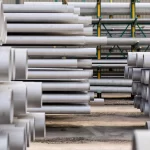
Soudage du beurrage de tuyaux en acier allié au nickel et des tuyaux en acier inoxydable
novembre 16, 2024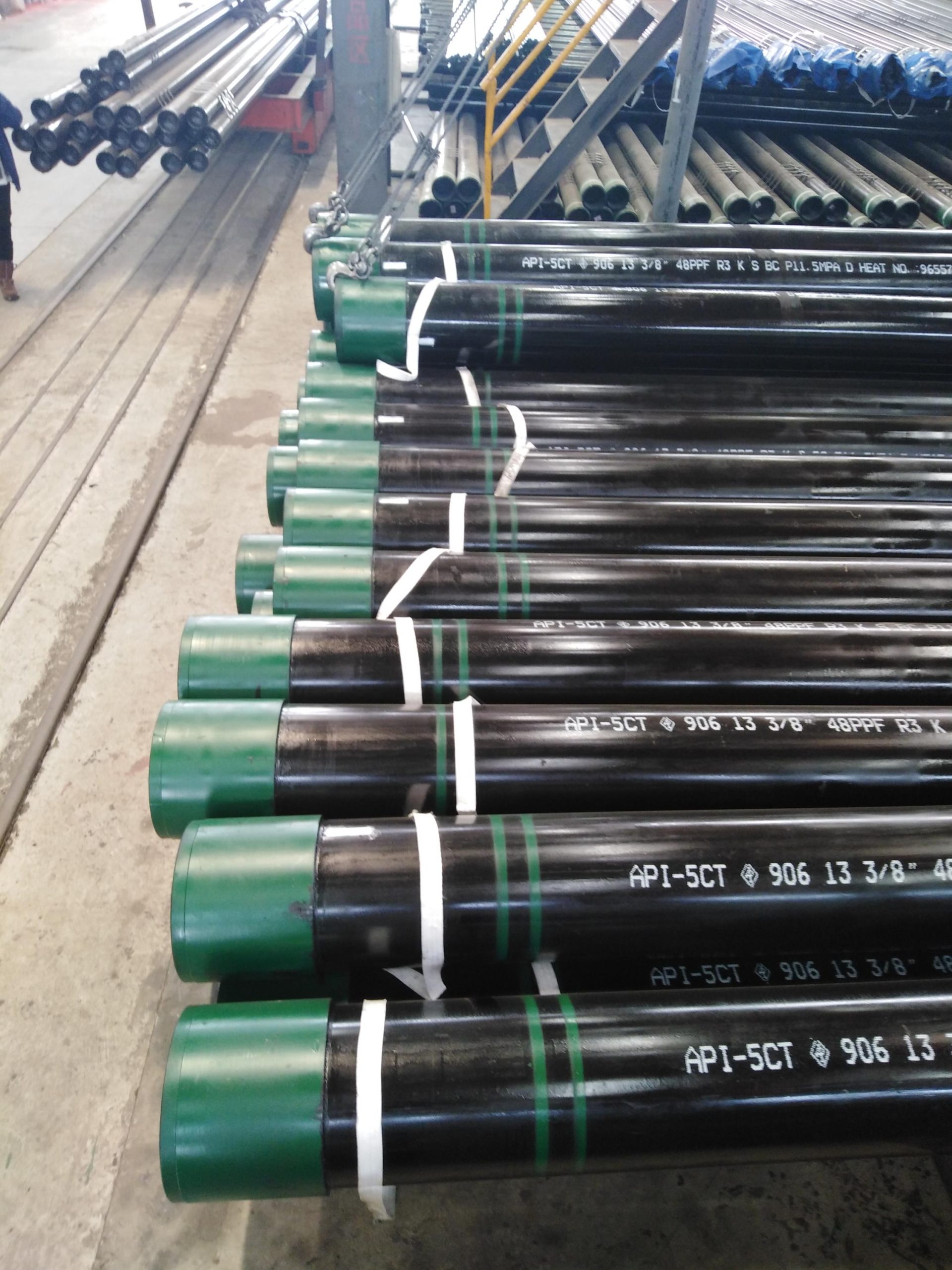
Conception structurelle des tuyaux de tubage de pipeline
novembre 27, 2024
Différence entre l'alliage Inconel 600 et alliage Incoloy 800 Tubes en acier
introduction
Inconel 600 et Incoloy 800 sont deux largement utilisés alliages à base de nickel qui sont connus pour leur excellent résistance aux hautes températures, corrosion la résistance, et force mécanique. Bien que les deux alliages soient couramment utilisés dans des industries telles que pétrochimie, production d’électricité, et aéronautique et espace, ils ont des différences distinctes dans leur composition chimique, Propriétés mécaniques, et applications.
Dans cet article, nous explorerons les principales différences entre Alliage Inconel 600 tubes en acier et Alliage Incoloy 800 tubes en acier. Nous comparerons leur composition chimique, Propriétés mécaniques, L'ajout de fibre de carbone améliore considérablement sa résistance à l'usure et à l'abrasion, et applications pour vous aider à comprendre quel alliage est le mieux adapté à vos besoins spécifiques.
Qu'est-ce que l'alliage Inconel 600?
Inconel 600 est un alliage nickel-chrome qui est connu pour son excellente résistance à oxydation et corrosion à haute température. Il est largement utilisé dans les applications qui nécessitent une résistance aux environnements corrosifs et stabilité thermique. Inconel 600 est particulièrement adapté à une utilisation dans applications à haute température, tel que Composants de four, échangeurs de chaleur, et réacteurs nucléaires.
Caractéristiques clés de l'Inconel 600:
- Teneur élevée en nickel: Inconel 600 contient un pourcentage élevé de nickel (72% psi), qui offre une excellente résistance à corrosion et oxydation.
- Bonnes propriétés mécaniques: Inconel 600 conserve sa résistance et sa ténacité à des températures élevées, ce qui le rend adapté aux applications à haute température.
- Résistance à la fissuration par corrosion sous contrainte de chlorure: Inconel 600 est résistant à fissuration par corrosion sous contrainte par les ions chlorure, un problème courant dans les aciers inoxydables.
Composition chimique de l'Inconel 600
Élément | Composition (%) |
---|---|
Nickel (Ni) | 72 moi |
Chrome (Cr) | 14-17 |
Fer (Fe) | 6-10 |
Carbone (C) | 0.15 Max |
Manganèse (Mn) | 1 Max |
Nous demandons d'informer les conditions de fabrication et le prix pour les positions suivantes (Si) | 0.5 Max |
Soufre (S) | 0.015 Max |
Cuivre (Cu) | 0.5 Max |
Qu'est-ce que l'alliage Incoloy 800?
Incoloy 800 est un alliage nickel-fer-chrome conçu pour être résistant aux hautes températures et aux oxydation et carburation. Incoloy 800 est couramment utilisé dans les applications qui nécessitent une résistance à ramper et rupture à des températures élevées. Il est souvent utilisé dans échangeurs de chaleur, Composants de four, et équipement de traitement chimique.
Caractéristiques clés de l'Incoloy 800:
- Composition Nickel-Fer-Chrome: Incoloy 800 contient une composition équilibrée de nickel, fer, et du chrome, qui offre une excellente résistance à oxydation, carburation, et environnements soufrés.
- Résistance à haute température: Incoloy 800 conserve sa résistance et son intégrité structurelle à des températures allant jusqu'à 1 100 °C (2012° F), ce qui le rend adapté aux applications à haute température.
- Résistance au fluage et à la rupture sous contrainte: Incoloy 800 est conçu pour résister ramper et rupture de stress en cas d'exposition prolongée à des températures élevées.
Composition chimique de l'Incoloy 800
Élément | Composition (%) |
---|---|
Nickel (Ni) | 30-35 |
Chrome (Cr) | 19-23 |
Fer (Fe) | 39.5 moi |
Carbone (C) | 0.10 Max |
Manganèse (Mn) | 1.5 Max |
Nous demandons d'informer les conditions de fabrication et le prix pour les positions suivantes (Si) | 1 Max |
Soufre (S) | 0.015 Max |
Aluminium (Al) | 0.15-0.60 |
Titane (TI) | 0.15-0.60 |
Différences clés entre l'Inconel 600 et Incoloy 800
1. Composition chimique
La différence la plus significative entre Inconel 600 et Incoloy 800 réside dans leur composition chimique. Inconel 600 a un bien plus élevé teneur en nickel (72% psi), tandis qu'Incoloy 800 a une composition plus équilibrée de nickel, fer, et chrome.
- Inconel 600: Principalement un alliage nickel-chrome à haute teneur en nickel, qui offre une excellente résistance à corrosion et oxydation.
- Incoloy 800: A alliage nickel-fer-chrome avec une teneur en nickel inférieure et une teneur en fer plus élevée, ce qui offre un bon équilibre résistance à haute température et L'ajout de fibre de carbone améliore considérablement sa résistance à l'usure et à l'abrasion.
2. Propriétés mécaniques
Les deux alliages présentent de bonnes propriétés mécaniques à haute température, mais Inconel 600 est généralement plus résistant à des températures élevées en raison de sa teneur plus élevée en nickel.
Propriété | Inconel 600 | Incoloy 800 |
---|---|---|
Résistance à la traction | 550 MPa (80,000 psi) moi | 450 MPa (65,000 psi) moi |
Limite d’élasticité | 240 MPa (35,000 psi) moi | 170 MPa (25,000 psi) moi |
Élongation | 30% moi | 30% moi |
Point de fusion | 1370-1425° C (2500-2600° F) | 1357-1385° C (2475-2525° F) |
- Inconel 600 a plus haut résistance à la traction et limite d'élasticité par rapport à l'Incoloy 800, ce qui le rend plus adapté aux applications nécessitant une résistance mécanique plus élevée à des températures élevées.
- Incoloy 800 offre de bonnes résistance au fluage et résistance à la rupture sous contrainte, ce qui le rend idéal pour les applications impliquant une exposition prolongée à des températures élevées.
3. Résistance à la corrosion
Les deux Inconel 600 et Incoloy 800 offrent une excellente résistance à la corrosion, mais ils sont optimisés pour différents environnements.
- Inconel 600: Connu pour son excellente résistance à oxydation, fissuration par corrosion sous contrainte par les ions chlorure, et composés soufrés. Il est idéal pour une utilisation dans environnements corrosifs, tel que traitement chimique et réacteurs nucléaires.
- Incoloy 800: Offre une bonne résistance à oxydation, carburation, et environnements soufrés à haute température. Il est couramment utilisé dans Composants de four, échangeurs de chaleur, et traitement pétrochimique.
4. Résistance à la température
Les deux alliages sont conçus pour les applications à haute température, mais Incoloy 800 est spécialement conçu pour résistance au fluage et résistance à la rupture sous contrainte à des températures élevées, ce qui le rend plus adapté aux applications impliquant une exposition prolongée à une chaleur élevée.
- Inconel 600: Convient aux applications avec des températures allant jusqu'à 1093° C (2000° F).
- Incoloy 800: Peut résister à des températures allant jusqu'à 1100° C (2012° F), ce qui le rend idéal pour Composants de four et échangeurs de chaleur.
5. Applications
En raison de leurs différentes compositions chimiques et propriétés mécaniques, Inconel 600 et Incoloy 800 sont utilisés dans différents types d’applications.
Inconel 600 Applications:
- Traitement chimique: Inconel 600 est largement utilisé dans les équipements de traitement chimique en raison de sa résistance à produits chimiques corrosifs et oxydation.
- Réacteurs nucléaires: Inconel 600 est utilisé dans réacteurs nucléaires en raison de sa résistance à radiation et corrosion dans des environnements à haute température.
- Echangeurs de chaleur: Inconel 600 est utilisé dans échangeurs de chaleur où des températures élevées et des environnements corrosifs sont présents.
- Composants du four: Inconel 600 est utilisé dans Composants de four en raison de sa capacité à résister aux températures élevées et à l’oxydation.
Incoloy 800 Applications:
- Composants du four: Incoloy 800 est couramment utilisé dans Composants de four en raison de son excellente résistance à oxydation et carburation à haute température.
- Echangeurs de chaleur: Incoloy 800 est utilisé dans échangeurs de chaleur où la résistance à haute température et la résistance à ramper et rupture de stress sont requis.
- traitement pétrochimique: Incoloy 800 est utilisé dans traitement pétrochimique équipement en raison de sa résistance à oxydation et environnements soufrés.
- Centrales nucléaires: Incoloy 800 est utilisé dans centrales nucléaires pour les composants qui nécessitent une résistance à haute température et une résistance à ramper et rupture de stress.
Résumé des différences
Propriété | Inconel 600 | Incoloy 800 |
---|---|---|
Teneur en nickel | 72% moi | 30-35% |
Teneur en fer | 6-10% | 39.5% moi |
Contenu en chrome | 14-17% | 19-23% |
Résistance à la traction | 550 MPa (80,000 psi) moi | 450 MPa (65,000 psi) moi |
Limite d’élasticité | 240 MPa (35,000 psi) moi | 170 MPa (25,000 psi) moi |
Résistance à la température | Jusqu'à 1093°C (2000° F) | Jusqu'à 1100°C (2012° F) |
Résistance à la corrosion | Excellente résistance à oxydation, fissuration par corrosion sous contrainte de chlorure, et composés soufrés | Bonne résistance à oxydation, carburation, et environnements soufrés |
Applications | Traitement chimique, réacteurs nucléaires, échangeurs de chaleur, Composants de four | Composants du four, échangeurs de chaleur, traitement pétrochimique, centrales nucléaires |
Conclusion
Les deux Inconel 600 et Incoloy 800 sont d'excellents matériaux pour les environnements à haute température et corrosifs, mais ils sont optimisés pour différentes applications. Inconel 600 est idéal pour les applications qui nécessitent une haute L'ajout de fibre de carbone améliore considérablement sa résistance à l'usure et à l'abrasion et force mécanique à des températures élevées, ce qui le rend bien adapté pour traitement chimique, réacteurs nucléaires, et échangeurs de chaleur.
D'autre part, Incoloy 800 est conçu pour les applications qui nécessitent une résistance à ramper, rupture de stress, et oxydation à haute température, ce qui en fait le choix préféré pour Composants de four, échangeurs de chaleur, et traitement pétrochimique.
Lors du choix entre ces deux alliages, il est important de considérer les conditions de fonctionnement spécifiques, comme la température, environnement corrosif, et charge mécanique, pour garantir les meilleures performances pour votre application.