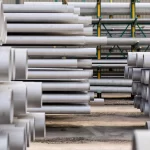
لحام أنابيب الصلب وسبائك النيكل بالزبدة وأنابيب الفولاذ المقاوم للصدأ
يوليو 16, 2024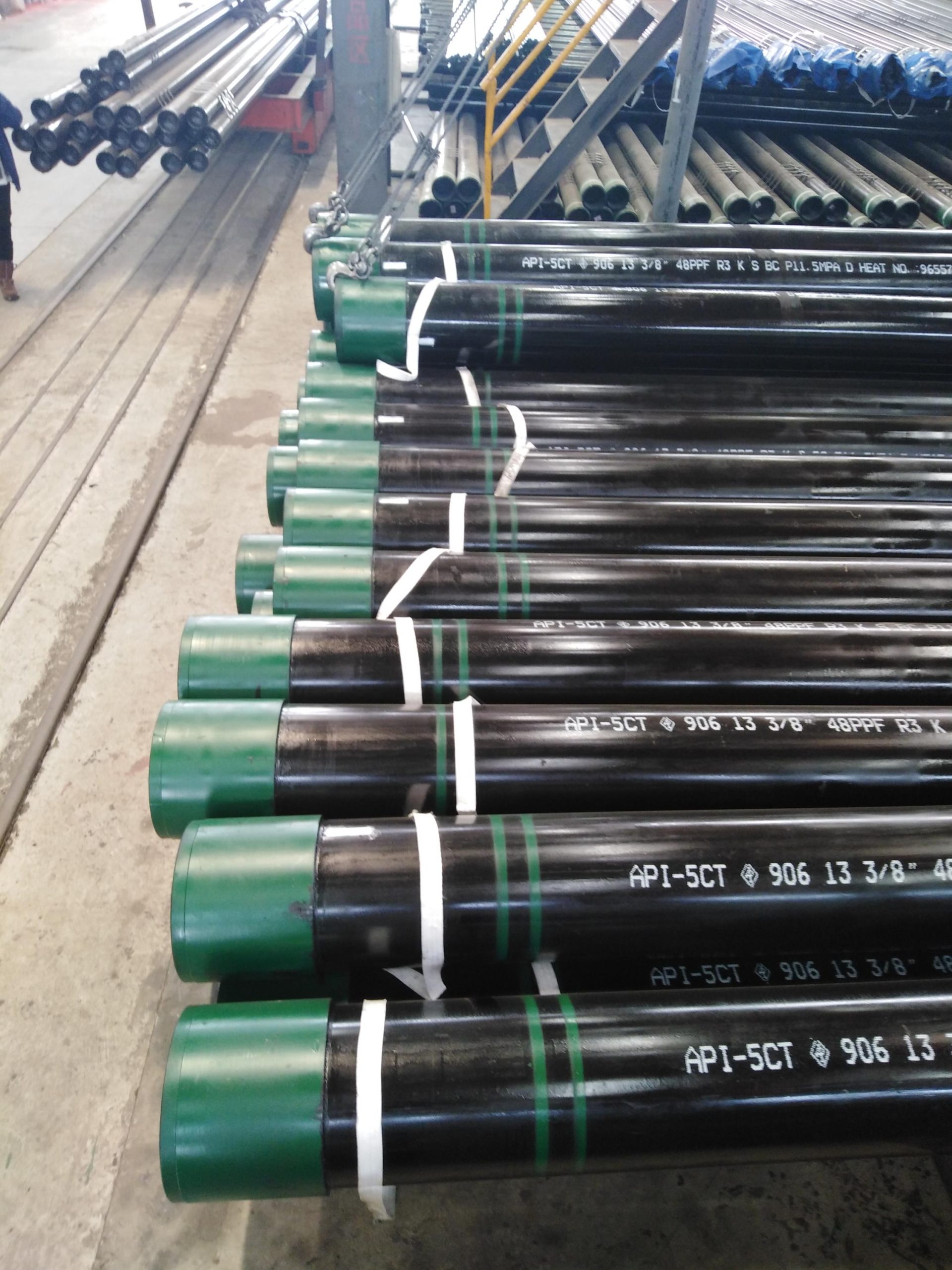
التصميم الهيكلي لأنابيب التغليف
يوليو 27, 2024
الفرق بين سبائك إنكونيل 600 وسبائك إنكولوي 800 أنابيب الصلب
مقدمة
إنكونيل 600 و إنكولوي 800 وهما تستخدم على نطاق واسع سبائك أساسها النيكل المعروفة بتميزها مقاومة درجات الحرارة العالية, تآكل مقاومة, و القوة الميكانيكية. في حين يتم استخدام كلا السبائك بشكل شائع في صناعات مثل البتروكيماويات, توليد الطاقة الكهربائية, و الطيران, لديهم اختلافات واضحة في التركيب الكيميائي, الخواص الميكانيكية, و تطبيقات.
في هذه المقالة, سوف نستكشف الاختلافات الرئيسية بين سبائك إنكونيل 600 أنابيب الصلب و سبيكة إنكولوي 800 أنابيب الصلب. سوف نقوم بمقارنة بهم التركيب الكيميائي, الخواص الميكانيكية, المقاومة للتآكل, و تطبيقات لمساعدتك على فهم أي سبيكة هي الأنسب لاحتياجاتك الخاصة.
ما هي سبائك إنكونيل 600?
إنكونيل 600 هو سبائك النيكل والكروم المعروف بمقاومته الممتازة الاكسده و تآكل في درجات حرارة عالية. ويستخدم على نطاق واسع في التطبيقات التي تتطلب مقاومة البيئات المسببة للتآكل و الاستقرار الحراري. إنكونيل 600 مناسب بشكل خاص للاستخدام في تطبيقات درجات الحرارة العالية, مثل مكونات الفرن, المبادلات الحرارية, و المفاعلات النووية.
الخصائص الرئيسية للإنكونيل 600:
- محتوى النيكل العالي: إنكونيل 600 يحتوي على نسبة عالية من النيكل (72% الحد الأدنى), مما يوفر مقاومة ممتازة ل تآكل و الاكسده.
- خصائص ميكانيكية جيدة: إنكونيل 600 يحافظ على قوته وصلابته عند درجات الحرارة المرتفعة, مما يجعلها مناسبة لتطبيقات درجات الحرارة العالية.
- مقاومة تكسير التآكل الناتج عن إجهاد الكلوريد: إنكونيل 600 مقاوم ل تكسير كلوريد-أيون الإجهاد والتآكل, مشكلة شائعة في الفولاذ المقاوم للصدأ.
التركيب الكيميائي للإنكونيل 600
عنصر | تكوين (%) |
---|---|
النيكل (ني) | 72 أنا |
الكروم (الجمهورية التشيكية) | 14-17 |
حديد (Fe) | 6-10 |
T11 (ج) | 0.15 ماكس |
المنغنيز (يغطي الأسود الملحوم وغير الملحوم والساخن) | 1 ماكس |
السيليكون (الاشتراكية الدولية) | 0.5 ماكس |
الكبريت (S) | 0.015 ماكس |
درجات (الاتحاد الجمركي) | 0.5 ماكس |
ما هي سبائك Incoloy 800?
إنكولوي 800 هو سبائك النيكل والحديد والكروم الذي تم تصميمه لقوة درجات الحرارة العالية والمقاومة الاكسده و carburization. إنكولوي 800 يستخدم عادة في التطبيقات التي تتطلب مقاومة زحف و تمزق في درجات حرارة مرتفعة. غالبا ما يستخدم في المبادلات الحرارية, مكونات الفرن, و معدات المعالجة الكيميائية.
الخصائص الرئيسية للIncoloy 800:
- تركيب النيكل والحديد والكروم: إنكولوي 800 يحتوي على تركيبة متوازنة من النيكل, حديد, والكروم, مما يوفر مقاومة ممتازة ل الاكسده, carburization, و البيئات التي تحتوي على الكبريت.
- قوة درجات الحرارة العالية: إنكولوي 800 يحتفظ بقوته وسلامته الهيكلية عند درجات حرارة تصل إلى 1100 درجة مئوية (2012F), مما يجعلها مناسبة لتطبيقات درجات الحرارة العالية.
- مقاومة الزحف وتمزق الإجهاد: إنكولوي 800 تم تصميمه للمقاومة زحف و تمزق الإجهاد تحت التعرض لفترات طويلة لدرجات حرارة عالية.
التركيب الكيميائي للIncoloy 800
عنصر | تكوين (%) |
---|---|
النيكل (ني) | 30-35 |
الكروم (الجمهورية التشيكية) | 19-23 |
حديد (Fe) | 39.5 أنا |
T11 (ج) | 0.10 ماكس |
المنغنيز (يغطي الأسود الملحوم وغير الملحوم والساخن) | 1.5 ماكس |
السيليكون (الاشتراكية الدولية) | 1 ماكس |
الكبريت (S) | 0.015 ماكس |
الألومنيوم (شركة) | 0.15-0.60 |
التيتانيوم (منظمة الشفافية الدولية) | 0.15-0.60 |
الاختلافات الرئيسية بين إنكونيل 600 و إنكولوي 800
1. التركيبة الكيميائية
الفرق الأكثر أهمية بين إنكونيل 600 و إنكولوي 800 يكمن في تركيبها الكيميائي. إنكونيل 600 لديه أعلى من ذلك بكثير محتوى النيكل (72% الحد الأدنى), بينما إنكولوي 800 لديه تكوين أكثر توازنا من النيكل, حديد, و الكروم.
- إنكونيل 600: في المقام الأول أ سبائك النيكل والكروم مع نسبة عالية من النيكل, مما يوفر مقاومة ممتازة ل تآكل و الاكسده.
- إنكولوي 800: ا سبائك النيكل والحديد والكروم مع محتوى أقل من النيكل ومحتوى حديد أعلى, الذي يوفر توازنا جيدا قوة درجات الحرارة العالية و المقاومة للتآكل.
2. الخصائص الميكانيكية
تظهر كلا السبائك خواص ميكانيكية جيدة عند درجات حرارة عالية, لكن إنكونيل 600 يكون أقوى بشكل عام في درجات الحرارة المرتفعة بسبب محتواه العالي من النيكل.
خاصية | إنكونيل 600 | إنكولوي 800 |
---|---|---|
مقاومة الشد | 550 الآلام والكروب الذهنية (80,000 هذه المبادرة) أنا | 450 الآلام والكروب الذهنية (65,000 هذه المبادرة) أنا |
مقاومة الخضوع | 240 الآلام والكروب الذهنية (35,000 هذه المبادرة) أنا | 170 الآلام والكروب الذهنية (25,000 هذه المبادرة) أنا |
استطالة | 30% أنا | 30% أنا |
نقطة الانصهار | 1370-1425° C (2500-2600F) | 1357-1385° C (2475-2525F) |
- إنكونيل 600 لديه أعلى قوة الشد و مقاومة الخضوع بالمقارنة مع إنكولوي 800, مما يجعلها أكثر ملاءمة للتطبيقات التي تتطلب قوة ميكانيكية أعلى في درجات حرارة مرتفعة.
- إنكولوي 800 عروض جيدة مقاومة الزحف و مقاومة تمزق الإجهاد, مما يجعلها مثالية للتطبيقات التي تنطوي على التعرض لفترات طويلة لدرجات حرارة عالية.
3. المقاومة للتآكل
كلا إنكونيل 600 و إنكولوي 800 تقديم مقاومة ممتازة للتآكل, ولكن تم تحسينها لبيئات مختلفة.
- إنكونيل 600: معروف بمقاومته الممتازة الاكسده, تكسير كلوريد-أيون الإجهاد والتآكل, و مركبات الكبريت. إنه مثالي للاستخدام في البيئات المسببة للتآكل, مثل المعالجة الكيميائية و المفاعلات النووية.
- إنكولوي 800: يقدم مقاومة جيدة ل الاكسده, carburization, و البيئات التي تحتوي على الكبريت في درجات حرارة عالية. يتم استخدامه بشكل شائع في مكونات الفرن, المبادلات الحرارية, و معالجة البتروكيماويات.
4. مقاومة درجات الحرارة
تم تصميم كلا السبائك لتطبيقات درجات الحرارة العالية, لكن إنكولوي 800 تم تصميمه خصيصًا لـ مقاومة الزحف و مقاومة تمزق الإجهاد في درجات حرارة مرتفعة, مما يجعلها أكثر ملاءمة للتطبيقات التي تنطوي على التعرض لفترات طويلة للحرارة العالية.
- إنكونيل 600: مناسبة للتطبيقات مع درجات حرارة تصل إلى 1093° C (2000F).
- إنكولوي 800: يمكن أن تتحمل درجات حرارة تصل إلى 1100° C (2012F), مما يجعلها مثالية ل مكونات الفرن و المبادلات الحرارية.
5. تطبيقات
بسبب اختلاف تركيبها الكيميائي وخواصها الميكانيكية, إنكونيل 600 و إنكولوي 800 يتم استخدامها في أنواع مختلفة من التطبيقات.
إنكونيل 600 تطبيقات:
- المعالجة الكيميائية: إنكونيل 600 يستخدم على نطاق واسع في معدات المعالجة الكيميائية بسبب مقاومته المواد الكيميائية المسببة للتآكل و الاكسده.
- المفاعلات النووية: إنكونيل 600 يستخدم في المفاعلات النووية بسبب مقاومته إشعاع و تآكل في البيئات ذات درجات الحرارة العالية.
- المبادلات الحرارية: إنكونيل 600 يستخدم في المبادلات الحرارية حيث توجد درجات حرارة عالية وبيئات قابلة للتآكل.
- مكونات الفرن: إنكونيل 600 يستخدم في مكونات الفرن نظراً لقدرته على تحمل درجات الحرارة العالية والأكسدة.
إنكولوي 800 تطبيقات:
- مكونات الفرن: إنكولوي 800 يستخدم عادة في مكونات الفرن بسبب مقاومته الممتازة الاكسده و carburization في درجات حرارة عالية.
- المبادلات الحرارية: إنكولوي 800 يستخدم في المبادلات الحرارية حيث قوة درجات الحرارة العالية ومقاومتها زحف و تمزق الإجهاد مطلوبة.
- معالجة البتروكيماويات: إنكولوي 800 يستخدم في معالجة البتروكيماويات المعدات بسبب مقاومتها الاكسده و البيئات التي تحتوي على الكبريت.
- محطات الطاقة النووية: إنكولوي 800 يستخدم في محطات الطاقة النووية للمكونات التي تتطلب قوة ومقاومة درجات الحرارة العالية زحف و تمزق الإجهاد.
ملخص الاختلافات
خاصية | إنكونيل 600 | إنكولوي 800 |
---|---|---|
محتوى النيكل | 72% أنا | 30-35% |
محتوى الحديد | 6-10% | 39.5% أنا |
محتوى الكروم | 14-17% | 19-23% |
مقاومة الشد | 550 الآلام والكروب الذهنية (80,000 هذه المبادرة) أنا | 450 الآلام والكروب الذهنية (65,000 هذه المبادرة) أنا |
مقاومة الخضوع | 240 الآلام والكروب الذهنية (35,000 هذه المبادرة) أنا | 170 الآلام والكروب الذهنية (25,000 هذه المبادرة) أنا |
مقاومة درجات الحرارة | تصل إلى 1093 درجة مئوية (2000F) | تصل إلى 1100 درجة مئوية (2012F) |
المقاومة للتآكل | مقاومة ممتازة ل الاكسده, تكسير الإجهاد والتآكل بالكلوريد, و مركبات الكبريت | مقاومة جيدة ل الاكسده, carburization, و البيئات التي تحتوي على الكبريت |
تطبيقات | المعالجة الكيميائية, المفاعلات النووية, المبادلات الحرارية, مكونات الفرن | مكونات الفرن, المبادلات الحرارية, معالجة البتروكيماويات, محطات الطاقة النووية |
خاتمة
كلا إنكونيل 600 و إنكولوي 800 هي مواد ممتازة للبيئات ذات درجات الحرارة العالية والتآكل, ولكن تم تحسينها لتطبيقات مختلفة. إنكونيل 600 مثالي للتطبيقات التي تتطلب مستويات عالية المقاومة للتآكل و القوة الميكانيكية في درجات حرارة مرتفعة, مما يجعلها مناسبة تمامًا لـ المعالجة الكيميائية, المفاعلات النووية, و المبادلات الحرارية.
ثم يمكن التحكم في صلابة منطقة الفصل المركزية بحيث لا تكون أكبر من الصلابة الحرجة لتسبب التكسير FIG, إنكولوي 800 تم تصميمه للتطبيقات التي تتطلب مقاومة زحف, تمزق الإجهاد, و الاكسده في درجات حرارة عالية, مما يجعله الخيار المفضل ل مكونات الفرن, المبادلات الحرارية, و معالجة البتروكيماويات.
عند الاختيار بين هاتين السبائك, من المهم مراعاة ظروف التشغيل المحددة, مثل درجة الحرارة, بيئة التآكل, والحمل الميكانيكي, لضمان أفضل أداء لتطبيقك.