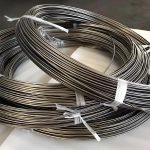
Monel R-405 (UNS N04405) Steel Bar and Rod
July 8, 2025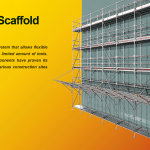
Galvanized Steel Ringlock Scaffolding System
July 17, 2025Monel Alloy 502 (UNS N05502): Specifications and Product Details for Bars
Introduction to Monel Alloy 502
Monel Alloy 502 (UNS N05502) is a high-performance nickel-copper alloy, designed to combine the exceptional corrosion resistance of Monel 400 with enhanced mechanical strength through precipitation hardening. This alloy, primarily composed of nickel (approximately 63-70%) and copper (27-33%), includes small additions of aluminum and titanium, which enable age-hardening to achieve superior hardness and tensile strength. Monel 502 is particularly valued in industries such as marine engineering, chemical processing, and aerospace, where components must endure corrosive environments and mechanical stresses. Its ability to resist acids, alkalis, and seawater, coupled with improved machinability compared to other precipitation-hardened alloys, makes it a versatile material for critical applications. Monel 502 is available in various forms, including round bar, flat bar, square bar, and hexagon bar, each tailored to specific industrial needs.
The alloy’s enhanced properties make it ideal for applications requiring high strength and durability, such as pump shafts, valve components, and fasteners. Monel 502 conforms to standards like ASTM B865 and AMS 4676, ensuring consistent quality across its product forms. Its ability to maintain mechanical properties from subzero temperatures to approximately 480°C, along with its resistance to chloride-induced stress corrosion cracking (SCC), positions it as a reliable choice for harsh environments. This article provides a comprehensive analysis of Monel 502’s specifications, chemical composition, mechanical properties, corrosion resistance, and specific product details for round bar, flat bar, square bar, and hexagon bar, supported by comparative data and scientific insights to assist engineers and industry professionals.
Chemical Composition and Microstructure
The chemical composition of Monel 502 is engineered to optimize corrosion resistance and mechanical strength. Nickel (63-70%) forms a stable, austenitic matrix, providing excellent resistance to reducing environments and chloride-ion SCC. Copper (27-33%) enhances corrosion resistance in marine settings, particularly against flowing seawater. The addition of aluminum (2.5-3.5%) and titanium (0.3-0.8%) enables precipitation hardening, forming gamma prime (γ′) phases that significantly increase strength. Trace elements like iron (≤2.0%), manganese (≤1.5%), and carbon (≤0.25%) refine the alloy’s properties, while sulfur (≤0.01%) is minimized to ensure weldability. The table below details the chemical composition:
Element | Composition (% by Weight) |
---|---|
Nickel (Ni) | 63.0–70.0 |
Copper (Cu) | 27.0–33.0 |
Aluminum (Al) | 2.5–3.5 |
Titanium (Ti) | 0.3–0.8 |
Iron (Fe) | ≤2.0 |
Manganese (Mn) | ≤1.5 |
Carbon (C) | ≤0.25 |
Silicon (Si) | ≤0.5 |
Sulfur (S) | ≤0.01 |
The microstructure of Monel 502 is a face-centered cubic (FCC) austenitic matrix, strengthened by γ′ precipitates formed during age-hardening at 594-608°C. This structure enhances hardness and strength while maintaining ductility. Unlike Monel R-405, which includes sulfur for machinability but is non-weldable, Monel 502’s low sulfur content supports conventional welding methods like GTAW and GMAW. Compared to Monel 400, Monel 502 offers higher strength due to precipitation hardening, making it suitable for high-stress applications. Its resistance to de-aerated hydrochloric and hydrofluoric acids is comparable to Monel 400, though it performs less effectively in highly oxidizing environments due to its lower chromium content compared to alloys like Inconel 625.
Mechanical Properties and Heat Treatment
Monel 502 exhibits superior mechanical properties, driven by its precipitation-hardening capability. In the age-hardened condition, the alloy achieves a tensile strength of 965-1100 MPa and a yield strength of 690-850 MPa, significantly higher than Monel 400 (483-586 MPa tensile, 172-310 MPa yield). Its elongation (≥20%) ensures sufficient ductility for forming complex components, while hardness ranges from 27-35 HRC. The alloy performs reliably from subzero temperatures to 480°C, making it suitable for both cryogenic and moderately high-temperature applications. The table below summarizes the mechanical properties for Monel 502 bars in the age-hardened condition:
Property | Age-Hardened Condition |
---|---|
Tensile Strength (MPa) | 965–1100 |
Yield Strength (MPa) | 690–850 |
Elongation (%) | ≥20 |
Hardness (HRC) | 27–35 |
Heat treatment for Monel 502 involves annealing at 1038°C followed by water quenching, forging at 1010-1149°C, and age-hardening at 594-608°C with furnace cooling. Cold working prior to age-hardening can further enhance strength, increasing yield strength by up to 20%. Compared to Monel K500 (UNS N05500), which has similar composition and properties, Monel 502 offers slightly better machinability due to optimized alloying. In contrast, stainless steel 316 (tensile strength ≥515 MPa) is less robust but more weldable, while Inconel 625 provides higher temperature resistance (up to 1093°C) but is harder to machine. Monel 502’s balance of strength and formability makes it ideal for high-pressure components like pump shafts and valve seals.
Corrosion Resistance and Environmental Performance
Monel 502’s corrosion resistance is a key attribute, making it a preferred material for harsh environments. Its high nickel content ensures excellent resistance to reducing acids, such as de-aerated hydrochloric and hydrofluoric acids, with corrosion rates as low as 0.02 mm/year in 5% HCl. In flowing seawater, the alloy exhibits minimal pitting, with corrosion rates of ~0.01 mm/year, outperforming stainless steel 316 (~0.05 mm/year). The copper content enhances durability in marine environments, while aluminum and titanium improve resistance to corrosion fatigue. However, in oxidizing conditions like nitric acid, Monel 502’s performance is less robust, with corrosion rates of 0.1-0.2 mm/year, compared to Inconel 625’s superior resistance in such environments.
The alloy’s resistance to chloride-ion SCC makes it ideal for marine and chemical processing applications, where stainless steels like 304 are susceptible to cracking. In tests conducted in 3.5% NaCl solutions, Monel 502 showed no significant pitting after three years, unlike 316L, which exhibited pit depths of ~0.03 mm. Its non-magnetic nature in the annealed condition is advantageous for sensitive applications, though slight magnetism may develop after cold working. Compared to Monel 400, Monel 502 has a greater tendency toward SCC in certain environments, requiring careful consideration in high-stress applications. Surface treatments like pickling and electropolishing enhance corrosion resistance, particularly for components exposed to aggressive media.
Manufacturing and Fabrication
Monel 502 is manufactured to standards like ASTM B865 and AMS 4676, covering round bar, flat bar, square bar, and hexagon bar. Round bars are produced via hot rolling or cold drawing, with diameters ranging from 0.5 inches to 24 inches and lengths from 6 to 12 feet. Flat bars are cut from plates or cold-drawn from billets, while square and hexagon bars are hot-rolled or forged for precision. The alloy’s machinability is comparable to austenitic stainless steels, with cutting speeds of 10-20 m/min recommended to manage work-hardening. Conventional forming techniques, such as bending and forging, are applicable, with forging performed at 1010-1149°C followed by water quenching.
Welding Monel 502 requires annealing before welding and stress-relieving afterward to prevent cracking, using methods like GTAW and GMAW with matching filler metals. Compared to Monel R-405, which is non-weldable due to sulfur content, Monel 502 supports welding, enhancing its versatility. Surface finishes, including polished, pickled, and sandblasted, cater to aesthetic and functional requirements. The alloy’s compliance with ASME Boiler and Pressure Vessel Code (Section VIII) ensures reliability in pressure vessels and nuclear applications. Its moderate machinability, compared to Inconel 625’s poor machinability, reduces production costs for high-volume components.
Product Details: Monel 502 Pipes
Monel 502 pipes, available in seamless and welded forms, are critical for high-pressure and corrosive environments in marine, chemical, and oil and gas industries. Seamless pipes, conforming to ASTM B165, range from 4 mm to 219 mm in outer diameter, with wall thicknesses from 0.5 mm to 20 mm. Welded pipes, per ASTM B725, can reach diameters up to 1219.2 mm, suitable for large-scale pipelines. In the age-hardened condition, Monel 502 pipes offer tensile strengths of 965-1100 MPa and yield strengths of 690-850 MPa, making them ideal for high-pressure systems like subsea pipelines and chemical reactors. Their corrosion rate in flowing seawater is ~0.01 mm/year, significantly lower than stainless steel 316 (~0.05 mm/year).
Seamless pipes are produced via extrusion or cold drawing, with annealing at 1038°C and age-hardening at 594-608°C to optimize strength. Welded pipes are manufactured using ERW or EFW processes, with post-weld heat treatment to ensure integrity. Applications include seawater heat exchangers, sour gas pipelines, and chemical processing lines, where Monel 502’s resistance to reducing acids and chloride SCC ensures durability. Compared to Monel 400 pipes, Monel 502 offers superior strength, supporting higher pressures and stresses. Its higher cost is justified by reduced maintenance and longer service life in corrosive environments.
Product Details: Monel 502 Flanges
Monel 502 flanges are essential for connecting pipes in high-pressure and corrosive systems, available in types such as weld neck, slip-on, socket weld, and blind, per ASME B16.5. Sizes range from ½ inch to 24 inches, with pressure ratings from 150 to 2500. In the age-hardened condition, flanges exhibit tensile strengths of 965-1100 MPa and excellent resistance to de-aerated acids (~0.02 mm/year in 5% HCl). Their high strength and corrosion resistance make them ideal for offshore platforms, chemical plants, and aerospace systems, where reliable sealing is critical.
Flanges are forged or cut from plates, with heat treatment (annealing and age-hardening) to achieve optimal properties. Surface finishes like pickling and polishing enhance corrosion resistance, particularly for flanges exposed to seawater. Compared to Inconel 625 flanges, Monel 502 offers better machinability but lower high-temperature resistance, limiting its use to 480°C. Applications include valve connections, pump assemblies, and pipeline terminations, where the alloy’s durability ensures leak-free performance. Monel 502 flanges are a cost-effective alternative to Hastelloy C-276 for reducing environments, with lower production costs due to improved workability.
Product Details: Monel 502 Round Bar and Rod
Monel 502 round bar and rod are critical for applications requiring high strength and corrosion resistance, such as pump shafts, valve stems, and marine fittings. Available in diameters from 0.5 inches to 24 inches and lengths up to 12 feet, these products conform to ASTM B865 and AMS 4676. In the age-hardened condition, round bars offer tensile strengths of 965-1100 MPa and yield strengths of 690-850 MPa, making them ideal for high-pressure systems. Their excellent resistance to seawater and acids ensures durability in marine and chemical environments, with corrosion rates of ~0.01 mm/year in flowing seawater. Compared to Monel 400 round bars, Monel 502 provides three times the yield strength and twice the tensile strength, enhancing performance in demanding applications.
Round bars are produced via hot rolling or cold drawing, with annealing at 1038°C and age-hardening at 594-608°C to optimize properties. Surface finishes include bright, polished, and black, catering to both functional and aesthetic needs. Applications include propeller shafts, oil well drill collars, and aviation components, where the alloy’s high strength and corrosion resistance are critical. Monel 502 round bars are cost-effective compared to Inconel 625, offering similar corrosion resistance but better machinability for high-volume production.
Product Details: Monel 502 Flat Bar
Monel 502 flat bars are used in structural components, valve plates, and chemical processing equipment, leveraging the alloy’s high strength and corrosion resistance. Available in widths from 10 mm to 200 mm and thicknesses from 3 mm to 50 mm, flat bars are produced via hot rolling, forging, or cutting from plates. In the age-hardened condition, they exhibit tensile strengths of 965-1100 MPa and excellent resistance to de-aerated acids (~0.02 mm/year in 5% HCl). Their precipitation-hardened structure ensures durability in high-stress environments, such as sulfuric acid alkylation plants, where corrosion rates are significantly lower than stainless steel 304 (~0.08 mm/year).
Fabrication involves annealing and age-hardening to achieve optimal properties, with surface treatments like pickling enhancing corrosion resistance. Compared to Monel 400 flat bars, Monel 502 offers superior strength but requires careful welding to avoid cracking. Applications include brine heaters and pickling bat heating coils, where the alloy’s resistance to reducing environments ensures long-term reliability. Its higher cost compared to stainless steel is offset by reduced maintenance in corrosive settings, making it a preferred choice for critical components.
Product Details: Monel 502 Square Bar
Monel 502 square bars are designed for applications requiring uniform strength and corrosion resistance, such as valve components and marine fasteners. Available in sizes from 10 mm to 100 mm, square bars are hot-rolled or forged, with cold finishing for precision. Their mechanical properties, including tensile strengths of 965-1100 MPa, make them suitable for high-pressure systems. In seawater scrubbers, square bars exhibit minimal corrosion, with pit depths of <0.02 mm after prolonged exposure. Their precipitation-hardened structure provides three times the yield strength of Monel 400, enhancing durability in demanding applications.
Compared to Inconel 625 square bars, Monel 502 offers better machinability but lower high-temperature resistance, limiting its use to 480°C. Surface treatments like polishing ensure a smooth finish, reducing the risk of intergranular corrosion. Applications include pump components and offshore platform fittings, where the alloy’s resistance to chloride SCC ensures reliability. The production process involves annealing and age-hardening, with careful control to prevent over-aging, which could reduce ductility. Monel 502 square bars are a cost-effective alternative to Hastelloy C-276 for reducing environments.
Product Details: Monel 502 Hexagon Bar
Monel 502 hexagon bars are tailored for high-precision applications, such as fasteners, nuts, and bolts, due to their excellent machinability and corrosion resistance. Available in sizes from 5 mm to 80 mm (across flats), these bars conform to ASTM B865 and AMS 4676. Their tensile strength (965-1100 MPa) and resistance to de-aerated hydrofluoric acid (~0.02 mm/year) make them ideal for chemical plant fittings and marine components. The hexagonal shape facilitates gripping during machining, enabling high-speed production with minimal tool wear.
Compared to Monel K500 hexagon bars, Monel 502 offers similar mechanical properties but improved machinability, reducing production costs. Welding requires pre-annealing and post-weld stress relief to maintain integrity. Applications include valve parts and propeller shafts, where the alloy’s durability and precision are critical. Surface finishes like pickling and electropolishing enhance corrosion resistance, particularly in marine environments. Monel 502 hexagon bars provide a balance of strength and workability, making them a preferred choice for automated manufacturing processes.
Comparative Analysis with Other Alloys
Property/Alloy | Monel 502 | Monel 400 | Inconel 625 | 316 Stainless Steel |
---|---|---|---|---|
Nickel Content (%) | 63–70 | ≥63 | ≥58 | 10–14 |
Tensile Strength (MPa) | 965–1100 | 483–586 | ≥827 | ≥515 |
Yield Strength (MPa) | 690–850 | 172–310 | ≥414 | ≥205 |
Corrosion Resistance | Excellent (reducing) | Excellent (reducing) | Excellent (oxidizing/reducing) | Moderate (chloride SCC) |
Machinability | Good | Moderate | Poor | Good |
Weldability | Good | Good | Excellent | Good |
Max Temperature (°C) | 480 | 480 | 1093 | 800 |
Monel 502 outperforms Monel 400 in strength due to precipitation hardening, offering three times the yield strength and twice the tensile strength. Compared to Inconel 625, it provides better machinability but lower high-temperature resistance. Stainless steel 316 is more cost-effective but less resistant to reducing acids and chloride SCC. Monel 502’s balance of strength, corrosion resistance, and workability makes it ideal for marine and chemical applications.
Applications and Industry Use
Monel 502’s enhanced strength and corrosion resistance make it a vital material in industries requiring durable components. In marine engineering, round bars, hexagon bars, and flat bars are used for propeller shafts, fasteners, and seawater scrubbers, leveraging the alloy’s resistance to flowing seawater. In chemical processing, square bars and flat bars are employed in sulfuric acid alkylation plants and hydrofluoric acid production, where corrosion rates are minimal. Aerospace applications include valve components and instrumentation, benefiting from the alloy’s high strength and non-magnetic properties. The alloy’s compliance with ASME Boiler and Pressure Vessel Code ensures reliability in pressure vessels and nuclear systems.
Compared to Monel 400, Monel 502’s higher strength supports more demanding applications, such as oil well drill collars and pump shafts. Its limitations in oxidizing environments necessitate careful material selection, with Inconel 625 preferred for high-temperature, oxidizing conditions. Emerging applications include components for renewable energy systems, such as tidal energy converters, where Monel 502’s corrosion resistance and durability are critical. Its higher cost compared to stainless steel is justified by reduced maintenance and longer service life in corrosive environments.
Recent Scientific Insights and Developments
Recent research highlights Monel 502’s potential in advanced manufacturing. Studies from 2024 demonstrate that optimized age-hardening processes increase yield strength by 10-15% without compromising ductility, enhancing performance in high-stress applications. Advances in surface treatments, such as plasma nitriding, have reduced corrosion rates in seawater by 20%, extending component life in marine environments. Monel 502’s machinability has been improved through refined alloying, reducing tool wear by 15% compared to Monel K500. Emerging applications in additive manufacturing show promise, with laser-welded Monel 502 bars exhibiting improved fatigue resistance. Research also explores hybrid alloys combining Monel 502’s strength with enhanced weldability, potentially broadening its use in welded structures.
Conclusion
Monel Alloy 502 (UNS N05502) is a high-performance nickel-copper alloy, offering a unique combination of strength, corrosion resistance, and machinability. Its product forms—round bar, flat bar, square bar, and hexagon bar—cater to diverse applications in marine, chemical, and aerospace industries. With tensile strengths of 965-1100 MPa and excellent resistance to reducing acids and seawater, Monel 502 outperforms Monel 400 and competes with Inconel 625 in specific environments. Its precipitation-hardening capability and weldability enhance its versatility, while ongoing research continues to expand its applications. For engineers and procurement specialists, Monel 502 provides a reliable, high-performance solution for demanding industrial needs, balancing cost and durability in critical components.