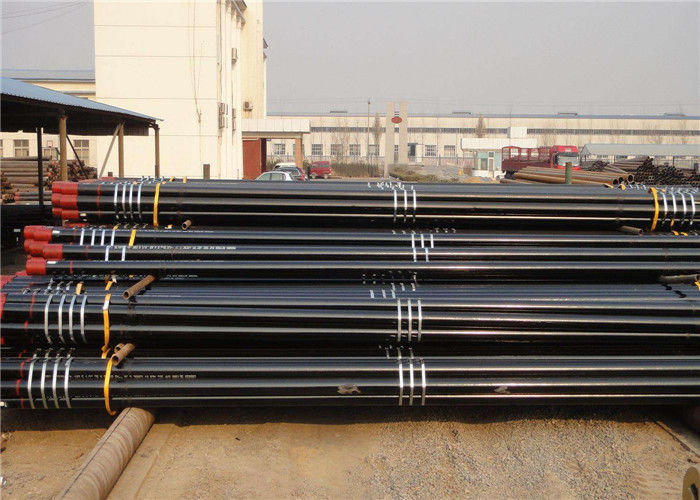
How is seamless steel pipe produced?
October 28, 2018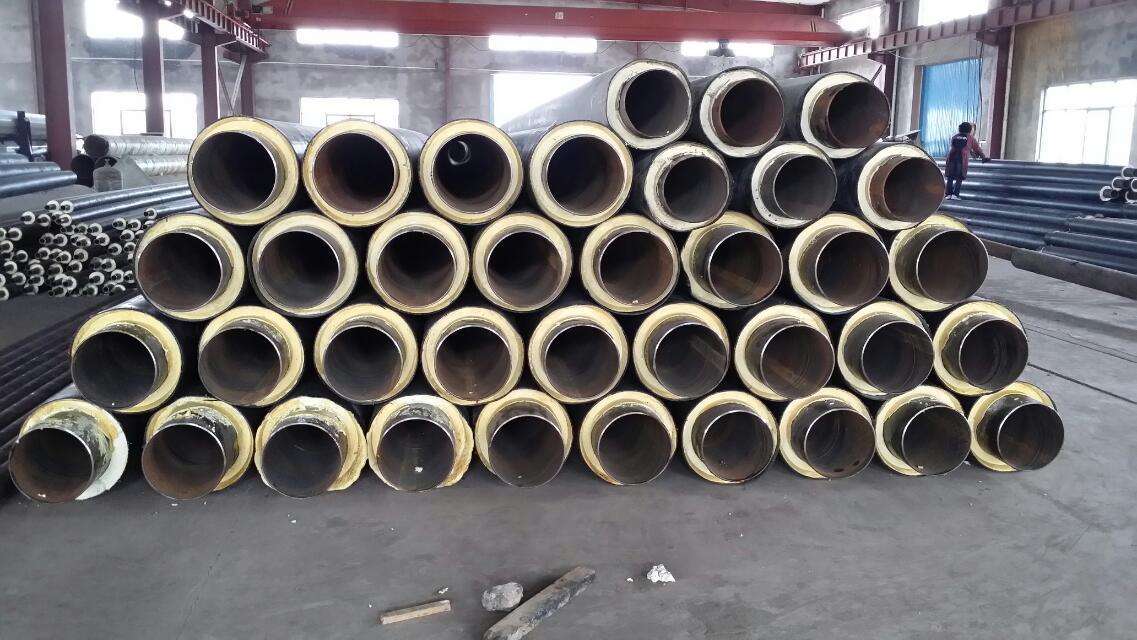
Polyurethane insulation steel pipe
November 5, 2018Flanges are disc-shaped parts that are most common in plumbing and flanges are used in pairs. In plumbing, flanges are mainly used for the connection of steel pipes. In the pipelines that need to be connected, a variety of flanges are installed, and the low-pressure pipelines can use wire-bonded flanges, and the welding flanges are used at pressures above 4 kg. A sealing point is added between the two flanges and then fastened with bolts. Different pressure flanges have different thicknesses and use different bolts.
Pumps and valves, when connected to the pipeline, part of these equipment, also made into the corresponding flange shape, also known as flange connection. Connection parts that are closed at the same time by bolting on both planes are generally referred to as “flanges”. For example, the connection of ventilation ducts may be referred to as “flange parts”.However, this connection is only a part of the equipment, such as the connection between the flange and the water pump, it is not good to call the pump “flange parts”. Smaller such as valves, etc., can be called “flange parts”.
Flange flange connections are an important connection for pipeline construction.
Flange connection is to fix two pipes, pipe fittings or equipment on a flange, and between the two flanges, with flange mats, bolted together to complete the connection. Some fittings and equipment have their own flanges and are also flanged.
Flange threaded connection (wire connection) flange and welded flange. Low-pressure small-diameter wire-bonded flanges, high-pressure and low-pressure large diameters are all welded flanges. The thickness of the flanges of different pressures and the diameter and number of connecting bolts are different.
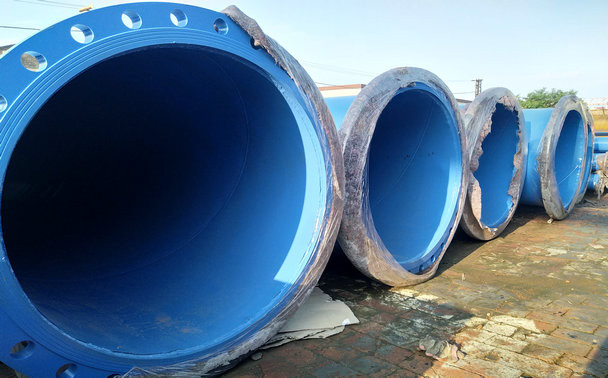
Depending on the level of pressure, the flange pads are also available in different materials, from low pressure asbestos pads, high pressure asbestos pads to metal pads.
Pipe connection, heat treatment and non-destructive testing pipe section connection pipe can be directly connected in the following ways: (1) Butt welding between pipes or between pipe and valve box or other accessories, butt welding should be full penetration type, and the root quality is Special regulations, or full penetration type, but no special provisions for root quality; (2) Sleeve welded joints, sleeve welding shall be carried out according to recognized standards, with appropriate size sleeves and related welding processes; (3) Approved type Threaded sleeve connection. The scope of use of the above pipe connection method is as follows: (1) Butt weld connection and sleeve weld connection shall comply with the requirements of Table 2.5.1.2(1). The connection mode between the pump and the pipe system is applicable to the pipe system. The outer diameter is taken to improve the quality of the weld root. The butt welding I, II, III does not adopt the butt welding of the root quality of the weld. II, III However, toxic media or pipes that are expected to cause fatigue and severe corrosion during work are excluded D ≤ 88.9 mm