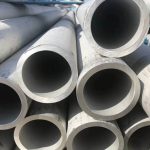
Composition of 201 Stainless Steel Pipes
May 21, 2023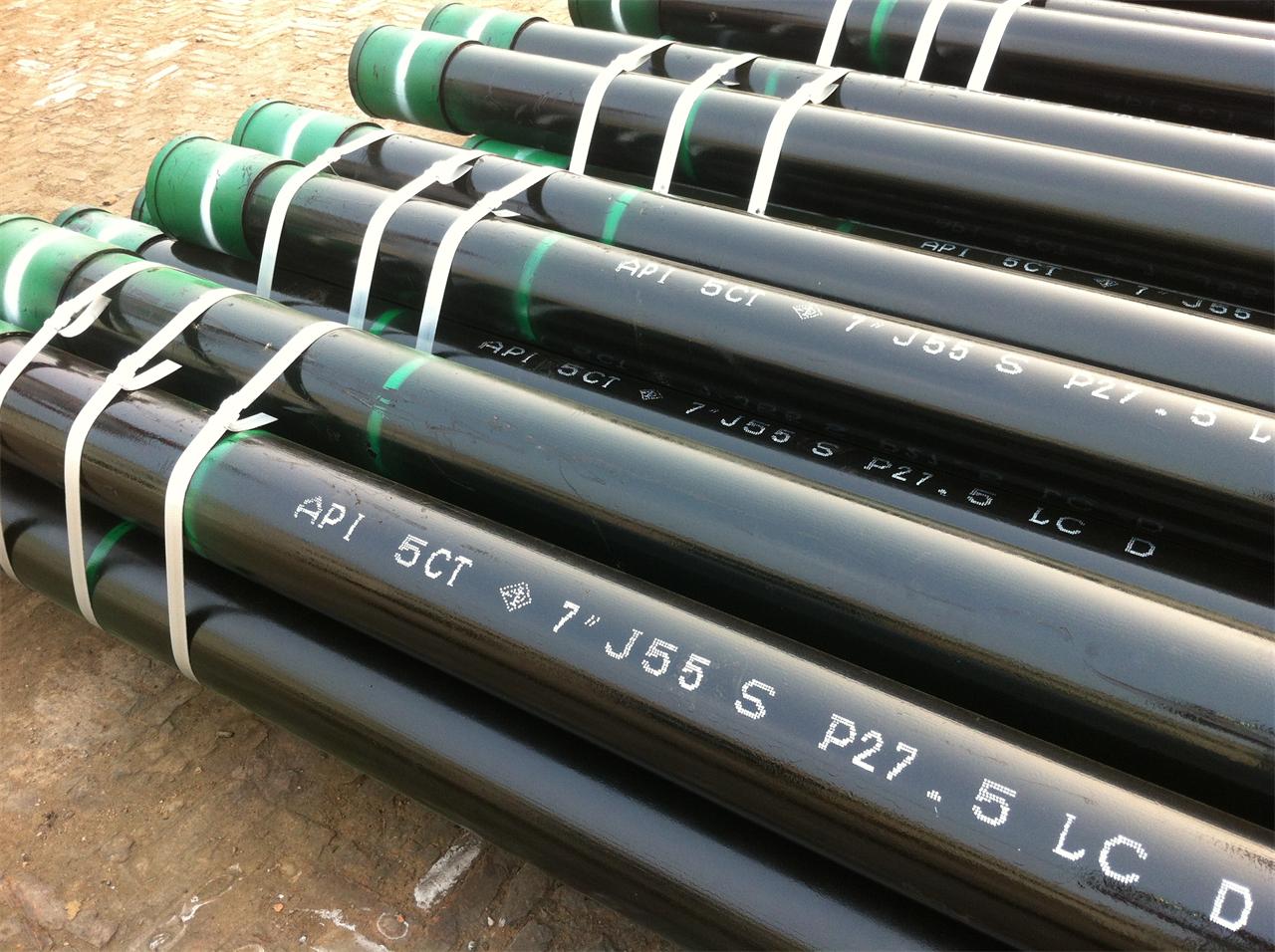
J55 K55 HFW Oil Casing Pipe Research and Development Status and Prospect
June 2, 2023Background technology: Domestic A335.P91 steel pipe is equivalent to 9Cr-1Mo martensitic heat-resistant steel in China, characterized by large diameter and thick-walled (508×32.54mm) pipes, primarily employed in the power generation and chemical industries as high-pressure steam pipelines or reheating section pipelines.
When A335.P91 steel pipes are utilized as high-pressure steam pipelines in the chemical industry, it is required that the hardness of the welded steel pipe, after heat treatment, complies with the ASME (American Society of Mechanical Engineers) specifications, with a Brinell hardness value (hereinafter referred to as hardness) less than or equal to 241HB.
The post-weld heat treatment is mainly aimed at relieving substantial stress in the welded area, improving the microstructure of the weld metal and its heat-affected zone, transforming quenched martensite into tempered martensite, reducing the hardness of the joint regions, enhancing toughness, deformability, and high-temperature endurance strength. Presently, the heat treatment process for steel pipes involves wrapping a heater around the weld seam, insulating it with thermal insulation, and maintaining a temperature of 760±10℃ for 5 hours.
During the winter in northern regions, when conducting heat treatment on A335.P91 steel pipes, the low temperatures, which can drop to -20℃, and strong winds may impact the heat treatment, resulting in a hardness value of approximately 300HB for the weld seam after heat treatment, failing to meet ASME specifications. Elevated hardness values at the weld seam increase brittleness, residual stress, and susceptibility to cracking. In extremely cold winters, performing heat treatment on large-diameter, thick-walled steel pipes often encounters the aforementioned issues, with excessively high hardness values for the weld seam, unable to meet ASME specifications, and unable to guarantee the quality of the weld.
Invention content
In order to solve the problem of the hardness of the weld seam of large-diameter A335 alloy steel pipes and thick-walled A335 alloy steel pipes not meeting the ASME specification requirements after heat treatment in winter, this invention proposes a method for assisting the heat treatment of A335 alloy steel pipe welds, which can make the hardness of the steel pipe weld seam meet the ASME specification requirements after heat treatment, and improve the quality of the base material welding.
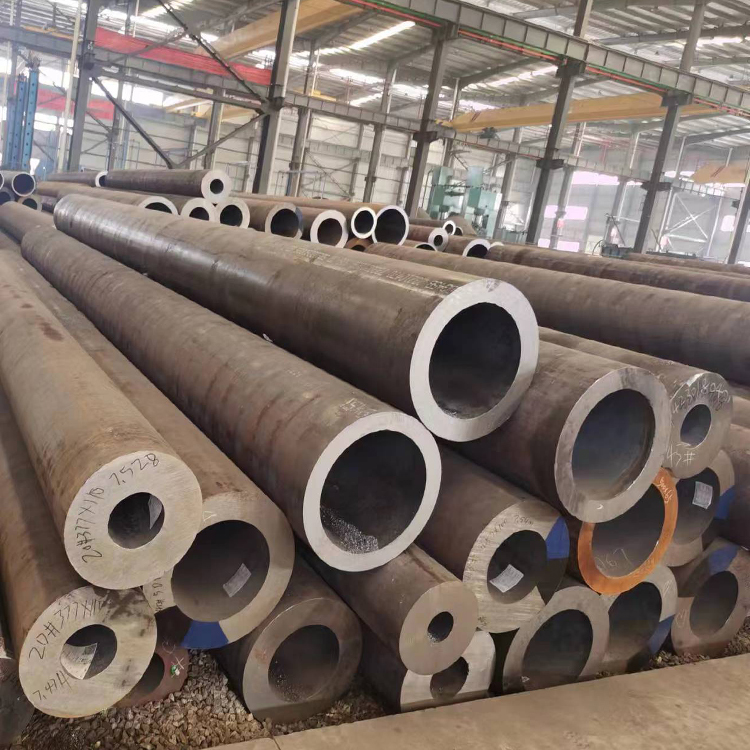
ASTM A335 STEEL GRADE
The types of alloy steel covered by the ASTM A335 – ASME SA335 specification are designed with a “P” prefix, from P5 to P92. Grades P11/P22 and P91/92 are typically found in power stations, whereas grade P5 and P9 are more common for application in the petrochemical industry. Grades P9 and P91 are in the list, the more expensive (a P91 seamless pipe may cost approx 5€ per kg.).
ASTM A335 Low-Alloy Steel (Grades) |
UNS equivalent |
C≤ | Mn | P≤ | S≤ | Si≤ | Cr | Mo |
P1 | K11522 | 0.10~0.20 | 0.30~0.80 | 0.025 | 0.025 | 0.10~0.50 | – | 0.44~0.65 |
P2 | K11547 | 0.10~0.20 | 0.30~0.61 | 0.025 | 0.025 | 0.10~0.30 | 0.50~0.81 | 0.44~0.65 |
P5 | K41545 | 0.15 | 0.30~0.60 | 0.025 | 0.025 | 0.5 | 4.00~6.00 | 0.44~0.65 |
P5b | K51545 | 0.15 | 0.30~0.60 | 0.025 | 0.025 | 1.00~2.00 | 4.00~6.00 | 0.44~0.65 |
P5c | K41245 | 0.12 | 0.30~0.60 | 0.025 | 0.025 | 0.5 | 4.00~6.00 | 0.44~0.65 |
P9 | S50400 | 0.15 | 0.30~0.60 | 0.025 | 0.025 | 0.50~1.00 | 8.00~10.00 | 0.44~0.65 |
P12 | K11562 | 0.05~0.15 | 0.30~0.60 | 0.025 | 0.025 | 0.5 | 0.80~1.25 | 0.44~0.65 |
P22 | K21590 | 0.05~0.15 | 0.30~0.60 | 0.025 | 0.025 | 0.5 | 1.90~2.60 | 0.87~1.13 |
P91 | K91560 | 0.08~0.12 | 0.30~0.60 | 0.02 | 0.01 | 0.20~0.50 | 8.00~9.50 | 0.85~1.05 |
P92 | K92460 | 0.07~0.13 | 0.30~0.60 | 0.02 | 0.01 | 0.5 | 8.50~9.50 | 0.30~0.60 |
MECHANICAL PROPERTIES
A335 Low-Alloy Pipe | UNS Number | Yield Strength ksi | Tensile Strength ksi | Elongation % | Rockwell | Brinell |
P1 | K11522 | 30 | 55 | 30 | – | – |
P2 | K11547 | 30 | 55 | 30 | – | – |
P5 | K41545 | 40 | 70 | 30 | – | 207 max |
P9 | S50400 | 30 | 60 | 30 | – | – |
P12 | K11562 | 32 | 60 | 30 | – | 174 max |
P22 | K21590 | 30 | 60 | 30 | – | – |
P91 | K91560 | 60 | 85 | 20 | – | – |
The method for assisting the heat treatment of A335 alloy steel pipe welds in this invention includes the following steps:
(1) Wrap a heater around the weld seam;
(2) For long pipe section welds: wrap a heater at a position 550-700 mm away from the heater wrapped around the weld seam on the steel pipe, and use thermal insulation material to wrap the entire steel pipe;
(3) For short pipe and elbow welds: use thermal insulation material to wrap the entire steel pipe;
(4) Start the heat treatment of the steel pipe, controlling the temperature at the weld seam to 760±10℃ during the heat treatment process, and the heat treatment time is 5 hours; during the heat treatment process, for long pipe section welds, the heater at a distance of 550-700 mm from the heater wrapped around the weld seam will control the temperature of the A335 alloy steel pipe wrapped by the heater to 200-300℃ until the heat treatment is completed.
In the aforementioned steps (2) and (3), the thickness of the thermal insulation material wrapped around the A335 alloy steel pipe is 200-250 mm.
In the aforementioned step (4), the method also includes using an infrared thermometer to measure the temperature of the insulation material at the weld seam. If the temperature of the outermost layer of insulation material is higher than 40℃, another layer of insulation material will be wrapped.
The method also includes step (5): after the heat treatment is completed, when the temperature of the insulation material drops below 20℃, remove the insulation material.
The heater mentioned is an electric heating sheet.
The insulation material mentioned is aluminum silicate insulation cotton.
The inventor found in the experiment that during the heat treatment process of large-diameter and thick-walled steel pipes, not only is the temperature at the weld seam high, but the temperature at the position 550-700 mm away from the heater wrapped around the weld seam on the steel pipe is also high, reaching up to 109℃. This indicates that there is a significant heat transfer between the weld seam and the position 550-700 mm away from the heater wrapped around the weld seam, and the heat dissipation of the steel pipe is rapid. In the existing methods, there are no protective measures for the position 550-700 mm away from the weld seam on the steel pipe. In addition, during winter construction, the temperature can drop to -20℃, and there are strong winds. These external factors affect the temperature of the position
550-700 mm away from the heater wrapped around the weld seam on the steel pipe, which in turn affects the temperature at the weld seam, ultimately affecting the hardness value of the weld seam after heat treatment.
The method of this invention also wraps a heater at a position 550-700 mm away from the heater wrapped around the weld seam on the steel pipe to provide temperature compensation for the position 550-700 mm away from the heater wrapped around the weld seam, and controls the temperature at the position 550-700 mm away from the heater wrapped around the weld seam to 200-300℃. Compared with the existing methods, this reduces the heat transfer between the weld seam and the position 550-700 mm away from the heater wrapped around the weld seam on the steel pipe, and greatly reduces the impact of temperature and other factors on the temperature at the weld seam through the position 550-700 mm away from the heater wrapped around the weld seam on the steel pipe. This slows down the heat dissipation rate of the steel pipe, ensures the temperature of the steel pipe during the heat treatment process, improves the quality of the heat treatment, and uses the method of this invention for heat treatment of the steel pipe. The hardness value at the weld seam is less than or equal to 241HB, which meets the ASME specification requirements. The method of this invention also uses thermal insulation material to wrap the entire steel pipe, further reducing the impact of temperature and other factors on the temperature at the weld seam.
Attached figure explanation
Figure 1 is a schematic diagram of the heat treatment of the weld seam of a long pipe section using the method of this invention;
Figure 2 is a schematic diagram of the heat treatment of the weld seam of a short pipe and elbow using the method of this invention.
Specific implementation
The method of this invention is introduced below in conjunction with the
Introduce the method of the present invention below in conjunction with accompanying drawing.
Embodiment one:
(1) Wrap the electric heating sheet at the weld of the steel pipe, and wrap the insulation cotton outside the electric heating sheet;
(2) As shown in Figure 1, the direction indicated by the arrow in Figure 1 is left. For the long welding joint of the pipe section: the distance between the steel pipe 10 and the electric heating sheet 11 wrapped at the weld 12 is 550 mm. Electric heating sheet 13 and right electric heating sheet 14, the distance L from the right edge of left electric heating sheet 13 to the left edge of electric heating sheet 11 is 550 millimeters; The left edge of right electric heating sheet 14 is to the right edge of electric heating sheet 11 The distance L is 550 mm; and the steel pipe 10 is completely wrapped with aluminum silicate thermal insulation cotton, and the thickness of the aluminum silicate thermal insulation cotton is 200 mm; wherein, the diameter of the left electric heating sheet 13 and the right electric heating sheet 14 is the same as that of the steel pipe 10 Cooperate, to be able to wrap up a circle of weld seam of steel pipe 10;
(3) As shown in Figure 2, for the welding joint of the short pipe 15 and the elbow 16: wrap the heating rope 17 on the elbow 16, use aluminum silicate insulation cotton to wrap the steel pipe completely, that is, wrap the short pipe 15 and the elbow The head 16 is completely wrapped, and the thickness of the aluminum silicate insulation cotton is 200 mm;
(4) Start to heat-treat the steel pipe. During the heat-treatment process, the temperature at the weld seam is controlled at 760°C, and the heat-treatment time is 5 hours; The temperature of the steel pipe 10 wrapped by the electric heater is controlled to be 200°C. Use the right electric heater 14 to control the temperature of the steel pipe 10 wrapped by the electric heater to 200°C until the heat treatment ends; The wrapped electric heater 11 is at a distance of 550 mm for temperature compensation, which reduces the influence of environmental factors such as air temperature and strong wind on the temperature of the weld 12 at a distance of 550 mm from the electric heater 11, slowing down the temperature of the steel pipe. 10 cooling speed;
During the heat treatment process, use an infrared thermometer to measure the temperature of the aluminum silicate insulation cotton at 12 places of the weld. If the temperature of the outermost layer of aluminum silicate insulation cotton is higher than 40°C, wrap another layer of aluminum silicate insulation cotton. Insulation cotton;
(5) After the heat treatment, the temperature of the welding seam dropped to 300°C, and the steel pipe 10 was allowed to cool naturally, and when the temperature of the aluminum silicate insulation wool dropped below 20°C, the aluminum silicate insulation wool was removed.
Embodiment two:
(1) Wrap the electric heating sheet at the weld of the steel pipe, and wrap the insulation cotton outside the electric heating sheet;
(2) As shown in Figure 1, the direction indicated by the arrow in Figure 1 is left. For the long welded joint of the pipe section: the distance between the steel pipe 10 and the electric heating sheet 11 wrapped at the weld 12 is 600 mm. Electric heating sheet 13 and right electric heating sheet 14, the distance L from the right edge of left electric heating sheet 13 to the left edge of electric heating sheet 11 is 600 millimeters; The left edge of right electric heating sheet 14 is to the right edge of electric heating sheet 11 The distance L is 600 mm; and the steel pipe 10 is completely wrapped with aluminum silicate thermal insulation cotton, and the thickness of the aluminum silicate thermal insulation cotton is 220 mm; wherein, the diameter of the left electric heating sheet 13 and the right electric heating sheet 14 is the same as that of the steel pipe 10 Cooperate, to be able to wrap up a circle of weld seam of steel pipe 10;
(3) As shown in Figure 2, for the welding joint of the short pipe 15 and the elbow 16: wrap the heating rope 17 on the elbow 16, use aluminum silicate insulation cotton to wrap the steel pipe completely, that is, wrap the short pipe 15 and the elbow The head 16 is fully wrapped, and the thickness of the aluminum silicate insulation cotton is 220 mm;
(4) Start to heat-treat the steel pipe. During the heat-treatment process, the temperature at the weld seam is controlled at 765°C, and the heat-treatment time is 5 hours; The temperature of the steel pipe 10 wrapped by the electric heating sheet is controlled to be 250°C, and the temperature of the steel pipe 10 wrapped by the electric heating sheet 14 is controlled to 250°C by using the right electric heating sheet 14 until the heat treatment is completed; to slow down the heat dissipation rate of the steel pipe 10;
During the heat treatment process, use an infrared thermometer to measure the temperature of the aluminum silicate insulation cotton at 12 places of the weld. If the temperature of the outermost layer of aluminum silicate insulation cotton is higher than 40°C, wrap another layer of aluminum silicate insulation cotton. Insulation cotton;
(5) After the heat treatment, the temperature of the welding seam dropped to 300°C, and the steel pipe 10 was allowed to cool naturally, and when the temperature of the aluminum silicate insulation wool dropped below 20°C, the aluminum silicate insulation wool was removed.
Embodiment three:
(1) Wrap the electric heating sheet at the weld of the steel pipe, and wrap the insulation cotton outside the electric heating sheet;
(2) As shown in Figure 1, the direction indicated by the arrow in Figure 1 is left. For the long welding joint of the pipe section: the distance between the steel pipe 10 and the electric heating sheet 11 wrapped at the weld 12 is 750 mm. Electric heating sheet 13 and right electric heating sheet 14, the distance L from the right edge of left electric heating sheet 13 to the left edge of electric heating sheet 11 is 750 millimeters; The left edge of right electric heating sheet 14 is to the right edge of electric heating sheet 11 The distance L is 750 mm; and the steel pipe 10 is completely wrapped with aluminum silicate insulation cotton, and the thickness of the aluminum silicate insulation cotton is 250 mm; wherein, the diameter of the left electric heating sheet 13 and the right electric heating sheet 14 is the same as that of the steel pipe 10 Cooperate, to be able to wrap up a circle of weld seam of steel pipe 10;
(3) As shown in Figure 2, for the welding joint of the short pipe 15 and the elbow 16: wrap the heating rope 17 on the elbow 16, use aluminum silicate insulation cotton to wrap the steel pipe completely, that is, wrap the short pipe 15 and the elbow The head 16 is completely wrapped, and the thickness of the aluminum silicate insulation cotton is 250mm;
(4) Start to heat-treat the steel pipe. During the heat-treatment process, the temperature at the weld seam is controlled at 770°C, and the heat-treatment time is 5 hours; The temperature of the steel pipe 10 wrapped by the electric heating sheet is controlled to be 300°C, and the temperature of the steel pipe 10 wrapped by the electric heating sheet 14 is controlled to 300°C by using the right electric heating sheet 14 until the heat treatment is completed; to slow down the heat dissipation rate of the steel pipe 10;
During the heat treatment process, use an infrared thermometer to measure the temperature of the aluminum silicate insulation cotton at 12 places of the weld. If the temperature of the outermost layer of aluminum silicate insulation cotton is higher than 40°C, wrap another layer of aluminum silicate insulation cotton. Insulation cotton;
(5) After the heat treatment, the temperature of the welding seam dropped to 300°C, and the steel pipe 10 was allowed to cool naturally, and when the temperature of the aluminum silicate insulation wool dropped below 20°C, the aluminum silicate insulation wool was removed.
Using the method of the present invention reduces the heat transfer between the weld seam and the electric heating sheet wrapped at the steel pipe at a distance of 550-700 mm from the weld seam, and also greatly reduces the influence of air temperature and other factors on the temperature of the weld seam. Influence, slow down the heat dissipation speed of the steel pipe, ensure the temperature of the steel pipe in the heat treatment process, improve the quality of heat treatment, use the method of the present invention to carry out heat treatment to the steel pipe, the hardness value of the weld seam is less than or equal to 241HB, meet the specification requirement of ASME. The method of the present invention also uses heat-insulating material to fully wrap the steel pipe, which further reduces the influence of air temperature and other factors on the temperature of the weld.
Comparative example one
(1) Wrap the electric heating sheet at the welding seam, and wrap the insulation cotton outside the electric heating sheet;
(2) Start to heat-treat the steel pipe. During the heat-treatment process, the temperature at the weld seam is controlled at 765° C., and the heat-treatment time is 5 hours.
Table 1 below is a data comparison of the hardness value at the weld after the heat treatment method of Comparative Example 1 and the methods of Example 1, Example 2 and Example 3 are completed.
Table 1
It can be concluded from Table 1 that the steel pipe is heat treated using the method of Comparative Example 1. After the heat treatment is completed, 5 points are selected at the weld. The hardness values of the 5 points are 299HB, 311HB, 317HB, 291HB, 294HB, and 5 The hardness values of the points are all greater than 241HB, which cannot meet the requirements of the ASME standard; using the method of embodiment two, after the heat treatment is completed, 5 points are selected at the weld, and the hardness values of the 5 points are respectively 200HB, 215HB, 218HB, and 222HB , 217HB, the hardness values of 5 points are all less than 241HB, which meets the requirements of the ASME specification; using the method of embodiment 1 and embodiment 3, the hardness value of the weld after heat treatment is also all less than 241HB, which meets the specification requirements of ASME.