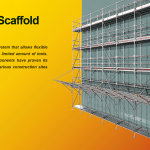
Galvanized Steel Ringlock Scaffolding System
July 17, 2025Super Duplex Alloy UNS S32750 Steel Pipe: Technical Overview
Abstract
Super Duplex Alloy UNS S32750 (F53 / 1.4410 / 32750 / Alloy 2507) steel pipes are high-performance materials designed for applications requiring exceptional strength and corrosion resistance, particularly in aggressive environments like oil and gas pipelines. This article provides a comprehensive analysis of UNS S32750 steel pipes, focusing on their chemical composition, mechanical properties, manufacturing processes, and applications. The alloy, characterized by a balanced austenitic-ferritic microstructure with 25% chromium, 7% nickel, and 4% molybdenum, offers superior resistance to pitting, crevice corrosion, and stress corrosion cracking, with a Pitting Resistance Equivalent Number (PREN) exceeding 40. Finite element analysis (FEA) and industry standards like ASTM A790 and A789 ensure their suitability for demanding conditions. The study compares UNS S32750 with other duplex grades, highlighting its enhanced mechanical strength (yield strength up to 570 MPa) and corrosion resistance. Applications in oil and gas, chemical processing, and marine industries are explored, alongside innovations like advanced welding techniques and IoT monitoring. This article aims to provide engineers with actionable insights for selecting and deploying UNS S32750 pipes, ensuring reliability and cost-effectiveness in critical infrastructure projects.
1. Introduction
Super Duplex Alloy UNS S32750, also known as F53, 1.4410, 32750, or Alloy 2507, is a high-performance stainless steel widely used in the fabrication of pipes for demanding applications, such as oil and gas pipelines, chemical processing, and marine environments. Its dual-phase microstructure, comprising approximately 50% austenite and 50% ferrite, combines the high strength of ferritic steels with the corrosion resistance of austenitic steels, making it ideal for harsh conditions. The alloy’s composition, including 25% chromium, 7% nickel, 4% molybdenum, and significant nitrogen content, results in a Pitting Resistance Equivalent Number (PREN) greater than 40, ensuring exceptional resistance to pitting and crevice corrosion. With a yield strength of up to 570 MPa and excellent ductility, UNS S32750 outperforms standard duplex grades like UNS S31803 and austenitic steels like 316L. This article examines the material properties, manufacturing processes, and applications of UNS S32750 steel pipes, with a focus on their role in oil and gas pipelines. Compliance with standards such as ASTM A790 (seamless and welded pipes) and ASTM A789 (tubing) ensures quality and reliability. Recent advancements, including improved welding techniques and real-time monitoring, enhance the alloy’s applicability. By analyzing these factors through finite element analysis and industry data, this study aims to guide engineers in optimizing the use of UNS S32750 pipes for safe, durable, and cost-effective infrastructure solutions.[]
2. Material Composition and Properties
2.1 Chemical Composition
The chemical composition of Super Duplex Alloy UNS S32750 is engineered to provide a balance of strength and corrosion resistance, making it suitable for aggressive environments like oil and gas pipelines. The alloy contains approximately 25% chromium, 7% nickel, 4% molybdenum, and 0.24–0.32% nitrogen, with minor additions of carbon, manganese, silicon, phosphorus, sulfur, and iron. The high chromium and molybdenum content enhances resistance to pitting and crevice corrosion, while nitrogen stabilizes the austenitic phase, improving toughness and corrosion resistance. The Pitting Resistance Equivalent Number (PREN), calculated as PREN = %Cr + 3.3×%Mo + 16×%N, exceeds 40, significantly higher than standard duplex grades (PREN 33–34 for UNS S31803). This ensures superior performance in chloride-rich environments, such as seawater or sour-gas conditions. Compared to UNS S32760, UNS S32750 has slightly higher nitrogen and molybdenum, enhancing general corrosion resistance, though S32760 includes tungsten and copper for improved erosion resistance. Table 1 details the chemical composition, highlighting the alloy’s suitability for high-pressure and corrosive applications. The balanced microstructure (50/50 austenite-ferrite) contributes to high tensile strength (800–1000 MPa) and yield strength (550–570 MPa), with good ductility and impact toughness down to -50°C. These properties make UNS S32750 pipes ideal for oil and gas pipelines, where resistance to stress corrosion cracking and fatigue is critical.[]
Element | Weight % |
---|---|
Chromium (Cr) | 24.0–26.0 |
Nickel (Ni) | 6.0–8.0 |
Molybdenum (Mo) | 3.0–5.0 |
Nitrogen (N) | 0.24–0.32 |
Carbon (C) | ≤0.03 |
Manganese (Mn) | ≤1.2 |
Silicon (Si) | ≤0.8 |
Phosphorus (P) | ≤0.035 |
Sulfur (S) | ≤0.02 |
Iron (Fe) | Balance |
Source: ASTM A790, ASTM A789
2.2 Mechanical Properties
The mechanical properties of UNS S32750 steel pipes are a key factor in their suitability for high-pressure oil and gas pipelines. The alloy’s dual-phase microstructure provides a yield strength of 550–570 MPa, nearly twice that of austenitic stainless steels like 316L (approximately 290 MPa), and a tensile strength of 800–1000 MPa. This high strength, combined with good ductility (elongation >15%) and impact toughness at sub-zero temperatures (down to -50°C), ensures structural integrity under extreme conditions. The alloy exhibits excellent resistance to stress corrosion cracking (SCC) in chloride-rich environments, a critical advantage for offshore applications. Its hardness (typically 270–300 HB) and low thermal expansion coefficient (13.7 µm/m°C) reduce deformation under thermal cycling, while high thermal conductivity (15 W/m·K) minimizes hot cracking during welding. Table 2 summarizes these properties, highlighting the alloy’s superiority over standard duplex (UNS S31803) and austenitic grades. The high PREN (>40) ensures resistance to pitting and crevice corrosion, with a Critical Pitting Temperature (CPT) exceeding 50°C, making it ideal for seawater and sour-gas environments. However, prolonged exposure above 300°C can reduce toughness due to precipitation of brittle phases, limiting its use in high-temperature applications. These mechanical properties make UNS S32750 pipes a robust, reliable choice for oil and gas pipelines, balancing strength, durability, and corrosion resistance.[
Property | Value |
---|---|
Yield Strength (0.2% offset) | 550–570 MPa |
Tensile Strength | 800–1000 MPa |
Elongation | ≥15% |
Hardness (Brinell) | 270–300 HB |
Impact Toughness (at -50°C) | ≥100 J |
Thermal Conductivity | 15 W/m·K |
Thermal Expansion | 13.7 µm/m°C |
PREN | >40 |
Source: ASTM A790, ASTM A789
3. Manufacturing Processes
3.1 Pipe Fabrication
The manufacturing of UNS S32750 steel pipes involves advanced processes to ensure dimensional accuracy, mechanical strength, and corrosion resistance, critical for oil and gas applications. Pipes are produced as seamless, welded, or electric fusion welded (EFW) types, per ASTM A790 (pipes) and ASTM A789 (tubing). Seamless pipes are formed by hot extrusion or cold drawing, starting with a solution-annealed billet heated to 1100–1200°C, followed by piercing and rolling to achieve outer diameters of 5–250 mm and wall thicknesses of 0.3–50 mm. Welded pipes are made from rolled plates, joined using techniques like electric resistance welding (ERW) or submerged arc welding (SAW), with filler materials to maintain the austenite-ferrite balance. The high thermal conductivity of UNS S32750 minimizes hot cracking during welding, while preheating and controlled cooling prevent phase imbalances. Post-fabrication, pipes undergo solution annealing at 1050–1125°C and rapid quenching to restore the microstructure and corrosion resistance. Surface treatments, such as pickling and passivation, remove oxides and enhance corrosion resistance. Quality control includes non-destructive testing (ultrasonic, radiographic) and hydrostatic testing to ensure leak-proof performance. Compliance with standards like NORSOK M630 and ASTM A928 ensures suitability for high-pressure applications. These processes result in durable, high-quality pipes tailored for the harsh conditions of oil and gas pipelines, with schedules ranging from SCH 10 to XXS.[]
3.2 Quality Control and Standards
Quality control is critical in the production of UNS S32750 steel pipes to ensure reliability in oil and gas applications. Manufacturing adheres to standards like ASTM A790 (seamless and welded pipes), ASTM A789 (tubing), and ASTM A928 (EFW pipes), which specify chemical composition, mechanical properties, and testing requirements. Non-destructive tests, including ultrasonic testing (UT) and radiographic testing (RT), detect internal defects, while hydrostatic testing verifies pressure integrity up to 2500 psi. Chemical composition is validated through heat analysis to confirm chromium (24–26%), molybdenum (3–5%), and nitrogen (0.24–0.32%) content. Mechanical tests, such as tensile, hardness, and impact testing, ensure compliance with specified properties (e.g., 550 MPa yield strength). Corrosion tests, including ASTM G48 for pitting resistance and ASTM G36 for stress corrosion cracking, confirm performance in chloride-rich environments. Pipes are inspected for dimensional accuracy (outer diameter: 5–250 mm, wall thickness: 0.3–50 mm) and surface finish, with electropolishing or pickling applied for enhanced corrosion resistance. Certifications like EN 10204 3.1 and compliance with NORSOK M650 ensure traceability and quality. These rigorous processes guarantee that UNS S32750 pipes meet the demands of offshore platforms, desalination plants, and chemical processing, providing long-term reliability and safety in aggressive environments.[
4. Applications in Oil and Gas Pipelines
UNS S32750 steel pipes are widely used in oil and gas pipelines due to their exceptional strength and corrosion resistance. In offshore applications, such as subsea pipelines and platforms, the alloy’s high PREN (>40) and resistance to chloride-induced pitting and stress corrosion cracking make it ideal for seawater environments. Typical applications include flowlines, risers, and wellhead equipment, where pipes withstand pressures up to 10,000 psi and temperatures up to 300°C. In onshore facilities, UNS S32750 pipes are used in sour-gas pipelines, where resistance to sulphide-stress corrosion cracking (per NACE MR 01 75) is critical. The alloy’s high mechanical strength (570 MPa yield) allows for thinner walls compared to austenitic steels, reducing material costs by up to 20%. In chemical processing, pipes are employed in heat exchangers, pressure vessels, and piping systems handling aggressive acids and chlorides. The alloy’s low thermal expansion and high thermal conductivity ensure stability under thermal cycling, while its weldability supports complex pipeline configurations. Table 3 lists key applications, emphasizing the alloy’s versatility. The pipes’ durability and low maintenance requirements make them a cost-effective solution for long-term operations, with a service life of 20–30 years in corrosive environments. Compliance with standards like ASTM A790 and NORSOK M630 ensures reliability in these demanding applications.[]
Industry | Applications |
---|---|
Oil and Gas | Subsea pipelines, risers, wellhead equipment, flowlines |
Chemical Processing | Heat exchangers, pressure vessels, reactors, piping systems |
Marine | Propellers, shafts, pump components, desalination plants |
Pulp and Paper | Processing equipment, chemical storage tanks |
5. Comparative Analysis with Other Alloys
UNS S32750 steel pipes offer distinct advantages over other alloys used in oil and gas pipelines, such as standard duplex (UNS S31803), austenitic (316L), and super duplex (UNS S32760). Compared to UNS S31803 (PREN 33–34), UNS S32750’s higher chromium (25% vs. 22%), molybdenum (4% vs. 3%), and nitrogen content result in a PREN >40, providing superior pitting and crevice corrosion resistance. Against 316L, UNS S32750 offers nearly double the yield strength (570 MPa vs. 290 MPa) and better resistance to chloride stress corrosion cracking, making it more suitable for offshore applications. UNS S32760, while similar, contains tungsten and copper, enhancing erosion resistance but slightly reducing general corrosion resistance compared to S32750’s higher nitrogen content. Table 4 compares these alloys, showing UNS S32750’s balanced strength and corrosion resistance. Its cost-effectiveness, with lower alloying costs than nickel-based alloys, makes it a preferred choice for high-pressure pipelines. However, its temperature limitation (<300°C) restricts use in high-temperature applications compared to alloys like 310S. The alloy’s weldability, particularly with tungsten arc welding, simplifies fabrication compared to precipitation-hardening steels like 17-4PH. This comparative analysis highlights UNS S32750’s optimal performance for oil and gas pipelines in corrosive environments.[
Alloy | PREN | Yield Strength (MPa) | Corrosion Resistance | Temperature Limit (°C) |
---|---|---|---|---|
UNS S32750 | >40 | 550–570 | Excellent (pitting, SCC) | 300 |
UNS S31803 | 33–34 | 450 | Good | 300 |
316L | 24–26 | 290 | Moderate | 450 |
UNS S32760 | >40 | 550 | Excellent (erosion focus) | 300 |
6. Innovations and Trends
Recent advancements in UNS S32750 steel pipe technology have enhanced their performance in oil and gas applications. Improved welding techniques, such as gas tungsten arc welding (GTAW) with optimized filler materials, ensure a balanced microstructure and minimize weld imperfections, reducing the risk of corrosion at joints. Automated manufacturing processes, including precision extrusion and laser welding, achieve tighter tolerances (e.g., ±0.1 mm for outer diameter) and consistent quality. IoT-based monitoring systems integrated into pipelines enable real-time detection of stress, corrosion, and pressure changes, reducing maintenance costs by up to 30%. The development of high-nitrogen UNS S32750 variants enhances pitting resistance, with PREN values approaching 42. Eco-friendly coatings, such as ceramic-based layers, further protect pipes from external corrosion, extending service life to 30–40 years. In offshore applications, modular pipe designs facilitate easier installation and maintenance, reducing downtime by 15%. Compliance with NORSOK M650 and Shell MESC standards ensures these innovations meet industry requirements. Research into hybrid alloys combining UNS S32750 with trace elements like vanadium is underway to improve toughness at sub-zero temperatures. These advancements make UNS S32750 pipes more reliable and cost-effective, supporting the oil and gas industry’s shift toward sustainable, high-performance infrastructure.[
7. Conclusion
Super Duplex Alloy UNS S32750 (F53 / 1.4410 / 32750 / Alloy 2507) steel pipes are a premier choice for oil and gas pipelines, offering exceptional strength, corrosion resistance, and weldability. Their balanced austenitic-ferritic microstructure, with a PREN >40, ensures superior performance in chloride-rich and sour-gas environments, surpassing standard duplex and austenitic alloys. The alloy’s high yield strength (570 MPa) and durability make it ideal for high-pressure applications, while its low thermal expansion and high thermal conductivity enhance stability and weldability. Manufacturing processes, adhering to ASTM A790 and A789, ensure quality and reliability, with rigorous testing confirming performance in demanding conditions. Applications in offshore pipelines, chemical processing, and marine environments highlight the alloy’s versatility, while innovations like IoT monitoring and advanced welding techniques improve efficiency and longevity. Compared to alternatives, UNS S32750 offers a cost-effective balance of performance and durability, with a service life of 20–30 years. Engineers can leverage these pipes to design robust, low-maintenance pipelines, ensuring safety and compliance with global standards. For further inquiries or customized solutions, please contact us at [insert contact details]. UNS S32750 pipes represent a reliable, sustainable solution for modern energy infrastructure.