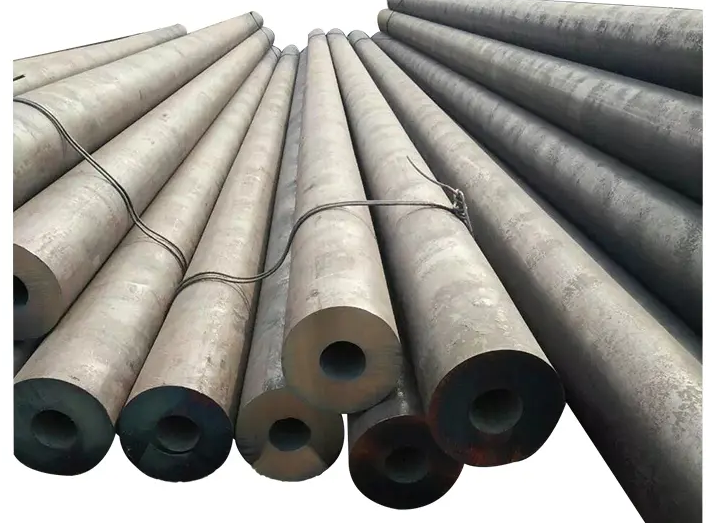
Uma nova tecnologia: A335 Alloy Steel Pipe Tratamento Térmico de Juntas de Solda
Maio 23, 2023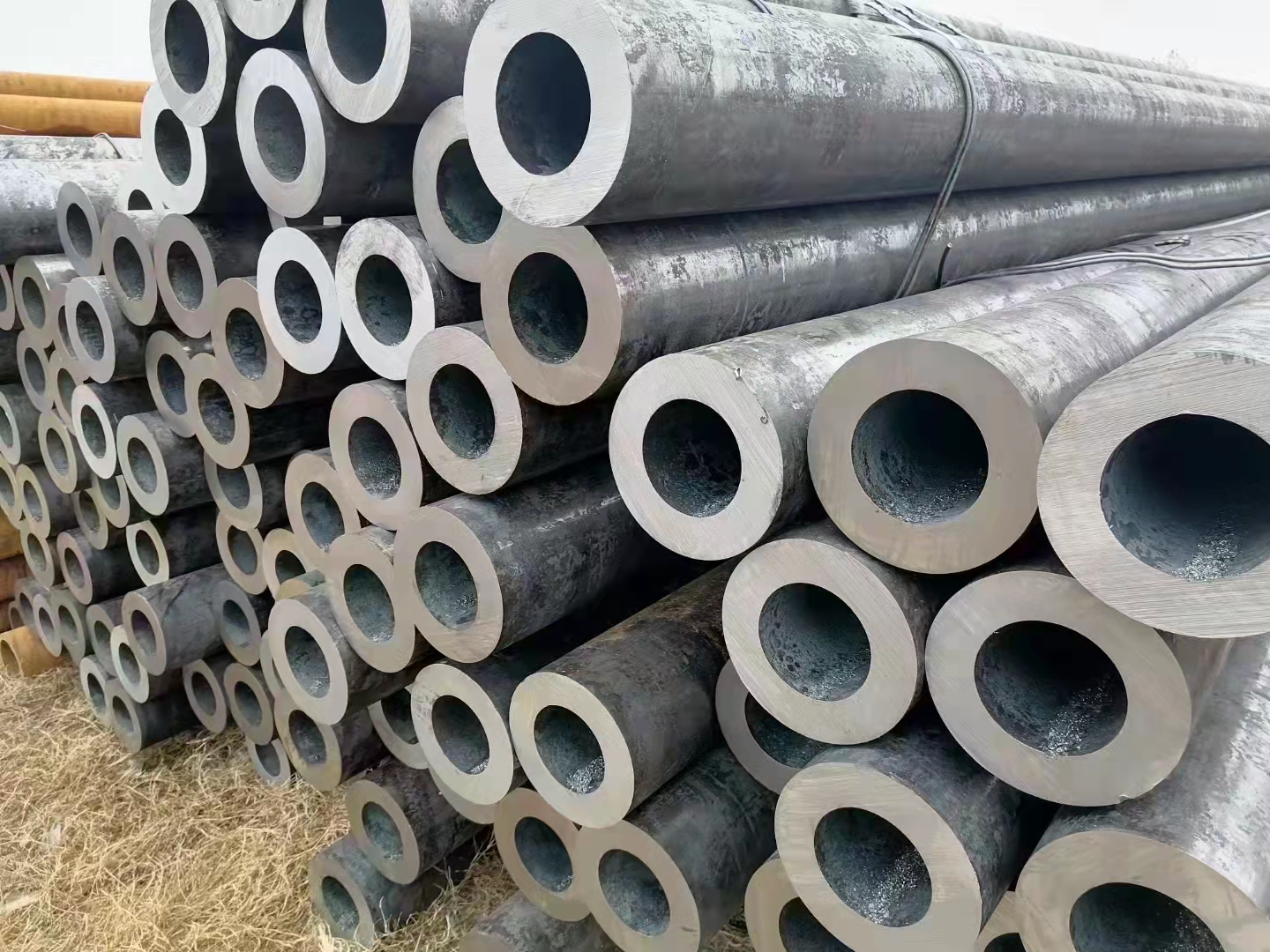
Qual é a diferença entre ASTM A105 e ASTM A234?
Junho 18, 2023As perspectivas de pesquisa e desenvolvimento da caixa de óleo HFW da ABTER STEEL no futuro são discutidas. Ressalta-se que o desenvolvimento do invólucro a óleo ABTER STEEL HFW deve destacar a siderurgia + fabricação de tubos + pipe processing
and the advantages of consistent quality system to achieve differentiated development; expand the specifications and output of developed products, research and develop large-diameter thick-walled K55, high anti-extrusion and corrosão resistência
Invólucro de óleo.
Palavras-chave: HFW; óleo invólucro; ABTER AÇO; research and development status; prospect; J55; K55
According to the forming method, oil casing pipes are divided into two types: seamless steel pipes and welded pipes. Compared with seamless steel pipes, welded pipes have the most notable features of high wall thickness and dimension accuracy, good collapse resistance, and short manufacturing process. , eficiência de produção elevada, wide range of specifications, economia de energia, low production cost, and high cost performance; assim sendo, high frequency welding (HFW for short) is commonly used in oil casings in foreign countries (such as the United States, Alemanha, Japão, Coreia do Sul, etc.) ) pipes instead of seamless steel pipes, domestic oil fields are also gradually promoting the use of [1]
.
ABTER STEEL Co., Ltd. (ABTER STEEL for short) has developed H40, J55, K55,
M65, L80 -1, N80 -Q, N80 -1 and P110 steel grade HFW oil casing products, incluindo a 7 outer diameters (219.08 ~508.00 mm), 46 especificações (Mesa 1), basically meet the product outline According to the requirements, 500,000 tons have been supplied to domestic and foreign oil fields and other users [2-3].
API 5CT Gr.J55 Pipe Casing
API 5CT-American Petroleum Institute is the specification for seamless casing and tubing, API 5CT J55 Tubo de revestimento is mainly used for shallow wells, poços geotérmicos, and water wells or oil well drilling mainly for supporting the well-wall during and after drilling to ensure the drilling process and the normal operation of the entire well after completion. World iron & steel is one of the leading China Casing Pipe manufacturers and suppliers, if you want to buy or import high-quality API J55 casing pipe, Por favor, sinta -se à vontade para entrar em contato conosco.
Padrão: API 5CT
Grau: J55
Tolerância.
OD<114.3mm tolerance ±0.79
OD≥114.3mm tolerance -0.5% +1%
Tolerância à espessura:-12.5%
Aplicações: Shallow wells, poços geotérmicos, and water wells or other oil wells
Technical Difficulties and Process Characteristics of J55 Casing
Compared with other welding methods, high-frequency welding is characterized by the absence of metal fillers (such as welding wire); assim sendo, when the welding process is stable, the welding quality depends largely on the quality of the steel strip. Por exemplo, the J55 casing produced by Baosteel’s Φ610 mm HFW longitudinal seam welded pipe unit has an original chemical composition of steel with C and Mn as the main strengthening elements, does not contain Nb, and has central segregation in the hot-rolled steel strip [1 ]
.
The range of J55 oil casing that can be manufactured is Ф219.08~508.00 mm, of which the steel belt widths used for the two specifications of Ф219.08 mm and Ф244.48 mm are 700 mm e 770 mm respectively, which are narrow strips. In order not to waste hot rolling capacity, Usually hot-rolled 1 420 mm, 1 560 mm wide strips are longitudinally sectioned along the center line. Due to the composition segregation of the hot-rolled steel strip, and the segregation of 1/2 part (the center of the steel strip) is serious, the center segregation zone is located at the weld after the pipe is made, and the segregation zone in the weld heat-affected zone after the online weld normalizing heat treatment There are strips of martensite on the casing, and API standards do not allow the presence of untempered martensite in the casing, so it is necessary to add
Add the whole tube heat treatment to eliminate, thus increasing the production cost. Aiming at the above problems, ABTER STEEL Co., Ltd. designed two test schemes to adjust the chemical composition of the steel strip used for J55 casing[1]
.
Scheme 1: Reduce carbon in material design to reduce steel strip center segregation, W (C) é 0.17% Para 0.20%, 0.075% lower than the original chemical composition, reducing carbon segregation; Si, Mn content and original composition same. After the trial production of scheme 1, the segregation in the center of the steel strip is reduced, but there is still a small amount of martensite on the segregation zone in the heat-affected zone after the weld normalizing heat treatment[1]
.
Scheme 2: Reduce carbon and manganese in material design to reduce steel strip center segregation, W (C) é 0.13% Para 0.18%, qual é 0.105% lower than the original chemical composition, reducing carbon segregation; W (MN) is 0.60%~1.00%, qual é 0.30% lower than the original chemical composition, which reduces the segregation of manganese, so that there is no martensitic structure after online normalizing heat treatment in the weld[1]; strength loss, improve the processing performance of the pipe and prevent the casing thread from sticking; add a small amount of Ca to purify the molten steel, promote the spheroidization of MnS, and improve the comprehensive performance of the material [4]. For the J55 steel strip designed according to the composition of Scheme 2, martensite will not appear in the heat-affected zone of the weld after pipe making, and the microstructure and strength meet the requirements of API Spec 5CT.
API 5CT K55/J55 Chemical Composition
Grau | C≤ | Si≤ | Mn≤ | P ≤ | S≤ | CR≤ | Ni≤ | Cu≤ | Mo≤ | V≤ |
API 5CT K55/J55 | 0.34-0.39 | 0.20-0.35 | 1.25-1.50 | 0.020 | 0.015 | 0.15 | 0.20 | 0.20 | / | / |
API 5CT K55/J55 Mechanical Property
Classe de aço | Força de rendimento (MPa) | Resistência à tração (MPa) | Total Elongation under load % |
API 5CT K55 | 379-552 | ≥655 | 0.5 |
API 5CT J55 | 379-552 | ≥517 | 0.5 |
Tratamento térmico (PSL2 and PSL1 are different)
API 5CT J55 PSL1 and API 5CT K55 PSL2 is the same (Rolling delivery);
PSL2 :J55 and K55 should be normalized or normalized and tempered. If thickened, normalizing or normalizing and tempering should be added after thickening.
Teste de impacto (PSL2 and PSL1 are different)
Tubulação: PSL1, J55 and K55 have no requirement; PSL2 J55 and K55 require minimum impact work 20J of full size specimen, and minimum impact work 27J of full size specimen.
Acoplamento: J55 and K55 impact tests are necessary. The minimum impact energy of the specimen is 20J, and the minimum impact energy of the full size specimen is 27J.
Technical difficulties and process characteristics of K55 casing
The yield strength range of K55 steel grade oil casing is between 379-552MPa, and the tensile strength is greater than 655MPa, which is characterized by a very low yield ratio of the material (0.58-0.84). Projetado a partir da composição química dos materiais
Em outras palavras, aços carbono-manganês comuns são ideais para atingir taxas de rendimento baixas, como aço 37Mn5, que é amplamente utilizado na produção de tubos de aço sem costura grau K55, com w(C) sobre 0.37% e W(MN) sobre 1.3%. A resistência ao escoamento de 37Mn5 após a laminação é de cerca de 450 MPa, a resistência à tração está acima 700 MPa, e a taxa de rendimento é 0.64, que pode atender aos requisitos das propriedades mecânicas do aço K55[5]
O processo de produção do invólucro HFW é: siderurgia → fundição contínua → laminação a quente em bobinas → soldagem de topo e cisalhamento de bobinas → formação de tira → soldagem → tratamento térmico de soldagem on-line ou tratamento térmico de todo o tubo → processamento de tubo → espera de inspeção de fábrica. The coil head and tail shear butt welding process is the key process to realize the continuous production of multiple coils and reflect the production efficiency of HFW welded pipes. No entanto, due to the low carbon equivalent of materials required for head-to-tail butt welding of coils, it is generally required that the carbon equivalent CEIIW be less than 0.43, otherwise it is easy to cause strip breakage and seriously affect production efficiency. Since the carbon equivalent CEIIW of 37Mn5 steel reaches 0.58, combined with the production process characteristics of welded pipes, this steel is obviously not suitable for the production of K55 steel grade HFW oil casing; assim sendo, the technical difficulty in the production of K55 steel grade HFW oil casing lies in the material The design must ensure a low yield ratio at a low carbon equivalent. The HFW forming method of ABTER STEEL Co., Ltd. adopts advanced row-roll forming technology, which provides a guarantee for obtaining excellent weld performance. Durante o processo de conformação, the steel strip passes through the rolls of each rolling mill, and gradually bends to the shape of the ideal tube blank according to the designed pass system [3], which is a continuous and dynamic deformation process. Neste processo, along with the transverse bending deformation of the steel strip, tensão, compression and springback occur simultaneously, shear deformation on the surface and in the thickness direction of the plate, and longitudinal stretching and extrusion deformation on the edge [6]. The stress state of various deformations is very complicated, but the strain ε can be estimated by the following formula: ε=t/(D+t) (1) where t——thickness of steel strip, mm; D——outer diameter of welded pipe, mm . Practice has proved that by means of carbon reduction, alloying and controlled cooling during hot rolling, it is possible to produce hot-rolled coils whose mechanical properties meet the requirements of K55 steel grade. Por exemplo, for a hot-rolled coil with a final rolling temperature greater than 860 °C and a coiling temperature of 570 ° C, the yield strength is 478 MPa and the tensile strength is 697 MPa [5]. For the medium-diameter Ф273 mm×10.16 mm casing, the strain after pipe making is about 3.6%. According to the stress-strain curve, when the strain of 3.6% ocorre, the yield strength after pipe making will increase to about 563 MPa, which has It exceeds the required range of yield strength of K55 steel grade [5]. For this kind of hot-rolled coil, in order to ensure that the yield strength after pipe making is less than 552 MPa, the strain after pipe making shall not exceed 3.0%. If the HFW casing of different specifications of K55 steel grade is limited by 3.0% strain, there are only Ф339.72 mm×9.65 mm, Ф406.4 mm×11.13 mm, Ф473.08 mm×11.05 mm, Ф508 mm×12.7 mm, Ф508 mm ×11.13 mm and other specifications of HFW bushings have a strain of less than 3.0%, that is to say, under the ideal condition of not considering the performance fluctuation of coils, only the above five specifications of casings The mechanical properties after pipe making can meet the requirements of K55 steel grade. For casings of other specifications, thermal processing must be used after pipe making to produce qualified HFW casings.
The on-site production shows that compared with the coil, the yield strength of the pipe body after forming is about 50-100 MPa higher than that of the coil, and the tensile strength is about 10-30 MPa lower. Desta maneira, the ideal coil yield strength should be controlled
It is around 400MPa, while the tensile strength should be controlled above 680MPa; the yield ratio is 0.59. Obviously, such a low yield ratio is difficult to achieve for ordinary carbon or low alloy steel.
Practice has shown that: due to the significant work hardening effect of small diameter HFW casing, the mechanical properties of the hot rolled plate after coiling can not meet the requirements of K55 steel grade. No entanto, the work hardening effect of large diameter casing is small with the same wall thickness. On the basis of laboratory research, two sets of technical solutions can be adopted to deal with it respectively. Plan 1, specifications above Ф339 mm, conduct fine-tuning tests on the chemical composition of the current steel grades, in order to produce qualified K55 steel grade casings through on-line weld heat treatment after pipe making; Plan 2, specifications below Ф339 mm, after passing the pipe making The normalizing heat treatment of the whole tube meets the performance requirements of K55 steel grade.
For the first set of schemes, the idea of composition design is: the best combination of two solid solution strengthening alloying elements, C and Mn, can effectively reduce the yield strength ratio of the material [7], such as the 37Mn5 steel grade for the production of K55 steel grade tubulação de aço sem costura , and its yield strength ratio can reach 0.64; assim sendo, carbon is reduced on the basis of 37Mn5 to meet the requirements of low carbon equivalent and low yield strength ratio. Por outro lado, aluminum killed steel is a traditional fine-grained steel, and Al is used as an alloying element It is unfavorable to reduce the yield strength ratio of the material, and the Al content should be reduced. For the second set of schemes, the method of normalizing heat treatment to the welded pipe is used to eliminate the work hardening effect caused by strip forming. Because the normalizing heat treatment of the welded pipe can not only eliminate the influence of the work hardening of the material and the fluctuation of the properties of the coil itself on the mechanical properties, but also make the mechanical properties and microstructure of the welding seam close to the pipe body, and the mechanical properties of the whole pipe are stable. Good sex. The composition design idea is as follows: on the basis of carbon-manganese steel, V is the main strengthening element, impurities such as P and S are controlled, and the molten steel is purified by Ca treatment. K55 steel grade casing with stable performance. The tensile properties of the two schemes after pipe making all meet the requirements of the API Spec 5CT standard (Mesa 2). The Ф473.08 mm×11.05 mm K55 steel grade casing products are shown in Figure 1.
Development prospect of ABTER STEEL HFW oil casing
According to the literature [8], petroleum and combustible gases (such as natural gas, shale gas, metano de cama de carvão, etc.) are the main energy consumed by human beings at present. No passado 30 anos, the world’s fossil energy usage has continued to grow, mainly from petroleum, combustible gas and coal. Other types of energy, such as water energy, nuclear energy, biomass energy, wind energy, and solar energy, only account for a small proportion of the total energy. Even at the most optimistic development rate, it is impossible to replace fossil energy and occupy a dominant position at least before 2050 . Since my country became a net oil importer in 1993, my country’s crude oil consumption has increased at an average annual rate of 5.77%, and has become the world’s second largest crude oil consumer. According to the predictions of the International Energy Agency (AIE) and the US Energy Information Administration (EIA), By 2030, my country’s demand for oil and gas will basically be about 800 million tons of crude oil and about 200 billion m3 of natural gas. China’s “Twelfth Five-Year Plan” plans for oil and gas equivalent: China National Petroleum Corporation’s 400 milhões de toneladas, of which overseas exploration accounts for 50%, domestic key mining Songliao, Ordos, Xinjiang, Bohai Bay and Sichuan-Chongqing areas; China Petrochemical Corporation plans The production equivalent is 110 milhões de toneladas; that of China National Offshore Oil Corporation is 100 milhões de toneladas. Durante o “Twelfth Five-Year Plan” período, the average annual demand for oil well pipes is about 3.2 milhões de toneladas. Oil well pipes are important materials and equipment necessary for oil and gas exploration and development, and account for an average of 20% Para 30% of the entire well construction cost. The process of oil and gas industry exploration and development is the process of using and consuming oil well pipes in large quantities. Before the 1980s, all or mainly oil well pipes used in my country relied on imports. Until 1998, the localization rate of oil well pipes in my country reached 85% [9]. Atualmente, my country’s oil well pipe production capacity has reached 10 milhões de toneladas, and the production capacity is seriously overcapacitated. sob a ação sucessiva da força de teste inicial, the production capacity of enterprises with steelmaking + fabricação de tubos + pipe processing capabilities is about 5.5 milhões de toneladas, such as Tianjin Steel Pipe Group Co., Ltd., ABTER AÇO, Hengyang Valin Steel Pipe Co., Ltd., Pangang Group Chengdu Steel Vanadium Co., Ltd., Wuxi Simlais Petroleum Special Pipe Manufacturing Co., Ltd., etc.; companies with pipe manufacturing + pipe processing capabilities have a production capacity of about 1.3 milhões de toneladas, such as Baoji Petroleum Steel Pipe Co., Ltd.; The production capacity of enterprises with pipe processing capacity is about 3.2 milhões de toneladas, such as various oilfield processing enterprises.
Under the background of serious overcapacity of oil well pipes in my country, the development of ABTER STEEL HFW oil casing should highlight the advantages of steelmaking + fabricação de tubos + pipe processing and consistent quality system, differentiated development, and carry out work in the following aspects:
(1) Expand the specifications and output of H40 steel grade oil casing to meet the demand for economical oil casing in low-pressure, low-permeability oil and gas areas.
(2) Expand the specifications and output of M65, L80-1, N80-Q and P110 steel grade oil casing pipes to meet the needs of oilfields to reduce costs and increase efficiency.
(3) Research and develop large-diameter thick-walled K55 steel grade oil casing to meet the needs of specific foreign markets.
(4) Research and develop high anti-extrusion oil casing, such as 80-TT, to meet the demand for economical high anti-extrusion casing in oilfields.
(5) Research and develop corrosion-resistant petroleum casing, such as 80S, 90S and 95S, to meet the demand for economical corrosion-resistant casing in oilfields.