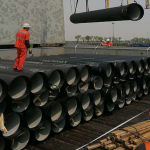
Ductile Iron Pipe for Wastewater
March 17, 2025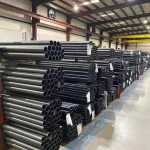
ASTM A209/A209M Alloy Steel Boiler Superheater Pipe
March 28, 2025Introduction to the Double Flange 90° Duck Foot Ductile Iron Bend
The Double Flange 90° Duck Foot Ductile Iron Bend is a specialized pipe fitting designed to redirect fluid flow at a 90-degree angle while providing enhanced stability through its distinctive “duck foot” base. Crafted from ductile iron, this fitting is a robust solution for piping systems requiring both directional change and structural support. Its double-flanged design—one flange connecting to a pipe and the other forming a wide, anchoring base—makes it ideal for applications like wastewater, stormwater, and irrigation systems. With its high strength, corrosion resistance, and adaptability, this bend is a critical component in modern infrastructure across various industries. Let’s explore its specifications and why it’s a standout choice.
Material: Ductile Iron
The fitting is made from ductile iron, an iron-carbon alloy (2-4% carbon, 1-3% silicon) treated with magnesium (0.03-0.06%) to form spherical graphite nodules instead of flakes. This gives it exceptional properties:
-
Tensile Strength: 60,000-120,000 psi, rivaling mild steel.
-
Ductility: 10-20% elongation, allowing it to flex without fracturing.
-
Corrosion Resistance: Forms a protective oxide layer, enhanced by coatings and linings.
Ductile iron’s combination of strength and toughness makes it superior to brittle gray cast iron, while its cost-effectiveness and natural corrosion resistance outshine carbon steel in moist or aggressive environments. Its casting properties also enable the complex duck foot shape to be produced efficiently.
Standards
The double flange 90° duck foot bend adheres to international standards ensuring quality and compatibility:
-
EN 545: European standard for ductile iron fittings in potable water systems, specifying linings and pressure ratings.
-
EN 598: Focuses on wastewater applications, emphasizing resistance to chemical and abrasive conditions.
-
ISO 2531: Global standard for ductile iron pipes and fittings, covering dimensions and mechanical properties.
-
ANSI/AWWA: U.S. standards (e.g., AWWA C110) for fittings, ensuring performance in water and wastewater systems.
These standards mandate rigorous testing (e.g., hydrostatic pressure tests up to 50 bar for PN40) and compatibility with other pipeline components.
Size
Available in sizes from DN50 to DN2600mm (50 mm to 2,600 mm, or roughly 2 to 102 inches), this fitting caters to a wide range of applications:
-
DN50-DN300: Small laterals, irrigation lines, or pump connections.
-
DN350-DN800: Medium-sized wastewater or stormwater systems.
-
DN900-DN2600: Large municipal sewers or irrigation trunk lines.
The size dictates flange dimensions and bolt hole patterns, ensuring a secure fit across the spectrum.
Color
The fitting’s exterior is coated in various colors for identification and protection:
-
Blue: Common for potable water (per EN 545), though adaptable for other uses.
-
Black: Standard for wastewater or industrial applications.
-
Red: Often used for fire protection systems or custom orders.
-
Other (e.g., Green): Per customer request, typically for specific project coding.
These colors are applied via coatings like fusion-bonded epoxy (FBE) or zinc-bitumen, enhancing corrosion resistance.
Joint Type: Flange Type
The flange type joint defines this fitting:
-
Double Flange: One standard flange connects to a pipe or fitting, while the duck foot flange anchors to a base (e.g., concrete pad or equipment). Both use bolts and gaskets (e.g., EPDM, NBR) for a leak-tight seal.
-
Design: Flanges conform to standards like ISO 7005 or AWWA C110, with bolt holes (4-12, depending on size) for secure fastening.
This rigid connection excels in high-pressure or stable setups, though it lacks the flexibility of push-on joints.
Pressure Ratings
The bend supports multiple pressure classes:
-
PN10: 10 bar (145 psi), for low-pressure systems like gravity sewers.
-
PN16: 16 bar (232 psi), common in irrigation or moderate-pressure wastewater.
-
PN25: 25 bar (363 psi), for higher-pressure force mains.
-
PN40: 40 bar (580 psi), for industrial or high-pressure applications.
These ratings align with wall thickness and flange strength, ensuring safety under specified loads.
Pressure Class
|
Rating (Bar)
|
Typical Use
|
---|---|---|
PN10
|
10
|
Gravity sewers
|
PN16
|
16
|
Irrigation, mild pressure
|
PN25
|
25
|
Wastewater force mains
|
PN40
|
40
|
Industrial high-pressure
|
OEM Availability
OEM (Original Equipment Manufacturer) acceptable means the fitting can be customized:
-
Dimensions: Adjusted sizes or flange patterns.
-
Coatings/Linings: Specific materials per client needs.
-
Branding: Logos or markings for proprietary systems.
This flexibility supports tailored solutions for unique projects.
Fitting Types
The double flange 90° duck foot bend is part of a broader family of ductile iron fittings:
-
Socket Bend: Push-on joint for flexibility.
-
Flanged Bend: Standard 90° or other angles with two pipe flanges.
-
Socket and Flanged Tee: Combines socket and flange connections.
-
Flanged Socket: Transitions from flange to socket.
-
Socket Taper: Reduces diameter with push-on ends.
-
Blank Flanges: Caps or seals pipe ends.
-
Adapters/Couplings: Connects ductile iron to PVC or other materials.
-
Dismantling Joints: Allows easy removal of components.
-
PVC Fittings: Specialized for hybrid systems.
The duck foot bend stands out for its anchoring base, complementing these options in complex layouts.
Surface Treatment
Surface treatments enhance durability:
-
Fusion-Bonded Epoxy (FBE) Coating: Thick, uniform external layer for corrosion resistance.
-
Cement Lining Inside + Zinc and Bitumen Outside: Internal corrosion barrier (cement) with external galvanic protection (zinc) and moisture shield (bitumen).
-
Zinc + Bitumen Inside and Outside: Dual protection, less common but effective.
-
Custom Treatments: Per customer requirements (e.g., PU, epoxy-ceramic).
Treatment
|
Purpose
|
Application
|
---|---|---|
FBE Coating
|
Corrosion resistance
|
Aggressive soils
|
Cement + Zinc/Bitumen
|
Internal/external shield
|
Wastewater, water
|
Zinc + Bitumen (In/Out)
|
Dual corrosion
|
Mild conditions
|
Custom (e.g., PU)
|
Specific needs
|
Harsh environments
|
Inspection
Quality assurance includes:
-
Foundry In-House: Internal checks for defects (e.g., porosity, dimensional accuracy).
-
Third-Party Inspection: Available upon request, per standards like ISO 9001 or client specifications, ensuring impartial validation.
Tests include hydrostatic pressure, coating adhesion, and material composition analysis.
Applications
The fitting serves multiple systems:
-
Stormwater Systems: Redirects runoff from horizontal drains to vertical outlets, anchored in manholes.
-
Wastewater Systems: Supports risers in pump stations or transitions sewage flows, resisting chemical attack.
-
Irrigation Systems: Routes water from mains to vertical feeds, stabilized against soil movement.
System
|
Role
|
Benefit
|
---|---|---|
Stormwater
|
Vertical outlet
|
Load distribution
|
Wastewater
|
Riser anchoring
|
Corrosion resistance
|
Irrigation
|
Feed transition
|
Stability under pressure
|
Advantages
-
High Quality: Ductile iron and robust coatings ensure durability.
-
Customization: OEM options meet specific needs.
-
Stability: Duck foot base resists thrust and supports weight.
-
Versatility: Suits stormwater, wastewater, and irrigation.
-
Longevity: 50-100 years with proper treatment.
Package
-
Standard Wooden Pallets: DN50-DN300, stacked for stability.
-
Wooden Cases: DN350-DN2600, protecting larger fittings during transport.
Manufacturing Process
-
Melting: Iron melted at 2,500-2,800°F (1,370-1,540°C).
-
Magnesium Treatment: Adds ductility via nodules.
-
Casting: Poured into duck foot bend molds.
-
Annealing: Heat-treated for stress relief.
-
Machining: Flanges drilled and faced.
-
Finishing: Coated and lined per specs.
Design Nuances
The duck foot’s wide base—say, 300 mm across for a DN200 bend—spreads a 5-ton load from a vertical riser across a concrete pad, cutting stress by 50% versus a standard flange. In a PN25 wastewater force main, it holds firm against 363 psi surges, where a push-on joint might slip.
Application Examples
In a Florida stormwater system, a DN600 duck foot bend anchors a vertical outlet under a highway, its FBE coating shrugging off saline soil. In an Indian irrigation project, a DN150 blue bend feeds a vertical sprinkler line, its cement lining ensuring clean flow for 30 years.
Material Edge
Ductile iron’s nodules absorb seismic shocks—during a 2010 Chile quake, DN300 duck foot bends stayed intact while cast iron cracked. Its zinc-bitumen coating outlasts steel’s rust-prone life by decades.
Installation Insights
Bolting a DN400 bend to a pad takes 45 minutes—eight bolts torqued to 120 ft-lbs with an EPDM gasket seal it tight. In contrast, welding a steel bend risks burn-through and doubles labor time.
Economic Value
A DN200 bend at $100 outprices PVC at $60, but its 75-year life versus PVC’s 30 saves $200 in replacements over a century, per 100 meters.
The Double Flange 90° Duck Foot Ductile Iron Bend is a powerhouse fitting, blending directional change with structural stability. From its ductile iron core to its FBE coatings and customizable design, it excels in stormwater, wastewater, and irrigation systems, offering decades of reliable service.