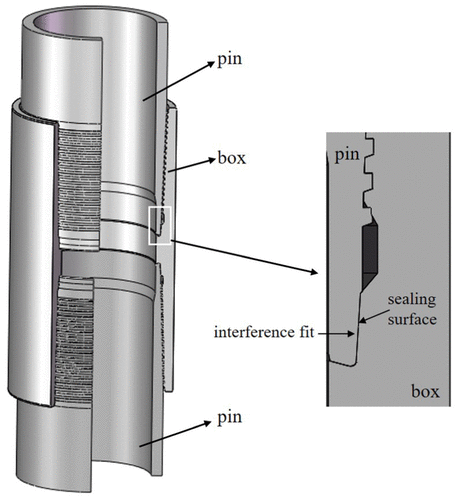
La carcasa aplicación de canalización en pozos de gas de alta temperatura
Enero 4, 2019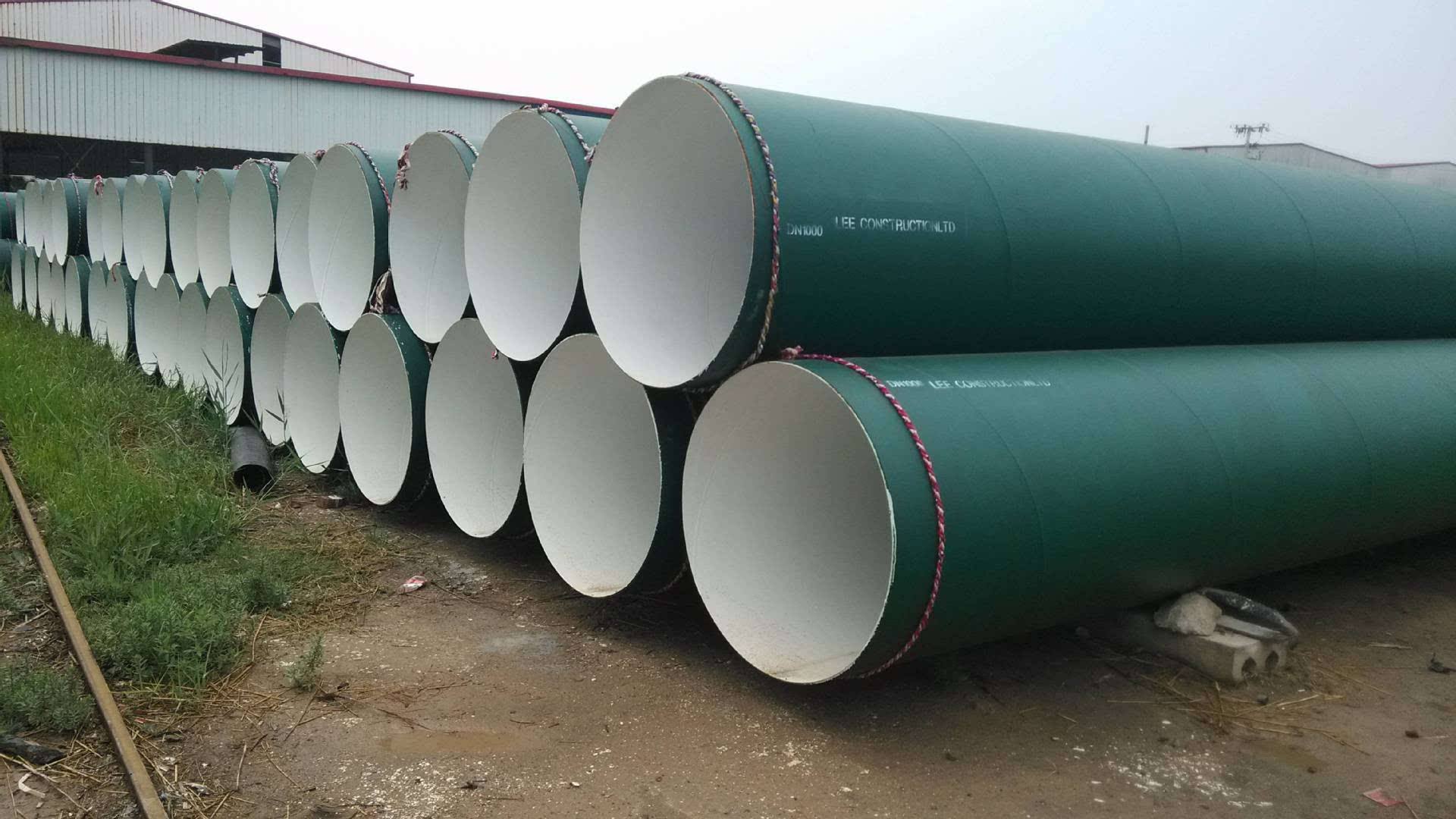
¿Cómo es el peso teórico de tubo de acero en espiral calcula?
Enero 8, 2019RESUMEN
los corrosión resistencias de esmalte-tubo de acero revestido en 3.5 solución de NaCl% en peso se evaluó y se comparó con las de tubo recubierto con epoxi usando potencial de circuito abierto, po lineal- resistencia larization, y Spectros impedancia electroquímica- pruebas de copia. T-001c esmalte en suspensión y polvo de esmalte GP2118 se pulverizaron a la tubería de acero en procesos húmedos y electrostáticas, respectivamente. La composición de fase y microestructuras de los dos esmaltes se caracterizaron por difracción de rayos x y la microscopía electrónica de barrido (SEM). La rugosidad superficial de los esmaltes y de su resistencia de la unión con sustratos de acero fueron cuanti fi para entender la calidad del revestimiento. Las imágenes SEM reveló que ambos tipos de revestimientos de esmalte tienen una estructura sólida con burbujas aisladas. ensayos electroquímicos mostraron una alta resistencia a la corrosión de los recubrimientos de esmalte como verificable ed en la inspección visual de las muestras analizadas. En particular, las muestras de esmalte recubiertos GP2118 superaron consistentemente las muestras epoxi recubierto.
PALABRAS CLAVE: corrosión, espectroscopía de impedancia electroquímica, revestimiento de esmalte, tubería acero, microscopía electrónica de barrido
INTRODUCCIÓN
Natural gas, petróleo, y tuberías de transmisión y recolección de líquidos peligrosos han alcanzado 484,000 millas en las tuberías de envejecimiento U.S.1 se enfrentan a la reducción
vida útil y la fiabilidad como resultado de la corrosión. Ellos pueden ser protegidos de la corrosión por un revestimiento protector, protección catódica, y el uso de inhibidores de la corrosión. De recubrimiento como una barrera física para electrolitos Penetra- ción es uno de los métodos fi cientes más eficaces y EF en la mitigación de la corrosión.
Cuando se aplica internamente para tuberías de acero, capa- ING tiene varias ventajas. primero, el recubrimiento interno puede evitar de fluido o gas a partir de la interacción y la reacción con el acero subyacente. Segundo, tubo de acero revestido reduce los depósitos y bacterias microbiológicos bio fi lm Forma- ciones debido a que la mayor rugosidad de la superficie de la tubería sin recubrimiento ayuda a proteger las bacterias y proporcionar condiciones de crecimiento para colonies.2 bacteriana tercer y último, el
revestimiento interno puede reducir la caída de presión sobre una distancia larga de una tubería y por lo tanto la potencia requerida para transmitir de petróleo y gas. La caída de presión en el tubo revestido se demostró experimentalmente que 35% menor que en el tubo de acero desnudo en un número de Reynolds de
1 × 107.3
Hoy, revestimientos epoxi a base de dos partes de disolvente, disolvente recubrimientos libres y aglutinadas por fusión, y revestimientos de poliamida son ampliamente utilizados en el petróleo crudo y el gas natural pipelines.4-6 Estos revestimientos se débilmente enlazados con
su sustrato de acero y por lo tanto propensas a la sub fi corrosion.7 lm
Esmalte de porcelana, como un material inorgánico, está unido químicamente al sustrato metales a una temperatura de 750 ° C a ~850 ° C. No sólo puede ser terminado con una superficie lisa y estética, sino que también proporcionan ex- estabilidad química cellent, buena resistencia a la corrosión, y durabilidad en diversas environments.8 duras diferencia
revestimiento epoxi, revestimiento de esmalte no tiene la corrosión fi lm sub cuando violó localmente debido a su enlace químico con substrates.9 de metal Ha sido ampliamente utilizado para la protección cocina doméstica utensilio o la protección recipiente de acero en las industrias. Su corrosión re- sistance de como revestimiento protector para el refuerzo de acero en estructuras de hormigón se ha investigado en pre- estudios vious y demostrado ser satisfactorio en general.10-11
en este estudio, el comportamiento de la corrosión de la tubería de acero internamente recubierto con dos tipos de esmalte (T-001 suspensión y GP2118 polvo) fue examinado en 3.5 solución% en peso de NaCl. La composición de la fase y la microestructura de los esmaltes se caracterizaron por difracción de rayos x
(DRX) y microscopía electrónica de barrido (SEM), respectivamente. Se determinó la rugosidad de la superficie de revestimiento de esmalte y su fuerza de adhesión sobre sustratos tubos de acero. Los comportamientos electroquímicos se estudiaron con un potencial de circuito abierto (OCP), lineal polar- resistencia ización (LPR), y IMPED electroquímica- espectroscopia de Ance (EIS) pruebas. Las inspecciones visuales se realizaron en muestras analizadas en busca de signos visibles de corrosión. La resistencia a la corrosión de acero esmaltado se compara con la de acero recubierto con epoxi.
PROCEDIMIENTOS EXPERIMENTALES
Esmaltado y muestras
Un tubo de acero 5L X65 API (MRC Global) con 323.85 mm de diámetro exterior y 9.53 mm en espesor de pared se utiliza como metal de sustrato en este estudio. La composición química del acero proporcionado por el proveedor se presenta en la Tabla 1. El tubo de acero fue primera corta en 18 25 mm x 50 especímenes de cupones mm. Los especímenes de corte fueron entonces acero chorreado para 1 min para deshacerse de la cascarilla de laminación y se oxida, y finalmente limpia con
un disolvente de limpieza disponible comercialmente.
Hay dos tipos de esmalte se aplicaron en los cupones de acero: T-001 suspensión y GP2118 polvo. Las composiciones químicas de T-001 fritas de vidrio y polvo de esmalte GP2118 se determinaron por rayos X de fluorescencia (XRF) tal como se presenta en la tabla 2. La suspensión de esmalte fue preparado por fritas de vidrio primera fresado, arcilla, y ciertos electrolitos, y luego la mezcla con agua hasta que la mezcla estaba en un estado de suspensión estable. La suspensión de esmalte se roció manualmente sobre las muestras de reducción utilizando una pistola de pulverización, que fue impulsado por un chorro de aire comprimido tal como se especifica en la Tabla 3. Las muestras se calentaron a 150 ° C durante 10 min para eliminar la humedad, fi rojo a 815 ° C durante 10 min, y finalmente se enfrió a temperatura ambiente. Para la pulverización electrostática, el polvo de esmalte GP2118 con un tamaño medio de partícula de 32.8 se utilizó micras. Un campo eléctrico se forma entre un electrodo de boquilla y la muestra. partículas de esmalte, propulsado fuera de la pistola de pulverización mediante una corriente de aire, se hizo con carga negativa, migrado hacia la muestra (electrodo positivo) y se des- postulada. Después de la pulverización de potencia, las muestras de acero se trasladaron a un horno y fi rojo a 843 ° C durante 10 min, y luego se trasladó a cabo y se enfrió a temperatura ambiente. El espesor de la T-001 revestimiento se controla por el tiempo de pulverización, mientras que el espesor del recubrimiento GP2118 fue controlada por el número de pistolas de pulverización. Para comparacion, fueron pre muestras de acero revestido de epoxi- Pared y probado. En este caso, 3M Scotchkote 323 † epoxi, que fue aplicada en la industria de tuberías, se utilizó para recubrir las muestras. cupones de acero se revistieron con el cepillo epoxi a temperatura ambiente y después se secaron en aire durante 3 d antes de las pruebas electroquímicas.
Caracterización del esmalte Revestimientos
El espesor del revestimiento y rugosidad se midieron con un calibrador de espesor de revestimiento minitest 6008 † y microscopio óptico Hirox †, respectivamente.
La resistencia de la unión entre el revestimiento y su sustrato de acero se determinaron utilizando PosiTest † D4541-09.12 siguiente ASTM Para mejorar su vínculo con el revestimiento, un 20 Dolly diámetro mm en la base se hace rugosa con papel de lija, y limpiado con alcohol para eliminar la oxidación y contaminantes. La base de la plataforma se adhirió con una capa uniforme de pegamento a la superficie de revestimiento de prueba. Después de curar durante 24 h, el revestimiento alrededor de la plataforma móvil se eliminó usando una 20 mm herramienta de corte con el fin de aislar el carro en un área de prueba c específica. El carro fue finalmente salió de la superficie de la muestra perpendicularmente a una tasa de estrés 0.4 MPa / s. La fuerza máxima de cada muestra revestida se registró.
A la finalización de los ensayos de corrosión, las fases en el recubrimiento se examinaron directamente sobre la superficie de muestras de acero revestidas por XRD (Philip X'Pert †) con ángulo de difracción (2yo) varió entre 10 ° y 55 °. Las secciones transversales de las muestras de esmalte recubiertos se prepararon para el análisis de la microestructura con SEM (Hitachi S4700 †). Cada muestra esmaltado fue primer frío montado en resina epoxi (EpoxyMount †, Allied Productos de alta tecnología, Cª) y cortar en una 10 sección transversal de espesor mm usando una sierra de diamante. Entonces, la sección transversal se sometió a abrasión con los papeles de carburo a 1200 arena, se enjuagaron con agua desionizada, y finalmente se secó en aire a temperatura ambiente antes de su examen. Imágenes de SEM se analizaron con el software ImageJ † para la evaluación de la porosidad.
Las pruebas electroquímicas
Cada muestra se suelda con un alambre de cobre para las mediciones electroquímicas como se ilustra en la figura 1. Todas las partes de la muestra, excepto el esmalte- o la cara recubierto con epoxi fueron cubiertos con epoxi marina.
El área de esmalte o epoxi expuesto era 30 mm x 20 mm de tamaño.
Todas las muestras se sumergieron en 3.5 solución de NaCl al% en peso con el pH de 7 y probado a tempera habitación- tura de 69 D. La solución se preparó añadiendo cloruro de fi ed sodio puri (Fisher Scientific c, Cª) en agua destilada.
En el momento de 1, 3, 6, 13, 27, 41, 55, y 69 D, OCP, LPR, y las pruebas de EIS se realizaron para supervisar la evolución de corrosión del esmalte- y muestras de acero revestido de epoxi. Un sistema de tres electrodos estándar se utilizó para ensayos electroquímicos, incluyendo una 25.4 mm x 25.4 mm x 0.254 hoja de platino mm como un contraelectrodo, electrodo de calomelanos saturado (SCE) como un electrodo de referencia, y la muestra revestida como un electrodo de trabajo. Los tres electrodos se conectaron a un potenciostato Gamry 1000E / Galvanostato † para adquisición de datos.
Después de cada OCP estable (que dura 1 h) fue grabado, una prueba de EIS se realizó con un potencial de onda sinusoidal de 10 mV de amplitud alrededor de la OCP y una frecuencia de 100 kHz a 5 megahercio. La prueba LPR se llevó a cabo mediante el escaneo de un rango de ± 15 mV alrededor de la OCP a una velocidad de barrido de 0.167 mV / s. Las curvas de LPR se utilizan para determinar la resistencia Rp polarización, que es igual a la pendiente de la región lineal de una curva de polarización en torno a corriente cero:13
Rp =? E =? I
donde? E? I y representan los incrementos de tensión y corriente, respectivamente, en la parte lineal de una curva de polarización en i = 0. mediciones LPR se utilizaron para calcular la densidad de corriente de corrosión por la ecuación de Stern-Geary:13
icorr = vavc = ½2.303dva + βcThRp (2)
donde ßa y βc representar la constante anódica Tafel (0.12) y la constante de Tafel catódica (0.12), respectivamente, y icorr es la corriente de corrosión.
RESULTADOS Y DISCUSIÓN
Caracterización de revestimiento
Fases en el esmalte - Patrones de difracción de rayos X en la superficie de GP2118 y T-001 muestras de esmalte recubiertos después de inmersión en 3.5 solución% en peso de NaCl para 69 d se identifican y se muestra en la figura 2. Cuarzo SiO2 está presente en ambos tipos de revestimientos de esmalte. Los picos de intensidad más altos de cuarzo SiO2 fueron a 26 ° y 26.5 ° para GP2118 y T-001 esmaltes, respectivamente.
Microestructura en esmalte Interface / sustrato - imágenes de SEM de corte transversal en la interfase acero / recubrimiento con diferentes cationes fi Magni se presentan en la figura 3. Los revestimientos de esmalte tienen una estructura sólida con aire desconectado burbujas a través del espesor de revestimiento (Figuras 3[A1] y [b1]). se formaron las burbujas de aire durante la sustancia química a alta temperatura
reacción de la frita de vidrio esmalte con el acero durante anillo fi process.14-15 Los revestimientos de esmalte tienen numerosas
pequeños poros aislados con la excepción de esmalte GP2118 que tiene unos poros grandes con un diámetro de aproximadamente 105 Μm. El contenido de porosidad de T-001 esmalte se midió para ser 4.26%, que es inferior a 12.72% para el esmalte GP2118. Figuras 3(a2) y (b2) mostrar las interfaces fi ed esmalte / acero Magni en la que salientes de pequeña Fe crecen en la capa de esmalte para formar varios puntos de anclaje. Estas partículas de espinela epitaxiales mejorar la unión entre el esmalte y su substrate.16 acero
Pull-Off Fuerza - El espesor medido, rugosidad de la superficie, y resistencia de la unión de tres tipos de recubrimientos se resume en la tabla 4. El promedio y la desviación estándar del espesor y rugosidad superficial de cada revestimiento se calculan a partir de
27 mediciones tomadas a partir de tres muestras diferentes que fueron pulidas para tienen una superficie plana para el ensayo de tracción-off. El promedio y la desviación estándar de la resistencia de unión de cada revestimiento se calculan a partir de las tres pruebas pull-off realizados. Se puede observar en la tabla 4 que el recubrimiento epoxi es la más gruesa (396 Μm) y T-001 esmalte es el más delgado (230 Μm). los
rugosidad de los recubrimientos es de alrededor de tres 1 Μm, indicando superficies lisas en todos los especímenes.
A la finalización de las pruebas de pull-off, las superficies Dolly y de fractura sustrato se muestran en la figura 4. En una prueba de adherencia pull-off, cuatro posibles modos de fallo incluyen: (1) descanso adhesión entre el revestimiento y su sustrato de acero, (2) rotura de cohesión dentro de la capa de revestimiento, (3) rotura del pegamento, y (4) descanso mixto o un combi- nación de los saltos anteriores en locations.17 múltiple
revestimientos de esmalte tienen un modo de fallo mixta en- volving un descanso en el interior del revestimiento (ruptura cohesiva) y una rotura en el pegamento utilizado para unir la plataforma rodante para el espécimen. Revestimiento epoxi también tiene un modo de fallo mixta que implica una ruptura en el interior del revestimiento (ruptura cohesiva), un descanso entre el recubrimiento y el sustrato de acero (descanso adhesivo), y una ruptura pegamento. No hay saltos de adhesivos para revestimientos de esmalte debido a que los puntos de anclaje en la interfaz de aumentar la unión entre un recubrimiento de esmalte y su acero sustrato como se muestra en la figura 3. Específicamente, recubrimiento de esmalte GP2118 tiene la resistencia de unión más alta con un valor medio de 17.89 MPa, recubrimiento epoxi tiene la resistencia de unión más baja de 8.01 MPa, y T-001 recubrimiento de esmalte tiene una fuerza de unión de 16.85 MPa.
Figuras 5(un) y (b) representar las morfologías superficiales fi ed fractura Magni como se muestra en las Figuras 4(a2) y (b2), respectivamente. Cuando el carro se quitó el espécimen recubierto a ángulo recto, una grieta inicia y se propaga a través de grandes burbujas de aire dentro del Escudo- ING bajo cargas cada vez mayores. cifras 6(un) y (b) Demostración de las imágenes SEM para las secciones transversales de los SPE probado- cIMEnS en áreas rectangulares de cifras 4(a2) y (b2), respectivamente. Las superficies de fractura de las muestras son generalmente lisa con el mínimo recubrimiento se mantuvo espesores de aproximadamente 70 M y
40 Para M y T GP2118-001 esmaltes, respectivamente. En comparación con la figura 3, cifras 6(un) y (b) Indican que las superficies de fractura están muy lejos de sus capas de unión correspondientes en las interfaces Esmalte / sustrato y atravesar la capa más débil que conecta burbuja grande de aire en el recubrimiento debido a la adherencia del esmalte sobre superficies de acero es químicamente reforzado con el crecimiento de las partículas epitaxial espinela en el esmalte durante Reacción química en el anillo de fi ProcESS.16