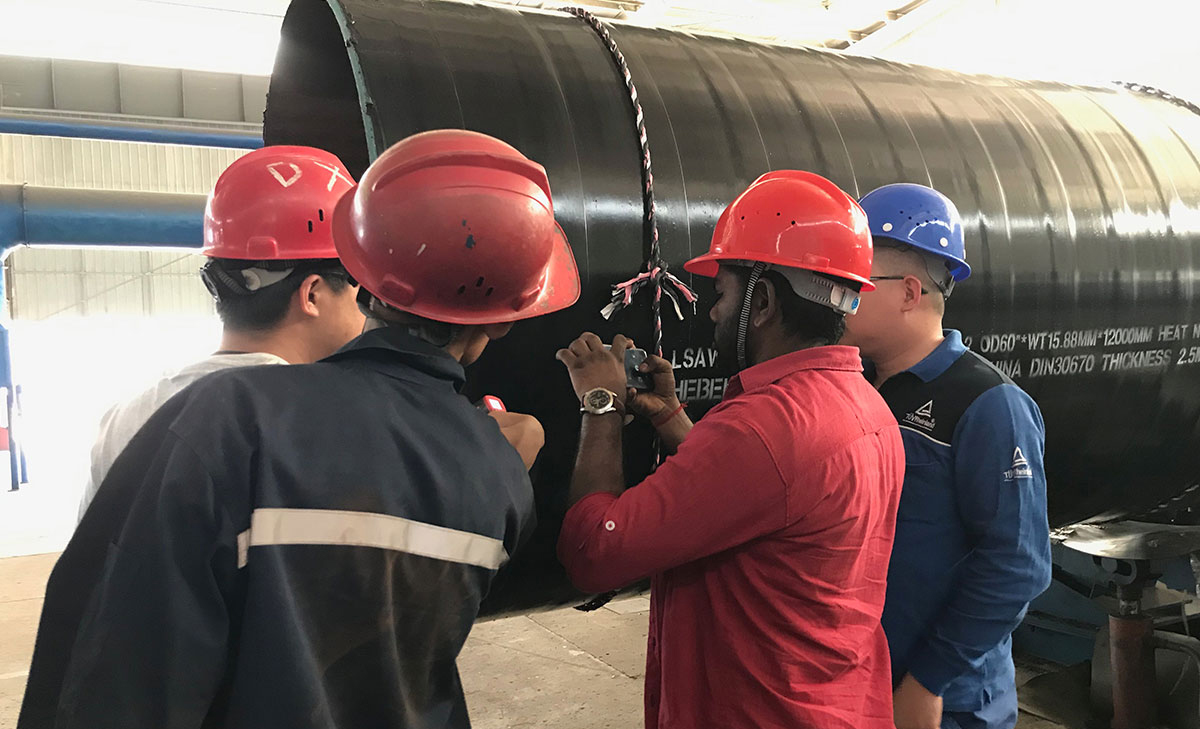
What is the difference between FBE coating pipe and epoxy coating pipe ?
September 7, 2023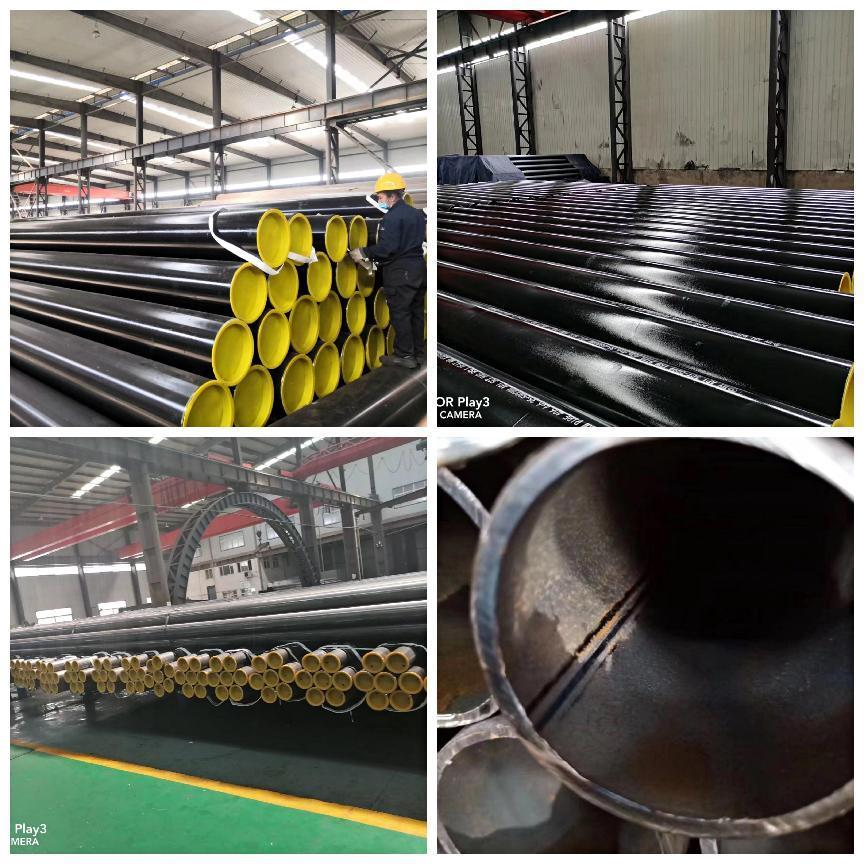
API 5L X52 and A106: Exploring the Differences – The Comparative Analysis
September 12, 2023The Differences Between ERW and HFW Steel Pipe
Understanding the differences between ERW (Electric Resistance Welded) and HFW (High Frequency Welding) steel pipes is essential for those in the industry. They are both used in the manufacturing of steel pipes, but their methodologies, applications, and quality of resultant products differ significantly.
Introduction to ERW and HFW
ERW and HFW are two popular welding methods used in the production of steel pipes. ERW stands for Electric Resistance Welding, a process that uses electric currents to heat the edges of the steel strip, creating a weld seam. On the other hand, HFW stands for High Frequency Welding, a type of ERW that uses high-frequency electric currents to heat the surfaces of the steel strip.
ERW: Electric Resistance Welding
ERW steel pipe is manufactured through low-frequency or high-frequency resistance welding. In this process, the weld is not filled with additional filler material. The weld seam is achieved by the heat generated by the resistance to electric current.
ERW pipes are typically used in transportation of oil, natural gas, and other vapor-liquid objects. They are also used in piling projects and in the chemical industry.
Advantages of ERW
ERW steel pipes have certain advantages, such as:
- Economical: ERW pipes are less expensive to produce as compared to other types of steel pipes.
- Efficiency: ERW process is very efficient as it avoids the need for filler materials.
- Flexibility: ERW pipes can be manufactured to meet different diameters and wall thicknesses.
Disadvantages of ERW
Despite its advantages, ERW steel pipes do have some disadvantages, including:
- Quality: ERW pipes can suffer from poor weld quality, especially in low-frequency ERW. This can lead to a weaker pipe structure.
- Anomalies: ERW pipes are prone to defects such as hook cracks and gray spots, which can compromise the integrity of the weld.
HFW: High Frequency Welding
HFW is a type of ERW process, but it uses high frequency electric current to generate the heat for welding. The high frequency used in this method allows for a more stable and uniform weld seam, reducing the likelihood of defects.
HFW pipes are often used in high-pressure applications due to their superior strength and toughness. They are commonly used in the oil and gas industry, particularly in offshore pipelines, as well as in the construction industry.
Advantages of HFW
HFW steel pipes bring several advantages, such as:
- Quality: HFW pipes generally have better weld quality due to the high-frequency welding process. This results in stronger and more durable pipes.
- Efficiency: Like ERW, HFW is also a very efficient process, and it eliminates the need for filler materials.
- Versatility: HFW pipes can be used in both high-pressure and low-pressure applications, making them very versatile.
Disadvantages of HFW
Despite the advantages, HFW steel pipes also have their drawbacks, including:
- Cost: HFW pipes are more expensive to produce due to the higher frequency of electric current required.
- Limitations: HFW cannot be used for all materials and thicknesses, limiting its scope.
Key Differences Between ERW and HFW
Despite HFW being a subtype of ERW, significant differences exist between the two:
- Frequency of current: ERW can use either low-frequency or high-frequency electric current, while HFW strictly uses high-frequency current.
- Weld quality: HFW generally offers better weld quality due to the high-frequency welding process.
- Cost: ERW pipes are typically less expensive to produce than HFW pipes.
- Applications: While both ERW and HFW pipes are used in a variety of applications, HFW pipes are often preferred in high-pressure environments due to their superior strength and durability.
Conclusion
In conclusion, ERW and HFW are two distinct welding methods used in the production of steel pipes. Each method has its own set of advantages and disadvantages, and each is suited to specific applications. While ERW is cost-effective and flexible, it may suffer from lower weld quality. HFW, on the other hand, provides superior weld quality and strength but at a higher cost. Understanding these differences can help industry professionals make informed decisions about the right type of pipe for their specific needs.
API 5L / ASTM A106 / A53 Grad B carbon Seamless steel pipe
We can supply API 5L / ASTM A106 / A53 Grad B carbon Seamless steel pipe. Detailed information on seamless steel pipe, pls see below date sheet.
Carbon steel tubes are made of ingot or solid round steel by perforation, and then hot rolled, cold rolled or cold drawn.Hot rolled carbon steel pipe is divided into general steel pipe, low and medium pressure boiler steel pipe, high pressure boiler steel pipe, alloy steel pipe, stainless steel pipe, petroleum cracking pipe, geological steel pipe and other steel pipe.
Standard
|
API, ASTM, BS, DIN, GB, JIS
|
|||
Outside Diameter
|
21.3-1420mm
|
|||
Wall Thickness
|
2.11-300mm
|
|||
Dia Tolerance
|
Control with in the standard, OD:+-1%, WT:+-10%
|
|||
Materials |
10#,20#,45#,Q235,Q345,Q195,Q215,Q345C,Q345A
|
|||
ASTM A53A/A53B/ A178C/A106B API5L
|
||||
ST37,ST37-2,DIN 1629 ST35, ST45,DIN 17175 ST35.8,DIN 17175 19Mn5
|
||||
16Mn,Q345B,T1,T2,T5,T9,T11,T12,T22,T91,T92,P1,P2,P5,P9,P11,P12,P22,P91,P92,15CrMO,Cr5Mo,10CrMo910,12CrMo,13CrMo44,30CrMo,A333
GR.1,GR.3,GR.6,GR.7 |
||||
Gr.B,X42,X46,X52,X60,X65,X70,X80,X100
|
||||
Inspection
|
ISO,BV,SGS,MTC
|
|||
Packing
|
Steel strip packed. Standard Export Seaworthy Package.Suit forall kinds of transport,or as required
|
|||
Application |
Widely used in Structure, Accessorize,Construction,
Fluid transportation,machinery parts,the stress parts of the automobile tractor parts and so on |
|||
MOQ
|
1 ton,sample order accepted
|
|||
Shipment time
|
Within 7-10 workdays after receiving deposit or L/C
|