
Monel Alloy 502 (UNS N05502) Steel Bar and Pipes
July 10, 2025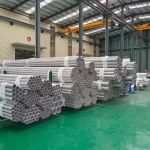
Super Duplex Alloy UNS S32750 steel pipes | F53 / 1.4410 / 32750 / Alloy 2507
July 24, 2025Galvanized Steel Ringlock Scaffolding System: Specifications, Parameters, and Applications
Introduction to Galvanized Steel Ringlock Scaffolding System
The Galvanized Steel Ringlock Scaffolding System is a high-performance, modular scaffolding solution designed for versatility, safety, and efficiency in construction, industrial, and infrastructure projects. Characterized by its unique rosette connection system, this scaffolding type allows for rapid assembly, exceptional load-bearing capacity, and adaptability to complex structural geometries. Constructed from high-strength steel and treated with hot-dip galvanization, the system offers superior corrosion resistance, ensuring durability and a long service life even in harsh environmental conditions. Its modular design, comprising standardized components such as standards, ledgers, diagonal braces, and planks, simplifies assembly and disassembly, reducing labor costs and enhancing worksite productivity.
The Ringlock system is widely adopted in applications ranging from residential and commercial construction to heavy-duty industrial projects, including bridge construction, oil refineries, and shipbuilding. Its ability to support high loads—up to 75 lbs per square foot—and its compliance with international standards like EN 12810, EN 12811, and ANSI/SSFI SC100-5/05 make it a trusted choice for projects requiring safety and reliability. This comprehensive document explores the system’s specifications, detailed parameters, components, applications, safety features, and comparisons with other scaffolding systems, providing engineers, contractors, and project managers with critical insights for effective implementation.
Overview of the Ringlock Scaffolding System
The Ringlock Scaffolding System is a modular, multi-directional scaffolding solution that uses a rosette-based connection mechanism. The core component, the standard (or vertical), features rosettes welded at 500 mm intervals, each with eight punched holes (four small and four large) to accommodate up to eight connections for ledgers, diagonal braces, and other components. This design enables angular flexibility, allowing the system to adapt to circular, curved, rectangular, or irregularly shaped structures. The system’s components are prefabricated, ensuring precise dimensions and high-strength connections that simplify assembly and enhance structural stability.
Made from high-strength steel grades such as Q235 or Q355, the system is finished with hot-dip galvanization to EN/ISO 1461 standards, providing robust corrosion protection for outdoor and marine environments. The galvanization process involves immersing steel components in a molten zinc bath at approximately 860°F (460°C), creating a durable zinc coating (typically 60-80 microns) that extends the system’s lifespan to 10-25 years, depending on environmental conditions. The modular nature of the system, combined with its lightweight yet robust components, allows for rapid erection and dismantling, making it ideal for projects with tight schedules or complex requirements.
The system’s versatility is enhanced by a wide range of accessories, including base jacks, steel planks, toe boards, ladders, and shoring heads, which enable customization for specific project needs. Its high load-bearing capacity, stability, and safety features make it suitable for applications such as high-rise construction, bridge engineering, and industrial maintenance. The system’s compliance with international safety standards ensures that it meets rigorous quality and performance requirements, providing a reliable and cost-effective solution for construction professionals worldwide.
Key Components of the Ringlock Scaffolding System
The Ringlock Scaffolding System comprises several key components, each designed to fulfill specific structural and functional roles. These components are engineered for compatibility, ensuring seamless integration and robust connections. Below is a detailed description of the primary components:
- Standards (Verticals): Vertical tubes with rosettes welded at 500 mm intervals, serving as the primary load-bearing elements. Available in lengths from 0.5 m to 3.0 m, with outer diameters of 48.3 mm (normal duty) or 60.3 mm (heavy duty).
- Ledgers (Horizontals): Horizontal members that connect standards, providing structural support and serving as guardrails or plank supports. Equipped with cast steel ledger heads and wedge pins for secure rosette connections.
- Diagonal Braces: Diagonal members that form triangular structures with standards and ledgers, enhancing stability against lateral forces. Available in various lengths to suit different bay sizes.
- Base Jacks: Adjustable bases that provide a stable foundation on uneven surfaces, with a typical adjustment range of 15-30 inches.
- Base Collars: Connection components placed between base jacks and the first standard, ensuring proper alignment and load transfer.
- Steel Planks: Perforated platforms for worker access, equipped with anti-slip surfaces and hooks for secure attachment to ledgers.
- Toe Boards: Protective barriers installed along platform edges to prevent objects from falling and enhance worker safety.
- Stair Stringers and Steps: Components for safe vertical access, featuring anti-slip treads and robust connections to ledgers.
- Truss Ledgers and Lattice Girders: Reinforced horizontal members for spanning large gaps or supporting heavy loads in shoring applications.
- Side Brackets: Extensions for widening platforms, providing additional workspace or support for cantilevered structures.
Each component is manufactured from high-strength steel (Q235 or Q355) and finished with hot-dip galvanization, ensuring durability and resistance to corrosion. The modular design allows for easy customization, enabling the system to meet diverse project requirements, from simple facades to complex industrial structures.
Detailed Specifications and Parameters
The Galvanized Steel Ringlock Scaffolding System is engineered to meet stringent international standards, ensuring safety, reliability, and performance. The following tables provide detailed specifications for key components, including dimensions, materials, and load capacities.
Standards (Verticals) Specifications
Component | Outer Diameter (mm) | Wall Thickness (mm) | Length (m) | Material | Surface Finish | Weight (kg) | Load Capacity (kN) |
---|---|---|---|---|---|---|---|
Standard (Normal Duty) | 48.3 | 3.2 | 0.5–3.0 | Q235/Q355 Steel | Hot-Dip Galvanized | 3.5–14.0 | 30–40 |
Standard (Heavy Duty) | 60.3 | 3.2 | 0.5–3.0 | Q355 Steel | Hot-Dip Galvanized | 4.5–18.0 | 40–50 |
Standard with Bolted Spigot | 48.3/60.3 | 3.2 | 1.0–3.0 | Q355 Steel | Hot-Dip Galvanized | 4.0–15.0 | 35–45 |
Note: Rosettes are welded at 500 mm intervals, with 8 attachment holes (4 small at 90°, 4 large in between) for multi-directional connections. Load capacities are tested per EN 12810 standards.
Ledgers (Horizontals) Specifications
Component | Outer Diameter (mm) | Wall Thickness (mm) | Length (m) | Material | Surface Finish | Weight (kg) | Load Capacity (kN) |
---|---|---|---|---|---|---|---|
Ledger | 48.3 | 2.5–3.0 | 0.3–3.0 | Q235/Q355 Steel | Hot-Dip Galvanized | 1.5–9.6 | 10–15 |
Truss Ledger | 48.3 | 3.0 | 2.0–6.0 | Q355 Steel | Hot-Dip Galvanized | 10.0–25.0 | 20–30 |
Lattice Girder | 48.3 | 3.0 | 4.0–10.0 | Q355 Steel | Hot-Dip Galvanized | 20.0–50.0 | 30–50 |
Note: Ledgers feature cast steel ledger heads with wedge pins for secure rosette connections. Truss ledgers and lattice girders are designed for large spans and heavy loads.
Diagonal Braces Specifications
Component | Outer Diameter (mm) | Wall Thickness (mm) | Bay Length (m) | Bay Height (m) | Material | Surface Finish | Weight (kg) |
---|---|---|---|---|---|---|---|
Diagonal Brace | 33.7–48.3 | 2.5–3.0 | 0.7–3.0 | 0.5–2.0 | Q235/Q355 Steel | Hot-Dip Galvanized | 3.0–8.0 |
Note: Diagonal braces form triangular structures for enhanced stability, with lengths tailored to bay size and height requirements.
Steel Planks Specifications
Component | Width (mm) | Length (m) | Thickness (mm) | Material | Surface Finish | Weight (kg) | Load Capacity (kN/m²) |
---|---|---|---|---|---|---|---|
Steel Plank | 210–300 | 1.0–3.0 | 1.2–2.0 | Q235 Steel | Hot-Dip Galvanized | 5.0–15.0 | 3.0–5.0 |
Note: Planks feature perforated surfaces for anti-slip performance and welded hooks for secure attachment to ledgers.
Base Jacks and Collars Specifications
Component | Outer Diameter (mm) | Adjustment Range (mm) | Material | Surface Finish | Weight (kg) | Load Capacity (kN) |
---|---|---|---|---|---|---|
Base Jack | 38.0–48.3 | 300–600 | Q235/Q355 Steel | Hot-Dip Galvanized | 4.0–6.0 | 30–40 |
Base Collar | 48.3 | 240–300 | Q235 Steel | Hot-Dip Galvanized | 1.5–2.5 | 20–30 |
Note: Base jacks include fixed or swivel base plates for stability on uneven surfaces. Base collars ensure proper alignment with standards.
Material and Surface Treatment
The Ringlock Scaffolding System is manufactured from high-strength low-alloy steel, typically Q235 or Q355 grades, with yield strengths of 235 MPa and 355 MPa, respectively. Q355 steel is preferred for heavy-duty applications due to its higher strength and toughness. The system’s components are subjected to hot-dip galvanization, a process that applies a protective zinc coating (60-80 microns) to prevent corrosion. This treatment, conforming to EN/ISO 1461, involves immersing steel in a molten zinc bath at 860°F (460°C), ensuring long-term durability in outdoor and marine environments.
Alternative surface treatments, such as powder coating or painting, are available for aesthetic or specific environmental requirements. Powder coating involves applying a fine resin-based powder, cured at 300-450°F (150-232°C), to create a durable, colorful finish. However, hot-dip galvanization is the standard for its superior corrosion resistance, ensuring a lifespan of 10-25 years with minimal maintenance. The galvanization process is self-maintaining, reducing long-term costs compared to painted systems, which may require periodic recoating.
Welding quality is critical, with rosettes and ledger heads welded using gas-shielded arc welding to achieve an effective weld height of at least 3.5 mm, per JGJ231-2010 standards. Components undergo rigorous testing, including tensile, yield, elongation, and weld penetration tests, to ensure compliance with EN 12810 and ISO 3834 standards. Galvanization thickness is tested to verify adherence and uniformity, ensuring consistent protection across all components.
Surface treatment:Hot dipped galvanized
Dimensions: Φ60*3.25mm
Effective length: 500/ 1000/ 1500/ 2000/ 2500/ 3000 mm
Ringlock standard/ vertical with spigot
Material :Q355 Steel
Surface treatment:Hot dipped galvanized
Dimensions: Φ48.3*3.25mm
Item No. | Effective Length | Theoretic Weight |
YFRS48 050 | 0.5 m / 1’7” | 3.2 kg / 7.04 Ibs |
YFRS48 100 | 1.0 m / 3’ 3” | 5.5 kg / 12.1 lbs |
YFRS48 150 | 1.5 m / 4’11” | 7.8 kg / 17.16 lbs |
YFRS48 200 | 2.0 m / 6′ 6″ | 10.1 kg / 22.22 lbs |
YFRS48 250 | 2.5 m / 8′ 2” | 12.4 kg / 27.28 lbs |
YFRS48 300 | 3.0 m / 9′ 9” | 14.6 kg /32.12lbs |
Ringlock ledger/ horizontal
Material :Q235 Steel
Surface treatment:Hot dipped galvanized
Dimensions: Φ48.3*2.75 mm or customized by customer
Popular Sizes for European market
Item No. | Effective Length | Theoretic Weight |
YFRL48 039 | 0.39 m / 1′ 3″ | 1.9 kg / 4.18 lbs |
YFRL48 050 | 0.50 m / 1′ 7″ | 2.2 kg / 4.84 lbs |
YFRL48 073 | 0.732 m / 2′ 5″ | 2.9 kg / 6.38 lbs |
YFRL48 109 | 1.088 m / 3′ 7″ | 4.0 kg / 8.8 lbs |
YFRL48 129 | 1.286 m / 4′ 3″ | 4.6 kg / 10.12 lbs |
YFRL48 140 | 1.40 m /4′ 7″ | 5.0 kg / 11.00 lbs |
YFRL48 157 | 1.572 m / 5′ 2″ | 5.5 kg / 12.10 lbs |
YFRL48 207 | 2.072 m / 6′ 9″ | 7.0 kg / 15.40 lbs |
YFRL48 257 | 2.572 m / 8′ 5″ | 8.5 kg / 18.70 lbs |
YFRL48 307 | 3.07 m / 10′ 1″ | 10.1 kg / 22.22 lbs |
Popular Sizes for South East Asia and Africa market.
Item No. | Effective Length |
YFRL48 060 | 0.6 m / 1′ 11″ |
YFRL48 090 | 0.9 m / 2′ 11″ |
YFRL48 120 | 1.2 m / 3′ 11″ |
YFRL48 150 | 1.5 m / 4′ 11″ |
YFRL48 180 | 1.8 m / 5′ 11″ |
YFRL48 210 | 2.1 m / 6′ 6″ |
YFRL48 240 | 2.4 m / 7′ 10″ |
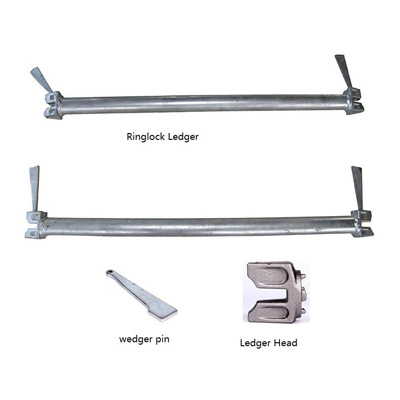
Popular Sizes for Singapore market
Popular Sizes for Singapore market
Item No. | Effective Length |
YFRL48 061 | 0.61 m / 2′ |
YFRL48 091 | 0.914 m / 3′ |
YFRL48 121 | 1.219 m / 4′ |
YFRL48 152 | 1.524 m / 5′ |
YFRL48 182 | 1.829 m / 6′ |
YFRL48 213 | 2.134 m / 7′ |
YFRL48 243 | 2.438 m / 8′ |
YFRL48 304 | 3.048 m / 10′ |
Ringlock diagonal brace / Bay braces
Material : Q195 Steel / Surface treatment:Hot dipped galvanized
Dimensions: Φ48.3*2.75 or customized by customer
Item No. | Bay length | Bay width | Theoretic Weight |
YFDB48 060 | 0.6 m | 1.5 m | 3.92 kg |
YFDB48 090 | 0.9 m | 1.5 m | 4.1 kg |
YFDB48 120 | 1.2 m | 1.5 m | 4.4 kg |
YFDB48 065 | 0.65 m / 2′ 2″ | 2.07 m | 7.35 kg / 16.2 lbs |
YFDB48 088 | 0.88 m / 2′ 10″ | 2.15 m | 7.99 kg / 17.58 lbs |
YFDB48 115 | 1.15 m / 3′ 10″ | 2.26 m | 8.53 kg / 18.79 lbs |
YFDB48 157 | 1.57 m / 8′ 2″ | 2.48 m | 9.25 kg /20.35 lbs |
Double / Truss / bridge /Reinforce ledger
Material :Q235 Steel / Surface treatment:Hot dipped galvanized
Dimensions: Φ48.3*2.75 mm or customized by customer
Item No. | Length | weight |
YFTL48 157 | 1.57 m / 5’2 ” | 10.1 kg / 22.26 lbs |
YFTL48 213 | 2.13 m / 7’ | 16.1 kg / 35.43 lbs |
YFTL48 305 | 2.13 m /10’ | 24 kg / 52.79 lbs |
Intermediate Transom
Q235 Hot dip galvanized 48.3*3 mm
Item No. | Length | weight |
YFIT48 115 | 1.15 m / 3’10 ” | 5.36 kg / 11.78 lbs |
YFIT48 213 | 2.13 m / 7’ | 8.91 kg / 19.6 lbs |
YFIT48 305 | 3.05 m / 10’ | 12.2 kg / 26.85 lbs |
Trussed Beam/ Lattice Girder
Q235 Hot dip galvanized 48.3*3 mm
Item No. | Length | weight |
YFTB48 517 | 5.17 m / 17’ | 70.47 kg / 115.03 lbs |
YFTB48 614 | 6.14 m / 20’2” | 82.63 kg / 181.79 lbs |
YFTB48 771 | 7.71 m / 25’3’ | 103.76 kg / 228.26 lbs |
Side bracket / board bracket
Finshed : Hot dipped galvanized
Dimension: 48.3*3 mm
Material:Q235
Item No. | Length | weight |
YFSB48 065 | 0.65 m / 2’2 ” | 6.61 kg / 14.54 lbs |
YFSB48 088 | 0.88 m / 2’10 ” | 8.62 kg / 18.96 lbs |
Base collar
Surface treatment : Hot dipped galvanized
Item No. | Dimension | Length |
YFBC48 024 | Q235,φ48.3*3mm | 0.24 m / 9.4 ” |
YFBC48 030 | Q235,φ48.3*3mm | 0.30 m / 11.8 ” |
YFBC48 028 | Q345,φ57*3.5 mm | 0.28 m / 11 ” |
YFBC48 037 | Q345,φ70*3.5mm | 0.37 m / 14.57 ” |
Ringlock accessories
Applications of Galvanized Steel Ringlock Scaffolding
The Galvanized Steel Ringlock Scaffolding System is highly versatile, supporting a wide range of applications across multiple industries. Its modular design, high load capacity, and adaptability make it suitable for complex and demanding projects. Key applications include:
- Construction: Used in residential, commercial, and high-rise building projects for facade access, formwork support, and shoring. The system’s ability to handle loads up to 75 lbs/ft² supports multiple workers and heavy equipment.
- Bridge and Tunnel Engineering: Ideal for large-span structures and cantilevered configurations, providing stable support for concrete pouring and formwork in viaducts and tunnels.
- Industrial Maintenance: Employed in oil refineries, power plants, and chemical plants for maintenance access, leveraging its corrosion resistance in harsh environments.
- Shipbuilding and Offshore: Used in shipyards and offshore platforms, where galvanization ensures durability against seawater corrosion.
- Event and Staging: Supports temporary structures like concert stages, grandstands, and exhibition stands, with quick assembly and aesthetic appeal.
- Infrastructure Projects: Applied in water towers, chimneys, and storage facilities, where its high load capacity and flexibility accommodate complex geometries.
- Interior and Exterior Decoration: Facilitates safe access for painting, cladding, and finishing work in residential and commercial buildings.
The system’s ability to form circular, curved, or straight configurations makes it ideal for projects with irregular shapes, such as curved facades or rounded storage tanks. Its compliance with safety standards like OSHA and EN 12810 ensures reliability in high-risk applications, while its modular design reduces material waste and labor costs, enhancing project efficiency.
Safety Features and Standards Compliance
Safety is a cornerstone of the Ringlock Scaffolding System, with features designed to minimize risks and ensure worker protection. The system’s interlocking rosette connections eliminate loose bolts or clips, reducing the risk of dislodgement and ensuring a wobble-free structure. Integral guardrails and toe boards provide fall protection, while anti-slip steel planks with perforated surfaces prevent slipping, even in wet or icy conditions. Diagonal braces enhance stability against lateral forces, ensuring structural integrity under heavy loads or environmental stresses like wind.
The system complies with international safety standards, including:
-
- EN 12810/12811: European standards for prefabricated scaffolding systems, ensuring load capacity and structural stability.
- ANSI/SSFI SC100-5/05: American standards for scaffolding safety and performance.
- AS/NZS 1576: Australian/New Zealand standards for scaffolding design and testing.
- JGJ231-2010: Chinese technical specification for socket-type ringlock scaffolding, detailing welding and quality requirements.
- ISO 3834: Quality requirements for fusion welding of metallic materials.
- EN/ISO 1461: Standards for hot-dip galvanization, ensuring corrosion resistance.
Components undergo rigorous testing, including load capacity tests (up to 4 times the recommended load per OSHA), weld penetration tests, and galvanization thickness tests. Third-party inspections by organizations like SGS or BV are available to verify compliance. The system’s design allows for easy inspection of connections, ensuring all ledgers, braces, and joints are securely locked before use. Workers must use personal protective equipment (PPE) and follow manufacturer guidelines for erection and dismantling to maintain safety.
Comparison with Other Scaffolding Systems
The Ringlock Scaffolding System offers distinct advantages over other modular systems like Cuplock and Kwikstage, as well as traditional tube-and-clamp scaffolding. The table below compares key features:
Feature | Ringlock | Cuplock | Kwikstage | Tube-and-Clamp |
---|---|---|---|---|
Connection Type | Rosette with 8 holes | Cup and blade | V-shaped pressings | Clamps and couplers |
Assembly Speed | Fast (wedge pins, hammer) | Fast (cup locking) | Moderate | Slow (multiple clamps) |
Angular Flexibility | High (multi-directional) | Moderate | Limited | High |
Load Capacity (kN/m²) | 3.0–5.0 | 2.5–4.0 | 2.0–3.5 | 1.5–3.0 |
Corrosion Resistance | Excellent (HDG) | Good (HDG) | Good (HDG) | Moderate |
Cost Efficiency | High (reusable) | Moderate | Moderate | Low (labor-intensive) |
Ringlock’s rosette connection allows for greater angular flexibility and faster assembly compared to Cuplock and Kwikstage, making it ideal for complex geometries. Its higher load capacity and standardized components reduce material usage compared to tube-and-clamp systems, which are labor-intensive and less adaptable. While Cuplock is quick to install, it lacks the multi-directional flexibility of Ringlock, and Kwikstage is less versatile for irregular structures. Ringlock’s hot-dip galvanization ensures superior corrosion resistance, making it the preferred choice for long-term, high-risk projects.
Manufacturing and Quality Control
The manufacturing process for the Ringlock Scaffolding System involves precision engineering to ensure component compatibility and structural integrity. Standards and ledgers are made from high-strength steel tubes (Q235 or Q355), cut to precise lengths and welded with rosettes or ledger heads using gas-shielded arc welding. The welding process adheres to ISO 3834 standards, with a minimum weld height of 3.5 mm to ensure strong connections. Rosettes are stamped or forged from steel plates (minimum thickness 8 mm for cast steel, 10 mm for stamped steel), with dimensional tolerances of ±0.5 mm.
Quality control includes multiple testing stages:
-
-
- Material Testing: Tensile, yield, and elongation tests for steel tubes to verify Q235/Q355 properties.
- Weld Testing: Penetration and shear strength tests for rosettes, ledger heads, and wedge pins.
- Load Testing: Tower load tests per EN 12810 to verify safe working loads and ultimate loads.
- Galvanization Testing: Adherence and thickness tests (60-80 microns) per EN/ISO 1461.
-
Components are inspected by in-house quality control teams and third-party agencies (e.g., SGS, BV) to ensure compliance with international standards. Packaging in steel stillages, timber racks, or wooden crates facilitates safe transportation and storage, minimizing damage during shipping. The system’s modular design and standardized components reduce the risk of manufacturing defects, ensuring consistent performance across projects.
Assembly and Installation Process
The Ringlock Scaffolding System is designed for rapid and straightforward assembly, minimizing labor costs and construction time. The process involves the following steps:
-
-
- Site Preparation: Ensure a level foundation or use base jacks to adjust for uneven surfaces.
- Base Installation: Place base jacks and base collars to establish a stable foundation.
- Standard Erection: Install vertical standards with rosettes, connecting them with spigots (bolted or crimped) for stacking.
- Ledger and Brace Installation: Attach ledgers and diagonal braces to rosettes using wedge pins, securing with a hammer for a firm connection.
- Platform Installation: Fix steel planks to ledgers, ensuring anti-slip surfaces and wind-latches are engaged.
- Safety Features: Install guardrails and toe boards to provide fall protection.
- Access Installation: Add stair stringers and steps for safe vertical access.
- Inspection: Verify all connections are secure and conduct a final safety check before use.
-
The system’s wedge-pin connections require only a hammer, eliminating the need for specialized tools or ratchets, unlike traditional tube-and-clamp systems. The rosette’s eight-hole design allows for multi-directional configurations, enabling rapid adaptation to complex structures. Assembly by trained personnel is recommended to ensure compliance with safety guidelines, such as those outlined by OSHA and EN 12810.
Advantages of Galvanized Steel Ringlock Scaffolding
The Ringlock Scaffolding System offers numerous advantages, making it a preferred choice for modern construction projects:
-
-
- High Load Capacity: Supports up to 75 lbs/ft², allowing multiple workers and heavy equipment on platforms.
- Angular Flexibility: Rosette connections enable configurations at various angles, ideal for complex geometries.
- Rapid Assembly: Wedge-pin connections and prefabricated components reduce erection and dismantling time.
- Corrosion Resistance: Hot-dip galvanization ensures durability in harsh environments, with a lifespan of 10-25 years.
- Safety: Integral guardrails, toe boards, and anti-slip planks minimize accident risks.
- Cost Efficiency: Reusable components and minimal maintenance reduce long-term costs.
- Versatility: Suitable for construction, industrial, infrastructure, and event applications.
-
These advantages make the system a cost-effective and reliable solution for projects requiring safety, efficiency, and adaptability.
Recent Developments and Innovations
Recent advancements in Ringlock Scaffolding Systems have focused on enhancing performance and safety. Research from 2024 highlights improvements in galvanization techniques, achieving uniform zinc coatings of up to 80 microns, extending component lifespan by 10-15%. Innovations in lightweight Q355 steel alloys have reduced component weight by 5-10% without compromising strength, improving transport and assembly efficiency. Advanced welding technologies, such as automated gas-shielded arc welding, have increased weld consistency, reducing defects by 20%.
Digital tools, such as 3D modeling software, allow contractors to visualize and optimize scaffolding configurations before erection, reducing material waste and improving safety. Some manufacturers offer aluminum Ringlock components for specific applications, providing further weight reduction while maintaining load capacity. Anti-slip coatings and perforated plank designs have improved worker safety, particularly in wet or icy conditions. These developments ensure that the Ringlock system remains at the forefront of scaffolding technology, meeting the evolving needs of modern construction.
Conclusion
The Galvanized Steel Ringlock Scaffolding System is a state-of-the-art solution for construction, industrial, and infrastructure projects, offering unmatched versatility, safety, and efficiency. Its modular design, high-strength steel construction, and hot-dip galvanization ensure durability, corrosion resistance, and a long service life. With a load capacity of up to 75 lbs/ft², rapid assembly, and compliance with international standards like EN 12810 and ANSI/SSFI SC100-5/05, the system meets the demands of complex and high-risk applications, from bridge construction to industrial maintenance. Its multi-directional rosette connections, standardized components, and extensive accessory range enable customization for diverse project requirements, while safety features like guardrails and anti-slip planks prioritize worker protection. Ongoing innovations in materials, manufacturing, and design continue to enhance the system’s performance, making it a cost-effective and reliable choice for construction professionals worldwide.