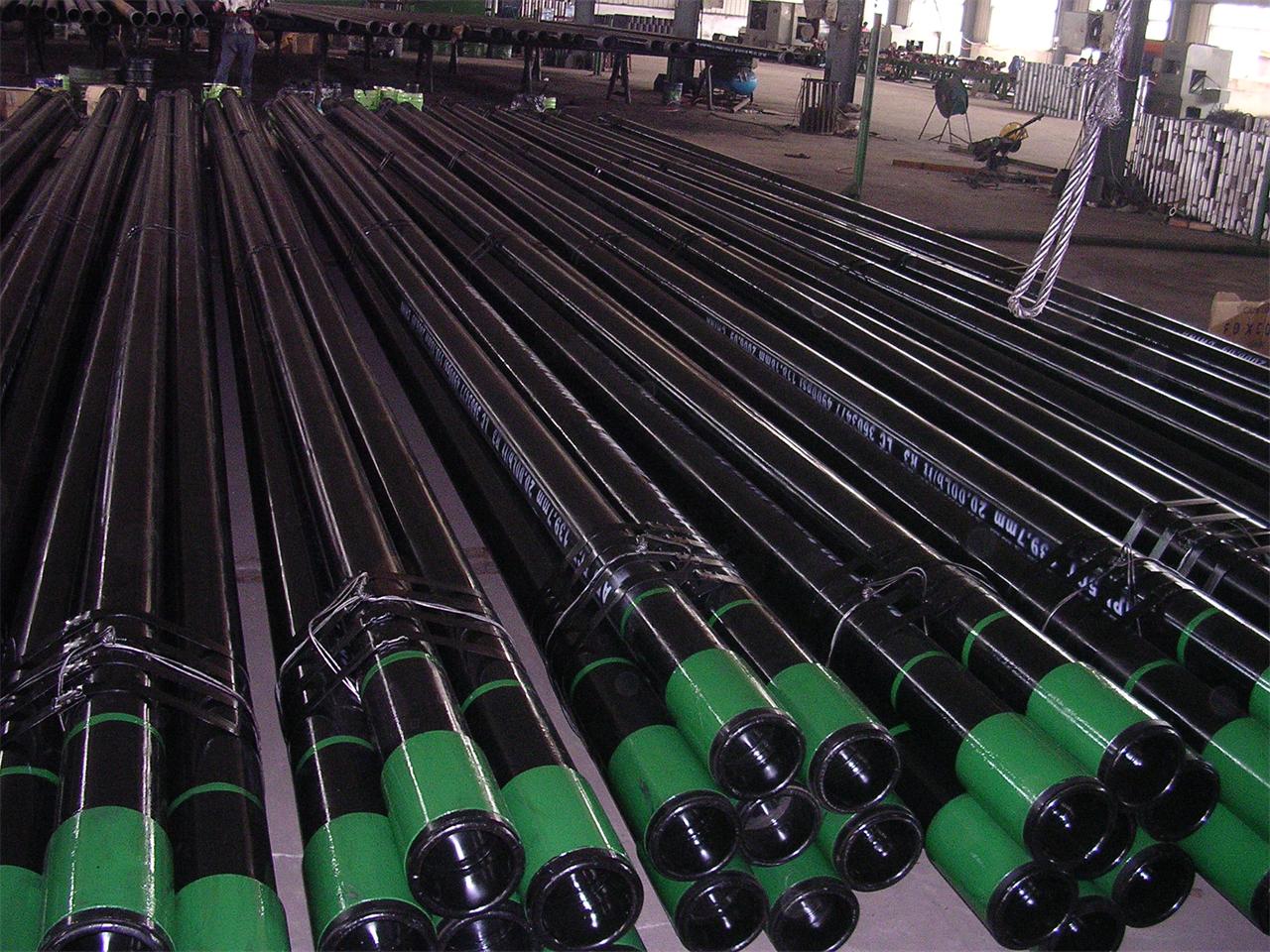
процесс термообработки нефтяных обсадных труб,Как проверяются и тестируются масляные кожухи для обеспечения их качества?
сентябрь 4, 2023Масляный корпус высокой прочности и вязкости и способ его изготовления
Описание
Нефтяная колонна, обладающая высокой прочностью и ударной вязкостью, является важнейшим компонентом при бурении нефти и газа.. Он рассчитан на выдерживание высокого давления, абразивные материалы, и агрессивные среды, часто встречается при бурении. Масляный корпус часто изготавливается из стали и должен обладать особыми свойствами, такими как высокая прочность., стойкость, а также коррозия сопротивление.
Метод производства
Способ производства включает в себя несколько этапов., включая подбор материалов, термическая обработка, формирование, и осмотр.
1. Выбор материала
Основным материалом корпуса обычно является высококачественная углеродистая или легированная сталь.. Материал выбирается исходя из ожидаемых условий проведения буровых работ., например, температура, давление, и агрессивная среда.
2. Формирование
Сталь нагревается до определенной температуры, а затем формуется в трубы.. Часто это делается путем горячей прокатки., где сталь пропускают через ряд роликов, которые придают ей трубу желаемой формы и размера.. Затем трубы охлаждают и закаливают..
3. Термическая обработка
следующий, трубы проходят процесс термообработки. Это может включать закалку и отпуск., которые используются для повышения прочности и ударной вязкости стали.. Закалка предполагает нагрев стали до высокая температура а затем быстро охладить его, в то время как отпуск предполагает нагрев стали до более низкой температуры, а затем медленное ее охлаждение..
4. Проверка и тестирование
в заключение, трубы проверяются и тестируются на предмет соответствия требуемым стандартам.. Это может включать визуальный осмотр, испытание на твердость, и ультразвуковой контроль. Если трубы проходят эти испытания, после этого они готовы к использованию в качестве масляных кожухов.
Это базовое описание того, как производятся высокопрочные и вязкие масляные кожухи.. Реальные процессы могут быть более сложными и варьироваться в зависимости от конкретных требований к обсадной колонне..
преимущества
- Повышенная долговечность: Высокая прочность и ударная вязкость этих масляных корпусов позволяют им выдерживать высокое давление и абразивные материалы., увеличение срока их службы и уменьшение необходимости замены.
- Улучшенная безопасность: Эти свойства также повышают безопасность буровых работ., поскольку они снижают риск разрушения обсадной колонны, что может привести к катастрофическим авариям.
- Экономически эффективным: Хотя производственный процесс может быть более сложным и дорогостоящим., Повышенная долговечность и безопасность этих оболочек может привести к значительной экономии затрат в долгосрочной перспективе..
Заключение
Производство нефтяных обсадных колонн высокой прочности и вязкости является важнейшим аспектом обеспечения безопасных и эффективных буровых работ.. Хотя производственный процесс может быть сложным, преимущества с точки зрения долговечности, безопасность, и экономия средств делают это выгодной инвестицией.
Изобретение относится к области техники изготовления стальных бесшовных труб в металлургической промышленности., и, в частности, относится к нефтяной колонне со сверхвысокой прочностью и ударной вязкостью, подходящей для глубоких скважин или сверхглубоких скважин, и к способу ее добычи..
Фоновая техника
С увеличением глубины бурения на нефтяных и газовых месторождениях, повышение температуры и давления, геологическая среда нефтяной колонны, используемой для стационарных устьев скважин, существенно изменилась, и используемые механические условия также соответственно изменились. Внешняя экструзионная нагрузка, которую он несет, и осевые нагрузки становятся все выше и выше.. В высококачественных масляных корпусах, таких как V125, соответствующих стандарту Американского института нефти, обычно используются легированные стали серии Cr-Mo-V.. Из-за сложной плавки, процессы прокатки и термообработки нефтяных корпусов из этой марки стали, состав сплава и процесс производства не подходят. , приведет к снижению прочности и ударной вязкости масляного корпуса., и не может выдерживать внешнюю экструзионную и осевую нагрузку, создаваемую глубокими или сверхглубокими скважинами., что усугубит повреждение и выход из строя масляного картера, а повреждение и выход из строя обсадной колонны легко приведут к выходу из строя ствола скважины. Сложные проблемы, такие как нестабильность, повреждение резервуара, трудности при бурении и цементировании, и т.п., серьезно угрожают безопасности нефтепромысловых операций, и даже привести к крупным экономическим потерям, таким как аварии, связанные с разрушением скважин.. Следовательно, месторождение выдвигает повышенные требования к эксплуатации нефтяных колонн.
В настоящий момент, Проблема, которую необходимо решить при изготовлении нефтяных колонн для глубоких или сверхглубоких скважин, заключается в сочетании сверхвысокой прочности и высокой ударной вязкости.. Характеристики высокопрочного и вязкого масляного корпуса зависят не только от состава используемого материала., но также тесно связан с методом его производства. Это ТРУБА, соответствующая ASME B36.10 и B36.19., ударная вязкость сверхвысокопрочных сталей зависит от чистоты стали, состав и уточнение структуры. Для снижения содержания серы применяется технология сверхчистой плавки., максимально возможное содержание примесей фосфора и газов в сверхвысокопрочных сталях, и уменьшить количество включений, так, чтобы можно было получить удовлетворительную ударную вязкость. Использование соответствующего процесса термообработки., микроструктура, характеризующаяся сверхмелким реечным мартенситом в качестве матрицы и дисперсной пластичной фазой аустенита, получена в стали сверхвысокой прочности., и полученные в процессе прокатки и правки. Высокоточные размер масляной оболочки и качество поверхности, а также низкое остаточное напряжение являются ключевыми техническими и эффективными способами достижения сверхвысокой прочности и ударной вязкости масляной оболочки..
тем не мение, современные марки стали, используемые в нефтяных колоннах, содержат большое количество примесей, таких как сера и фосфор., а в структуре металла присутствуют чешуйчатые включения. Неравномерное течение металла в процессе прокатки приводит к неравномерности механических свойств в горизонтальном и вертикальном направлениях.. Кроме того, в современном способе добычи нефтяных колонн, закалочной средой в процессе термообработки является вода., что легко вызвать растрескивание. В то же время, из-за необоснованного процесса прошивки и прокатки, процесс термообработки и метод выпрямления, лучшее Сочетание прочности и ударной вязкости корпуса, и вызвать чрезмерное остаточное напряжение, и точность геометрических размеров корпуса плохая, что напрямую влияет на способность изделия сопротивляться разрушению.
Содержание изобретения
Целью изобретения является преодоление недостатков предшествующего уровня техники и создание нефтяной колонны с высокой прочностью и ударной вязкостью, которая может соответствовать требованиям глубоких скважин или условий сверхглубокой параллельной добычи на нефтяных месторождениях..
Другой целью настоящего изобретения является создание способа изготовления нефтяной колонны с высокой прочностью и ударной вязкостью., который может соответствовать условиям добычи глубоких или сверхглубоких скважин на нефтяных месторождениях..
Настоящее изобретение реализуется посредством следующей технической схемы.:
Масляный корпус с высокой прочностью и вязкостью, характеризующийся тем, что компоненты по массе составляют: С: 0.22-0.35%, Si: 0.17-0.30%, MN: 0.45-0.60%, CR: 0.80-1.10%, МО: 0.70-1.10%, Al: 0.015-0.040%, Ni<0.20%, Cu<0.20%, V: 0.070-0.100%, NB<0.050%, в качестве<0.0015%, P<0.010%, S<0.003% , и баланс железный.
Роль основных легирующих элементов заключается в:
С: 0.22-0.35%. C — карбидообразующий элемент, который может повысить прочность стали.. Если он слишком низкий, эффект не очевиден, и если оно слишком высокое, это значительно снизит вязкость стали.
MN: 0.45-0.60%, Mn — элемент, образующий аустенит., которые могут улучшить прокаливаемость стали, увеличить количество остаточного аустенита в стали, и влияют на однородность горячекатаной конструкции.
CR: 0.80-1.10%. Хром может улучшить механические свойства., коррозионная стойкость и прокаливаемость стали, но это может увеличить отпускную хрупкость стали.
V: 0.070-0.100%, может очищать зерно, образовывать карбиды, и улучшить прочность и ударную вязкость стали. Но когда содержание достигает определенного количества, усиление его эффекта не будет очевидным. В то же время, потому что цена высокая, объем использования должен быть ограничен.
МО: 0.70-1.10%, в основном за счет твердосплавного упрочнения и твердого раствора для повышения прочности стали., если содержание слишком велико, прочность стали уменьшится.
NB<0.050 преимущественно измельчает зерно и значительно повышает ударную вязкость высокопрочных сталей.
Ni<0.20 главным образом улучшает прочность и ударную вязкость стали, улучшает коррозионную стойкость стали, и снижает температуру хрупкого перехода стали.
Cu<0.20, медь в легированной стали может улучшить прочность и устойчивость стали к атмосферной коррозии., слишком большое количество добавок сделает сталь хрупкой, обычно не более 0.2%.
Для обеспечения превосходного соответствия прочности и ударной вязкости, способ производства нефтяной колонны по настоящему изобретению включает следующие этапы:
(1) Плавка ингредиентов: Губчатое железо и стальной лом используются в качестве сырья для производства стали., расплавленный в расплавленную сталь в электродуговой печи (ЭФФ), а жидкая сталь для изготовления нефтяных кожухов получается после рафинирования вне печи (НЧ) и вакуум (ВД) дегазация. Массовый процент композиции составляет: С: 0.22-0.35%, Si: 0.17-0.30%, MN: 0.45-0.60%, CR: 0.80-1.10%, МО: 0.70-1.10%, Al: 0.015-0.040%, Ni< 0.20%, Cu<0.20%, V: 0.070-0.100%, NB<0.050%, в качестве<0.0015%, P<0.010%, S<0.003%, и баланс железный.
(2) Непрерывное литье и прокатка: Вышеупомянутую расплавленную сталь высокой чистоты непрерывно отливают в круглую заготовку., и охлажденную непрерывнолитую заготовку нагревают в кольцевой нагревательной печи.. Температура печи нагрева трубных заготовок составляет 1300-1320 ° С. , непрерывная прокатка, фиксированное уменьшение диаметра, охлаждение, и распиловка; среди них, температура центрирования тепла равна 1260-1270 ° C, температура горячего пирсинга 1240-1250 ° C, температура непрерывной прокатки 1070-1120 ° C, а температура уменьшения фиксированного диаметра равна 910-910 °С 930 °С.
Кольцевая печь:
Температура нагрева заготовки трубы: 1280~1290℃, допустимая разница температур: ±5℃.
Процесс перфорации:
Трехроликовый конический прошивной стан используется для уменьшения деформации сдвига при прокалывании легированной стали и предотвращения таких дефектов, как трещины., складывание, и отслоение на поверхности капилляра. Скорость удлинения пирсинга 3.5-4.2, отношение диаметра к стенке равно 20-28, Скорость расширения диаметра ниже 35%, выходная скорость прошивного станка ниже 0,9 м/с., а допуск на диаметр заготовки круглой трубы непрерывной разливки должен составлять ≤±1,4%. , Допуск овальности ≤ 2.5%, обеспечить точность геометрических размеров и формы капилляра. Температура прожига 1240-1250°С..
Непрерывный процесс прокатки:
Целью процесса непрерывной прокатки является уменьшение диаметра., удлинить и уменьшить стенку капилляра, перенесенную в процессе прокалывания, и в то же время улучшить шероховатость внутренней и внешней поверхностей заготовки и улучшить однородность толщины стенки..
При непрерывной прокатке, внутренняя поверхность капилляра контактирует с оправкой в верхней части прохода, но не у боковины. Металл в верхней части отверстия растягивается за счет внешнего давления валка и давления оправки., и он расширяется в окружном направлении, одновременно расширяясь в осевом направлении., в то время как металл на боковой стенке отверстия также расширяется, когда металл в верхней части отверстия расширяется. Он растягивается и соответственно сжимается в продольном направлении.. Контролируйте скорость обжатия каждого процесса непрерывной прокатки., так, что соотношение эффективной площади поперечного сечения заготовки трубы до и после деформации в процессе непрерывной прокатки составляет 2.8 в 6.5, чтобы гарантировать, что вертикальная и горизонтальная энергия удара масляного корпуса будет одинаковой. Максимальная входная скорость непрерывной прокатки находится в пределах 1,5 м/с., скорость выхода в пределах 3,5 м/с, а отношение площади поперечного сечения капиллярной трубки к пустой трубке составляет около 3.7. Температура непрерывной прокатки составляет 1070~1120℃..
Процесс уменьшения фиксированного диаметра:
Процесс калибровки и обжатия представляет собой процесс непрерывной прокатки полых тел.. В дополнение к роли калибровки, это также требует большой скорости снижения, а количество рабочих стендов 24. Первый, Сточные трубы нагреваются до температуры от 920°C до 1050°C в нагревательной печи, а затем выпускаются. После измерения температуры поверхности на выходе рольганга, Для удаления ненужных труб из установки непрерывной прокатки в процессе прокатки используется устройство для удаления окалины водой под высоким давлением 20 МПа.. Шкала, затем прокатывают на калибровочно-редукционном стане. Температура калибрования прокатки 910-930°С., скорость на входе калибрующей прокатки составляет 0,5-1,4 м/с., скорость на выходе составляет 0,51-7 м/с., а коэффициент эффективной площади поперечного сечения находится в пределах 1.5.
(3) Термическая обработка: для вышеупомянутой пустой трубы применяется процесс термообработки с закалкой и последующим отпуском..
Процесс закалки выглядит следующим образом.: нагрев нефтяного корпуса до 940°С. до 920°С. и держать его в тепле в течение 30 минут до полного образования аустенита. Закалочная среда представляет собой маслянистую закалочную жидкость для повышения прочности и твердости стали..
Процесс закалки выглядит следующим образом.: температура отпуска 640°С. до 660°С., сохранение тепла для 2 часов, воздушное охлаждение используется для очистки кристаллических зерен, гомогенизировать структуру, устранить внутреннее напряжение, и улучшить ударную вязкость стали.
(4) Сточная труба после вышеуказанной термообработки подвергается термокалибровке и термической правке., и, наконец, дефектоскопия для получения готовой нефтяной колонны..
Для минимизации остаточного напряжения масляного корпуса, уменьшить остаточное напряжение, вызванное калибровкой, улучшить размер и точность округлости масляного корпуса, и улучшить механические свойства масляного корпуса, Температура калибровки находится между 550 а также 600 °C В течение периода, калибровочная скорость на выходе сточной трубы находится между 1.2 и 2,4 м/с.
В процессе термической правки, уменьшение предела упругости 1.55 в 1.75 раз (снижение предела упругости является отправной точкой пластической деформации поверхности стальной трубы.) и соответствующая температура правки выбрана так, чтобы уменьшить остаточное напряжение, возникающее в процессе правки.. Улучшите округлость и прямолинейность масляного корпуса и улучшите производительность масляного корпуса.. Оптимальная температура, определенная теоретическим расчетом и экспериментом, составляет 450-580°С., но в реальном процессе, ради безопасности, температура термической правки составляет 500–540 °C..
Чтобы улучшить производительность масляного кожуха, установлен строгий диапазон контроля геометрической точности. Геометрическая точность корпуса отвечает следующим требованиям.: погрешность диаметра составляет ±0,8% от размера диаметра., погрешность толщины стенки составляет ±8% от размера толщины стенки., и эллипс. Погрешность прямолинейности конца трубы составляет ±0,5%., погрешность прямолинейности конца трубы составляет 1,5 мм/м., и погрешность прямолинейности тела трубы составляет 1,0 мм/м..
Масляный корпус, изготовленный способом производства по изобретению, может достигать марки стали V150.. Показатели, достигаемые механическими свойствами масляного корпуса, следующие::
Предел текучести: 1057~1210МПа
Прочность на растяжение: ≥1180 МПа
Ударная вязкость: Полномасштабная продольная энергия удара по Шарпи ≥ 80 Дж.
Полномасштабная поперечная энергия удара по Шарпи ≥ 75 Дж.
относительное удлинение: ≥16%
Общие характеристики корпуса (в качестве примера возьмем φ244,48×15,11)
Прочность тела трубы против обрушения: ≥80 МПа;
Сила скольжения: ≥2800КН;
Предел текучести в трубе: ≥115 МПа;
Остаточный стресс: ≤200 МПа.
Геометрические размеры масляного картера;
Диапазон диаметров: 242.52мм~246,43 мм;
Из округлости: ≤1,2 мм;
толщина стенки: -8.0%t~8,0%t;
Прямолинейность: конец трубы 1,5 мм/м, тело трубы 1,0 мм/м.
Настоящее изобретение имеет следующий технический эффект.:
1. Масло обсадные трубы В настоящем изобретении используется система сплавов Cr-Ni-Mo-V, закаленная и отпущенная марка стали., который может получить определенное количество аустенитной вязкости, диспергированной на ультратонкой реечной мартенситной матрице после термообработки. Фаза, улучшить прочность и ударную вязкость стали, чтобы адаптироваться к внешней нагрузке экструзии и осевой нагрузке, создаваемой глубокими или сверхглубокими скважинами.
2. В способе производства настоящего изобретения, за счет рациональной формулировки таких процессов, как прошивка и прокатка, кристаллические зерна стали могут быть максимально измельчены, и структурных дефектов можно избежать.
3. В способе производства настоящего изобретения, разумен выбор процесса термообработки, и в качестве матрицы можно сформировать реечный мартенсит субмикронного порядка., наноразмерная частица второй фазы в качестве фазы дисперсионного упрочнения и определенное количество аустенита с высокой стабильностью.. Многофазная композитная структура жесткой фазы обеспечивает превосходное сочетание прочности и ударной вязкости..
4. В способе производства настоящего изобретения, процесс термической правки обоснованно сформулирован, что может минимизировать остаточное напряжение обсадной колонны.
5. Сформулирован строгий диапазон контроля геометрической точности., что может улучшить производительность масляного корпуса по разумной цене.
6. Закалочная среда в процессе термообработки по настоящему изобретению представляет собой маслянистую закалочную жидкость., что позволяет избежать таких дефектов, как трещины на поверхности стальной трубы..
Подробные способы
Настоящее изобретение будет подробно описано ниже вместе с конкретными примерами..
Настоящее изобретение будет подробно описано ниже на примере производства масляного кожуха диаметром 244,48×15,11..
пример:
Губчатое железо и стальной лом используются в качестве сырья для производства стали., и расплавлен в расплавленную сталь в электродуговой печи.. После рафинирования вне печи и вакуумной дегазации, компоненты расплавленной стали для изготовления нефтяных обсадных колонн: С: 0.22-0.35%, Si: 0.17-0.30%, MN: 0.45-0.60%, CR: 0.80-1.10%, МО: 0.70-1.10%, Al: 0.015-0.040%, Ni<0.20%, Cu<0.20%, V: 0.070-0.100%, NB<0.050%, в качестве<0.0015%, P<0.010%, S<0.003%, и баланс железный.
Вышеуказанную расплавленную сталь непрерывно отливают в круглую заготовку.. Нагрейте охлажденную непрерывнолитую заготовку в кольцевой нагревательной печи., температура печи нагрева трубной заготовки 1310°С., после этого, центрирование, пирсинг, непрерывная прокатка, определение размера и уменьшение, охлаждение, распиловка; среди них, температура центрирования 1265°C , температура горячего пирсинга составляет 1245°C., температура непрерывной прокатки 1100°С., а температура обжатия фиксированного диаметра составляет 920°C.. Он быстро охлаждается до 450°C с помощью охлаждающего слоя и метода обдувочного охлаждения., и распиловка. Для вышеуказанной пустой трубы применяется процесс термообработки с закалкой и последующим отпуском.: закалка при 930°С (маслянистая закалочная жидкость), отпуск при 645°С. После термической калибровки при 560°C, термическая правка при 520°C, и финальная дефектоскопия, получается готовая нефтяная колонна.
В процессе пирсинга, скорость удлинения 3.7, Скорость расширения диаметра 28%, и выходная скорость прошивного станка составляет 0,7 м/с.. В процессе непрерывной прокатки, отношение эффективной площади поперечного сечения пустой трубы до и после непрерывной деформации прокатки равно 4.3, скорость входа 1,2 м/с, и скорость на выходе 2,9 м/с.. В процессе фиксированного и уменьшенного диаметра, коэффициент эффективной площади поперечного сечения равен 1.2, скорость входа 0,9 м/с, и скорость на выходе составляет 1,3 м/с.. Скорость калибровки на выходе пустой трубы составляет 1,8 м/с.. В процессе термической правки, коэффициент уменьшения выпрямления равен 1.6 раз уменьшение предела упругости.
Механические свойства нефтяной колонны, изготовленной указанным способом, могут достигать следующих показателей::
Предел текучести: 1109MPa;
Прочность на растяжение: 1213MPa;
Ударная вязкость: Продольная полномасштабная энергия удара по Шарпи: 121J;
Горизонтальная полномасштабная энергия удара по Шарпи: 114J;
относительное удлинение: 17%.
Общие характеристики корпуса:
Прочность трубы на разрушение: 93.1MPa;
Сила скольжения: 3208КН;
Предел текучести в трубке: 130.6MPa;
Остаточный стресс: 162.31MPa.
Геометрические размеры масляного картера:
Диапазон диаметров: 245.90мм~246,20 мм;
Из округлости: ≤0,6 мм;
толщина стенки: -4.5%t~7,0%t;
Прямолинейность: конец трубы 1,2 мм/м, тело трубы 0,9‰.
Нефтяная колонна, изготовленная с использованием стальной конструкции согласно изобретению и разумного контроля различных технологических условий, может соответствовать требованиям прочности и ударной вязкости, предъявляемым к глубоким и сверхглубоким скважинам.. Контроль деформации прокатки и термообработки, получить такие эффекты, как усиление осадков, измельчение зерна и усиление фазового превращения, повысить прочность и ударную вязкость стали, и решить проблему легких трещин при термообработке бесшовных стальных труб из легированной стали.. Использование методов термической калибровки и термической правки., решена проблема низкого остаточного напряжения, необходимого для бесшовных стальных труб., и изгиб, эллиптическая деформация, и точность размеров бесшовных стальных труб контролируются.