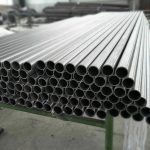
ASTM B338 Ti-Pd Alloy Gr7 Titanium Steel Pipe
January 5, 2025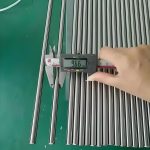
Quality in Turning of Inconel X-750 Superalloy Steel Pipe
January 14, 2025Inconel Alloy X-750 Superalloy Pipes & Tubes: Physical Constants and Thermal Properties”
Main Topic | Subtopics |
---|---|
1. Introduction to Inconel Alloy X-750 | – Overview of Inconel Alloy X-750 – Common applications and industries – Benefits of using Inconel Alloy X-750 |
2. Chemical Composition of Inconel X-750 | – Key elements and their percentages – Table 1: Typical chemical composition – Role of each element in alloy performance |
3. Physical Properties of Inconel X-750 | – Density – Melting range – Specific heat capacity – Magnetic properties |
4. Thermal Properties of Inconel X-750 | – Thermal conductivity – Thermal expansion – Table 2: Thermal properties at various temperatures |
5. Mechanical Properties of Inconel X-750 | – Tensile strength – Yield strength – Elongation percentage – Table 3: Mechanical properties at different conditions |
6. Corrosion Resistance of Inconel X-750 | – Resistance to oxidation at high temperatures – Corrosion performance in cryogenic environments – Applications requiring corrosion resistance |
7. Heat Treatment of Inconel X-750 | – Common heat treatments (solution treating, stabilization treating, precipitation treating) – Influence on mechanical and thermal properties |
8. Physical Constants of Inconel X-750 | – Young’s modulus – Poisson’s ratio – Electrical resistivity – Coefficient of friction |
9. Manufacturing and Fabrication | – Availability of pipes and tubes – Methods of fabrication (hot working, cold working) – Machinability and welding of Inconel X-750 |
10. Applications of Inconel X-750 Pipes & Tubes | – Gas turbines – Rocket-engine components – Heat-treating fixtures – Pressure vessels |
11. Advantages of Inconel X-750 Over Other Alloys | – Comparison with other nickel-chromium alloys – Longevity and durability in extreme environments |
12. Limitations and Challenges | – Challenges in machining – Cost considerations – Effect of prolonged high-temperature exposure |
13. Case Studies | – Real-world examples of Inconel X-750 usage – Performance data and outcomes |
14. Thermal Properties in Detail | – High-temperature stability – Resistance to thermal fatigue – Role in sustaining mechanical properties under heat |
15. Frequently Asked Questions (FAQs) | – FAQs related to chemical composition, heat treatments, and thermal properties |
Inconel Alloy X-750 Superalloy Pipes & Tubes: Physical Constants and Thermal Properties
1. Introduction to Inconel Alloy X-750
Inconel Alloy X-750 (UNS N07750/W. Nr. 2.4669) is a high-performance nickel-chromium superalloy known for its exceptional mechanical properties and corrosion resistance in extreme environments. This alloy is particularly valued in industries like aerospace, power generation, and chemical processing. Its ability to perform at temperatures ranging from cryogenic levels to 1800°F (982°C) makes it a preferred choice for critical applications such as turbine components, fasteners, and heat-treating fixtures.
The precipitation-hardenable nature of Inconel X-750 enhances its strength, especially when subjected to specific heat treatments. However, at temperatures exceeding 1300°F (704°C), some of the effects of precipitation hardening diminish, but the alloy still retains useful mechanical strength up to 1800°F.
2. Chemical Composition of Inconel X-750
The chemical composition of Inconel Alloy X-750 significantly contributes to its high-temperature strength, corrosion resistance, and other favorable properties. Table 1 summarizes the typical composition:
Table 1: Chemical Composition of Inconel Alloy X-750
Element | Percentage (%) |
---|---|
Nickel (Ni) | 70.0 (min) |
Chromium (Cr) | 14.0-17.0 |
Iron (Fe) | 5.0-9.0 |
Titanium (Ti) | 2.25-2.75 |
Aluminum (Al) | 0.40-1.0 |
Niobium (Nb) | 0.7-1.2 (includes Ta) |
Cobalt (Co) | 1.0 (max) |
Carbon (C) | 0.08 (max) |
Manganese (Mn) | 1.0 (max) |
Silicon (Si) | 0.5 (max) |
Sulfur (S) | 0.01 (max) |
Copper (Cu) | 0.5 (max) |
Each element serves a distinct purpose. Nickel ensures high-temperature stability and oxidation resistance, while chromium adds to the corrosion-resistant properties. Aluminum and titanium facilitate precipitation hardening, improving strength.
3. Physical Properties of Inconel X-750
Inconel X-750 is characterized by its remarkable physical properties, enabling it to withstand a variety of environments. Below are some key physical constants:
- Density: 8.28 g/cm³
- Melting Range: 1393–1427°C (2540–2600°F)
- Specific Heat Capacity: 0.103 BTU/lb°F at 70°F (20°C)
- Electrical Resistivity: 620 µΩ·cm at room temperature
- Magnetic Properties: Non-magnetic
These properties make Inconel X-750 an ideal choice for components requiring durability under extreme thermal and mechanical stress.
4. Thermal Properties of Inconel X-750
Inconel X-750 excels in thermal performance, which is critical for applications exposed to fluctuating temperatures. Below are its thermal properties:
Table 2: Thermal Properties of Inconel Alloy X-750
Temperature (°F) | Thermal Conductivity (BTU/ft·h·°F) | Thermal Expansion (10⁻⁶/°F) |
---|---|---|
70 | 88.6 | 6.9 |
200 | 93.2 | 7.1 |
400 | 100.8 | 7.3 |
800 | 116.3 | 7.7 |
1200 | 132.8 | 8.0 |
These properties highlight Inconel X-750’s ability to maintain its structural integrity under thermal stress, making it invaluable for turbine blades, ducting systems, and thrust reversers.
5. Mechanical Properties of Inconel X-750
The mechanical properties of Inconel X-750 can vary depending on its heat treatment. Below are the general mechanical characteristics:
Table 3: Mechanical Properties of Inconel Alloy X-750
Property | Value |
---|---|
Tensile Strength | 160 ksi (1100 MPa) |
Yield Strength | 90 ksi (620 MPa) |
Elongation (% in 2 inches) | 25% |
Hardness (Rockwell C Scale) | 35-40 |
Inconel X-750 is specifically designed for applications that require high tensile strength, low elongation, and stability at elevated temperatures.
6. Corrosion Resistance of Inconel X-750
Inconel X-750 provides excellent resistance to oxidation and corrosion in various conditions. It performs well in environments where exposure to high temperatures, cryogenic conditions, or chemically reactive substances is inevitable. Applications in rocket engines and gas turbines utilize this corrosion-resistant property extensively.
- Oxidation Resistance: Resists scaling at temperatures up to 1800°F.
- Cryogenic Conditions: Exhibits no embrittlement and retains toughness.
7. Heat Treatment of Inconel X-750
Heat treatments are essential in tailoring Inconel X-750’s mechanical properties to specific application needs. Common methods include:
- Solution Treating (2100°F): Enhances ductility.
- Stabilization Treating (1550°F): Improves resistance to creep.
- Precipitation Treating (1300°F): Boosts hardness and tensile strength.
8. Physical Constants of Inconel X-750
Inconel X-750 exhibits physical constants that enable it to perform exceptionally in both high and low-temperature environments. These constants are vital for understanding its behavior in different industrial applications.
Key Physical Constants:
Property | Value |
---|---|
Young’s Modulus (Elastic Modulus): | 31 x 10⁶ psi (213 GPa) |
Shear Modulus: | 11.9 x 10⁶ psi (82 GPa) |
Poisson’s Ratio: | 0.31 |
Electrical Resistivity: | 620 µΩ·cm at room temperature |
Density: | 8.28 g/cm³ |
The high elastic modulus contributes to its strength under mechanical stress, and its electrical resistivity ensures stability in electrical applications at high temperatures.
9. Manufacturing and Fabrication
Availability of Inconel X-750 Pipes & Tubes
Inconel X-750 pipes and tubes are available in a variety of forms to meet different industrial requirements. Standard forms include seamless pipes, welded pipes, and custom-fabricated tubes.
Fabrication Techniques
Inconel X-750 is considered relatively easy to fabricate when proper techniques are employed. Common methods include:
- Hot Working:
- Recommended temperature range: 1800–2200°F (982–1204°C).
- Rapid cooling is necessary to preserve mechanical properties.
- Cold Working:
- Increases strength and hardness.
- Annealing is required to reduce work hardening effects.
- Machining:
- Inconel X-750 is challenging to machine due to its hardness and work-hardening nature.
- Use carbide-tipped tools and low cutting speeds for best results.
- Welding:
- Inconel X-750 can be welded using conventional welding methods, such as gas tungsten arc welding (GTAW) and gas metal arc welding (GMAW).
- Post-weld heat treatment is recommended to restore mechanical properties.
Fabrication Challenges
- High hardness can cause tool wear during machining.
- Specialized equipment is often required for shaping and cutting.
10. Applications of Inconel X-750 Pipes & Tubes
Inconel X-750 pipes and tubes are employed across a wide range of industries due to their exceptional strength, thermal stability, and corrosion resistance. Below are key application areas:
Aerospace Industry
- Turbine Blades and Wheels: Withstands high centrifugal stresses and temperatures in jet engines.
- Thrust Reversers: Used in components exposed to extreme heat during landing.
Energy and Power Generation
- Nuclear Reactors: Utilized in reactor cores and heat exchangers due to its resistance to radiation and thermal stress.
- Steam Generators: Handles high-temperature and high-pressure environments.
Chemical and Petrochemical Processing
- Heat Exchangers: Resists corrosion in harsh chemical environments.
- Pipes and Tubes: Transport reactive chemicals at elevated temperatures.
Other Industrial Applications
- Heat-Treating Fixtures: Maintains strength and stability in furnaces.
- Extrusion Dies: Resists deformation under extreme mechanical stress.
- Cryogenic Systems: Performs exceptionally in sub-zero temperatures without embrittlement.
11. Advantages of Inconel X-750 Over Other Alloys
Inconel X-750 offers numerous advantages compared to other nickel-based and stainless steel alloys, especially in extreme environments:
Feature | Inconel X-750 | Other Alloys |
---|---|---|
Temperature Resistance: | Retains strength up to 1800°F. | Often limited to 1200–1500°F. |
Corrosion Resistance: | Excellent in both high-temperature oxidation and cryogenic conditions. | May degrade faster in oxidizing environments. |
Mechanical Strength: | High tensile and yield strength even after prolonged exposure to heat. | Lower strength over time at high temperatures. |
Longevity: | Suitable for long-term applications in high-stress environments. | May require frequent replacement. |
Inconel X-750’s ability to resist thermal fatigue and oxidation gives it a competitive edge in critical applications.
12. Limitations and Challenges
Despite its outstanding properties, Inconel X-750 does have some limitations:
1. Machining Difficulties:
- The hardness of Inconel X-750 causes significant wear on cutting tools.
- Requires advanced machining techniques and equipment.
2. Cost Considerations:
- The alloy is more expensive than stainless steel and some other nickel-based alloys.
- Its high price may limit its use in non-critical applications.
3. Prolonged Exposure at High Temperatures:
- While it retains strength up to 1800°F, the effects of precipitation hardening diminish over time at temperatures above 1300°F.
13. Case Studies
Case Study 1: Gas Turbine Application
- Objective: To improve turbine blade lifespan in high-temperature environments.
- Outcome: Blades manufactured with Inconel X-750 exhibited 30% longer operational lifetimes compared to previous materials, reducing maintenance costs.
Case Study 2: Cryogenic Tank Application
- Objective: To enhance tank durability for liquid nitrogen storage.
- Outcome: Inconel X-750 pipes showed no embrittlement over 5 years of continuous use in cryogenic conditions, ensuring safety and reliability.
14. Thermal Properties in Detail
Thermal properties play a pivotal role in the success of Inconel X-750 pipes and tubes in critical applications:
High-Temperature Stability:
Inconel X-750 maintains its mechanical integrity under high thermal loads. This property makes it an ideal material for turbines, exhaust systems, and heat exchangers.
Resistance to Thermal Fatigue:
Thermal fatigue occurs when a material is subjected to repeated temperature changes. Inconel X-750’s thermal expansion coefficient and high tensile strength minimize fatigue-related failures.
Cryogenic Performance:
The alloy remains ductile and corrosion-resistant at cryogenic temperatures, making it a preferred choice for space applications and low-temperature storage systems.
15. Frequently Asked Questions (FAQs)
Q1: What makes Inconel X-750 unique compared to other superalloys?
A1: Its combination of high-temperature strength, corrosion resistance, and precipitation-hardening properties sets it apart from other superalloys.
Q2: How does Inconel X-750 perform under cryogenic conditions?
A2: Inconel X-750 maintains its toughness and resistance to corrosion even at extremely low temperatures, making it suitable for cryogenic storage and aerospace applications.
Q3: What is the maximum temperature Inconel X-750 can withstand?
A3: Inconel X-750 retains useful strength up to 1800°F (982°C).
Q4: Can Inconel X-750 pipes be welded?
A4: Yes, Inconel X-750 can be welded using standard methods, but post-weld heat treatment is recommended to restore mechanical properties.
Q5: Why is Inconel X-750 preferred in gas turbines?
A5: Its ability to handle high centrifugal stresses, combined with its oxidation resistance, makes it ideal for turbine components.
Q6: Is Inconel X-750 resistant to oxidation?
A6: Yes, it provides excellent oxidation resistance, even at temperatures up to 1800°F, making it suitable for extreme heat applications.