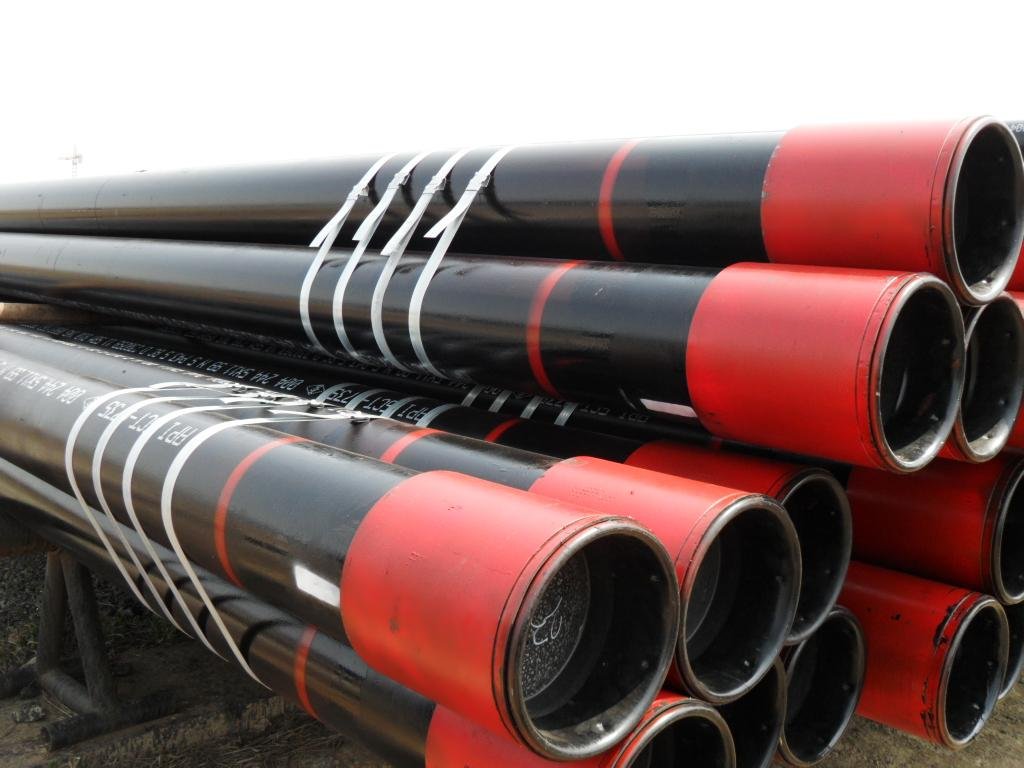
Classification and function of casing
June 17, 2022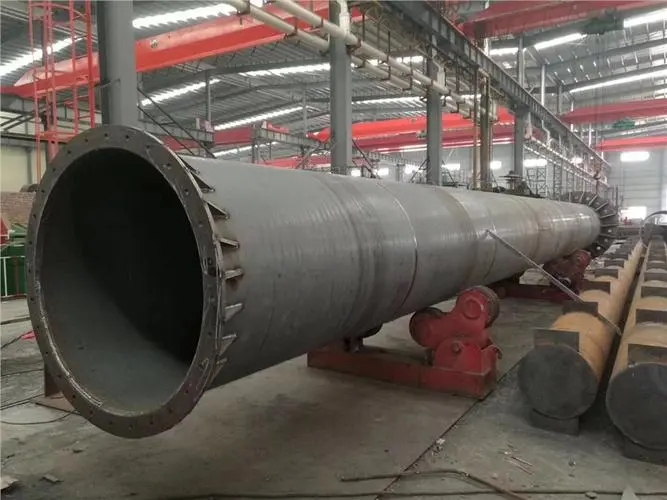
How wear occurs in pipes and why high-strength wear-resistant steel outperforms regular steel pipe in abrasive environments
June 21, 2022Welded vs. Seamless Production in the Tube-Making Process
Steel tubes, from automobile manufacturing to gas pipes, can be either welded from alloys – metals made from different chemical elements – or constructed seamlessly from a melting furnace.
The production method lends much to the various designs of the steel pipe. Changing the diameter and thickness can lead to differences in strength and flexibility for large-scale projects such as gas transportation pipelines and precise instruments such as hypodermic needles.
The closed structure of a tube, be it round, square or whatever shape, can suit whatever application is needed, from the flow of liquids to the prevention of corrosion.
Seamless Tubing Manufacturing
Knowing that distinction can also help in determining which tubing is best for a given application, welded or seamless. The method of manufacturing welded and seamless tubing is evident in their names alone. Seamless tubes are as defined – they do not have a welded seam. The tubing is manufactured through an extrusion process where the tube is drawn from a solid stainless steel billet and extruded into a hollow form. The billets are first heated and then formed into oblong circular molds that are hollowed in a piercing mill. While hot, the molds are drawn through a mandrel rod and elongated. The mandrel milling process increases the molds length by twenty times to form a seamless tube shape. Tubing is further shaped through pilgering, a cold rolling process, or cold drawing.
Welded Tubing Manufacturing
A welded stainless steel tube is produced through roll forming strips or sheets of stainless steel into a tube shape and then welding the seam longitudinally. Welded tubing can be accomplished either by hot forming and cold forming processes. Of the two, cold forming results in smoother finishes and tighter tolerances. However, each method creates a durable, strong, steel tube that resists corrosion. The seam can be left beaded or it can be further worked by cold rolling and forging methods. The welded tube can also be drawn similar to seamless tubing to produce a finer weld seam with better surface finishes and tighter tolerances.
The Step-by-Step Engineering Process for Welded and Seamless Steel Tubes
The overall process of making steel tubes involves converting raw steel into ingots, blooms, slabs and billets (all of which are materials that can be welded), creating a pipeline on a production line and forming the pipe into a desired product.
Creating Ingots, Blooms, Slabs and Billets
Iron ore and coke, a carbon-rich substance from heated coal, are melted into a liquid substance in a furnace and then blasted with oxygen to create molten steel. This material is cooled into ingots, large castings of steel for storing and transporting materials, that are shaped between rollers under high amounts of pressure.
Some ingots are passed through steel rollers that stretch them into thinner, longer pieces to create blooms, intermediates between steel and iron. They are also rolled into slabs, pieces of steel with rectangular cross-sections, through stacked rollers that cut the slabs into shape.
Crafting These Materials Into Pipes
More rolling devices flatten – a process known as coining – blooms into billets. These are metal pieces with round or square cross-sections, which are even longer and thinner. Flying shears cut the billets at precise positions so the billets can be stacked and formed into seamless pipe.
Slabs are heated to about 2,200 degrees Fahrenheit (1,204 degrees Celsius) until they are malleable and then thinned into skelp, which are narrow strips of ribbon up to 0.25 miles (0.4 kilometers) long. The steel is then cleaned using tanks of sulfuric acid followed by cold and hot water and transported to pipe-making factories.
Developing Welded and Seamless Pipes
For welded pipes, an unwinding machine unwinds skelp and passes it through rollers to cause the edges to curl and create pipe shapes. Welding electrodes use an electric current to seal the ends together before a high-pressure roller tightens it. The process can produce pipe as quickly as as 1,100 ft (335.3 m) per minute.
For seamless pipes, a process of heating and high-pressure rolling of square billets causes them to stretch with a hole in the center. Rolling mills pierce the pipe for the desired thickness and shape.
Further Processing and Galvanization
Further processing may include straightening, threading (cutting tight grooves into the ends of pipes) or covering with a protective oil of zinc or galvanizing to prevent rusting (or whatever is necessary for the pipe’s purpose). Galvanization usually involves electrochemical and electrodeposition processes of zinc coatings to protect the metal from corrosive material such as salt water.
The process acts to deter harmful oxidizing agents in water and air. Zinc acts as an anode to oxygen to form zinc oxide, which reacts with water to form zinc hydroxide. These zinc hydroxide molecules form zinc carbonate when exposed to carbon dioxide. Finally, a thin, impenetrable, insoluble layer of zinc carbonate sticks to zinc to protect the metal.
A thinner form, electrogalvanization, is generally used in automobile parts that require rust-proofing paint such that the hot-dip reduces the strength of the base metal. Stainless steels are created when stainless parts are galvanized to carbon steel.
Choosing Between Welded and Seamless
There are benefits and drawbacks in choosing welded vs. seamless tubing.
Seamless Tubing
By definition seamless tubes are completely homogenous tubes, the properties of which give seamless tubing more strength, superior corrosion resistance, and the ability to withstand higher pressure than welded tubes. This makes them more suitable in critical applications in harsh environments, but it comes with a price.
Benefits
- Stronger
- Superior corrosion resistance
- Higher pressure resistance
Applications
- Oil and gas control lines
- Chemical injection lines
- Below sea safety valves
- Chemical processing plant steam and heat trace bundles
- Fluid and gas transfer
Welded Tubing
Welded tubing is generally less expensive than seamless tubing due to the simpler manufacturing process in creating welded tubing. It is also readily available, like seamless tubing, in long continuous lengths. Standard sizes can be produced with similar lead times for both welded and seamless tubing. Seamless tubing costs can be offset in smaller manufacturing runs if less quantity is required. Otherwise, though custom sized seamless tubing can be produced and delivered more quickly, it is more costly.
Benefits
- Cost-efficient
- Readily available in long lengths
- Fast lead times
Applications
- Architectural applications
- Hypodermic needles
- Automotive industry
- Food and beverage industry
- Marine industry
- Pharmaceutical industry
Costs of Welded vs Seamless
Costs of seamless and welded tubing are also related to such properties as strength and durability. Welded tubing’s easier manufacturing process can produce larger diameter tubing with thinner wall sizes for less. Such properties are more difficult to produce in seamless tubing. On the other hand, heavy walls can be achieved more easily with seamless tubing. Seamless tubing is often preferred for heavy wall tubing applications that require or can withstand high pressure or perform in extreme environments.