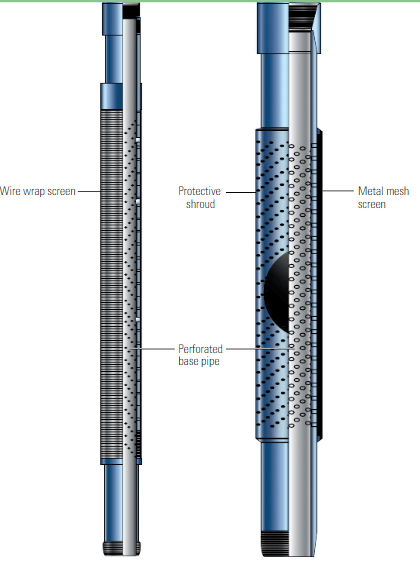
Forschung zur Auswahl von Sand Control Well Screens – Teil 2
April 22, 2023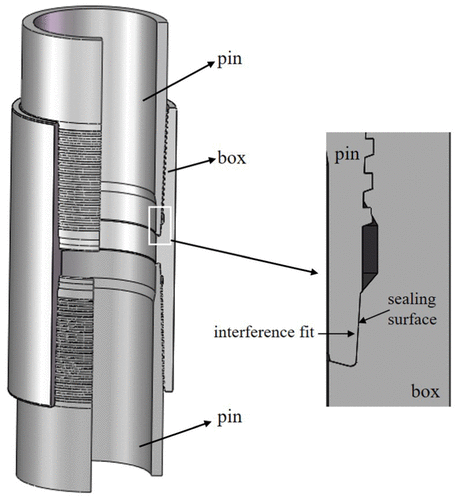
Forschung zur Auswahl von Sand Control Well Screens – Teil 4
April 22, 2023Forschung zur Auswahl von Sandkontrollsieben – Teil 3
Model AlternativeEin Team aus Wissenschaft und Industrie überprüfte die jüngsten Fortschritte bei Bildschirmtests, Interpretation und Modellierung für SAS-Anwendungen. Basierend auf seinen Erkenntnissen, das team hat eine siebauswahlmethode vorgeschlagen, die auf durch labortests verifizierten numerischen und analytischen modellen basiert. Der primäre zweck dieser methode besteht darin, die anzahl physischer SRTs zu eliminieren oder zu reduzieren, die bei der auswahl einer siebgröße und eines siebtyps durchgeführt werden müssen für eine bestimmte Anwendung und um die Wissenschaft der Sandretention besser zu verstehen.
Die Studie verwendete numerische SRT-Simulationen, die mit experimentellen Daten übereinstimmten, um dem Team zu helfen, PSD-Sieb-Kombinationen zu verstehen und in Beziehung zu setzen und die Sandproduktion mit Formationssand-PSD zu korrelieren, bis die Sandproduktion stoppt oder auf Feinstaub beschränkt ist.9 Das Team untersuchte zunächst WWSs, die eine einfachere Geometrie als andere Siebtypen haben, und Simulationen mit der Diskrete-Elemente-Methode durchgeführt (DEM). Dieses numerische Modell beschreibt mechanisches Verhalten, wie Masse,
Figur 5. Simulationen von Sandrückhalteversuchen nach der Diskrete-Elemente-Methode (DEM). Mit dem DEM, Wissenschaftler verfolgen Informationen wie Masse, Geschwindigkeit, Kraft und Impuls um jedes Teilchen innerhalb der Rechendomäne, oder Simulationsbox (links). Die Forscher verwendeten das DEM und einen Molekulardynamiksimulator, um die Leistung in einem Vorpackungsexperiment zu modellieren, indem sie eine Packung polydisperser körniger Kugeln erzeugten (bunte Kugeln) über eine Wire-Wrap-Siebgeometrie (blaue Schicht) und dann Flüssigkeit durch die Packung fließen lassen. Die individuelle Größe und Anzahl der Partikel pro Größe wurden aus der gemessenen Partikelgrößenverteilung der Formationssandprobe erhalten, die für den entsprechenden Versuch verwendet wurde. Anschließend wurden Simulationen nach der Methode der diskreten Elemente verwendet, um die pro Einheitsfläche des Siebs erzeugte Sandmasse für verschiedene Siebgrößen und Partikelgrößenverteilungen zu berechnen. Gegen Ende der polydispersen Simulation, was erforderlich 24 Stunden auf einem Netzwerkcluster mit 48 Prozessoren, Sandpartikel (Rechts, Grün, lila, braun, Blau und weiß) Brücke über die Sieböffnungen (Rosa)
Figur 6. Bestimmung der produzierten Sandmasse und der Partikelgrößenverteilung der gesamten Formation. Die Mondal-Sharma (MS) Das Verfahren verwendet eine Korrelation zwischen der Anzahl von Partikeln mit einem Durchmesser Dp, die durch eine Siebschlitzöffnung mit einer Breite erzeugt werden, W. Die Anzahl der durch das Sieb erzeugten Teilchen jedes Durchmessers wird gezählt und gegen Dp/W aus jeder Simulation aufgetragen (oben). In diesem Fall, Formations-PSDs A und B wurden jeweils in fünf Bin-Größen verteilt (Unterseite, gestrichelt) um die zahlenbasierten Größenverteilungen zu generieren (D1A bis D5A und D1B bis D5B) verwendet, um das Simulationsfeld zu füllen (Unterseite). (Adaptiert von Mondal et al, Referenz 9.)
Figur 7. Partikelgrößenverteilung (PSD) von zurückgehaltenem und produziertem Formationssand. Die PSD der ersten Sandschicht, die auf dem Sieb zurückbleibt (Rot) hat die erwartete Verteilung der Sandpartikel mit Breiten größer als die Schlitzgröße. Die PSD der zweiten Schicht (Grün) nähert sich dem des Formationssandes (Blau). Denn die Größen der auf der zweiten Schicht zurückgehaltenen Partikel werden durch die Porengrößen der ersten Schicht bestimmt, die zurückgehaltenen Teilchen werden schließlich die gleiche PSD und Permeabilität wie der Formationssand haben. (Adaptiert von Chanpura et al, Referenz 13.)
um stabile Partikelbrücken zu bilden, wohingegen der kritischste Parameter, der die Anzahl der produzierten Sandpartikel beeinflusst, das Verhältnis der Schlitzbreite zum Partikeldurchmesser ist. Ähnlich, hohe Flüssigkeitsviskositäten und niedrige Druckgradienten erleichtern die Partikelüberbrückung; ein erhöhter flüssigkeitsdruck erhöht die partikelproduktion, wenn druckgradienten bis zu etwa 2.3 MPa/m [100 psi/ft]. Bei höheren Steigungen, jedoch, es gibt keine solche Abhängigkeit. Als die Ergebnisse aus dem DEM-Modell aufgetragen wurden, Das Team beobachtete eine Potenzgesetzbeziehung. Diese Beziehung wurde durch Auftragen der experimentellen Daten bestätigt, die eine hervorragende Übereinstimmung und konsistente Trends zwischen Modell- und Versuchsergebnissen offenbarten.
Basierend auf dieser neu hergestellten Beziehung, Das Team entwickelte den Mondal-Sharma (MS) Methode, die die Menge und Größe der produzierten Feststoffe verwendet, um die Masse des produzierten Sandes abzuschätzen (Figur 6).
Beim Vergleich der geschätzten Sandmasse, die mit der M-S-Methode produziert wurde, mit der Sandmasse, die in Experimenten produziert wurde, Es wurde eine gute Übereinstimmung gefunden. Die M-S-Methode, die DEM-Simulationsergebnisse verwendet, um eine einfache Korrelation zu entwickeln, kann verwendet werden, um die Masse des produzierten Sandes abzuschätzen, ohne DEM-Simulationen für jede mögliche Kombination aus Sand und Sieb durchzuführen.11 Als nächstes erweiterte das Forschungsteam die Anwendung der M-S-Methode auf einfache quadratische Maschen (PSM) Bildschirme, fast die gleichen Ergebnisse erzielen. Einige Schlussfolgerungen aus WWS- und PSM-Simulationen beinhalten die folgenden:• Simulationen sind in der Lage, die Sandmasse abzuschätzen, die für eine gegebene PSD und Siebgröße produziert wird. • Die Simulationsergebnisse stimmen stark mit denen aus sorgfältig kontrollierten Prepack-Experimenten überein. • Simulationen zeigen, dass die Sandmasse pro Einheit Siebfläche und pro Einheit produziert wird Die offene Strömungsfläche ist bei einschichtigen PSMs größer als bei Schlitzgeometrien derselben Nennleistung und der entsprechenden standardmäßigen offenen Strömungsfläche. • Simulationen zeigen, dass das Verhältnis von Drahtdicke zu Öffnungsgröße ein Schlüsselfaktor zu sein scheint, der zu der Erhöhung beiträgt Masse der Sandproduktion aus einschichtigen PSMs.
12Die Forscher wandten sich dann analytischen Lösungen und Monte-Carlo-Simulationen zu, um die Sandproduktion durch WWSs und PSM-Siebe unter Aufschlämmungstestbedingungen vorherzusagen. Ihre Ergebnisse zeigten, dass die analytische Lösung und die numerische Simulation hervorragend übereinstimmten. Das Team zeigte, dass die vorgeschlagenen Methoden in der Lage waren, sowohl die Massen- als auch die Größenverteilung des produzierten Feststoffs in einer SRT vom Schlammtyp abzuschätzen, unter Berücksichtigung der vollen PSD von Formationssand. Das zeigten auch Simulationen, mit Ausnahme eines Handy-Bußgeldproblems, Die Sandproduktion wird vernachlässigbar, sobald die Schlitzöffnung mit Partikeln bedeckt ist, die größer als die Öffnung sind (Figur 7).
Wie im Fall des Modellierens von vorverpackten SRTs, Die vorgeschlagenen Methoden können verwendet werden, um die Sandproduktion in SRTs vom Schlammtyp für verschiedene Siebgrößen abzuschätzen, wodurch die auswahl der siebgröße basierend auf einem akzeptablen niveau der sandproduktion ermöglicht wird. Die endgültige Siebauswahl kann dann durch ein SRT vom Slurry-Typ bestätigt werden.13 Die Ergebnisse zeigten, dass mehr als 90% der gesamten Sandproduktion nach Masse während der Bildung der ersten Partikelschicht auf dem Sieb auftritt und dass sich der PSD des zurückgehaltenen Sandes dem des Formationssandes annähert, nachdem sich einige Sandschichten auf dem Sieb angesammelt haben. Die Ergebnisse zeigten auch, dass die Sandmasse, die während der Bildung der ersten Partikelschicht auf dem Sieb erzeugt wird, unabhängig von der Form der PSD für Körner kleiner als die Öffnungs-Porengröße ist und von der Form bestimmt wird
Forschung zur Auswahl von Sand Control Well Screens – Teil 1
Forschung zur Auswahl von Sand Control Well Screens – Teil 2
Forschung zur Auswahl von Sand Control Well Screens – Teil 3
Forschung zur Auswahl von Sand Control Well Screens – Teil 4