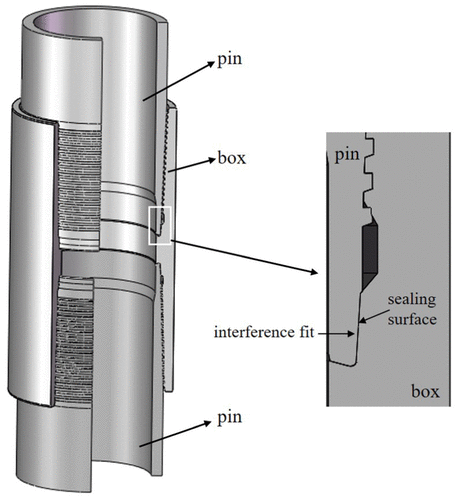
Casing pipe application in high-temperature gas wells
January 4, 2019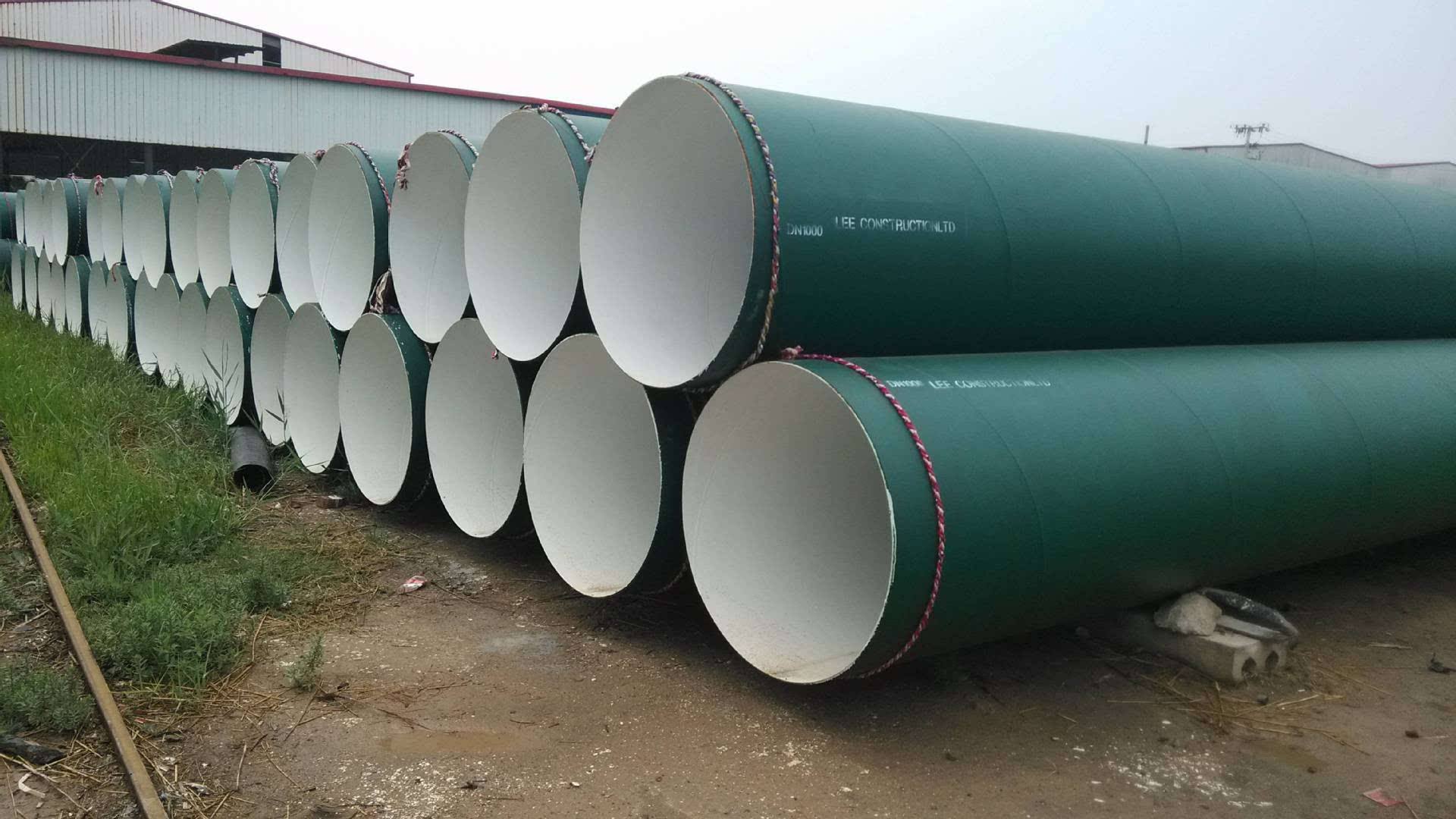
How is the theoretical weight of spiral steel pipe calculated?
January 8, 2019ABSTRACT
The corrosion resistances of enamel-coated steel pipe in 3.5 wt% NaCl solution was evaluated and compared with those of epoxy-coated pipe using open-circuit potential, linear po- larization resistance, and electrochemical impedance spectros- copy tests. T-001c enamel slurry and GP2118 enamel powder were sprayed to steel pipe in wet and electrostatic processes, respectively. The phase composition and microstructures of the two enamels were characterized with x-ray diffraction and scanning electron microscopy (SEM). The surface roughness of enamels and their bond strength with steel substrates were quantified to understand coating quality. SEM images revealed that both types of enamel coatings have a solid structure with isolated bubbles. Electrochemical tests showed a high corrosion resistance of the enamel coatings as verified in visual inspection on the tested samples. In particular, the GP2118 enamel-coated samples consistently outperformed the epoxy-coated samples.
KEY WORDS: corrosion, electrochemical impedance spectroscopy, enamel coating, pipeline steel, scanning electron microscopy
INTRODUCTION
Natural gas, oil, and hazardous liquid transmission and gathering pipelines have reached 484,000 miles in the U.S.1 Aging pipelines are faced with reduced
service life and reliability as a result of corrosion. They can be protected from corrosion by protective coating, cathodic protection, and use of corrosion inhibitors. Coating as a physical barrier to electrolyte penetra- tion is one of the most effective and efficient methods in corrosion mitigation.
When internally applied to steel pipelines, coat- ing has several advantages. First, the internal coating can prevent fluid or gas from interacting and reacting with underlying steel. Second, coated steel pipe reduces microbiological deposits and bacteria biofilm forma- tions because the higher surface roughness of uncoated pipe helps shield the bacteria and provide growth conditions for bacterial colonies.2 Third and last, the
internal coating can reduce pressure drop over a long distance of a pipeline and thus power required to transmit oil and gas. The pressure drop in coated pipe was experimentally demonstrated to be 35% lower than that in bare steel pipe at a Reynolds number of
1 × 107.3
Today, two-part solvent based epoxy coatings, solvent free and fusion bonded coatings, and polyamide coatings are widely used in crude oil and natural gas pipelines.4-6 These coatings are weakly bonded with
their steel substrate and thus prone to under-film corrosion.7
Porcelain enamel, as an inorganic material, is chemically bonded to substrate metals at a temperature of 750°C to ∼850°C. It can not only be finished with a smooth and aesthetical surface, but also provide ex- cellent chemical stability, good corrosion resistance, and durability in various harsh environments.8 Unlike
epoxy coating, enamel coating has no under-film corrosion when locally breached because of its chemical bond with metal substrates.9 It has been widely used for household cooking utensil protection or steel container protection in industries. Its corrosion re- sistance as a protective coating for steel reinforcement in concrete structures has been investigated in pre- vious studies and demonstrated to be satisfactory in general.10-11
In this study, the corrosion behavior of steel pipe internally coated with two types of enamel (T-001 slurry and GP2118 powder) was examined in 3.5 wt% NaCl solution. The phase composition and microstructure of enamels were characterized with x-ray diffraction
(XRD) and scanning electron microscopy (SEM), respectively. The surface roughness of enamel coating and its bond strength over steel pipe substrates were determined. The electrochemical behaviors were studied with open-circuit potential (OCP), linear polar- ization resistance (LPR), and electrochemical imped- ance spectroscopy (EIS) tests. Visual inspections were made on tested samples for any obvious signs of corrosion. The corrosion resistance of enamel-coated steel is compared with that of epoxy-coated steel.
EXPERIMENTAL PROCEDURES
Enameling and Specimens
An API 5L X65 steel pipe (MRC Global) with 323.85 mm in outer diameter and 9.53 mm in wall thickness was used as substrate metal in this study. The chemical composition of the steel provided by the vendor is presented in Table 1. The steel pipe was first cut into 18 25 mm × 50 mm coupon specimens. The cut specimens were then steel blasted for 1 min to get rid of mill scale and rusts, and finally cleansed with
a commercially available cleansing solvent.
Two types of enamel were applied on the steel coupons: T-001 slurry and GP2118 powder. The chemical compositions of T-001 glass frits and GP2118 enamel powder were determined by x-ray fluorescence (XRF) as presented in Table 2. The enamel slurry was prepared by first milling glass frits, clay, and certain electrolytes, and then mixing them with water until the mixture was in a stable suspension state. The enamel slurry was manually sprayed on coupon specimens using a spray gun, which was powered by a jet of compressed air as specified in Table 3. The specimens were heated at 150°C for 10 min to drive off moisture, fired at 815°C for 10 min, and finally cooled to room temperature. For electrostatic spraying, the GP2118 enamel powder with an average particle size of 32.8 μm was used. An electric field was formed between a nozzle electrode and the sample. Enamel particles, propelled out of the spray gun by a stream of air, became negatively charged, migrated toward the sample (positive electrode) and were de- posited. After power spraying, the steel coupons were moved into a furnace and fired at 843°C for 10 min, and then moved out and cooled to room temperature. The thickness of the T-001 coating was controlled by the spraying time, while the thickness of the GP2118 coating was controlled by the number of spray guns. For comparison, epoxy-coated steel samples were pre- pared and tested. In this case, 3M Scotchkote 323† epoxy, which was applied in pipeline industry, was used to coat the samples. Steel coupons were coated by brushing epoxy at room temperature and then dried in air for 3 d prior to electrochemical tests.
Characterization of Enamel Coatings
The coating thickness and roughness were measured with a coating thickness gauge MiniTest 6008† and optical microscope Hirox†, respectively.
The bond strength between the coating and its substrate steel were determined using PosiTest† following ASTM D4541-09.12 To enhance its bond with the coating, a 20 mm diameter dolly at the base was roughened with abrasive papers, and cleansed with alcohol to remove oxidation and contaminants. The base of the dolly was adhered with a uniform layer of glue to the test coating surface. After curing for 24 h, the coating around the dolly was removed using a 20 mm cutting tool in order to isolate the dolly on a specific test area. The dolly was finally pulled off the sample surface perpendicularly at a stress rate of 0.4 MPa/s. The maximum strength of each coated sample was recorded.
At the completion of corrosion tests, the phases in coating were examined directly on the surface of coated steel samples by XRD (Philip X’Pert†) with diffraction angle (2θ) varied between 10° and 55°. Cross sections of the enamel-coated samples were prepared for microstructure analysis with SEM (Hitachi S4700†). Each enamel-coated sample was first cold mounted in epoxy resin (EpoxyMount†, Allied High Tech Products, Inc.) and cut into a 10 mm thick cross section using a diamond saw. Then, the cross section was abraded with carbide papers to 1200 grit, rinsed with deionized water, and finally dried in air at room temperature prior to examination. SEM images were analyzed with ImageJ† software for porosity evaluation.
Electrochemical Tests
Each sample was soldered with a copper wire for electrochemical measurements as illustrated in Figure 1. All sides of the sample except the enamel- or epoxy-coated face were covered with Marine epoxy.
The exposed enamel or epoxy area was 30 mm × 20 mm in size.
All samples were immersed in 3.5 wt% NaCl solution with the pH of 7 and tested at room tempera- ture for 69 d. The solution was prepared by adding purified sodium chloride (Fisher Scientific, Inc.) into distilled water.
At the time of 1, 3, 6, 13, 27, 41, 55, and 69 d, OCP, LPR, and EIS tests were performed to monitor the corrosion evolution of the enamel- and epoxy-coated steel samples. A standard three-electrode system was used for electrochemical tests, including a 25.4 mm × 25.4 mm × 0.254 mm platinum sheet as a counter electrode, saturated calomel electrode (SCE) as a reference electrode, and the coated sample as a working electrode. All three electrodes were connected to a Gamry 1000E Potentiostat/Galvanostat† for data acquisition.
After each stable OCP (lasting for 1 h) was recorded, an EIS test was performed with a sinusoidal potential wave of 10 mV in amplitude around the OCP and a frequency of 100 kHz to 5 mHz. The LPR test was conducted by scanning a range of ±15 mV around the OCP at a scan rate of 0.167 mV/s. The LPR curves are used to determine the polarization resistance Rp, which is equal to the slope of the linear region of a polarization curve around zero current:13
Rp =ΔE=Δi
where ΔE and Δi represent the voltage and current increments, respectively, in the linear portion of a polarization curve at i = 0. LPR measurements were used to calculate the corrosion current density by the Stern-Geary equation:13
icorr =βaβc=½2.303ðβa + βcÞRp (2)
where βa and βc represent the anodic Tafel constant (0.12) and the cathodic Tafel constant (0.12), respectively, and icorr is the corrosion current.
RESULTS AND DISCUSSION
Coating Characterization
Phases in Enamel — XRD patterns on the surface of GP2118 and T-001 enamel-coated samples after immersion in 3.5 wt% NaCl solution for 69 d are identified and displayed in Figure 2. Quartz SiO2 is present in both types of enamel coatings. The highest intensity peaks of quartz SiO2 were at 26° and 26.5° for GP2118 and T-001 enamels, respectively.
Microstructure at Enamel/Substrate Interface — Cross-sectional SEM images at the steel/coating interface with different magnifications are presented in Figure 3. The enamel coatings have a solid structure with disconnected air bubbles through the coating thickness (Figures 3[a1] and [b1]). The air bubbles were formed during the high-temperature chemical
reaction of the enamel glass frit with the steel during firing process.14-15 The enamel coatings have numerous
isolated small pores with the exception of GP2118 enamel that has a few large pores with a diameter of approximately 105 μm. The porosity content of T-001 enamel was measured to be 4.26%, which is lower than 12.72% for the GP2118 enamel. Figures 3(a2) and (b2) show the magnified enamel/steel interfaces at which small-Fe protrusions grow into the enamel coating to form various anchor points. These epitaxial spinel particles improve the bonding between the enamel and its steel substrate.16
Pull-Off Strength — The measured thickness, surface roughness, and bond strength of three types of coatings are summarized in Table 4. The average and the standard deviation of the thickness and surface roughness of each coating were calculated from
27 measurements taken from three different samples that were polished to have a flat surface for the pull-off test. The average and the standard deviation of the bond strength of each coating were calculated from the three pull-off tests conducted. It can be seen from Table 4 that epoxy coating is the thickest (396 μm) and T-001 enamel is the thinnest (230 μm). The
roughness of the three coatings is around 1 μm, indicating smooth surfaces in all specimens.
At the completion of pull-off tests, the dolly and substrate fracture surfaces are shown in Figure 4. In a pull-off bond test, four possible failure modes include: (1) adhesion break between the coating and its steel substrate, (2) cohesion break within the coating layer, (3) glue break, and (4) mixed break or a combi- nation of the above breaks at multiple locations.17
Enamel coatings have a mixed failure mode in- volving a break inside the coating (cohesive break) and a break in glue used to bond the dolly to the specimen. Epoxy coating also has a mixed failure mode involving a break inside the coating (cohesive break), a break between the coating and the substrate steel (adhesive break), and a glue break. There are no adhesive breaks for enamel coatings because the anchor points on the interface increase the bonding between an enamel coating and its substrate steel as shown in Figure 3. Specifically, GP2118 enamel coating has the highest bond strength with an average value of 17.89 MPa, epoxy coating has the lowest bond strength of 8.01 MPa, and T-001 enamel coating has a bond strength of 16.85 MPa.
Figures 5(a) and (b) represent the magnified fracture surface morphologies as shown in Figures 4(a2) and (b2), respectively. When the dolly was pulled off the coated specimen at right angle, a crack initiated and ProPaGaTEd acroSS larGE aIr bubblES wIThIn ThE coaT- InG undEr IncrEaSInG loadS. FIGurES 6(a) and (b) Show SEM IMaGES For ThE croSS SEcTIonS oF ThE TESTEd SPE- cIMEnS In rEcTanGular arEaS oF FIGurES 4(a2) and (b2), rESPEcTIvEly. ThE FracTurE SurFacES oF ThE SPEcIMEnS arE GEnErally SMooTh wITh ThE MInIMuM rEMaInEd coaTInG ThIcknESSES oF aPProxIMaTEly 70 μM and
40 μM For GP2118 and T-001 EnaMElS, rESPEcTIvEly. In coMParISon wITh FIGurE 3, FIGurES 6(a) and (b) IndIcaTE ThaT ThE FracTurE SurFacES arE Far away FroM ThEIr corrESPondInG bondInG layErS aT ThE EnaMEl/ SubSTraTE InTErFacES and PaSS ThrouGh ThE wEakEST layEr connEcTInG larGE aIr bubblES In ThE coaTInG bEcauSE ThE adhErEncE oF EnaMEl on STEEl SurFacES IS chEMIcally STrEnGThEnEd wITh ThE GrowTh oF EPITaxIal SPInEl ParTIclES In ThE EnaMEl durInG chEMIcal rEacTIon In ThE firInG ProcESS.16