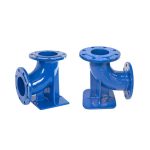
Double Flange 90° Duck Foot Ductile Iron Bend
March 23, 2025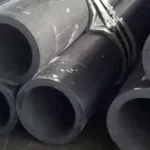
Optimization of the Seamless Steel Pipe Continuous Rolling Process
April 2, 2025ASTM A209/A209M is a standard specification for seamless carbon-molybdenum alloy-steel boiler and superheater tubes, commonly used in high-temperature and high-pressure applications like power generation systems. It covers several grades, specifically T1, T1a, and T1b, which differ slightly in their chemical composition and mechanical properties but are all designed for elevated temperature service. Since your original query asked about EN 10305-1 E235 seamless precision steel pipes, I’ll pivot to focus on ASTM A209/A209M as requested while ensuring the response aligns with the depth and structure you seem to expect (e.g., chemical composition, mechanical properties, dimensional accuracy, and testing requirements). Let’s break this down systematically.
Overview of ASTM A209/A209M
The ASTM A209/A209M standard applies to seamless tubes with nominal wall thickness, specifically for use in boilers, superheaters, and heat exchangers. These tubes are made from carbon-molybdenum alloy steel, which provides enhanced creep resistance and strength at high temperatures compared to plain carbon steel. The “M” in A209M indicates that metric (SI) units can be used, though inch-pound units are also standard depending on the order.
The standard specifies:
-
Size Range: Tubes from 1/2 inch to 5 inches [12.7 mm to 127 mm] in outside diameter.
-
Wall Thickness: Minimum wall thickness ranging from 0.035 inches to 0.500 inches [0.9 mm to 12.7 mm].
-
Grades: T1, T1a, and T1b, with slight variations in chemistry and properties.
Chemical Composition of ASTM A209/A209M Grades
The chemical composition of ASTM A209/A209M tubes is tightly controlled to ensure the desired high-temperature performance. The primary alloying elements are carbon, molybdenum, and manganese, with limits on phosphorus and sulfur to enhance weldability and reduce brittleness.
Table 1: Chemical Composition of ASTM A209/A209M Grades
Element
|
T1 (% max)
|
T1a (% max)
|
T1b (% max)
|
---|---|---|---|
Carbon (C)
|
0.10–0.20
|
0.15–0.25
|
0.14 max
|
Manganese (Mn)
|
0.30–0.80
|
0.30–0.80
|
0.30–0.80
|
Phosphorus (P)
|
0.025
|
0.025
|
0.025
|
Sulfur (S)
|
0.025
|
0.025
|
0.025
|
Silicon (Si)
|
0.10–0.50
|
0.10–0.50
|
0.10–0.50
|
Molybdenum (Mo)
|
0.44–0.65
|
0.44–0.65
|
0.44–0.65
|
Notes:
-
The steel must be fully killed, meaning it’s deoxidized to reduce gas porosity and improve homogeneity.
-
Variations in carbon content across grades (e.g., lower in T1b) affect strength and toughness slightly.
-
Molybdenum enhances high-temperature strength and resistance to creep, critical for boiler and superheater applications.
Mechanical Properties of ASTM A209/A209M Grades
The mechanical properties of ASTM A209/A209M tubes are specified to ensure they can withstand the stresses of high-pressure and high-temperature environments. These properties are determined through tensile tests, hardness tests, and other mechanical evaluations.
Table 2: Mechanical Properties of ASTM A209/A209M Grades
Property
|
T1
|
T1a
|
T1b
|
---|---|---|---|
Tensile Strength (min), ksi [MPa]
|
55 [380]
|
60 [415]
|
53 [365]
|
Yield Strength (min), ksi [MPa]
|
30 [205]
|
32 [220]
|
28 [195]
|
Elongation (min), %
|
30
|
30
|
30
|
Hardness (max), Brinell (HB)
|
146
|
153
|
137
|
Hardness (max), Rockwell (HRB)
|
80
|
81
|
77
|
Notes:
-
These values apply to tubes in the fully annealed, isothermally annealed, or normalized and tempered condition.
-
Heat treatment is mandatory: hot-finished tubes are heat-treated at 1200°F [650°C] or higher; cold-finished tubes are heat-treated after final cold finishing at the same temperature or higher.
-
Elongation is measured on a standard 2-inch [50 mm] gauge length or smaller proportional specimens.
Schedules and Dimensional Accuracy
ASTM A209/A209M does not explicitly define “schedules” like ASME B36.10 (common for piping), as it focuses on tubes with specific outside diameters (OD) and minimum wall thicknesses (WT) tailored for boilers and superheaters. However, dimensional accuracy is critical, and tolerances are specified to ensure proper fit and performance.
Table 3: Dimensional Tolerances for ASTM A209/A209M Tubes
Parameter
|
Tolerance (Inch-Pound Units)
|
Tolerance (SI Units)
|
---|---|---|
Outside Diameter (OD)
|
||
OD ≤ 2 in [50.8 mm]
|
±0.005 in
|
±0.13 mm
|
OD > 2 in [50.8 mm]
|
±0.010 in
|
±0.25 mm
|
Wall Thickness (WT)
|
±10% of nominal WT
|
±10% of nominal WT
|
Length (Cut Lengths)
|
+1/8 in, -0 in [+3.2 mm, -0 mm]
|
+3.2 mm, -0 mm
|
Straightness
|
1/8 in per 5 ft [3 mm per 1.5 m]
|
3 mm per 1.5 m
|
Notes:
-
Tubes are typically supplied in random lengths (e.g., 16–22 ft [4.8–6.7 m]) or specific cut lengths as agreed upon.
-
Ovality (out-of-roundness) is included in the OD tolerance.
-
Wall thickness is specified as minimum rather than nominal, meaning the actual WT must not be less than the specified value but can exceed it within tolerance.
Inspection and Test Requirements for ASTM A209/A209M
The ASTM A209/A209M standard mandates a series of inspections and tests to verify the quality, mechanical properties, and dimensional accuracy of the tubes. These tests ensure the tubes can withstand the demanding conditions of boiler and superheater applications. Below is a detailed list of required inspections and tests, similar to the format you requested for EN 10305-1.
1. Mandatory Inspections and Tests
These tests are required by the standard to confirm compliance.
-
Chemical Composition Analysis
-
Purpose: Verify the material’s composition meets the specified limits for the grade (T1, T1a, T1b).
-
Procedure: Performed on a sample from each heat (cast) using methods like spectrometry.
-
Frequency: One test per heat.
-
Acceptance Criteria: Must meet the limits in Table 1 above.
-
-
Tensile Test
-
Purpose: Determine tensile strength, yield strength, and elongation.
-
Procedure: Conducted per ASTM A370 on a specimen from each lot (≤50 tubes for one test; >50 tubes requires two tests).
-
Frequency: One test per lot (or two for larger lots).
-
Acceptance Criteria: Must meet the values in Table 2 above.
-
-
Flattening Test
-
Purpose: Assess ductility by flattening the tube without cracking.
-
Procedure: A section of the tube is flattened between parallel plates until a specified deformation is reached (per ASTM A999/A999M).
-
Frequency: One test on specimens from each end of one finished tube per lot.
-
Acceptance Criteria: No cracks or breaks on the tube surface.
-
-
Flaring Test (for Tubes ≤ 5 in [127 mm] OD)
-
Purpose: Evaluate the tube’s ability to be flared without cracking.
-
Procedure: A conical mandrel expands the tube end to a specified diameter (per ASTM A999/A999M).
-
Frequency: One test on specimens from each end of one finished tube per lot.
-
Acceptance Criteria: No cracks or defects after flaring.
-
-
Hardness Test
-
Purpose: Ensure the tube’s hardness is within acceptable limits.
-
Procedure: Brinell or Rockwell hardness tests (per ASTM A370) on specimens from two tubes per lot.
-
Frequency: Two tests per lot.
-
Acceptance Criteria: Must meet the maximum hardness values in Table 2 (e.g., 146 HB for T1).
-
-
Hydrostatic Test or Nondestructive Electric Test (NDET)
-
Purpose: Verify the tube’s integrity under pressure or detect surface/subsurface defects.
-
Procedure:
-
Hydrostatic Test: Tubes are pressurized to a specified level (e.g., 1000 psi [7 MPa] or as calculated per ASTM A999/A999M) without leakage.
-
NDET: Eddy current or ultrasonic testing to detect flaws (per ASTM E213 or E309).
-
-
Frequency: 100% of tubes (one test method required unless otherwise specified).
-
Acceptance Criteria: No leaks (hydrostatic) or defects beyond acceptance limits (NDET).
-
-
Dimensional Inspection
-
Purpose: Confirm OD, WT, length, and straightness meet tolerances.
-
Procedure: Measured using calibrated tools (e.g., micrometers, gauges).
-
Frequency: Typically 100% inspection, or sampling as agreed.
-
Acceptance Criteria: Must meet tolerances in Table 3 above.
-
-
Surface Quality Inspection
-
Purpose: Ensure the tube surface is free of defects like cracks, laps, or seams.
-
Procedure: Visual inspection or enhanced methods (e.g., dye penetrant) if specified.
-
Frequency: 100% of tubes.
-
Acceptance Criteria: No defects that impair usability.
-
2. Optional Inspections and Tests
These are performed only if specified in the purchase order.
-
Product Analysis
-
Purpose: Verify chemical composition of the finished product (beyond heat analysis).
-
Procedure: Similar to heat analysis but taken from finished tubes.
-
Frequency: As agreed (e.g., one test per lot).
-
-
Impact Test
-
Purpose: Assess toughness at specified temperatures (not common for boiler tubes unless low-temperature service is expected).
-
Procedure: Per ASTM A370, typically using Charpy V-notch specimens.
-
Frequency: As agreed.
-
-
Additional NDT
-
Purpose: Enhanced defect detection (e.g., ultrasonic testing for internal flaws).
-
Procedure: Per ASTM E213 (ultrasonic) or E309 (eddy current).
-
Frequency: As agreed, often 100% for critical applications.
-
-
Surface Roughness Measurement
-
Purpose: Verify surface finish for specific applications (e.g., heat exchanger tubes).
-
Procedure: Measured using a profilometer per ASTM standards.
-
Frequency: As agreed.
-
3. Test Units and Sampling
-
Definition of Lot: Tubes from the same heat, size, and heat treatment batch.
-
Sampling for Mechanical Tests: One or two tubes per lot (≤50 tubes: one test; >50 tubes: two tests).
-
NDT and Dimensional Checks: Typically 100% unless sampling is agreed upon.
4. Test Reports and Certification
-
Inspection Certificate: Supplied per ASTM A999/A999M, typically a 3.1 certificate per EN 10204, including results of all mandatory tests.
-
Content: Chemical composition, mechanical properties, dimensional checks, NDT results, and heat treatment details.
5. Retesting and Non-Conformance
-
Retesting: If a test fails, retesting is allowed on twice the number of specimens from the same lot.
-
Rejection: If retests fail, the lot may be rejected, or individual tubes can be tested.
-
Reprocessing: Tubes failing mechanical or dimensional requirements can be reprocessed (e.g., re-heat-treated) and retested if agreed upon.
Specifications and Applications
ASTM A209/A209M tubes are designed for high-pressure service in boilers and superheaters, where temperatures can exceed 500°C (930°F). Key specifications include:
-
Manufacturing Process: Seamless, either hot-finished or cold-finished.
-
Heat Treatment: Mandatory post-forming heat treatment (e.g., normalizing and tempering or annealing).
-
Surface Condition: Free of scale; may be supplied with protective coatings (e.g., oil-dipped) if specified.
-
Marking: Tubes are marked with the standard (ASTM A209), grade (e.g., T1), and manufacturer’s identification.
Common Applications:
-
Power Generation: Boiler tubes, superheater tubes, and reheaters in coal, gas, or oil-fired plants.
-
Industrial Furnaces: Tubes in heat recovery systems or petrochemical furnaces.
-
Heat Exchangers: For high-temperature fluid transfer in chemical plants.
Comparison with EN 10305-1 E235 (Contextual Note)
Since your original query referenced EN 10305-1 E235, it’s worth noting that ASTM A209/A209M tubes serve a different purpose. EN 10305-1 E235 tubes are low-carbon precision tubes for general engineering (e.g., hydraulic systems, automotive parts), with a focus on dimensional accuracy and cold-forming properties. ASTM A209/A209M, conversely, targets high-temperature service with alloying for creep resistance, so its mechanical properties (e.g., tensile strength at elevated temperatures) and testing requirements (e.g., flaring and hydrostatic tests) are tailored for that environment.
Conclusion
ASTM A209/A209M seamless carbon-molybdenum alloy-steel tubes are engineered for reliability in high-temperature, high-pressure environments like boilers and superheaters. Their chemical composition, with controlled molybdenum content, ensures enhanced creep resistance, while their mechanical properties and rigorous testing (tensile, flattening, flaring, hardness, hydrostatic/NDT) guarantee performance under stress. Dimensional tolerances are specified to ensure proper fit in complex systems, though they are less stringent than precision standards like EN 10305-1 due to the different application focus.