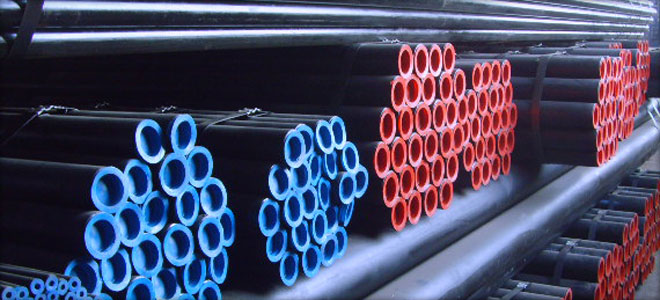
ASTM A106 seamless carbon steel pipes VS ASTM 53 High-Temperature Pipe
September 8, 2017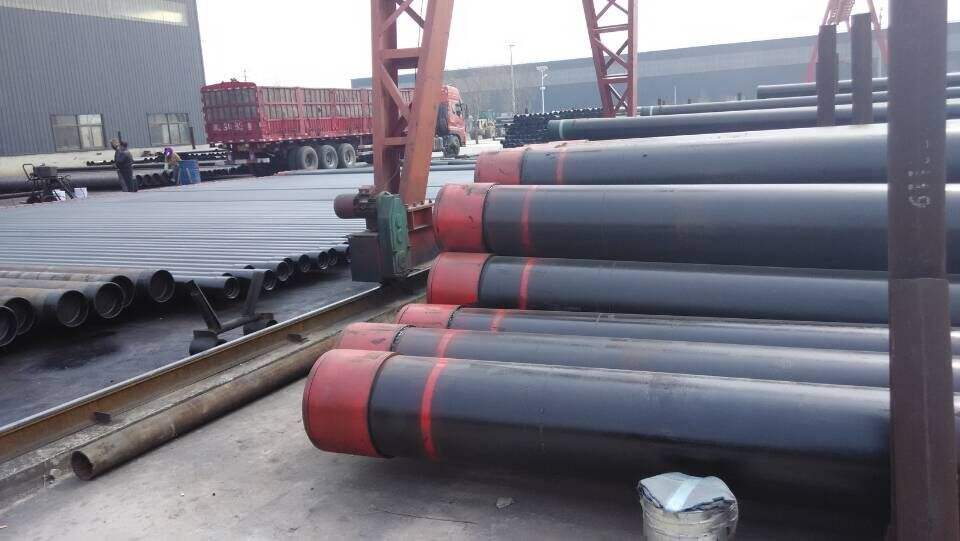
L-80 AND N-80 CASING PIPE – MINIMUM COLLAPSE RESISTANCE OF CASING – UNDER AXIAL LOAD
September 22, 2017Table C.61—Summary of NDE methods for seamless and the body of welded pipe
Grade |
Visual inspection (see 10.14) |
Wall thickness determination |
Ultrasonic inspection |
Flux leakage inspection | Eddy current inspection | Magnetic particle inspection a |
1 | 2 | 3 | 4 | 5 | 6 | 7 |
H40, J55 K55, N80 Type 1 | R | N | N | N | N’ | N |
N80Q, L80 C95, M65 | R | R | A | A | A | A |
P110 | R | R | A | A | A | NA |
C90, T95, Q125 | R | R | C | B | B | B |
N = not required R = required A = one method or any combination of methods shall be used B = at least one method shall be used in addition to ultrasonic inspection to inspect the outside surface C = ultrasonic inspection shall be used to inspect the outside and inside surfaces NA = not applicable |
||||||
a MPI is permitted for end-area inspection. MPI is permitted for pipe body outside-surface inspection in combination with other methods of pipe body inspection. ‘ |
Table C.62—Acceptance (inspection) levels
Grade | External imperfection | Internal imperfection | |||
Longitudinal | Transverse | Longitudinal | Transverse | ||
1 | 2 | 3 | 4 | 5 | |
N80Q, M65, L80, C95 | L4 | 一 | L4 | — | |
P110to A.9 (SR16) | L4 | L4 | L4 | L4 | |
P110 | L2 | L2 | L2 | L2 | |
P110 to A.9 (SR16) and A.2 (SR2) | L2 | L2 | L2 | L2 | |
C90 | UT | L2 | L2 | L2 | L2 |
T95-Q125 | 2nd method | L2 | L2 | — | — |
Weld seam | |||||
P110, Q125 | L2 | N | L2 | N | |
All other grades | L3 | N | L3 | N | |
N = not required; Lx = acceptance (inspection) level. |
Table C.63一Artificial reference indicators
Acceptance | Notch depth a | Notch length | Width | Radially drilled hole |
(inspection) level | max. at full depth | diameterb | ||
max. | max. | |||
% | mm | mm | mm | |
1 | 2 | 3 | 4 | 5 |
L2 | 5 | 50 | 1 | 1,6 |
L3 | 10 | 50 | 1 | 3,2 |
L4 | 12,5 | 50 | 1 | 3,2 |
a Depth as a percent of specified wall thickness. The depth tolerance shall be 士 15 % of the calculated notch depth with a minimum
notch depth of 0,3 mm ± 0,05 mm.
b Drilled hole diameter (through the pipe wall) shall be based on the drill bit size.
Table C.64—Size of stamp markings
Product | Label 1 | Marking height |
mm | ||
Pipe | <4-1/2 | 4,8 |
>4-1/2 | 6,4 | |
Coupling | Pipe sizes < 4-1/2 | 6,4 |
Pipe sizes > 4-1/2 to < 7-5/8 | 9,5 | |
Pipe sizes > 7-5/8 | 12,7 |
Table C.65一Grade colour codes
Grade | Number and colour of bands for pipe and pup-joints & 1,8 m | Colour(s) for coupling | ||
Tvpe | Entire coupling | Bandfs) | ||
1 | 2 | 3 | 4 | 5 |
H40 | None or black band at the manufacturer’s ootion | None | Same as for oiDe | |
J55 tubing |
One bright green | Bright green | None | |
J55 casing |
One bright green | Bright green | One white | |
K55 | Two briqht areen | Briaht areen | None | |
M65 | One bright qreen, one blue | M65 pipe uses L80 Type 1 couplings | ||
N80 | 1 | One red | Red | None |
N80 | Q | One red, one briqht qreen | Red | Green |
L80 | 1 | One red, one brown | Red | One brown |
L80 | 9Cr | One red, one brown, two vellow | Red | Two vellow |
L80 | 13Cr | One red, one brown, one vellow | Red | One vellow |
C90 | 1 | One purple | Purple | None |
C90 | 2 | One purple, one vellow | Purple | One vellow |
T95 | 1 | One silver | Silver | None |
T95 | 2 | One silver, one vellow | Silver | One vellow |
C95 | One brown | Brown | None | |
P110 | One white | White | None | |
Q125 | 1 | One oranqe | Oranqe | None |
Q125 | 2 | One oranqe, one vellow | Oranqe | One vellow |
Q125 | 3 | One oranae, one areen | Oranae | One areen |
Q125 | 4 | One oranae, one brown | Oranqe | One brown |
Table C.66—Thread type markings
Product | Thread type | Marked symbol |
Casing | Short round | STC |
Long round | LC | |
Buttress | BC | |
Extreme-line | XC | |
Tubing | Non-upset | NU |
External upset | EU | |
Integral joint | IJ |
3 Comments
Schedule 80 pipe comparied to 40?
A previous description of pipe wall thicknesses as “Standard”, “Extra Strong” and “Double Extra Strong” has been supplanted by a schedule of 10, 20, 30, 40 60, 80, 100, 120 and 160. Schedule 40 pipe generally compares with the previous use of “Standard”. For metal pipe, Schedule 80 pipe has a thicker wall and can withstand greater pressures than a Sch 40 pipe. A point of confusion is that for PVC piping, Schedule 80 pipe has a thinner wall than Sch 40 pipe.
Thicker pipe wall is required to contain higher fluid pressures. For the same fluid pressure, a thicker pipe wall is required for a larger diameter pipe than that required for a pipe of smaller diameter. A schedule of pipe sizes and wall thicknesses has been established by ASTM standards governing manufacturing of pipe.