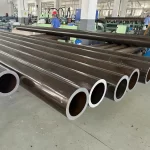
Auswirkungen von körnigem Bainit und polygonalem Ferrit auf API
September 13, 2024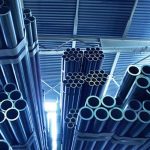
Hochtemperatur- und hochdruckbeständige Leitungsrohre, Stahl und Rohre von Schlüsseltechnologien
September 21, 2024Einführung:
Leitungsrohre sind ein wichtiges, aber oft übersehenes Stück Infrastruktur, das das Rückgrat unserer Energieverteilungssysteme bildet. Durch den Transport von Flüssigkeiten und Gasen über weite Strecken, Diese Metallrohre treiben unsere Wirtschaft und unsere Lebensweise an. Jedoch, Die Anforderungen an die strukturelle Integrität von Leitungsrohren sind immens – sie müssen sowohl dem Innendruck der sich im Inneren bewegenden Flüssigkeiten als auch den äußeren Kräften standhalten, die von den umgebenden Böden über viele Jahrzehnte hinweg ausgeübt werden. Dies stellt hohe Anforderungen an die Herstellung und Konstruktion von Leitungsrohren, um die öffentliche Sicherheit und Betriebssicherheit zu gewährleisten.
In diesem Bericht werden die strukturellen mechanischen und metallurgischen technischen Überlegungen untersucht, die der Herstellung von Leitungsrohren zugrunde liegen. Zu den wichtigsten Schwerpunktbereichen gehören gemeinsame Leitungsrohre Materialien, Dicken- und Geometriedesigns, Schweiß- und Beschichtungsverfahren, und Qualitätskontrollmaßnahmen. Ziel ist es, einen Einblick in die Konstruktion von Leitungsrohren zu geben, um den immensen und multidirektionalen Belastungen standzuhalten, denen sie im Untergrund ausgesetzt sind.
Materialien für Leitungsrohre:
Die Wahl des Materials ist eine grundlegende Entscheidung bei der Konstruktion von Leitungsrohren, da es kritische Eigenschaften wie die Festigkeit, Duktilität, und Korrosion Widerstand. Kohlenstoffstähle wurden aufgrund ihrer Verfügbarkeit und Wirtschaftlichkeit traditionell verwendet. Jedoch, Fortschrittliche Sorten von legierten und rostfreien Stählen haben Kohlenstoffsorten für viele Anwendungen zunehmend ersetzt:
- Kohlenstoffstähle: Wird für Niederdruck-Verteilungsleitungen verwendet. Kompositionen enthalten 0.15-0.3% Carbon. Bieten Sie moderate Festigkeit zu geringen Kosten. Jedoch, Eingeschränkte Korrosionsbeständigkeit führt zum Einsatz von Schutzbeschichtungen.
- Legierte Stähle: Wird für Hochdruckleitungen verwendet. Legierungselemente wie Chrom, Molybdän verbessert die Festigkeitseigenschaften erheblich. Beliebte Sorten sind X65, X70, X80 mit minimalen Streckgrenzen bis zu 80 KSI. Bieten ein gutes Verhältnis von Festigkeit zu Gewicht.
- Rostfreie Stähle: Einsatz für extrem korrosive Anwendungen mit Schwefelwasserstoff oder Kohlendioxid. Stähle wie 316L und 904L haben eine ausgezeichnete Korrosionsbeständigkeit durch einen Chromgehalt von 16-25%. Jedoch, Reduzierte Umformbarkeit erfordert teurere Schweißprozesse.
Leitungsrohrstahl muss Spezifikationen in Bezug auf mechanische Eigenschaften wie Zugfestigkeit und Schlagzähigkeiten erfüllen. Die Produktion wird streng kontrolliert, um eine gleichbleibende Metallurgie in jedem wärmebehandelten Rohr zu gewährleisten.
Design der Rohrdicke:
Die Dicke von Leitungsrohrwänden wird bewusst auf der Grundlage von Faktoren wie Innendrücken festgelegt, Betriebstemperaturen, Bodenbedingungen, und Designleben. Die Rohrdruckwerte werden in psi oder bar dargestellt, wo Rohre mit höherer Nennleistung dickeres Material erfordern, um größeren Schnittgrößen sicher standzuhalten.
Zu den Überlegungen zur Dicke gehören:
- Eindämmung des Drucks: Die minimal erforderliche Dicke pro Code wird anhand von Druckbehältergleichungen berechnet, die Spannungen durch interne und manchmal externe Lasten berücksichtigen. Höhere Drücke erfordern dickere Querschnitte.
- Handhabung/Installation: Das Rohr muss ausreichend steif sein, um Beschädigungen und Verformungen während des Transports zu widerstehen, besaitung, Biegen, und Schweißarbeiten. Dickere Wände tragen zur Aufrechterhaltung der Rohrintegrität bei.
- Korrosions-Aufmaß: Ein zusätzliches Dickenmaß berücksichtigt alle Metallverluste, die während der Lebensdauer durch äußere Korrosions- oder Erosionseffekte zu erwarten sind. typisch 0.09-0.18 Zoll für unterirdische Rohre.
- Überlegungen zum Gewicht: Zu dicke Wände erhöhen die Transport- und Installationskosten erheblich. Strukturelle Analysen zielen darauf ab, das für die Sicherheit erforderliche Mindestmaß zu verwenden.
Die richtige Wandstärke stellt sicher, dass Leitungsrohre einem Druck von über 50+ Jahre unter Tage bei gleichzeitiger Minimierung des Materialeinsatzes und der Installationskosten. Zerstörungsfreie Prüfung auf Gleichmäßigkeit der Dicke.
Rohr-Geometrie:
Mehr als Materialauswahl und Dicke, Eine präzise Rohrgeometrie ist entscheidend, um mechanischen und hydraulischen Belastungen im Betrieb standzuhalten. Enge Maßtoleranzen werden eingehalten für:
- Durchmesser: Die Nennweiten reichen von 2-60 Zoll für die meisten Übertragungsleitungen. Toleranzen von +0.125 Zoll sorgen für ein gleichmäßiges Innenvolumen.
- Rundheit: Ovalitäten kleiner als 1% der Nennweite pro Code. Unrundheit erzeugt unerwünschte Druckspitzen.
- Geradheit: Die Abweichung von einer geraden Mittellinie muss unter den allgemein akzeptierten Werten auf der Grundlage der Rohrlänge bleiben. Knicke oder Kräuselungen schwächen das Rohr strukturell.
- Endbearbeitungen: Abgeschrägte Enden an den meisten Rohren erleichtern das Stumpfschweißen. Es werden auch quadratisch geschnittene Enden verwendet, erfordert eine zeitaufwändigere Vorbereitung vor dem Zusammenfügen.
- Oberflächengüte: Gewalzte oder hergestellte Oberflächen unterhalb eines GivenRa/Ry-Schwellenwerts gemäß API-Spezifikation. Glattere Oberflächen erleichtern das Auftragen der Beschichtung und vermeiden Defekte.
- Toleranzen: Alle Maßprüfungen erfolgen mit Mikrometern und anderen Werkzeugen, um sicherzustellen, dass die Rohre den Industriestandards wie ANSI entsprechen, API- oder ASTM-Kriterien.
Die Einhaltung strenger geometrischer Spezifikationen ist entscheidend für eine zuverlässige Feldleistung von Leitungsrohren über viele Druckzyklen hinweg.
Schweißen von Leitungsrohren:
Die beiden vorherrschenden Verbindungstechniken für Leitungsrohre erfordern eine sorgfältige technische Umsetzung, um die Ziele der strukturellen Integrität zu erreichen.
Längs- oder Spiralschweißen: Wird für die meisten Anwendungen mit großem Durchmesser verwendet, Hochdruck-Stahlrohrleitungen. Dabei werden gewalzte Bänder oder Platten zu zylindrischen Röhren mit automatisierten Schweißmaschinen. Dadurch entstehen Rohrlängen bis zu 60 Füße und Durchmesser bis in den 60-Zoll-Bereich. Vorteile sind kontinuierlichere Rohrqualitäten und höhere Feldproduktionsraten. Jedoch, Erreichen einer vollständigen Fugendurchdringung und Verschmelzung über große, Verjüngte Kanten stellen technische Herausforderungen dar.
Stumpfschweißen: Wird häufig für kleinere Durchmesser eingesetzt, Sammelleitungen mit niedrigerem Druck. Dabei werden Rohrenden aneinander gestoßen und konzentrierte Hitze so geleitet, dass die beiden Verbindungsbereiche vollständig miteinander verschmelzen. Obwohl kleinere Durchmesser von 2-16 Zoll sind leichter unterzubringen, Es entstehen Diskontinuitäten an jedem Schweißpunkt, die getestet werden müssen. Ausrichtung ist wichtig.
Roboter- und automatische Schweißtechniken wie SAW (Unterpulverschweißen) Förderung der gemeinsamen Qualitätssicherung und Wiederholbarkeit bei hohen Arbeitsgeschwindigkeiten. Noch, Jede Schweißnaht wird zerstörungsfrei mittels Röntgen bewertet, Ultraschall-, oder röntgenologische Methoden, um sicherzustellen, dass die Struktur- und Druckeindämmungsfähigkeiten den geltenden Sicherheitsvorschriften für Pipelines entsprechen.
Beschichtungen für den Korrosionsschutz:
Freiliegende Kohlenstoff- und niedriglegierte Stähle sind auf Schutzbeschichtungen angewiesen, um die Rohrintegrität in korrosiven unterirdischen oder untergetauchten Umgebungen über viele Jahrzehnte hinweg zu erhalten. Gängige Korrosionsschutzmethoden sind:
Schmelzgebundenes Epoxid (FBE): Wärmegehärtetes Epoxidpulver ergibt eine harte, Undurchlässige Schale, die direkten Erdverschüttungen und kathodischen Schutzanwendungen standhält. Als Flüssigkeit auf vorgewärmte Rohre aufgetragen, Es haftet hartnäckig. Wird häufig für Übertragungsleitungen zum Transport von Erdgas eingesetzt, Öl, und andere Rohstoffe.
Dreilagiges Polyurethan: Mehrere Schichten aus flüssigem Polyurethan, Klebstoff, und Decklack bieten Flexibilität mit ähnlichem Schutz wie schmelzgebundenes Epoxidharz für einige Sauergasleitungen. Bessere Dehnungseigenschaften ermöglichen thermische Zyklen.
Beschichtung mit Betongewicht: Geschlämmtes zementartiges Material, das auf nassen FBE-Beschichtungen zirkuliert, ballt sich zu einer Schutzhülle zusammen, die auch Rohrvibrationen während der Verfüllung dämpft und Masse für die Auftriebskontrolle vor der Küste hinzufügt.
Spezielle Legierungen und unkonventionelle Beschichtungen ermöglichen die Aufnahme von Schwefelwasserstoff in Pipelines, Kohlendioxid und abrasive Schlämme sowie. Bei der Auswahl der Beschichtung wird die Wirtschaftlichkeit berücksichtigt, Herausforderungen bei der Anwendung, und langfristige Abschirmfähigkeit gegen Korrosion.
Qualitätssicherung in der Fertigung:
Aufgrund von Aufgaben der öffentlichen Sicherheit und des Umweltschutzes, Leitungsrohre werden während der gesamten Herstellung strengen Qualitätskontrollen unterzogen. Zu den wichtigsten Phasen der Qualitätssicherung gehören:
- Walzprüfung von Stahlzusammensetzungen, Festigkeiten und Schlageigenschaften an Proben aus jeder Hitze.
- Zerstörungsfreie Prüfung des Rohrkörpers mittels Ultraschall, Magnetisches Teilchen, oder Röntgenuntersuchungen, um nach Unvollkommenheiten zu suchen.
- Geometrische Maße für Durchmesser, Wandstärken, Geradheit und Ovalitäten elektronisch erfasst.
- Visuelle und mechanische Prüfungen von Schweißraupen und Wärmeeinflusszonen mittels Eindring- und Biegeprüfungen.
- Hydrotesting von fertigen Rohrsträngen bei erhöhten Drücken, oft 1.5 multipliziert mit dem MAOP.
- Schichtdickenkontrollen und Lebensdauererkennungstests auf Nadellöcher oder Bereiche mit fehlender FBE.
- Rückverfolgbarkeit von Rohraufzeichnungen auf die ursprünglichen Wärmezahlen für eine chargenweise Fehleranalyse, falls erforderlich.
Qualitätsmanagementsysteme auf Basis von ISO, CSA- oder API-Standards treiben die Fertigung mit Null-Fehler-Mentalität voran. Dies bietet die Gewissheit, dass die Leitungsrohre dem Druck über einen längeren Untertageeinsatz sicher standhalten.
Das Rückgrat der Infrastruktur
Stellen Sie sich die riesigen Netzwerke von Pipelines vor, die sich durch die Länder schlängeln, Transport von lebenswichtigen Ressourcen wie Öl, Gas, und Wasser. Diese Pipelines sind die unbesungenen Helden der modernen Infrastruktur, Und das Herzstück sind Metallrohre, Entwickelt mit Präzision und Festigkeit, um verschiedenen Umwelteinflüssen standzuhalten.
Die Kunst der Rohrherstellung
Die Reise eines Metallrohrs beginnt mit den Rohstoffen, Typischerweise Stahl, die aufgrund ihrer Haltbarkeit und Festigkeit ausgewählt wird. Der Herstellungsprozess umfasst mehrere Schritte, Jedes ist entscheidend für die Gewährleistung der Integrität und Leistung der Leitung.
- Materialauswahl und -aufbereitung: Alles beginnt mit der Auswahl der richtigen Stahlsorte. Anschließend wird der Stahl zu Blechen oder Coils verarbeitet, Bereit, in Rohre umgewandelt zu werden.
- Bildung: Hier passiert die Magie. Der Stahl wird durch Verfahren wie Walzen oder Extrudieren in eine zylindrische Form gebracht. Es ist faszinierend zu beobachten, wie sich flache Bleche in runde Rohre verwandeln!
- Schweißen: Um sicherzustellen, dass das Rohr seine Form behält, die Kanten sind miteinander verschweißt. Es gibt verschiedene Schweißtechniken, wie z.B. elektrisches Widerstandsschweißen (ERW) oder Unterpulverschweißen (SÄGE), jeweils basierend auf dem Verwendungszweck des Rohrs ausgewählt.
- Größenbestimmung und Formgebung: Nach dem Schweißen, Das Rohr wird auf genaue Abmessungen dimensioniert. Dieser Schritt ist entscheidend, um sicherzustellen, dass das Rohr perfekt in die vorgesehene Anwendung passt.
- Wärmebehandlung: Um die mechanischen Eigenschaften des Rohrs zu verbessern, Es wird einer Wärmebehandlung unterzogen. Bei diesem Prozess wird das Rohr auf eine bestimmte Temperatur erhitzt und dann abgekühlt, was seine Festigkeit und Flexibilität verbessert.
- Inspektion und Prüfung: Qualitätskontrolle ist oberstes Gebot. Die Rohre werden strengen Tests unterzogen, einschließlich Ultraschallprüfung und hydrostatischer Prüfung, um sicherzustellen, dass sie den Industriestandards entsprechen und dem Druck standhalten, dem sie vor Ort ausgesetzt sind.
Strukturmechanik: Die Wissenschaft der Stärke
Jetzt, Lassen Sie uns über die Strukturmechanik sprechen, die bei der Konstruktion dieser Metallwunder eine Rolle spielt. Im Kern, Es geht darum zu verstehen, wie sich Materialien unter verschiedenen Kräften und Bedingungen verhalten.
- Beanspruchung und Dehnung: Rohre müssen einem immensen Druck standhalten, Speziell in Öl- und Gasanwendungen. Ingenieure analysieren Stress (Kraft pro Flächeneinheit) und Dehnung (Verformung) um sicherzustellen, dass das Rohr diese Kräfte bewältigen kann, ohne zu versagen.
- Knicken und Einklappen: Stell dir vor, ein Strohhalm bricht zusammen, wenn du zu stark saugst. Rohre sind unter äußerem Druck ähnlichen Risiken ausgesetzt. Ingenieure entwerfen Rohre, die Knicken und Einstürzen widerstehen, Verwendung mathematischer Modelle und Simulationen, um solche Ausfälle vorherzusagen und zu verhindern.
- Ermüdung und Bruch: Mit der Zeit, Wiederholte Beanspruchung kann dazu führen, dass Materialien geschwächt und gebrochen werden. Durch die Untersuchung von Müdigkeit, Ingenieure können Rohre entwerfen, die länger halten, auch bei konstanten Druckzyklen.
Entwerfen für die reale Welt
Bei der Konstruktion von Metallrohren geht es nicht nur darum, Zahlen zu knacken. Es geht darum, reale Bedingungen wie Temperaturschwankungen zu berücksichtigen, korrosive Umgebungen, und seismische Aktivität. Ingenieure verwenden fortschrittliche Software, um diese Bedingungen zu simulieren, Sicherstellung, dass die Rohre in jedem Szenario zuverlässig funktionieren.
Innovationen im Rohrdesign
Der Bereich der Rohrherstellung entwickelt sich ständig weiter, mit Innovationen zur Verbesserung von Leistung und Nachhaltigkeit. Zum Beispiel, Forscher erforschen neue Materialien und Beschichtungen, um die Korrosionsbeständigkeit zu verbessern, was in rauen Umgebungen ein großes Problem darstellt.
Der Vergleich zwischen den Kriechversuchsdaten und den Simulationsergebnissen bei drei verschiedenen Temperaturen ist in dargestellt: Die unbesungenen Helden
Der Vergleich zwischen den Kriechversuchsdaten und den Simulationsergebnissen bei drei verschiedenen Temperaturen ist in dargestellt:
Die Entwicklung und Herstellung von Leitungsrohren, die über Jahrzehnte als strukturelle Leitungen für Flüssigkeiten dienen, erfordert das Verständnis der anspruchsvollen interaktiven Belastungen, denen sie ausgesetzt sind, und die Umsetzung einer intelligenten Materialauswahl, Präzise Fertigungstechniken, und Qualitätskontrollprotokolle. Der Einsatz von Strukturanalysen und metallurgischen technischen Prinzipien kommt Herstellern und Endverbrauchern zugute, indem sichergestellt wird, dass die Integrität der Transportpipelines sowohl unter internem Druck als auch unter äußeren Kraftbelastungen ununterbrochen bleibt. Kontinuierliche Verbesserungen bei den Stahlsorten, Fähigkeiten der zerstörungsfreien Prüfung, Und Korrosionsschutzmethoden werden die Zuverlässigkeit der unterirdischen Infrastruktur, die Energieressourcen zu Gesellschaften weltweit transportiert, weiter verbessern. Metallrohre sind vielleicht nicht das glamouröseste Thema, Aber sie sind für unser tägliches Leben unerlässlich. Vom Transport von Öl und Gas bis zur Lieferung von sauberem Wasser, Sie spielen eine wichtige Rolle in einer modernen Infrastruktur. Das Verständnis der strukturellen Mechanik und des Designs hinter diesen Rohren gibt uns eine tiefere Wertschätzung für die technischen Meisterleistungen, die dafür sorgen, dass unsere Welt reibungslos funktioniert.