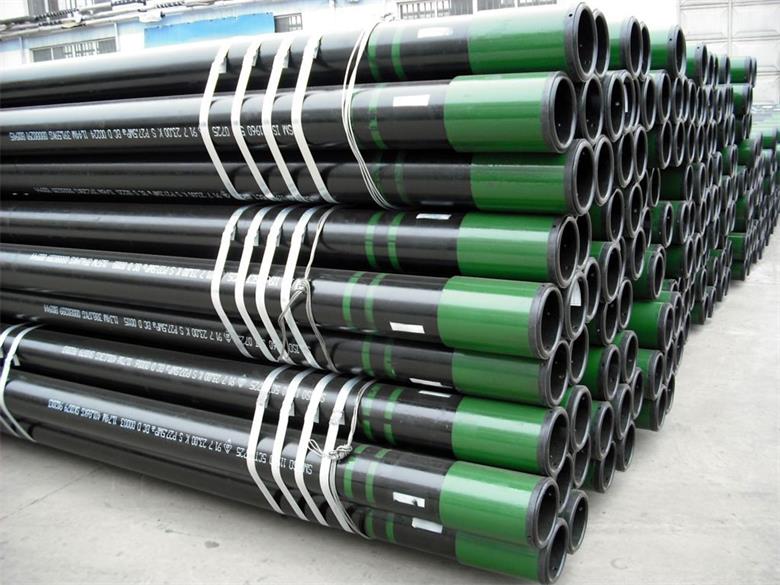
Oil casing with high strength and toughness and production method thereof
September 4, 2023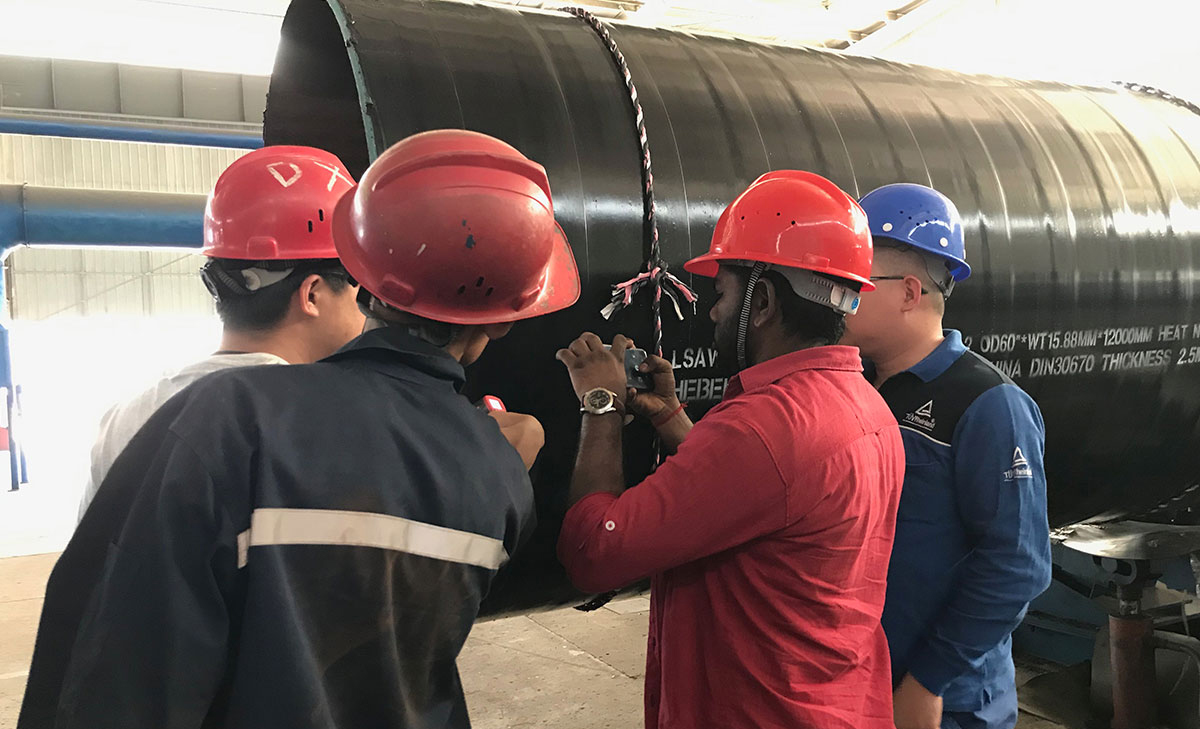
What is the difference between FBE coating pipe and epoxy coating pipe ?
September 7, 2023oil casing pipes heat treatment process,How are the oil casings inspected and tested to ensure their quality?
Can you provide more details about the heat treatment process for oil casings?
Sure, heat treatment for oil casings is a crucial process for enhancing the mechanical properties and corrosion resistance of the casing material. The process primarily involves heating, holding, and cooling operations, which change the microstructure of the material and hence its properties.
Here’s a general outline of the heat treatment process for oil casings:
1. Normalizing:
This is the first step in the heat treatment process. The oil casing is heated to a specific temperature above its critical point, typically 850-900°C, and then cooled in open air. The purpose of this process is to refine the grain structure of the steel and improve its mechanical properties.
2. Quenching:
In quenching, the casing is heated to a high temperature, above the critical point, and then rapidly cooled using water or oil. The purpose of this process is to increase the steel’s hardness and strength, but it also makes the steel more brittle.
3. Tempering:
To reduce the brittleness induced by quenching, tempering is performed. The casing is reheated to a temperature below the critical point (between 200°C and 700°C), and then cooled. This results in a good balance of hardness, strength, and toughness.
4. Quenching and Tempering (Q&T)
This is a combination of the above processes, where the casing undergoes quenching followed by tempering. This process is also known as “through-hardening”. It provides the steel with high strength and toughness.
5. Annealing:
This process involves heating the casing to a specific temperature, maintaining this temperature for a certain period, and then slowly cooling it. This process is used to reduce hardness, increase ductility, and help eliminate internal stresses.
6. Case Hardening:
For some specific applications, only the surface of the casing needs to be hardened. This is achieved through processes like carburizing or nitriding where the material is heated in a carbon-rich or nitrogen-rich environment. The surface layer of the casing absorbs these elements, changing its composition and making it harder.
Remember, the exact temperatures and durations for each process can vary based on the type of steel and the required properties for the specific application of the oil casing. It’s also important to control the heating and cooling rates precisely to prevent unwanted changes or defects in the material.
It’s also worth noting that not all oil casings undergo all these heat treatment processes. The choice of heat treatment process(es) depends on the desired mechanical properties required for a particular application.
How are the oil casings inspected and tested to ensure their quality?
Oil casings are a critical part of the drilling and extraction process in the oil and gas industry. They are used to line the inside of a wellbore and prevent it from collapsing. The quality of oil casings is paramount, as a failure could lead to catastrophic results, including environmental damage and loss of the well.
Here are the common methods for inspecting and testing oil casings to ensure their quality:
- Visual Inspection: The first step in testing oil casings is a visual inspection. This involves looking for obvious signs of damage or wear, such as cracks, corrosion, or deformities.
- Magnetic Particle Inspection (MPI): This non-destructive testing method involves magnetizing the casing and then applying fine magnetic particles to the surface. If there are any cracks or flaws in the casing, the particles will be attracted to these areas, making them visible.
- Ultrasonic Testing (UT): UT is a non-destructive testing technique that uses high-frequency sound waves to detect imperfections in the casing. The sound waves are reflected off flaws in the material, and the reflected waves are then measured and analyzed. This method can detect both surface and subsurface defects.
- Eddy Current Testing (ECT): This method uses electromagnetic fields to detect flaws in conductive materials. A coil carrying current is placed near the casing, and the changes in the electromagnetic response are then used to identify defects.
- Radiographic Testing (RT): RT uses high-energy radiation to inspect the casing. The radiation is passed through the casing onto a detector or film on the other side. Any flaws or defects in the casing will show up as dark areas on the film.
- Hydrostatic Testing: This method involves filling the casing with a liquid, usually water, and applying pressure. If the casing can withstand the pressure for a specific period without leaking or showing signs of deformation, it is considered to have passed the test.
- Dimensional Inspection: This involves checking the casing’s dimensions, such as diameter, thickness, and length, to ensure they meet the specified requirements.
- Hardness Testing: This is to ensure the casing has the required hardness and strength to withstand the rigors of drilling and operation.
- Destructive Testing: In some cases, a sample of the casing material may be taken and subjected to conditions that mimic those it will face in operation until it fails. This can provide valuable information about the casing’s performance and potential failure modes.
After inspection and testing, casings that pass are approved for use, while those that fail are either repaired, if possible, or discarded. Regular testing and inspection are crucial to maintain the integrity of oil casings and ensure safe and efficient operations in the oil and gas industry.