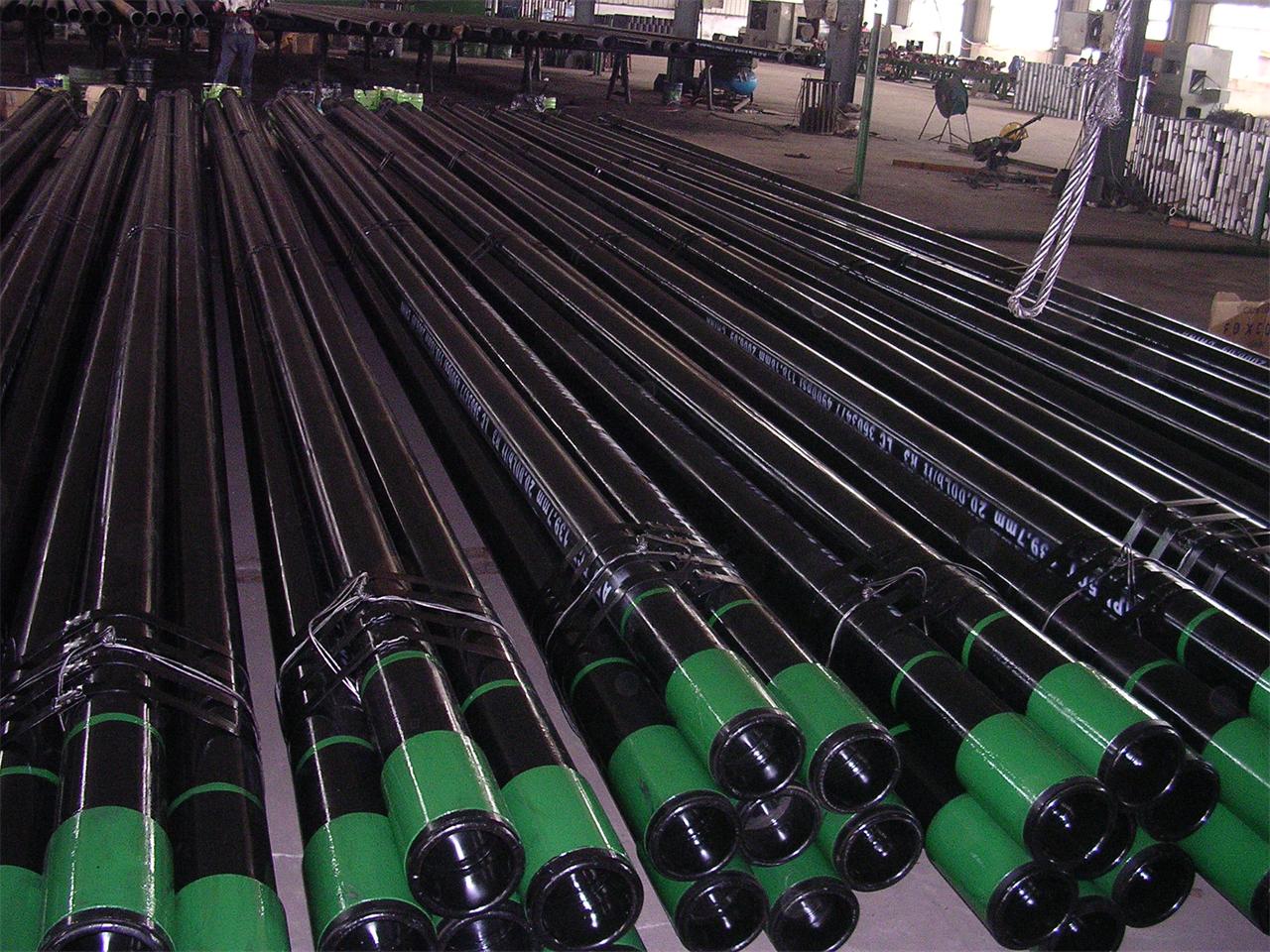
oil casing pipes heat treatment process,How are the oil casings inspected and tested to ensure their quality?
September 4, 2023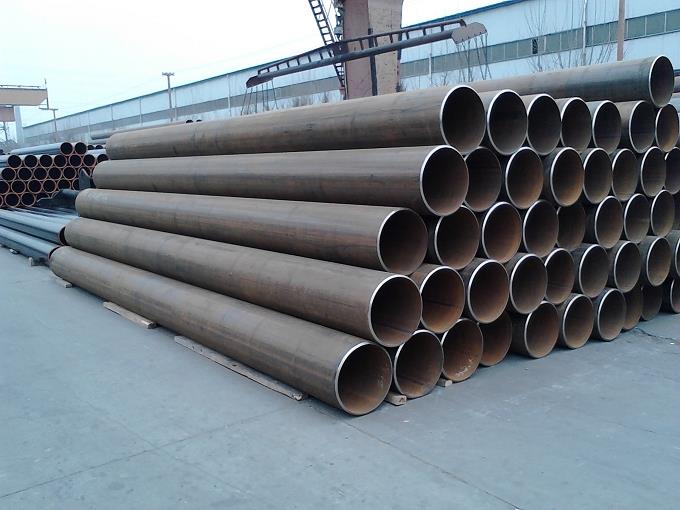
What’s The Differences Between ERW and HFW Steel Pipe
September 10, 2023Fusion Bonded Epoxy (FBE) coating and Epoxy coating refer to different types of protective coatings used on pipelines to prevent corrosion and other environmental damage. Both coatings provide a barrier between the metal pipe and the environment, but they have some differences in their composition, application, and performance.
Fusion Bonded Epoxy (FBE) Coating
Fusion Bonded Epoxy (FBE) is a powder coating that is applied as a dry powder and then melted and fused to the pipe surface with heat. This process results in a hard, continuous layer that adheres strongly to the pipe and provides excellent corrosion resistance.
Composition
FBE coating is made of solid epoxy resin, curing agents, and various additives. The resin and curing agent react during the heat application to form cross-linked polymers, which give the coating its strength and resistance properties.
Application
The FBE coating process starts with surface preparation, which typically involves cleaning and sandblasting the pipe surface to remove rust, scale, and other contaminants. The FBE powder is then applied to the heated pipe surface, where it melts and fuses to the pipe. This typically requires temperatures of around 200-250°C.
Performance
FBE coatings are known for their excellent adhesion to the steel surface, good chemical resistance, and excellent anti-corrosion properties. They also provide electrical insulation, which can help prevent cathodic disbondment, a common problem with metal pipelines. However, they can be susceptible to damage from handling and installation, and may require an additional protective layer, such as an abrasion-resistant overcoat (ARO), in some situations.
Epoxy Coating
Epoxy coating refers to a wide range of coatings made from epoxy resins. These can be applied as liquids or powders, and can be either single or multi-component systems. Epoxy coatings can be used for many applications, including pipeline coating.
Composition
Epoxy coatings are made from epoxy resins, which are a type of thermosetting polymer. They also include a curing agent or hardener, which reacts with the resin to form a hard, durable coating. The exact composition of an epoxy coating can vary widely depending on the specific product and application.
Application
Like FBE, epoxy coating application begins with surface preparation. The epoxy is then applied to the pipe surface as a liquid or powder, and cured to form a solid coating. The curing process can be done at room temperature or with heat, depending on the specific product.
Performance
Epoxy coatings are known for their excellent adhesion, good chemical resistance, and good anti-corrosion properties. They also have high electrical resistance, which can help prevent electrochemical reactions that can lead to corrosion. However, the performance of an epoxy coating can vary widely depending on the specific product and application.
Comparison and Conclusion
Both FBE coating and epoxy coating provide good protection against corrosion and have similar properties in terms of adhesion and chemical resistance. The main difference between them lies in their application process and performance characteristics.
FBE coating is applied as a powder and requires heat to melt and fuse the coating to the pipe surface, resulting in a strong, continuous layer. It is known for its excellent corrosion resistance and electrical insulation properties, but can be susceptible to handling and installation damage.
Epoxy coating, on the other hand, can be applied as a liquid or powder and can be either single or multi-component systems. It also provides good corrosion resistance and has high electrical resistance. However, the performance of an epoxy coating can vary widely depending on the specific product and application.
In the end, the choice between FBE and epoxy coating will depend on the specific requirements of the project, including environmental conditions, service life expectations, and budget considerations.
Coating: PU coating, fiber glass coating, coal tar epoxy coating, painting coating, FBE coating, 3PP coating, 3PE coating
Usage: It is widely used in fluid pipe,drill pipe,gas pipe,hydraulic pipe,etc
The anti corrosion coating can be used for ERW/LSAW/SSAW pipe,straight seam pipe,seamless steel pipe,etc.And the coated pipes are widely used in pipeline projects in the field of petroleum,chemical, natural gas,heating,sewage treatment,water,bridges,steel structures,piling and other marine water.
Standard | API 5L | ||
Grade | PSL-1 | API 5L – Gr.B/X42/X46/X52/X60/X70 etc. | |
( Material) | PSL-2 | ISO3183 – L245/L290/L320/L360/L415/L485 etc. | |
Minimum Order Quantity | 1 Ton | ||
Outside Diameter Ranges | PSL-1 | 0.405-80(in) or 10.3mm-2032mm | |
PSL-2 | 4 1/2 -80(in) or 114.3mm-2032mm | ||
Wall Thickness Ranges | SCH10~SCH160 Or STD,XS,XXS Or 1.73mm~59.54mm | ||
Length | For 20Ft Container | 4.8m-5.8m | |
(negotiable) | For 40Ft Container | 4.8m-12m | |
Most common choice | 6m, 12m | ||
Type | Welded | ERW,LSAW/SSAW | |
Seamless | Cold Drawn,Hot Finished,Hot Expanded | ||
Cap (negotiable) | Pipe size should under DN600 | ||
Pipe End | Plain end | All sizes | |
Bevel end | Pipe size above DN50, and the thickness should greater than 3.2mm | ||
Our advantages | ·Diverse products(Steel pipes, pipe fittings, other fittings) | ||
·Any third party inspection is accepted by we company. | |||
·Quick response in quotation,delivery,after-service. | |||
·Focus on pipe & tube solution for project application. |
External Coating | |
Coating type | Coating Standard |
3LPE/3LPP | DIN30670-1991,CAN/CSA Z245,21-2010,ISO21809-1-2009 SY/T 0413-2002,GB/T23257-2009 |
2LPE/2LPP | SY/T 0315-2002,GB/T23257-2009,ISO21809-1-2009 |
FBE(Fusion-bond epoxy) | SY/T 0315-2005,AWWA C213-2001,CAN/CSAZ245.20-2010,ISO218909-2-2007,API RP5L9-2001 |
Bitumen coating
Enamel &Tape hot-applied |
BS534-1990,AWWA203-2002,AWWA214-2000 |
Liquid epoxy coating | AWWWA C210-2007 |
Polyurethane insulated coating | SY/T0415-1996,CJ/T114-2000.EN253-1994 |
Internal Coating | |
Liquid Epoxy Coating | AWWAC210-2007 |
FBE | AWWAC213-2001 |
Cement Mortar Lining | BS534-1990,AWWA C205-2001 |
Bitumen Coating | BS534-1990 |
Item | Chemical Composition % | Mechanical Property | ||||||
Steel | C | Mn | S | P | Si | yield point Mpa | tensile strength Mpa | elongation % |
BS1387 | <0.2 | < 1.2 | <0.045 | <0.045 | <0.30 | >195 | 325-460 | 20 (min) |
A53 A | 0.25 | 0.95 | 0.045 | 0.05 | — | >205 | > 330 | 26–30 |
A53 B | 0.3 | 1.2 | 0.045 | 0.05 | — | >240 | > 415 | 21–26 |
A500AD | <0.26 | <1.35 | <0.035 | <0.035 | 0<0.30 | 230–250 | 310-400 | 22–26 |
A500 B C | < 0.26 | < 1.35 | <0.035 | <0.035 | 0<030 | 315–345 | 400–425 | 21–22 |
S235 | <0.20 | < 1.4 | <0.040 | <0.040 | <0.3 | >235 | > 425 | 21–22 |
S355 | < 0.22 | < 1.6 | <0.030 | <0.030 | < .55 | >355 | 470-630 | 21-22 |
C250 | < 0.3 | < 1.2 | <0.045 | <0.040 | <0.3 | 250 | 320 | 25 |
C350 | < 0.22 | < 1.6 | <0.035 | <0.035 | <0.55 | 350 | 430 | 22 |