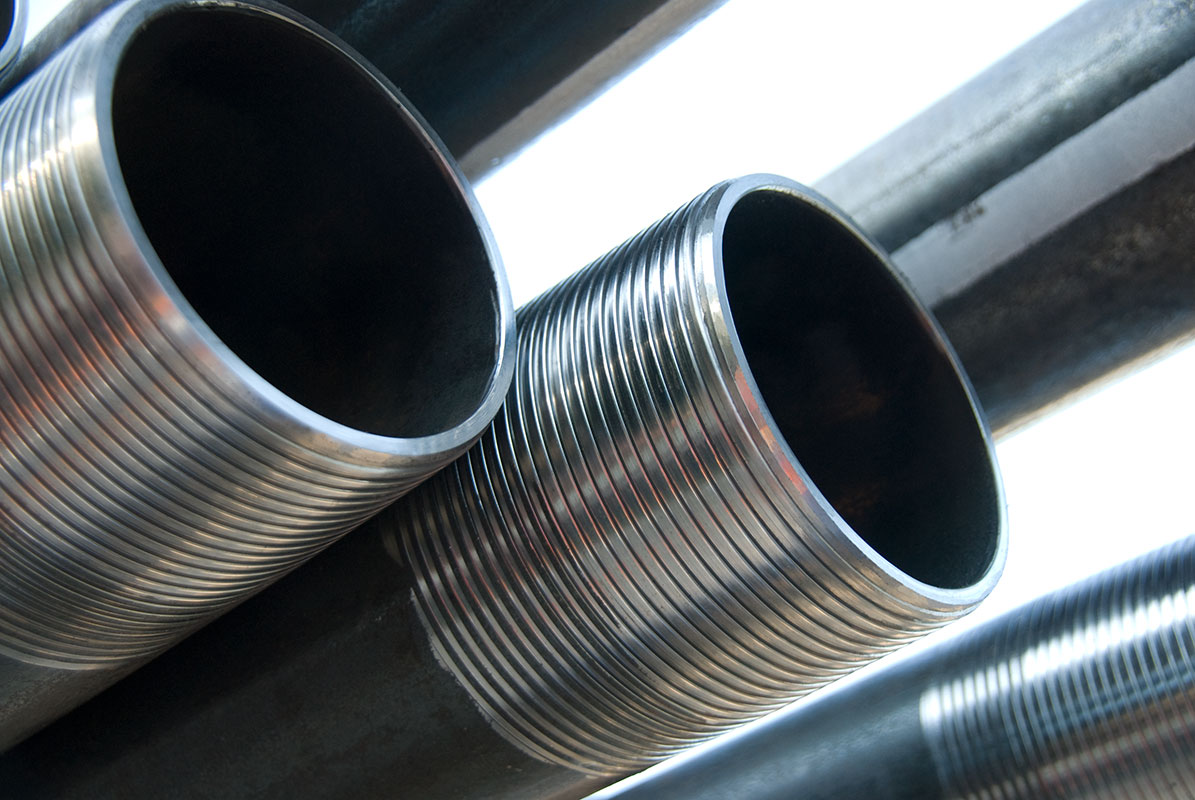
Oil Casing Pipe Market Size, Growth Potential 2024-2031
September 7, 2024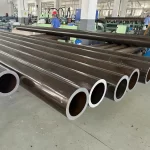
API X65 Line-Pipe Steels Effects of Granular Bainite and Polygonal Ferrite on Yield Point Phenomenon
September 13, 2024Crack Control Technology for X80 Large Diameter Line Pipes
Introduction
In the realm of pipeline engineering, the integrity and reliability of line pipes are paramount, especially when dealing with high-strength materials like X80 large diameter line pipes. These pipes are crucial for transporting oil and gas over long distances, and their performance directly impacts the safety and efficiency of the entire pipeline system. Crack control technology plays a vital role in ensuring the structural integrity of these pipes, preventing failures that could lead to catastrophic consequences. This article delves into the advanced crack control technologies employed in X80 large diameter line pipes, highlighting their importance and effectiveness in maintaining pipeline integrity.
Understanding X80 Large Diameter Line Pipes
What are X80 Line Pipes?
X80 line pipes are high-strength steel pipes used in the construction of pipelines for transporting oil and gas. The “X80” designation refers to the pipe’s minimum yield strength of 80,000 psi, making it suitable for high-pressure applications. These pipes are typically large in diameter, allowing for the efficient transport of large volumes of hydrocarbons.
Key Properties of X80 Line Pipes
- High Strength: The high yield strength of X80 pipes allows them to withstand high internal pressures, making them ideal for long-distance transportation of oil and gas.
- Toughness: X80 pipes exhibit excellent toughness, which is crucial for resisting crack propagation and ensuring pipeline integrity.
- Weldability: Despite their high strength, X80 pipes maintain good weldability, allowing for efficient construction and installation.
The Importance of Crack Control
Why is Crack Control Essential?
Crack control is essential for maintaining the structural integrity of pipelines, preventing failures that could lead to leaks, environmental damage, and safety hazards. Cracks can occur due to various factors, including mechanical stress, corrosion, and manufacturing defects. Effective crack control technologies are necessary to detect, monitor, and mitigate these issues.
Types of Cracks in Line Pipes
- Fatigue Cracks: Caused by cyclic loading and stress fluctuations over time, leading to progressive crack growth.
- Stress Corrosion Cracks: Result from the combined effects of tensile stress and a corrosive environment, leading to crack initiation and propagation.
- Hydrogen-Induced Cracks: Occur due to the absorption of hydrogen into the steel, causing embrittlement and cracking.
Advanced Crack Control Technologies
Non-Destructive Testing (NDT)
Non-destructive testing methods are employed to detect and evaluate cracks without causing damage to the pipe. Common NDT techniques include:
- Ultrasonic Testing (UT): Uses high-frequency sound waves to detect internal flaws and measure the thickness of the pipe wall.
- Magnetic Particle Inspection (MPI): Detects surface and near-surface cracks by applying magnetic particles to the pipe’s surface.
- Radiographic Testing (RT): Uses X-rays or gamma rays to create images of the pipe’s interior, revealing any defects or cracks.
Crack Arrestor Technology
Crack arrestors are devices or features integrated into the pipeline design to prevent the propagation of cracks. They work by absorbing the energy of a propagating crack, effectively stopping its progression. Types of crack arrestors include:
- Steel Sleeve Arrestors: Installed around the pipe at intervals, providing additional reinforcement to stop crack propagation.
- Composite Wraps: Made from high-strength materials, these wraps are applied to the pipe’s exterior to enhance its resistance to cracking.
Material Innovations
Advancements in material science have led to the development of high-strength, crack-resistant steels for X80 line pipes. These materials are engineered to exhibit superior toughness and resistance to crack initiation and propagation. Key innovations include:
- Microalloying: The addition of small amounts of alloying elements, such as niobium and vanadium, to enhance the steel’s strength and toughness.
- Thermo-Mechanical Controlled Processing (TMCP): A manufacturing process that optimizes the steel’s microstructure, improving its mechanical properties and crack resistance.
Benefits of Crack Control Technology
Enhanced Pipeline Safety
By effectively detecting and mitigating cracks, crack control technology enhances the safety of pipeline operations, reducing the risk of leaks and failures.
Extended Service Life
Crack control measures help extend the service life of pipelines by preventing crack initiation and propagation, reducing maintenance and repair costs.
Regulatory Compliance
Implementing advanced crack control technologies ensures compliance with industry standards and regulations, promoting safe and reliable pipeline operations.
Conclusion
Crack control technology is a critical component of pipeline engineering, particularly for high-strength materials like X80 large diameter line pipes. By employing advanced detection, monitoring, and mitigation techniques, pipeline operators can ensure the integrity and reliability of their systems, safeguarding against potential failures and enhancing overall safety. As the demand for energy continues to grow, the importance of crack control technology in maintaining pipeline infrastructure will remain paramount.
FAQ
1. What are the main causes of cracks in X80 line pipes?
Cracks can be caused by mechanical stress, corrosion, manufacturing defects, cyclic loading, and environmental factors.
2. How does non-destructive testing help in crack control?
Non-destructive testing methods detect and evaluate cracks without damaging the pipe, allowing for early detection and intervention.
3. What is the role of crack arrestors in pipeline integrity?
Crack arrestors prevent the propagation of cracks by absorbing their energy, effectively stopping their progression and enhancing pipeline safety.
4. How do material innovations contribute to crack resistance?
Advancements in material science, such as microalloying and TMCP, enhance the steel’s strength and toughness, improving its resistance to crack initiation and propagation.
5. Why is crack control technology important for pipeline safety?
Crack control technology ensures the structural integrity of pipelines, preventing failures that could lead to leaks, environmental damage, and safety hazards.