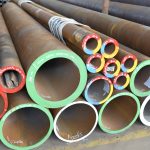
X10 CrMoV nb9-1 Alloy Steel High-Temperature Pipe
March 15, 2024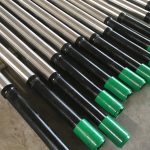
SS304L Oil Well Screen Sand Control Pipes
March 25, 2024Understanding the Differences Between Steel Pipe Varnish Coating, Zinc Coating, and Epoxy Coating
Introduction
Steel pipes are widely used in various industries for their durability, strength, and versatility. To enhance their performance and protect them from corrosion, different types of coatings are applied to steel pipes. Three common types of coatings used are varnish coating, zinc coating, and epoxy coating. In this article, we will explore the differences between these coatings, their properties, applications, and benefits. Understanding these differences will help professionals make informed decisions when choosing the appropriate coating for their steel pipes.
Varnish Coating
Composition and Properties
Varnish coating, also known as paint coating, is a protective layer applied to steel pipes. It is typically composed of a mixture of resins, solvents, pigments, and additives. Varnish coatings provide a thin layer of protection against corrosion, moisture, and UV radiation.
The properties of varnish coatings vary depending on the specific formulation. However, some common properties include:
- Corrosion Resistance: Varnish coatings provide a barrier between the steel surface and the surrounding environment, protecting the steel from corrosion caused by moisture, chemicals, and atmospheric conditions.
- Aesthetic Appeal: Varnish coatings can be formulated in various colors, providing an aesthetically pleasing appearance to steel pipes. This makes them suitable for applications where visual appeal is important.
- Ease of Application: Varnish coatings are relatively easy to apply using techniques such as brushing, spraying, or dipping. They dry quickly, allowing for efficient coating processes.
Applications
Varnish coatings are commonly used in the following applications:
- Indoor Applications: Varnish coatings are suitable for steel pipes used in indoor environments where the risk of exposure to harsh weather conditions is minimal. They are often used in architectural structures, furniture, and decorative applications.
- Mild Environments: Varnish coatings are effective in mild environments where the risk of corrosion is relatively low. They provide a protective layer against moisture and minor chemical exposure.
- Aesthetic Requirements: Varnish coatings are chosen when the appearance of the steel pipes is a significant factor. They can be customized to match specific color requirements and provide a glossy or matte finish.
Zinc Coating
Composition and Properties
Zinc coating, also known as galvanizing, involves applying a layer of zinc to the surface of steel pipes through a process called hot-dip galvanizing. The zinc coating forms a metallurgical bond with the steel, providing excellent corrosion protection.
The properties of zinc coatings include:
- Corrosion Resistance: Zinc coatings act as a sacrificial layer, corroding preferentially to protect the underlying steel. This provides long-lasting corrosion resistance, even in harsh environments.
- Self-Healing: If the zinc coating is damaged, it has the ability to self-heal through a process called cathodic protection. The zinc sacrifices itself to protect the exposed steel, preventing further corrosion.
- Ductility: Zinc coatings are relatively ductile, allowing for some flexibility in the steel pipes. This property is beneficial in applications where the pipes may be subjected to bending or deformation.
Applications
Zinc coatings are widely used in various applications, including:
- Outdoor Environments: Zinc coatings are highly effective in outdoor environments where steel pipes are exposed to moisture, saltwater, and atmospheric conditions. They are commonly used in construction, infrastructure, and marine applications.
- Underground Applications: Zinc coatings provide excellent corrosion protection for steel pipes buried underground, where they may be exposed to soil moisture and corrosive substances.
- Industrial Settings: Zinc coatings are suitable for steel pipes used in industrial settings, where they may come into contact with chemicals, gases, or abrasive materials. They offer robust corrosion resistance in such environments.
Epoxy Coating
Composition and Properties
Epoxy coating is a type of protective coating that consists of epoxy resins and a curing agent. It forms a strong, durable, and chemically resistant layer on the surface of steel pipes. Epoxy coatings can be applied through various methods, including powder coating and liquid coating.
The properties of epoxy coatings include:
- Corrosion Protection: Epoxy coatings provide exceptional corrosion protection, even in highly corrosive environments. They act as a barrier against moisture, chemicals, and abrasion, extending the lifespan of the steel pipes.
- Chemical Resistance: Epoxy coatings exhibit high resistance to a wide range of chemicals, making them suitable for applications where the pipes come into contact with corrosive substances.
- Adhesion Strength: Epoxy coatings have excellent adhesion to the steel surface, ensuring long-term protection and preventing delamination or peeling.
Applications
Epoxy coatings are commonly used in the following applications:
- Oil and Gas Industry: Epoxy coatings arefrequently used in the oil and gas industry for steel pipes that transport oil, gas, and other corrosive fluids. The high chemical resistance of epoxy coatings makes them ideal for these applications.
- Water and Wastewater Treatment: Steel pipes used in water and wastewater treatment facilities are often coated with epoxy to protect against corrosion caused by the chemicals and moisture present in these environments.
- Industrial Applications: Epoxy coatings are widely used in industrial settings where steel pipes are exposed to harsh chemicals, acids, and solvents. They provide reliable corrosion protection and ensure the longevity of the pipes.
FAQ
1. Which coating provides the best corrosion resistance?
Zinc coating, also known as galvanizing, provides the best corrosion resistance among the three coatings discussed. It acts as a sacrificial layer, protecting the underlying steel from corrosion even in harsh environments.
2. Can varnish coatings be used in outdoor applications?
Varnish coatings are not recommended for outdoor applications where steel pipes are exposed to harsh weather conditions. They are more suitable for indoor applications or mild environments with minimal exposure to moisture and chemicals.
3. Are epoxy coatings suitable for high-temperature applications?
Yes, epoxy coatings can withstand high temperatures and are suitable for high-temperature applications. However, it is essential to choose epoxy coatings specifically formulated for such conditions to ensure optimal performance.
4. Can zinc coatings be applied to existing steel pipes?
Yes, zinc coatings can be applied to existing steel pipes through a process called zinc spraying or zinc-rich paint. This method provides corrosion protection to the steel surface, even if it has already been exposed.
5. How long do epoxy coatings last?
The lifespan of epoxy coatings depends on various factors, including the application, environmental conditions, and maintenance. Generally, well-applied epoxy coatings can last for 10-20 years or more, providing long-term corrosion protection.
Conclusion
In conclusion, varnish coating, zinc coating, and epoxy coating are three common types of protective coatings used for steel pipes. Each coating offers unique properties and benefits, making them suitable for different applications and environments. Varnish coatings provide aesthetic appeal and moderate corrosion resistance, zinc coatings offer excellent corrosion protection in outdoor and industrial settings, and epoxy coatings provide exceptional corrosion and chemical resistance. Understanding the differences between these coatings allows professionals to make informed decisions when selecting the most appropriate coating for their steel pipes, ensuring long-lasting performance and durability.