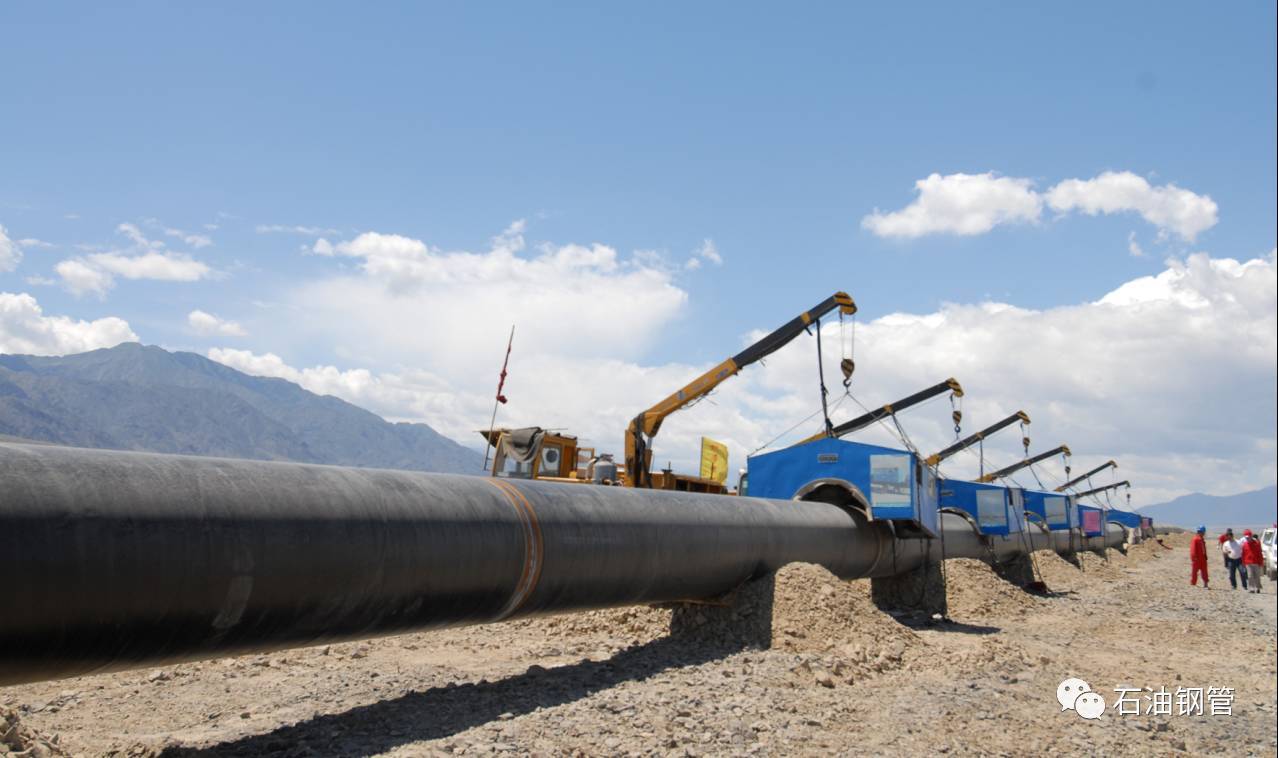
What are the risks of natural gas pipeline construction?
August 3, 2018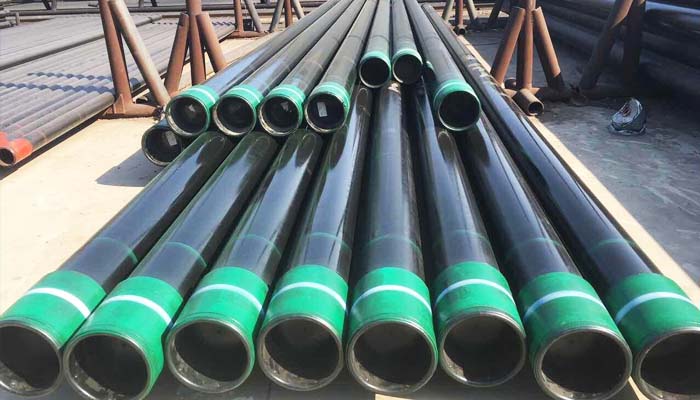
Protective coating for petroleum pipe
September 12, 2018What is the difference between pipe vs tube? A pipe is a round tubular to transport or distribute fluids and gases. Steel pipes are designated by a nominal size value (NPS or DN), which represent a rough indication of their inside diameter and fluid conveyance capacity. A tube is a round, rectangular, squared or oval hollow section measured by outside diameter (“OD”) and wall thickness (“WT”), expressed in inches or millimeters.
Pipes are used for conveying fluids and gases; tubes are used to manufacturing pressure equipment (tubing) and for mechanical applications.
PIPE INSIDE DIAMETER
The word “steel pipe” refers to round hollow sections used for transmission and distribution pipelines and piping systems that convey fluids and gases – such oil & gas, propane, steam, acids, and water.
The most important dimension for a steel pipe is the inside diameter (“pipe ID”), which indicates the rough (not the exact) fluid conveyance capacity of the tubular. The ID is expressed in NPS” or “DN” (nominal pipe size, or bore size).
The pipe outside diameter (OD) does not match the nominal size for pipes below NPS 14 inches (a 2 inches pipe, for instance, has an internal flow capacity of approximately 2 inches, but has an outside diameter of 2.375 inches). For pipes of a given NPS, the pipe outside diameter is fixed, whereas the pipe inside diameter decreases by increasing schedule values (pipe wall thickness).
The most important mechanical parameters for pipes are the pressure rating, the yield strength, and the ductility.
The standard combinations of pipe nominal diameter and wall thickness (schedule) are covered by the ASME B36.10 and ASME B36.19 specifications (respectively, carbon and alloy pipes, and stainless steel pipes).
PIPE INSIDE DIAMETER CALCULATOR
As mentioned, the outside diameter of pipes of a specific NPS is constant but the inside diameter of the pipe (ID) changes depending on the pipe schedule.
The pipe ID can be easily calculated, as long as the pipe NPS and schedule are known.
The pipe ID can be calculated by deducting from the pipe NPS the pipe wall thickness multiplied by 2 (the pipe WT can be taken from the schedule). Example: for a 12 NPS pipe (DN 300 mm), schedule 40, the pipe outside diameter and the wall thickness are 12.75 inches (324 mm) and 0.406 inches (10.4 mm).
Therefore, the pipe ID (internal diameter) is 12.75 inches – 2 x 0.406 inches = 11.94 inches, or Pipe ID = 324 mm – 2 x 10.4 mm = 303.2 mm.
It should be noted that this calculation is just theoretical, as pipes have a wall thickness tolerance which is generally +/-12.5% for ASME pipes. Hence the actual ID of a given pipe may differ by +/- 12,5% from the theoretical value.
TUBE OUTSIDE DIAMETER AND WALL THICKNESS
The word “tube” refers to round, square, rectangular, and oval hollow sections used for pressure equipment (boilers, heaters, and superheaters), for mechanical applications and for instrumentation systems. For these type of applications, the outside diameter and the wall thickness of the tube are the most important dimensions (contrary to pipes) together with its mechanical properties (yield, tensile strength, and elongation) are key.
The outside diameter and the wall thickness of a tube (“tube OD”) are expressed in inches or millimeters; the difference between the outside diameter and the wall thickness, multiplied by two, defines the inside diameter of the tube.
In terms of pipe vs tube pricing, steel tubes are generally more expensive than steel pipe due to their stricter manufacturing tolerances and mills productivity (tons produced by the hour). The most important physical properties of steel tubes are the hardness, the tensile strength, and highly precise dimensions.
TOP 10 DIFFERENCES PIPE VS TUBE
To summarize the difference between pipe and tube and the pipe meaning vs. tube meaning
PIPE VS TUBE: DIFFERENCE AREAS | PIPE | TUBE | |
1 | Key Dimensions | The most important dimension for a pipe is the inside diameter (ID), expressed in NPS (nominal pipe size) or DN (nominal diameter), which defines its fluid conveyance capacity. The NPS does not match the true inside diameter, it is a rough indication | The most important dimensions for a steel tube are the outside diameter (OD) and the wall thickness (WT). These parameters are expressed in inches or millimeters and express the true dimensional value of the hollow section. |
2 | Wall Thickness | The thickness of a steel pipe is designated with a “Schedule” value (the most common are Sch. 40, Sch. STD., Sch. XS/XH, Sch. XXS). Two pipes of different NPS and same schedule have different wall thicknesses in inches or millimeters. | The wall thickness of a steel tube is expressed in inches or millimeters. For tubing, the wall thickness is measured also with a gage nomenclature (BWG, SWG). |
3 | Tubular Shape | Round only | Round, rectangular, square, oval |
4 | Production range | Extensive (up to 80 inches and above) | Narrower range for tubing (up to 5 inches), larger for steel tubes for mechanical applications |
5 | Tolerances (straightness, dimensions, roundness, etc) | Tolerances are set, but rather loose | Steel tubes are produced to very strict tolerances. Tubulars undergo several dimensional quality checks, such as straightness, roundness, wall thickness, surface, during the manufacturing process. |
6 | Production Process | Pipes are generally made to stock with highly automated and efficient processes, i.e. pipe mills produce on a continuous basis and feed distributors stock around the world. | Tubes manufacturing is more lengthy and laborious |
7 | Delivery time | Can be short | Generally longer |
8 | Market price | Relatively lower price per ton than steel tubes | Higher due to lower mills productivity per hour, and due to the stricter requirements in terms of tolerances and inspections |
9 | Materials | Wide range of materials | Tubing is available in carbon steel, low alloy, stainless steel and nickel-alloys; steel tubes for mechanical applications are mostly of carbon steel |
10 | End Connections | The most common are beveled and plain ends | Threaded and grooved ends are available for quicker connections on site |