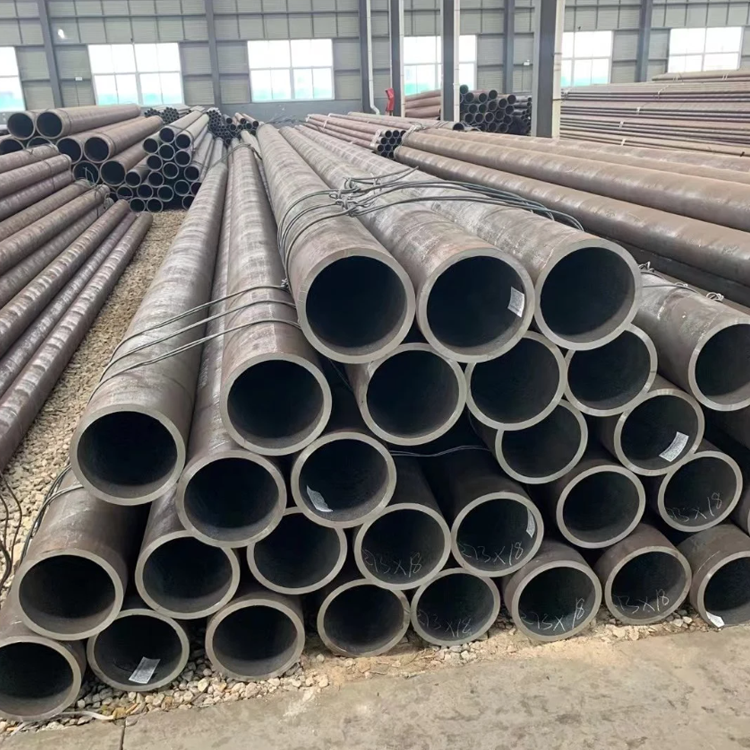
Strukturelles nahtloses Stahlrohr
August 22, 2023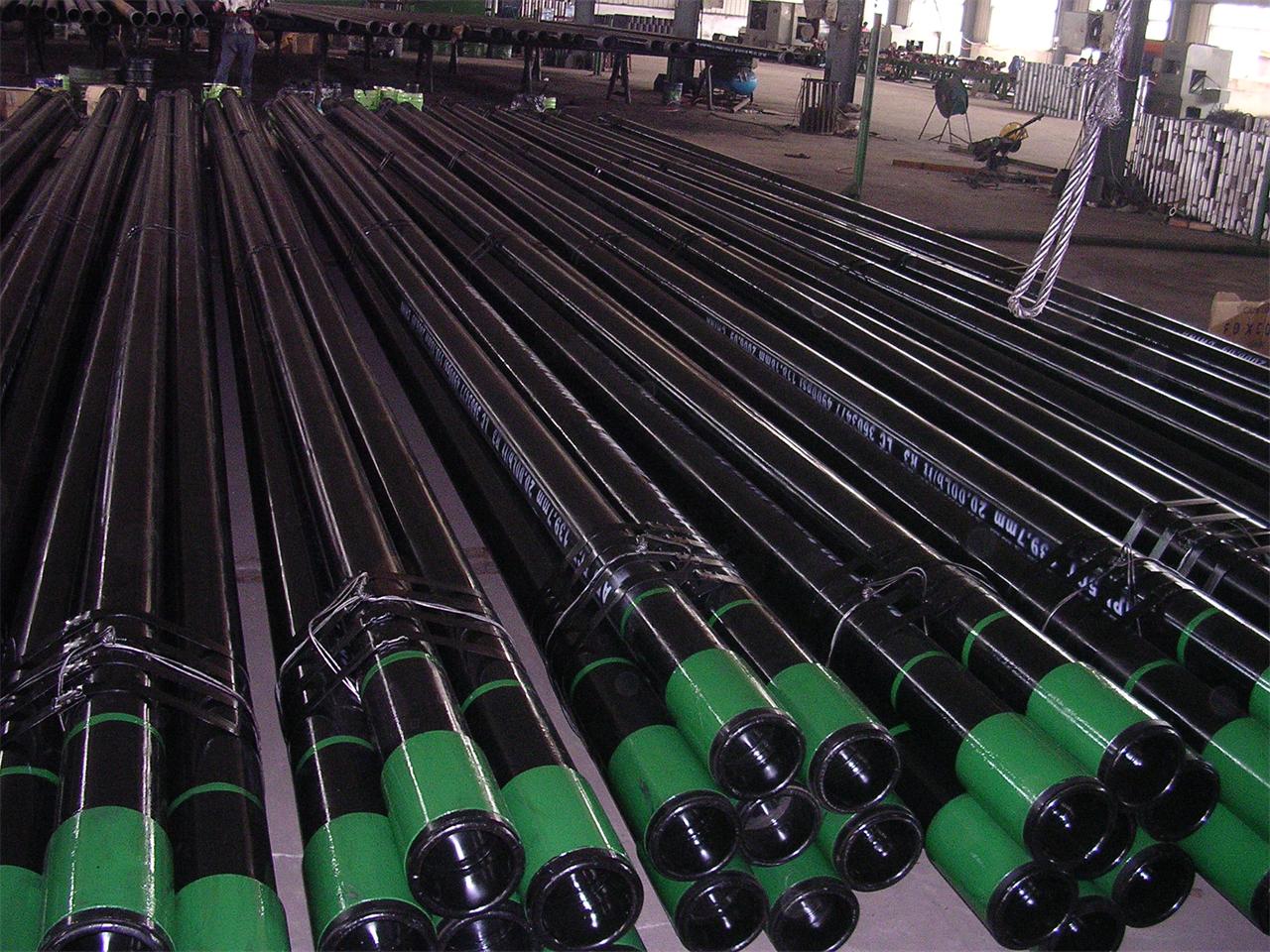
Wärmebehandlungsprozess für Ölmantelrohre,Wie werden die Ölgehäuse geprüft und getestet, um ihre Qualität sicherzustellen??
September 4, 2023Ölgehäuse mit hoher Festigkeit und Zähigkeit und Verfahren zu seiner Herstellung
Beschreibung
Ein Ölgehäuse mit hoher Festigkeit und Zähigkeit ist eine entscheidende Komponente bei Öl- und Gasbohrarbeiten. Es ist für hohen Druck ausgelegt, abrasive Materialien, und korrosiven Umgebungen, häufig bei Bohrarbeiten anzutreffen. Das Ölgehäuse besteht häufig aus Stahl und sollte bestimmte Eigenschaften wie eine hohe Festigkeit aufweisen, Zähigkeit, und Korrosion Widerstand.
Produktionsmethode
Die Produktionsmethode umfasst mehrere Schritte, inklusive der Materialauswahl, Wärmebehandlung, Bildung, und Inspektion.
1. Diese Informationen haben die hohe Festigkeit und Duktilität des Materials bestätigt
Das Grundmaterial für das Gehäuse ist in der Regel hochwertiger Kohlenstoffstahl oder legierter Stahl. Das Material wird basierend auf den erwarteten Bedingungen des Bohrvorgangs ausgewählt, wie zum Beispiel die Temperatur, Druck, und korrosive Umgebung.
2. Bildung
Der Stahl wird auf eine bestimmte Temperatur erhitzt und dann zu Rohren geformt. Dies erfolgt häufig durch Warmwalzen, Dabei wird der Stahl durch eine Reihe von Walzen geführt, die ihn in die gewünschte Rohrform und -größe bringen. Anschließend werden die Rohre abgekühlt und gehärtet.
3. Wärmebehandlung
Nächste, Die Rohre werden einem Wärmebehandlungsprozess unterzogen. Dies kann Abschrecken und Anlassen umfassen, die zur Erhöhung der Festigkeit und Zähigkeit des Stahls dienen. Beim Abschrecken wird der Stahl auf eine Temperatur erhitzt Schwefelwasserstoff- und Chloridgehalt und dann schnell abkühlen, Beim Anlassen wird der Stahl auf eine niedrigere Temperatur erhitzt und dann langsam abgekühlt.
4. Inspektion und Prüfung
Endlich, Die Rohre werden geprüft und getestet, um sicherzustellen, dass sie den erforderlichen Standards entsprechen. Hierzu können auch Sichtprüfungen gehören, Härteprüfung, und Ultraschallprüfung. Wenn die Rohre diese Tests bestehen, Anschließend können sie als Ölgehäuse verwendet werden.
Dies ist ein grundlegender Überblick darüber, wie Ölgehäuse mit hoher Festigkeit und Zähigkeit hergestellt werden. Die eigentlichen Prozesse können komplexer sein und je nach den spezifischen Anforderungen an das Gehäuse variieren.
Vorteile
- Erhöhte Haltbarkeit: Die hohe Festigkeit und Zähigkeit dieser Ölgehäuse ermöglicht es ihnen, hohem Druck und abrasiven Materialien standzuhalten, Sie verlängern ihre Lebensdauer und verringern den Bedarf an Ersatzteilen.
- Verbesserte Sicherheit: Diese Eigenschaften erhöhen auch die Sicherheit bei Bohrarbeiten, da sie das Risiko eines Gehäuseversagens verringern, was zu katastrophalen Unfällen führen kann.
- Kosteneffizient: Allerdings kann der Produktionsprozess komplexer und kostspieliger sein, Die erhöhte Haltbarkeit und Sicherheit dieser Gehäuse kann langfristig zu erheblichen Kosteneinsparungen führen.
Der Vergleich zwischen den Kriechversuchsdaten und den Simulationsergebnissen bei drei verschiedenen Temperaturen ist in dargestellt
Die Herstellung von Ölgehäusen mit hoher Festigkeit und Zähigkeit ist ein entscheidender Aspekt für die Gewährleistung sicherer und effizienter Bohrvorgänge. Der Produktionsprozess kann zwar komplex sein, die Vorteile hinsichtlich der Haltbarkeit, Sicherheit, und Kosteneinsparungen machen es zu einer lohnenden Investition.
Die Erfindung gehört zum technischen Gebiet der Herstellung nahtloser Stahlrohre in der metallurgischen Industrie, und betrifft insbesondere ein Ölgehäuse mit superhoher Festigkeit und Zähigkeit, das für Tiefbrunnen oder Ultratiefbrunnen geeignet ist, und ein Herstellungsverfahren dafür.
Das Pulver wird durch Hitze geschmolzen und zu einem Film eingeebnet und verfestigt
Mit zunehmender Bohrtiefe in Öl- und Gasfeldern, der Anstieg von Temperatur und Druck, Die geologische Umgebung der Erdölgehäuse, die für feste Bohrlochköpfe verwendet werden, hat sich erheblich verändert, und auch die verwendeten mechanischen Bedingungen haben sich entsprechend geändert. Die von ihm aufgenommene äußere Extrusionslast und die axialen Belastungen werden immer höher. Hochwertige Ölgehäuse wie das vom American Petroleum Institute spezifizierte V125 verwenden im Allgemeinen legierte Stähle der Cr-Mo-V-Serie. Aufgrund der komplexen Verhüttung, Walz- und Wärmebehandlungsprozesse von Ölgehäusen dieser Stahlsorte, Die Legierungszusammensetzung und das Herstellungsverfahren sind nicht geeignet. , führt dazu, dass die Festigkeit und Zähigkeit des Ölgehäuses abnimmt, und kann der externen Extrusionsbelastung und der axialen Belastung durch tiefe oder ultratiefe Bohrlöcher nicht standhalten, was die Beschädigung und den Ausfall des Ölgehäuses verschlimmert, und die Beschädigung und das Versagen des Gehäuses führen leicht zum Versagen des Bohrlochs. Komplexe Probleme wie Instabilität, Beschädigung des Reservoirs, Schwierigkeiten beim Bohren und Zementieren, usw., gefährden ernsthaft die Sicherheit des Ölfeldbetriebs, und sogar zu großen wirtschaftlichen Verlusten führen, beispielsweise durch Bohrunfälle. Deshalb, Das Ölfeld stellt höhere Anforderungen an die Leistung des Ölgehäuses.
Gegenwärtig, Das zu lösende Problem bei Ölgehäusen für tiefe oder ultratiefe Bohrlöcher ist die Abstimmung von ultrahoher Festigkeit und hoher Zähigkeit. Die Leistung hochfester und robuster Ölgehäuse hängt nicht nur von der verwendeten Materialzusammensetzung ab, sondern auch eng mit der Herstellungsmethode verbunden. Wie wir alle wissen, Die Schlagzähigkeit von ultrahochfestem Stahl hängt von der Reinheit des Stahls ab, die Zusammensetzung und Verfeinerung der Struktur. Um den Schwefelgehalt zu reduzieren, wird eine hochreine Schmelztechnologie eingesetzt, Phosphorverunreinigungselemente und Gase in ultrahochfestem Stahl so weit wie möglich zu reduzieren, und die Anzahl der Einschlüsse reduzieren, so dass eine zufriedenstellende Schlagzähigkeit erreicht werden kann. Verwendung eines geeigneten Wärmebehandlungsverfahrens, Die Mikrostruktur, die durch ultrafeinen Lattenmartensit als Matrix und dispergierte duktile Austenitphase gekennzeichnet ist, wird in ultrahochfestem Stahl erhalten, und während des Walz- und Richtprozesses erhalten werden. Hochpräzise Ölgehäusegröße und Oberflächenqualität sowie niedrige Eigenspannungen sind die wichtigsten technischen und effektiven Möglichkeiten, um Ölgehäuse mit extrem hoher Festigkeit und Zähigkeit zu erreichen.
Jedoch, Die derzeit in Ölgehäusen verwendeten Stahlsorten enthalten hohe Verunreinigungen wie Schwefel und Phosphor, und die Metallstruktur enthält schuppige Einschlüsse. Der ungleichmäßige Metallfluss während des Walzprozesses führt zu inkonsistenten mechanischen Eigenschaften in horizontaler und vertikaler Richtung. Außerdem, in der aktuellen Ölgehäuse-Produktionsmethode, Das Abschreckmedium im Wärmebehandlungsprozess ist Wasser, was leicht zu Rissen führen kann. Gleichzeitig, aufgrund des unzumutbaren Einstech- und Rollvorgangs, Wärmebehandlungsverfahren und Richtmethode, Das Beste: Stärke und Zähigkeit des Gehäuses stimmen überein, und eine übermäßige Eigenspannung verursachen, und die geometrische Maßhaltigkeit des Gehäuses ist schlecht, Dies wirkt sich direkt auf die Fähigkeit des Produkts aus, einem Kollaps zu widerstehen.
Inhalt der Erfindung
Der Zweck der Erfindung besteht darin, die Mängel im Stand der Technik zu überwinden und ein Ölgehäuse mit hoher Festigkeit und Zähigkeit bereitzustellen, das den Anforderungen von Tiefbohrungen oder ultratiefen parallelen Produktionsbedingungen in Ölfeldern gerecht wird.
Eine weitere Aufgabe der vorliegenden Erfindung besteht darin, ein Herstellungsverfahren für ein Ölgehäuse mit hoher Festigkeit und Zähigkeit bereitzustellen, die den Produktionsbedingungen von Tiefbrunnen oder Ultratiefbrunnen in Ölfeldern gerecht werden können.
Die vorliegende Erfindung wird durch das folgende technische Schema realisiert:
Ein Ölgehäuse mit hoher Festigkeit und Zähigkeit, dadurch gekennzeichnet, dass es sich bei den Komponenten um Gewichtsprozente handelt: C: 0.22-0.35%, Si: 0.17-0.30%, MN: 0.45-0.60%, CR: 0.80-1.10%, Mo: 0.70-1.10%, Al: 0.015-0.040%, NI<0.20%, Cu<0.20%, V: 0.070-0.100%, NB<0.050%, als<0.0015%, P<0.010%, S<0.003% , und der Rest ist Eisen.
Die Rolle der Hauptlegierungselemente ist:
C: 0.22-0.35%. C ist ein karbidbildendes Element, das die Festigkeit von Stahl erhöhen kann. Wenn es zu niedrig ist, Der Effekt ist nicht offensichtlich, und wenn es zu hoch ist, Dadurch wird die Zähigkeit von Stahl erheblich verringert.
MN: 0.45-0.60%, Mn ist ein austenitbildendes Element, was die Härtbarkeit von Stahl verbessern kann, Erhöhen Sie die Menge an Restaustenit im Stahl, und beeinflussen die Gleichmäßigkeit der warmgewalzten Struktur.
CR: 0.80-1.10%. Chrom kann die mechanischen Eigenschaften verbessern, Korrosionsbeständigkeit und Härtbarkeit von Stahl, Es kann jedoch die Anlasssprödigkeit von Stahl erhöhen.
V: 0.070-0.100%, kann Getreide verfeinern, Karbide bilden, und die Festigkeit und Zähigkeit von Stahl verbessern. Aber wenn der Inhalt eine gewisse Menge erreicht, die Steigerung seiner Wirkung wird nicht offensichtlich sein. Gleichzeitig, weil der Preis hoch ist, Die Nutzungsmenge sollte begrenzt sein.
Mo: 0.70-1.10%, hauptsächlich durch Karbid- und Mischkristallverfestigung zur Erhöhung der Festigkeit von Stahl, wenn der Inhalt zu hoch ist, die Zähigkeit von Stahl wird verringert.
NB<0.050 Verfeinert vor allem die Körnung und verbessert die Zähigkeit hochfester Stähle deutlich.
NI<0.20 Verbessert hauptsächlich die Festigkeit und Zähigkeit von Stahl, verbessert die Korrosionsbeständigkeit von Stahl, und senkt die Sprödigkeitsübergangstemperatur von Stahl.
Cu<0.20, Kupfer im legierten Stahl kann die Festigkeit und die atmosphärische Korrosionsbeständigkeit des Stahls verbessern, Zu viel Zusatz macht den Stahl spröde, im Allgemeinen nicht mehr als 0.2%.
Um eine hervorragende Festigkeits- und Zähigkeitsanpassung zu gewährleisten, Das Herstellungsverfahren des Ölgehäuses der vorliegenden Erfindung umfasst die folgenden Schritte:
(1) Zutaten schmelzen: Als Rohstoffe für die Stahlerzeugung werden Eisenschwamm und Stahlschrott verwendet, in einem Elektrolichtbogenofen zu geschmolzenem Stahl geschmolzen (EFF), und geschmolzener Stahl zur Herstellung von Ölgehäusen wird nach dem Raffinieren außerhalb des Ofens gewonnen (LF) und Vakuum (VD) Entgasung Die Zusammensetzung ist in Gewichtsprozent angegeben: C: 0.22-0.35%, Si: 0.17-0.30%, MN: 0.45-0.60%, CR: 0.80-1.10%, Mo: 0.70-1.10%, Al: 0.015-0.040%, NI< 0.20%, Cu<0.20%, V: 0.070-0.100%, NB<0.050%, als<0.0015%, P<0.010%, S<0.003%, und der Rest ist Eisen.
(2) Stranggießen und Walzen: Der oben erwähnte hochreine geschmolzene Stahl wird kontinuierlich zu einem runden Barren gegossen, und der abgekühlte Stranggussbarren wird in einem ringförmigen Heizofen erhitzt. Die Temperatur des Rohrknüppel-Heizofens beträgt 1300-1320 ° C. , kontinuierliches Rollen, feste Durchmesserreduzierung, Kühlung, und Sägen; darunter, die Wärmezentrierungstemperatur beträgt 1260-1270 ° C, die Heißstechtemperatur beträgt 1240-1250 ° C, die kontinuierliche Walztemperatur beträgt 1070-1120 ° C, und die feste Durchmesserverringerungstemperatur beträgt 910-910 °C 930°C.
Ringofen:
Erwärmungstemperatur des Rohrrohlings: 1280~1290℃, zulässiger Temperaturunterschied: ±5℃.
Perforationsprozess:
Ein konischer Locher mit drei Rollen wird verwendet, um die Scherbeanspruchung des legierten Stahls beim Einstechen zu reduzieren und Defekte wie Risse zu verhindern, falten, und Delamination auf der Oberfläche der Kapillare. Die Dehnungsrate des Piercings beträgt 3.5-4.2, Das Durchmesser-zu-Wand-Verhältnis beträgt 20-28, Die Durchmesserausdehnungsrate ist unten 35%, Die Austrittsgeschwindigkeit der Lochstechmaschine liegt unter 0,9 m/s, und die Durchmessertoleranz des Strangguss-Rundrohrrohlings muss ≤ ±1,4 % betragen , Ovalitätstoleranz ≤ 2.5%, um die geometrische Größe und Formgenauigkeit der Kapillare sicherzustellen. Die Einstechtemperatur beträgt 1240-1250°C.
Kontinuierlicher Walzprozess:
Der Zweck des kontinuierlichen Walzprozesses besteht darin, den Durchmesser zu reduzieren, Die durch den Durchstechvorgang übertragene Wand des Kapillarröhrchens wird verlängert und verkleinert, und gleichzeitig die Rauheit der Innen- und Außenflächen des Rohlingsrohrs verbessern und die Gleichmäßigkeit der Wandstärke verbessern.
Beim kontinuierlichen Rollen, Die Innenfläche der Kapillare steht am oberen Ende des Durchgangs mit dem Dorn in Kontakt, aber nicht an der Seitenwand. Das Metall am oberen Ende des Lochs wird durch den Außendruck der Walze und den Druck des Dorns gedehnt, und es dehnt sich in Umfangsrichtung aus, während es sich axial erstreckt, während sich das Metall an der Seitenwand des Lochs ebenfalls ausdehnt, wenn sich das Metall an der Oberseite des Lochs ausdehnt. Es wird gedehnt und schrumpft entsprechend in Längsrichtung. Kontrollieren Sie die Reduktionsrate jedes Prozesses des kontinuierlichen Walzens, so dass das Verhältnis der wirksamen Querschnittsfläche des Rohrrohlings vor und nach der Verformung im kontinuierlichen Walzprozess beträgt 2.8 An 6.5, um sicherzustellen, dass die vertikale und horizontale Aufprallenergie des Ölgehäuses tendenziell gleichmäßig ist. Die maximale Eintrittsgeschwindigkeit beim kontinuierlichen Walzen liegt innerhalb von 1,5 m/s, Die Austrittsgeschwindigkeit liegt innerhalb von 3,5 m/s, und das Verhältnis der Querschnittsfläche des Kapillarrohrs zum Blindrohr beträgt etwa 3.7. Die kontinuierliche Walztemperatur beträgt 1070 bis 1120 °C.
Prozess zur Reduzierung des festen Durchmessers:
Der Kalibrier- und Reduzierprozess ist ein Prozess des kontinuierlichen Walzens von Hohlkörpern. Zusätzlich zur Rolle der Dimensionierung, es erfordert auch eine große Reduktionsrate, und die Anzahl der Arbeitsstände beträgt 24. Zuerst, Im Nachwärmofen werden die Abfallrohre auf 920°C bis 1050°C erhitzt und anschließend freigegeben. Nach der Messung der Oberflächentemperatur am Ausgang des Rollganges, Während des Walzvorgangs wird ein 20-MPa-Hochdruckwasser-Entzunderungsgerät verwendet, um die Abfallrohre aus der kontinuierlichen Walzeinheit zu entfernen. Skala, Anschließend wird es in einem Kalibrier- und Reduzierwalzwerk gewalzt. Die Schlichtewalztemperatur beträgt 910-930°C, Die Eintrittsgeschwindigkeit des Schlichtwalzens liegt zwischen 0,5 und 1,4 m/s, Die Austrittsgeschwindigkeit liegt zwischen 0,51 und 7 m/s, und das effektive Querschnittsflächenverhältnis liegt innerhalb 1.5.
(3) Wärmebehandlung: Der Wärmebehandlungsprozess des Abschreckens und anschließenden Anlassens wird für das oben erwähnte Rohlingsrohr übernommen.
Der Abschreckvorgang ist wie folgt: Erhitzen des Erdölgehäuses auf 940° C. bis 920°C. und es warm zu halten 30 Minuten, bis sich Austenit vollständig gebildet hat. Das Abschreckmedium ist eine ölige Abschreckflüssigkeit zur Erhöhung der Festigkeit und Härte des Stahls.
Der Tempervorgang ist wie folgt: die Anlasstemperatur beträgt 640° C. bis 660°C., Wärmekonservierung für 2 Stunden, Zur Verfeinerung der Kristallkörner wird Luftkühlung eingesetzt, Homogenisieren Sie die Struktur, inneren Stress beseitigen, und verbessern die Zähigkeit des Stahls.
(4) Nach der oben genannten Wärmebehandlung wird das Abfallrohr einer Wärmekalibrierungs- und Wärmerichtbehandlung unterzogen, und schließlich die Fehlererkennung, um das fertige Erdölgehäuse zu erhalten.
Um die Eigenspannung des Ölgehäuses zu minimieren, Reduzieren Sie die durch die Dimensionierung verursachte Eigenspannung, Verbessern Sie die Größen- und Rundheitsgenauigkeit des Ölgehäuses, und verbessern die mechanischen Eigenschaften des Ölgehäuses, Die Schlichtetemperatur liegt zwischen 550 und 600 °C Während des Zeitraums, Die Größe der Auslassgeschwindigkeit des Abfallrohrs liegt zwischen 1.2 und 2,4 m/s.
Im thermischen Richtverfahren, die Elastizitätsgrenzenreduzierung von 1.55 An 1.75 mal (Die Reduzierung der Elastizitätsgrenze ist der Ausgangspunkt der plastischen Verformung der Stahlrohroberfläche) und die geeignete Richttemperatur werden ausgewählt, um die durch den Richtvorgang erzeugte Eigenspannung zu reduzieren. Verbessern Sie die Rundheit und Geradheit des Ölgehäuses und verbessern Sie die Leistung des Ölgehäuses. Die durch theoretische Berechnungen und Experimente ermittelte optimale Temperatur beträgt 450–580 °C, sondern im eigentlichen Prozess, Aus Sicherheitsgründen, Die thermische Richttemperatur liegt zwischen 500°C-540°C.
Um die Leistung des Ölgehäuses zu verbessern, Es wurde ein strenger Kontrollbereich für die geometrische Genauigkeit festgelegt. Die geometrische Genauigkeit des Gehäuses erfüllt die folgenden Anforderungen: Der Durchmesserfehler beträgt ±0,8 % der Durchmessergröße, Der Wanddickenfehler beträgt ±8 % der Wanddickengröße, und der Ellipse Der Geradheitsfehler des Rohrendes beträgt ±0,5 %, Der Geradheitsfehler des Rohrendes beträgt 1,5 mm/m, und der Geradheitsfehler des Rohrkörpers beträgt 1,0 mm/m.
Das mit dem erfindungsgemäßen Herstellungsverfahren hergestellte Ölgehäuse kann die Stahlgüte V150 erreichen. Die durch die mechanischen Eigenschaften des Ölgehäuses erreichten Indikatoren sind wie folgt:
Streckgrenze: 1057~1210 MPa
Zugfestigkeit: ≥1180 MPa
Schlagzähigkeit: Charpy-Schlagenergie in Längsrichtung ≥ 80 J
Transversale Charpy-Aufprallenergie ≥ 75 J
Dehnung: ≥16 %
Die Gesamtleistung des Gehäuses (Nehmen Sie als Beispiel φ244,48×15,11)
Kollapsfestigkeit des Rohrkörpers: ≥80 MPa;
Rutschfestigkeit: ≥2800KN;
Streckgrenze im Rohr: ≥115 MPa;
Verbleibender Stress: ≤200 MPa.
Geometrische Abmessungen des Ölgehäuses;
Durchmesserbereich: 242.52mm ~ 246,43 mm;
Unrundheit: ≤1,2 mm;
Wandstärke: -8.0%t~8,0%t;
Geradheit: Rohrende 1,5 mm/m, Rohrkörper 1,0 mm/m.
Die vorliegende Erfindung hat folgende technische Wirkung:
1. Das Öl Bohrrohr Die vorliegende Erfindung verwendet eine vergütete Stahlsorte des Cr-Ni-Mo-V-Legierungssystems, Dadurch kann nach der Wärmebehandlungsphase eine bestimmte Menge an Austenitzähigkeit erreicht werden, die auf der ultrafeinen Latten-Martensitmatrix verteilt ist, Verbessern Sie die Festigkeit und Zähigkeit von Stahl, um ihn an die äußere Extrusionsbelastung und die axiale Belastung durch tiefe oder ultratiefe Bohrlöcher anzupassen.
2. Im Herstellungsverfahren der vorliegenden Erfindung, durch rationale Formulierung von Prozessen wie Lochen und Rollen, Die Kristallkörner von Stahl können weitestgehend verfeinert werden, und bauliche Mängel können vermieden werden.
3. Im Herstellungsverfahren der vorliegenden Erfindung, Die Auswahl des Wärmebehandlungsverfahrens ist sinnvoll, und es ist möglich, einen Lattenmartensit im Submikronbereich als Matrix zu bilden, ein nanoskaliges Zweitphasenpartikel als Ausscheidungsverfestigungsphase und eine bestimmte Menge Austenit mit hoher Stabilität. Die mehrphasige Verbundstruktur der Zähphase sorgt für eine hervorragende Festigkeits- und Zähigkeitsanpassung.
4. Im Herstellungsverfahren der vorliegenden Erfindung, Der thermische Richtprozess ist sinnvoll formuliert, Dadurch kann die Eigenspannung des Gehäuses minimiert werden.
5. Es wurde ein strenger Kontrollbereich für die geometrische Genauigkeit formuliert, Dadurch kann die Leistung des Ölgehäuses zu angemessenen Kosten verbessert werden.
6. Das Abschreckmedium im Wärmebehandlungsverfahren der vorliegenden Erfindung ist eine ölige Abschreckflüssigkeit, Dadurch können Defekte wie Risse auf der Oberfläche des Stahlrohrs vermieden werden.
Detaillierte Wege
Die vorliegende Erfindung wird nachstehend im Detail in Verbindung mit spezifischen Beispielen beschrieben.
Die vorliegende Erfindung wird im Folgenden detailliert beschrieben, wobei die Herstellung eines Ölgehäuses mit einem Durchmesser von 244,48 × 15,11 als Beispiel genommen wird.
Beispiel:
Als Rohstoffe für die Stahlerzeugung werden Eisenschwamm und Stahlschrott verwendet, und in einem Elektrolichtbogenofen zu geschmolzenem Stahl geschmolzen. Nach dem Raffinieren außerhalb des Ofens und der Vakuumentgasung, Die Komponenten aus geschmolzenem Stahl zur Herstellung von Erdölgehäusen sind: C: 0.22-0.35%, Si: 0.17-0.30%, MN: 0.45-0.60%, CR: 0.80-1.10%, Mo: 0.70-1.10%, Al: 0.015-0.040%, NI<0.20%, Cu<0.20%, V: 0.070-0.100%, NB<0.050%, als<0.0015%, P<0.010%, S<0.003%, und der Rest ist Eisen.
Der oben genannte geschmolzene Stahl wird kontinuierlich zu einem runden Barren gegossen. Erhitzen Sie den abgekühlten Stranggussbarren im Ringheizofen, Die Temperatur des Rohrknüppel-Erwärmungsofens beträgt 1310 °C, danach, Zentrierung, durchbohren, kontinuierliches Rollen, Dimensionierung und Reduzierung, Kühlung, Der Stahl wird dann warmgewalzt, um ihn in seine endgültige Form zu bringen. Vorblöcke und Knüppel werden zu Stangen und Drähten geformt; darunter, die Wärmezentrierung liegt bei 1265°C , Die Heißstechtemperatur beträgt 1245°C, die kontinuierliche Walztemperatur beträgt 1100°C, und die feste Durchmesserreduzierungstemperatur beträgt 920°C. Durch die Kühlbett- und Blaskühlungsmethode wird es schnell auf 450 °C abgekühlt, und Sägen. Der Wärmebehandlungsprozess des Abschreckens und anschließenden Anlassens wird für das obige Rohlingsrohr übernommen: Abschrecken bei 930°C (ölige Abschreckflüssigkeit), Anlassen bei 645°C. Nach der Heißleimung bei 560 °C, Hitzeglätten bei 520°C, und abschließende Fehlererkennung, Man erhält das fertige Ölgehäuse.
Im Piercing-Prozess, die Dehnungsrate ist 3.7, Die Durchmesserausdehnungsrate beträgt 28%, und die Austrittsgeschwindigkeit der Lochmaschine beträgt 0,7 m/s. Im kontinuierlichen Walzverfahren, das Verhältnis der effektiven Querschnittsfläche des unfruchtbaren Rohres vor und nach der kontinuierlichen Walzverformung beträgt 4.3, die Eintrittsgeschwindigkeit beträgt 1,2m/s, und die Austrittsgeschwindigkeit beträgt 2,9 m/s. Im Verfahren mit festem und reduziertem Durchmesser, das effektive Querschnittsflächenverhältnis ist 1.2, die Eintrittsgeschwindigkeit beträgt 0,9m/s, und die Austrittsgeschwindigkeit beträgt 1,3 m/s. Die Kalibrieraustrittsgeschwindigkeit des Rohlingsrohrs beträgt 1,8 m/s. Im thermischen Richtverfahren, der Richtreduktionskoeffizient ist 1.6 mal die Reduzierung der Elastizitätsgrenze.
Die mechanischen Eigenschaften des nach dem oben genannten Verfahren hergestellten Ölgehäuses können die folgenden Indikatoren erreichen:
Streckgrenze: 1109MPa;
Zugfestigkeit: 1213MPa;
Schlagzähigkeit: Längsvolle Charpy-Aufprallenergie: 121J;
Horizontale, vollständige Charpy-Aufprallenergie: 114J;
Dehnung: 17%.
Die Gesamtleistung des Gehäuses:
Rohreinsturzfestigkeit: 93.1MPa;
Rutschfestigkeit: 3208KN;
Streckgrenze im Rohr: 130.6MPa;
Verbleibender Stress: 162.31MPa.
Geometrische Abmessungen des Ölgehäuses:
Durchmesserbereich: 245.90mm ~ 246,20 mm;
Unrundheit: ≤0,6 mm;
Wandstärke: -4.5%t~7,0%t;
Geradheit: Rohrende 1,2 mm/m, Rohrkörper 0,9‰.
Das durch das erfindungsgemäße Stahldesign und die angemessene Kontrolle verschiedener Prozessbedingungen hergestellte Ölgehäuse kann die Festigkeits- und Zähigkeitsanforderungen von Tiefbrunnen oder Ultratiefbrunnen erfüllen. Kontrollieren Sie die Walzverformung und die Wärmebehandlung, Effekte wie Niederschlagsverstärkung erzielen, Kornverfeinerung und Phasenumwandlungsstärkung, Verbessern Sie die Festigkeit und Zähigkeit von Stahl, und das Problem leichter Risse bei der Wärmebehandlung von nahtlosen Stahlrohren aus legiertem Stahl lösen. Verwendung thermischer Schlichte- und thermischer Richtverfahren, Die für nahtlose Stahlrohre erforderliche geringe Eigenspannung wird gelöst, und das Biegen, elliptische Verformung, und Maßgenauigkeit nahtloser Stahlrohre werden kontrolliert.